La tempra in aria è un processo di trattamento termico in cui il metallo caldo viene raffreddato rapidamente utilizzando aria, anziché liquidi come olio o acqua. Questo metodo offre numerosi vantaggi, tra cui un ridotto rischio di distorsione, una migliore finitura superficiale e benefici ambientali dovuti all'assenza di oli di tempra. È particolarmente adatto per materiali che richiedono velocità di raffreddamento controllate per ottenere le proprietà meccaniche desiderate. Inoltre, la tempra in aria è economicamente vantaggiosa, poiché elimina la necessità di costosi mezzi di tempra e riduce i requisiti di manutenzione. Il processo è anche più sicuro, poiché evita i rischi associati alla manipolazione di oli caldi o acqua. Nel complesso, la tempra in aria fornisce una soluzione affidabile ed efficiente per il trattamento termico in varie applicazioni industriali.
Punti chiave spiegati:
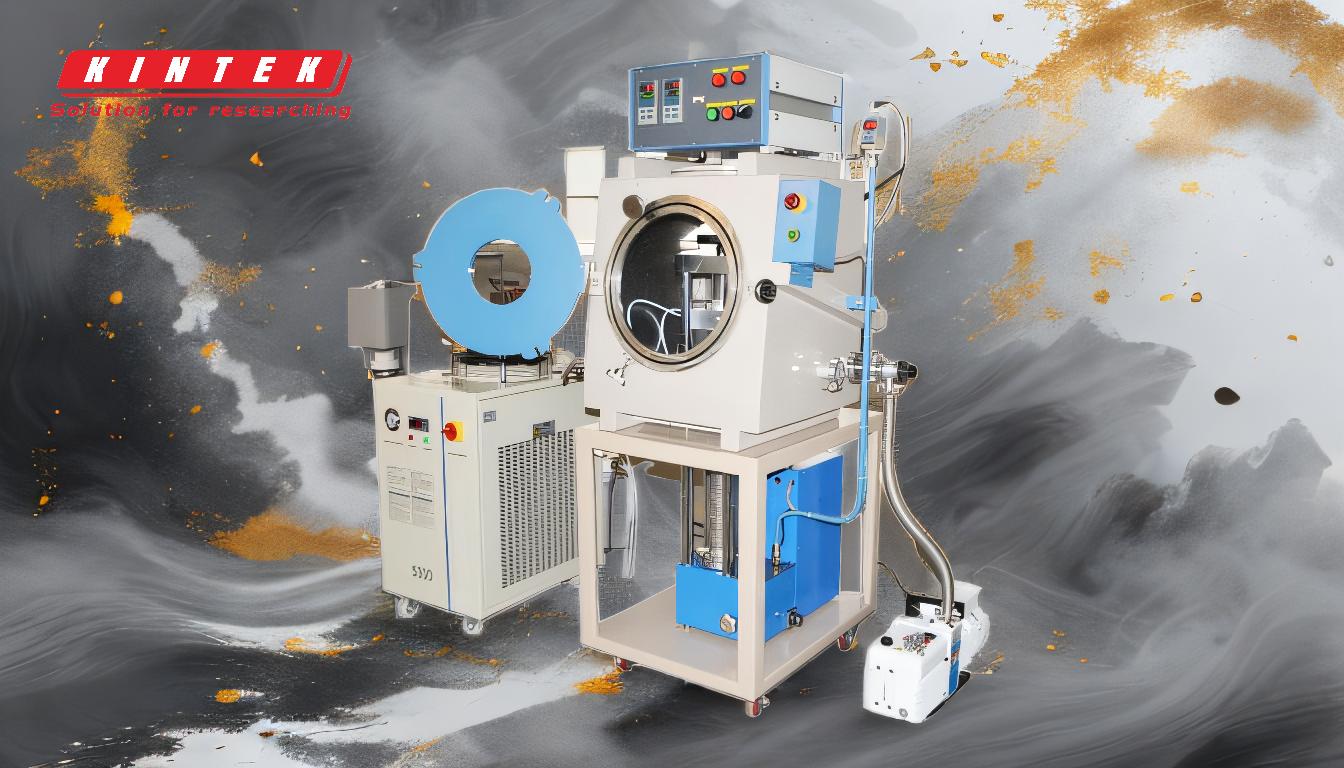
-
Rischio ridotto di distorsione:
- La tempra in aria comporta il raffreddamento del metallo a una velocità più lenta e controllata rispetto ai metodi di tempra in liquido. Ciò riduce lo stress termico e minimizza il rischio di deformazioni o distorsioni, il che è particolarmente importante per componenti complessi o progettati con precisione.
