Il processo di ricottura dei tubi prevede il riscaldamento del metallo a una temperatura specifica in cui la sua struttura cristallina diventa più fluida, consentendo ai difetti di ripararsi.Successivamente, il metallo viene mantenuto a quella temperatura per un periodo di tempo prestabilito e poi raffreddato a velocità controllata per ottenere una struttura più duttile e lavorabile.Il processo di ricottura si divide in tre fasi:Recupero, ricristallizzazione e crescita dei grani, che si verificano con l'aumento della temperatura.Questo processo viene comunemente eseguito con un forno a camera, dove il controllo preciso della temperatura e la velocità di raffreddamento sono essenziali per ottenere le proprietà desiderate del materiale.
Punti chiave spiegati:
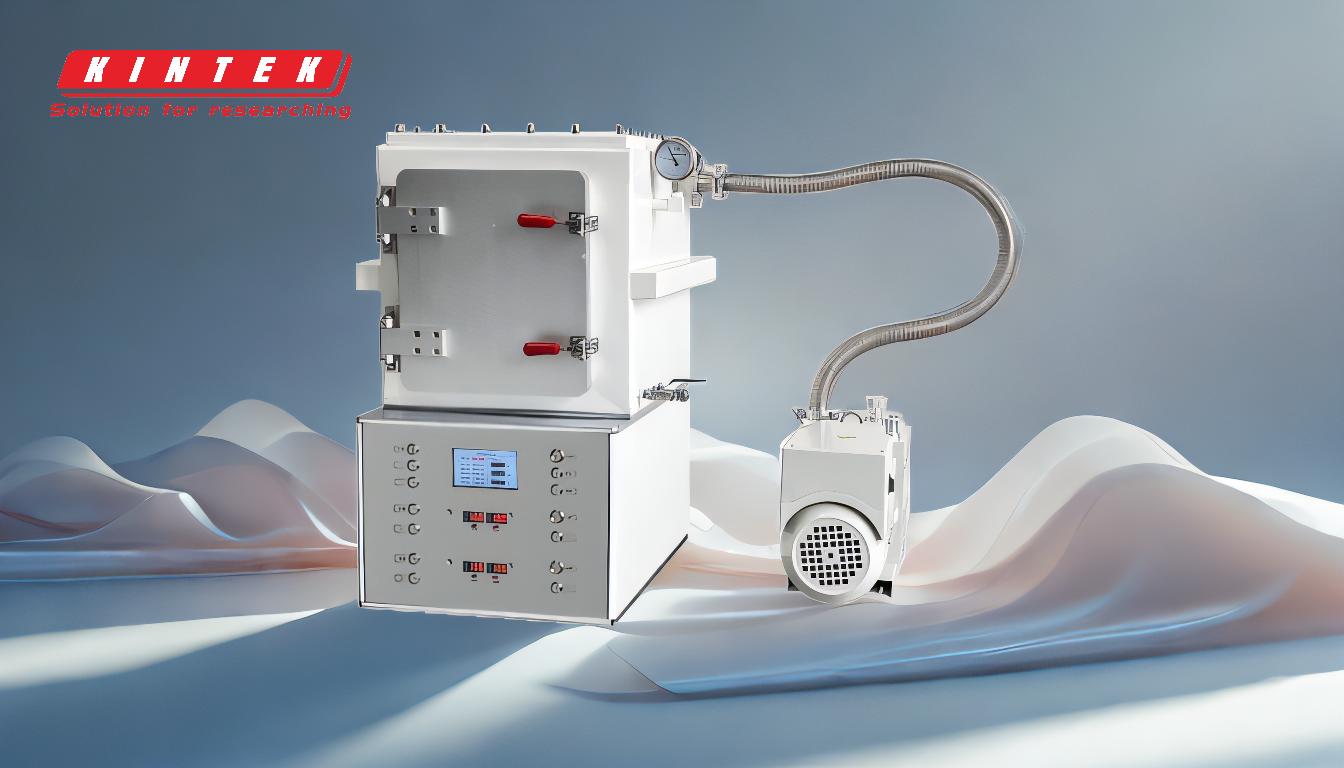
-
Tre fasi di ricottura:
- Recupero:È la fase iniziale in cui il metallo viene riscaldato a una temperatura che allevia le tensioni interne senza alterare la struttura dei grani.Il metallo inizia ad ammorbidirsi e le dislocazioni nella struttura cristallina iniziano a muoversi e a riorganizzarsi.
