La metallurgia delle polveri (PM) è un processo di produzione versatile che offre numerosi vantaggi, come alta efficienza, basso spreco di materiale e la capacità di produrre parti uniformi con tolleranze strette. Presenta però anche diversi svantaggi che possono limitarne l’applicazione in determinati scenari. Questi includono limitazioni nelle dimensioni e nella complessità delle parti, ridotta resistenza meccanica dovuta alla porosità e sfide nella produzione di parti che corrispondano alla resistenza e alla duttilità dei componenti fusi o forgiati. Di seguito esploriamo questi svantaggi in dettaglio.
Punti chiave spiegati:
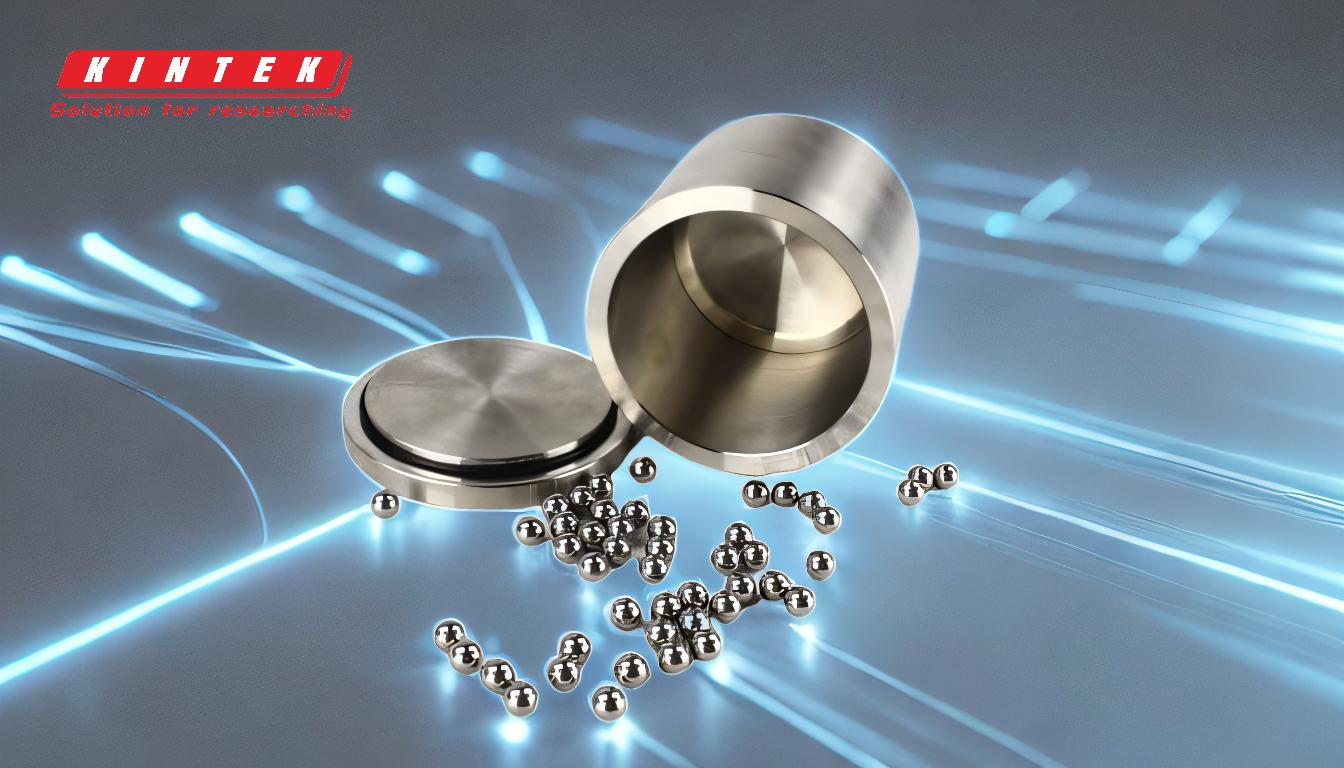
-
Limitazioni sulle dimensioni:
- La metallurgia delle polveri è vincolata dalle dimensioni delle presse utilizzate nel processo. Le presse più grandi del settore sono in genere di circa 1.500 tonnellate, il che limita la dimensione pratica dei pezzi a circa 40-50 pollici quadrati di area planare. Ciò rende la PM inadatta alla produzione di componenti molto grandi, che potrebbero richiedere metodi di produzione alternativi come la fusione o la forgiatura.
-
Parti di forma complessa:
- Sebbene la PM possa produrre parti con geometrie complesse, esistono limitazioni alla complessità delle forme che possono essere ottenute. Le parti dalla forma complessa spesso richiedono attrezzature avanzate e produttori qualificati per superare le sfide legate alla pressatura e alla sinterizzazione delle polveri. Ciò può aumentare i costi di produzione e i tempi di consegna, rendendo la PM meno competitiva per progetti altamente complessi.
