La sinterizzazione laser selettiva (SLS) e la fusione a fascio di elettroni (EBM) sono entrambe tecnologie di produzione additiva (stampa 3D), ma si differenziano notevolmente per i processi, i materiali e le applicazioni.La SLS utilizza un laser ad alta potenza per sinterizzare materiale in polvere, in genere polimeri o metalli, strato per strato per creare un oggetto 3D.L'EBM, invece, utilizza un fascio di elettroni per fondere la polvere di metallo in un ambiente sotto vuoto, rendendolo adatto ad applicazioni ad alta resistenza e ad alta temperatura.Mentre la SLS è versatile e funziona con una serie di materiali, l'EBM è più specializzata per le parti metalliche, in particolare nell'industria aerospaziale e medica.Entrambe le tecnologie eliminano la necessità di stampi, ma l'EBM offre una maggiore precisione e migliori proprietà meccaniche per i componenti metallici.
Punti chiave spiegati:
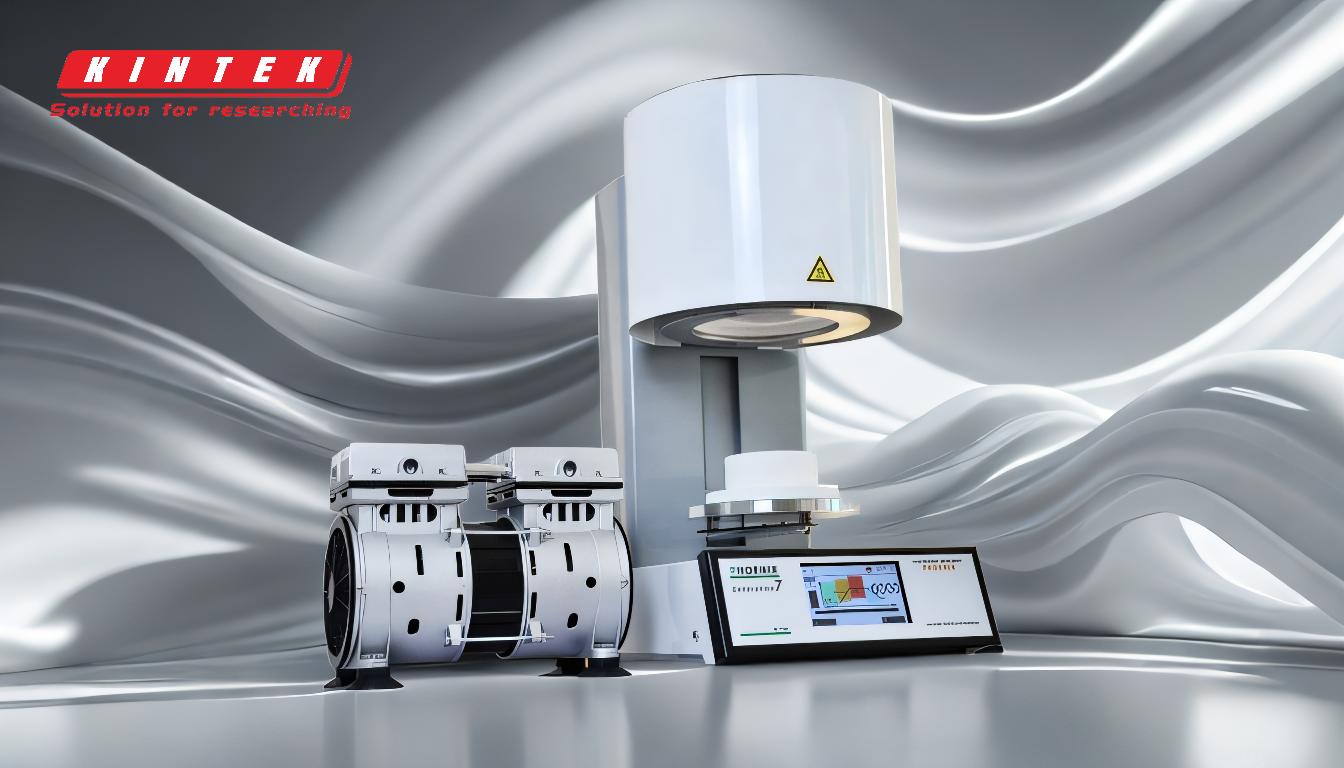
-
Meccanismo di processo:
- Sinterizzazione laser selettiva (SLS):Utilizza un laser ad alta potenza per sinterizzare (fondere) selettivamente il materiale in polvere, strato per strato, per costruire un oggetto 3D.Il laser riscalda la polvere quanto basta per unire le particelle senza fonderle completamente.