-
Finitura superficiale migliorata:
- Poiché la tempra in aria non comporta il contatto con i liquidi, evita problemi come l'ossidazione o la contaminazione della superficie che possono verificarsi con la tempra in olio o acqua. Ciò si traduce in una finitura superficiale più pulita e liscia, fondamentale per le applicazioni che richiedono elevati standard estetici o funzionali.
-
Benefici ambientali:
- La tempra in aria è un'alternativa ecologica alla tempra in olio o acqua. Elimina la necessità di oli da tempra, che possono essere pericolosi per l'ambiente e richiedono uno smaltimento adeguato. Ciò rende la tempra in aria un’opzione più sostenibile per i processi di trattamento termico.
-
Efficacia in termini di costi:
- L'assenza di oli di raffreddamento o altri liquidi riduce i costi operativi. Non è necessario acquistare, immagazzinare o smaltire mezzi di raffreddamento e i requisiti di manutenzione sono inferiori poiché non vi è alcun rischio di degradazione o contaminazione dell'olio.
-
Sicurezza:
- La tempra in aria è intrinsecamente più sicura rispetto ai metodi di tempra in liquido. Elimina i rischi associati alla manipolazione di oli o acqua caldi, come ustioni, incendi o fuoriuscite. Ciò rende il processo più adatto agli ambienti in cui la sicurezza è una priorità.
-
Versatilità:
- La tempra in aria può essere utilizzata per un'ampia gamma di materiali, inclusi acciai, leghe e altri metalli che richiedono velocità di raffreddamento controllate. È particolarmente efficace per i materiali soggetti a fessurazioni o distorsioni se esposti a un rapido raffreddamento.
-
Coerenza e affidabilità:
- La velocità di raffreddamento controllata della tempra in aria garantisce risultati costanti, rendendolo un metodo affidabile per ottenere le proprietà meccaniche desiderate come durezza, resistenza e tenacità. Questa coerenza è fondamentale per settori come quello aerospaziale, automobilistico e della produzione di utensili.
-
Efficienza energetica:
- I sistemi di raffreddamento ad aria spesso richiedono meno energia rispetto ai sistemi di raffreddamento a liquido, poiché non è necessario riscaldare o far circolare i mezzi di raffreddamento. Ciò contribuisce a ridurre il consumo energetico e i costi operativi.
Sfruttando questi vantaggi, la tempra in aria fornisce una soluzione pratica ed efficiente per il trattamento termico, soddisfacendo le esigenze delle moderne applicazioni industriali e affrontando al contempo i problemi ambientali e di sicurezza.
Tabella riassuntiva:
Vantaggio | Descrizione |
---|---|
Rischio ridotto di distorsione | Il raffreddamento controllato riduce al minimo lo stress termico, riducendo deformazioni e distorsioni. |
Finitura superficiale migliorata | Nessun contatto con liquidi impedisce l'ossidazione o la contaminazione, garantendo una finitura più pulita. |
Benefici ambientali | Elimina gli oli da tempra pericolosi, rendendolo ecologico e sostenibile. |
Efficacia in termini di costi | Non sono necessari costosi mezzi di raffreddamento o smaltimento, con conseguente riduzione dei costi operativi. |
Sicurezza | Evita i rischi di ustioni, incendi o fuoriuscite associati all'olio caldo o all'acqua. |
Versatilità | Adatto per un'ampia gamma di materiali che richiedono velocità di raffreddamento controllate. |
Coerenza e affidabilità | Garantisce proprietà meccaniche uniformi come durezza, resistenza e tenacità. |
Efficienza energetica | Richiede meno energia rispetto ai sistemi di tempra liquida, riducendo il consumo energetico. |
Pronti ad ottimizzare il vostro processo di trattamento termico? Contattaci oggi per scoprire come la tempra in aria può apportare vantaggi alle vostre operazioni!