- Ricristallizzazione:In questa fase, il metallo viene riscaldato a una temperatura più elevata, dove iniziano a formarsi nuovi grani privi di deformazioni, che sostituiscono i grani deformati.Ciò comporta una riduzione della durezza e un aumento della duttilità.
- Crescita dei grani:Se il metallo viene mantenuto troppo a lungo alla temperatura di ricristallizzazione, i grani continueranno a crescere, con conseguente diminuzione della resistenza.Il controllo del tempo e della temperatura è fondamentale per evitare una crescita eccessiva dei grani.
-
Riscaldamento del metallo:
- Il metallo viene riscaldato a una temperatura specifica in cui la struttura cristallina diventa fluida ma rimane allo stato solido.Questa temperatura è in genere inferiore al punto di fusione del metallo, ma abbastanza alta da consentire il movimento degli atomi all'interno del reticolo cristallino.
- La temperatura esatta dipende dal tipo di metallo da ricuocere.Ad esempio, l'acciaio viene generalmente ricotto a temperature comprese tra 700 e 900°C, mentre il rame viene ricotto a temperature più basse, tra 400 e 700°C circa.
-
Tempo di mantenimento:
- Dopo aver raggiunto la temperatura desiderata, il metallo viene mantenuto a tale temperatura per un periodo specifico, noto come tempo di mantenimento.Ciò consente la ricristallizzazione completa del metallo e la riparazione di eventuali difetti nella struttura cristallina.
- Il tempo di mantenimento varia a seconda del tipo di metallo, del suo spessore e delle proprietà desiderate.Ad esempio, i materiali più spessi possono richiedere tempi di mantenimento più lunghi per garantire un riscaldamento uniforme in tutto il materiale.
-
Raffreddamento controllato:
- Dopo il periodo di mantenimento, il metallo viene raffreddato a velocità controllata.Il raffreddamento lento è essenziale per evitare la formazione di nuove tensioni e per consentire al metallo di raggiungere una struttura più duttile e uniforme.
- La velocità di raffreddamento può variare a seconda del materiale e del risultato desiderato.Per alcuni materiali è preferibile il raffreddamento nel forno (raffreddamento in forno), mentre per altri può essere necessario il raffreddamento in aria o in un ambiente controllato.
-
Uso del forno a camera:
- Un forno a camera è comunemente utilizzato per il processo di ricottura grazie alla sua capacità di fornire un controllo preciso della temperatura e un riscaldamento uniforme.Il forno consente di riscaldare il metallo in modo uniforme, garantendo risultati omogenei in tutto il materiale.
- Il forno fornisce anche un ambiente controllato per il raffreddamento, che è fondamentale per ottenere le proprietà desiderate del materiale.
Seguendo queste fasi, il processo di ricottura può migliorare efficacemente la duttilità, ridurre la durezza e alleviare le tensioni interne dei tubi metallici, rendendoli più adatti a ulteriori lavorazioni o all'uso in varie applicazioni.
Tabella riassuntiva:
Fase | Descrizione |
---|---|
Recupero | Allevia le tensioni interne; le dislocazioni nella struttura cristallina si riorganizzano. |
Ricristallizzazione | Si formano nuovi grani privi di deformazioni che riducono la durezza e aumentano la duttilità. |
Crescita dei grani | Se la temperatura e il tempo non sono controllati, può verificarsi una crescita eccessiva dei grani. |
Riscaldamento | Metallo riscaldato a una temperatura specifica inferiore al punto di fusione per ottenere la fluidità. |
Tempo di mantenimento | Il metallo viene mantenuto in temperatura per consentire la ricristallizzazione e la riparazione dei difetti. |
Raffreddamento | Il raffreddamento controllato previene nuove tensioni e garantisce una struttura duttile. |
Forno a camera | Offre un controllo preciso della temperatura e un riscaldamento uniforme per risultati costanti. |
Ottimizzate la lavorazione dei metalli con tecniche di ricottura precise... contattateci oggi per una guida esperta!