- Fusione a fascio di elettroni (EBM):Utilizza un fascio di elettroni ad alta energia per fondere completamente la polvere di metallo in una camera a vuoto.Il fascio di elettroni scansiona il letto di polvere, fondendo il materiale strato per strato per creare un pezzo denso e ad alta resistenza.
-
Materiali utilizzati:
- SLS:Lavora principalmente con polimeri (ad esempio, nylon, poliammide) e alcune polveri metalliche.È versatile e può trattare un'ampia gamma di materiali, compresi i compositi.
- EBM:Esclusivo per le polveri metalliche, come il titanio, il cobalto-cromo e le leghe a base di nichel.È ideale per produrre pezzi ad alta resistenza e resistenti alle alte temperature.
-
Condizioni ambientali:
- SLS:Funziona in un'atmosfera controllata, in genere azoto o argon, per evitare l'ossidazione del materiale.Non richiede il vuoto.
- EBM:Richiede un ambiente ad alto vuoto per evitare la contaminazione e garantire il funzionamento efficace del fascio di elettroni.Questo rende il processo più complesso e costoso.
-
Precisione e finitura superficiale:
- SLS:Produce pezzi con buona finitura superficiale e moderata precisione.Tuttavia, la superficie può richiedere una post-elaborazione (ad esempio, levigatura o rivestimento) per ottenere finiture più lisce.
- EBM:Offre una maggiore precisione e migliori proprietà meccaniche grazie alla fusione completa della polvere metallica.I pezzi hanno una finitura superficiale più ruvida rispetto alla SLS, ma sono più resistenti e durevoli.
-
Applicazioni:
- SLS:Adatto per la prototipazione, i pezzi funzionali e la produzione di bassi volumi.Comunemente utilizzato nei settori automobilistico, aerospaziale e dei beni di consumo.
- EBM:Ideale per applicazioni ad alte prestazioni, come componenti aerospaziali, impianti medici e pale di turbine, in cui la forza e la resistenza termica sono fondamentali.
-
Costo e velocità di produzione:
- SLS:Generalmente più veloce e conveniente per la prototipazione e la produzione di piccoli lotti.Non richiede stampi, riducendo i costi iniziali.
- EBM:Più costoso a causa dell'ambiente sotto vuoto e delle attrezzature specializzate.È più lento ma produce pezzi con proprietà meccaniche superiori, giustificando il costo più elevato per le applicazioni critiche.
-
Requisiti di post-lavorazione:
- SLS:I pezzi possono richiedere una minima post-elaborazione, come la rimozione del supporto o la finitura della superficie.Tuttavia, il processo è relativamente semplice.
- EBM:I pezzi richiedono spesso un trattamento termico o una lavorazione per ottenere le proprietà meccaniche e la finitura superficiale desiderate.L'ambiente del vuoto aggiunge complessità alla post-lavorazione.
Comprendendo queste differenze chiave, gli acquirenti di apparecchiature e materiali di consumo possono prendere decisioni informate in base ai requisiti specifici dei loro progetti, come le proprietà dei materiali, la precisione e le esigenze applicative.
Tabella riassuntiva:
Aspetto | Sinterizzazione laser selettiva (SLS) | Fusione a fascio di elettroni (EBM) |
---|---|---|
Meccanismo di processo | Utilizza un laser ad alta potenza per sinterizzare il materiale in polvere strato per strato. | Utilizza un fascio di elettroni per fondere completamente la polvere di metallo nel vuoto. |
Materiali utilizzati | Polimeri (ad esempio, nylon, poliammide) e alcune polveri metalliche. | Esclusivamente per le polveri metalliche (ad esempio, titanio, cobalto-cromo, leghe a base di nichel). |
Condizioni ambientali | Funziona in atmosfera controllata (azoto/argon). | Richiede un ambiente ad alto vuoto. |
Precisione e finitura superficiale | Buona finitura superficiale, precisione moderata.Può richiedere una post-elaborazione. | Pezzi più precisi e resistenti.Finitura superficiale più ruvida ma proprietà meccaniche superiori. |
Applicazioni | Prototipazione, parti funzionali, produzione di bassi volumi (settore automobilistico, aerospaziale, beni di consumo). | Applicazioni ad alte prestazioni (aerospaziale, impianti medici, pale di turbine). |
Costo e velocità di produzione | Più veloce e conveniente per la prototipazione e la produzione di piccoli lotti. | Più costoso e lento, ma ideale per applicazioni critiche. |
Post-lavorazione | Minima (rimozione del supporto, finitura della superficie). | Spesso richiede un trattamento termico o una lavorazione a causa dell'ambiente sotto vuoto. |
Avete bisogno di aiuto per scegliere la tecnologia di stampa 3D più adatta al vostro progetto? Contattate i nostri esperti oggi stesso!