-
Porosità e ridotta resistenza meccanica:
- Uno degli svantaggi intrinseci del PM è la presenza di porosità nelle parti sinterizzate. La porosità si verifica a causa degli spazi tra le particelle di polvere che rimangono anche dopo la compattazione e la sinterizzazione. Questa porosità riduce la densità della parte finale, portando a una resistenza meccanica inferiore rispetto alle parti fuse o forgiate. Di conseguenza, le parti PM potrebbero non essere adatte per applicazioni che richiedono elevata resistenza o durata.
-
Duttilità inferiore:
- Le parti PM generalmente mostrano una duttilità inferiore rispetto a quelle prodotte mediante fusione o forgiatura. La duttilità è la capacità di un materiale di deformarsi sotto stress di trazione e la sua riduzione nelle parti in PM può limitarne l'uso in applicazioni in cui la flessibilità o la resistenza agli urti sono fondamentali.
-
Limitazioni materiali:
- Non tutti i materiali sono adatti alla metallurgia delle polveri. Alcune leghe o materiali potrebbero non compattarsi o sinterizzare in modo efficace, limitando la gamma di materiali utilizzabili. Inoltre, ottenere proprietà specifiche del materiale, come elevata robustezza o resistenza alla corrosione, può essere più impegnativo con la PM rispetto ad altri metodi di produzione.
-
Costo degli strumenti:
- Il costo iniziale degli utensili per la manutenzione meccanica può essere elevato, in particolare per parti personalizzate o complesse. Sebbene la PM sia economicamente vantaggiosa per la produzione di volumi elevati, l’investimento iniziale in attrezzature potrebbe non essere giustificato per cicli di produzione di volumi ridotti o di prototipi.
-
Parti per uso finale incomplete:
- A causa delle limitazioni della pressatura e della sinterizzazione delle polveri, alcune parti destinate all'uso finale potrebbero essere incomplete o richiedere operazioni secondarie per ottenere la forma o le proprietà desiderate. Ciò può aumentare il costo complessivo e la complessità della produzione.
-
Opzioni di finitura superficiale limitate:
- Le parti PM hanno spesso una finitura superficiale più ruvida rispetto alle parti lavorate o forgiate. Sebbene le operazioni secondarie come la lavorazione meccanica o il rivestimento possano migliorare la finitura superficiale, questi passaggi aggiuntivi aumentano i tempi e i costi di produzione.
-
Preoccupazioni ambientali e di sicurezza:
- Sebbene il PM sia generalmente considerato ecologico a causa del minimo spreco di materiale, la manipolazione di polveri metalliche fini può comportare rischi per la salute e la sicurezza, come problemi respiratori o rischi di incendio. Per mitigare questi rischi sono necessarie misure e attrezzature di sicurezza adeguate.
-
Dipendenza dalle caratteristiche della polvere:
- La qualità delle parti PM dipende fortemente dalle caratteristiche della polvere metallica utilizzata, come portata, densità, comprimibilità e resistenza. Le variazioni nelle proprietà della polvere possono portare a incongruenze nel prodotto finale, richiedendo rigorose misure di controllo della qualità.
In sintesi, mentre la metallurgia delle polveri offre vantaggi significativi in termini di efficienza e utilizzo dei materiali, i suoi svantaggi, come limitazioni dimensionali, porosità, proprietà meccaniche ridotte e sfide con forme complesse, devono essere attentamente considerati quando si seleziona un processo di produzione. Queste limitazioni rendono il PM più adatto per applicazioni specifiche in cui i suoi vantaggi superano i suoi svantaggi.
Tabella riassuntiva:
Svantaggio | Descrizione |
---|---|
Limitazioni sulle dimensioni | Limitato a parti con aree planari di 40-50 pollici quadrati a causa dei vincoli della pressa. |
Parti di forma complessa | Sono necessari strumenti avanzati e manodopera qualificata, con conseguente aumento dei costi e dei tempi di consegna. |
Porosità e resistenza ridotta | La porosità nelle parti sinterizzate riduce la resistenza meccanica e la durata. |
Duttilità inferiore | Flessibilità e resistenza agli urti ridotte rispetto alle parti fuse o forgiate. |
Limitazioni materiali | Gamma limitata di materiali adatti per PM; sfide nel raggiungimento delle proprietà. |
Costo degli strumenti | Costi iniziali elevati per gli utensili, soprattutto per parti personalizzate o complesse. |
Parti per uso finale incomplete | Potrebbe richiedere operazioni secondarie, aumentando i costi di produzione e la complessità. |
Opzioni di finitura superficiale limitate | Finitura superficiale più ruvida; ulteriori passi necessari per il miglioramento. |
Preoccupazioni ambientali e di sicurezza | Rischi per la salute derivanti da polveri metalliche fini; richiede misure di sicurezza. |
Dipendenza dalle caratteristiche della polvere | La qualità del prodotto finale dipende dalle proprietà della polvere, che richiedono controlli rigorosi. |
Hai bisogno di aiuto per scegliere il giusto processo di produzione? Contatta i nostri esperti oggi stesso per una consulenza personalizzata!