La deposizione sotto vuoto è una tecnica versatile utilizzata per depositare film sottili o rivestimenti su superfici in un ambiente controllato, tipicamente in condizioni di vuoto. Lo spessore dello strato depositato può variare in modo significativo, da un singolo strato atomico (nanometri) a diversi millimetri, a seconda del processo specifico, dei materiali e dei parametri coinvolti. Fattori come la durata del processo, i livelli di energia, le proprietà dei materiali e le condizioni ambientali (ad esempio, pressione del vuoto, temperatura) giocano un ruolo fondamentale nel determinare lo spessore finale e la qualità del film depositato. Questa tecnica è ampiamente utilizzata nei settori che richiedono un controllo preciso delle proprietà dei film, come l'elettronica, l'ottica e i rivestimenti.
Punti chiave spiegati:
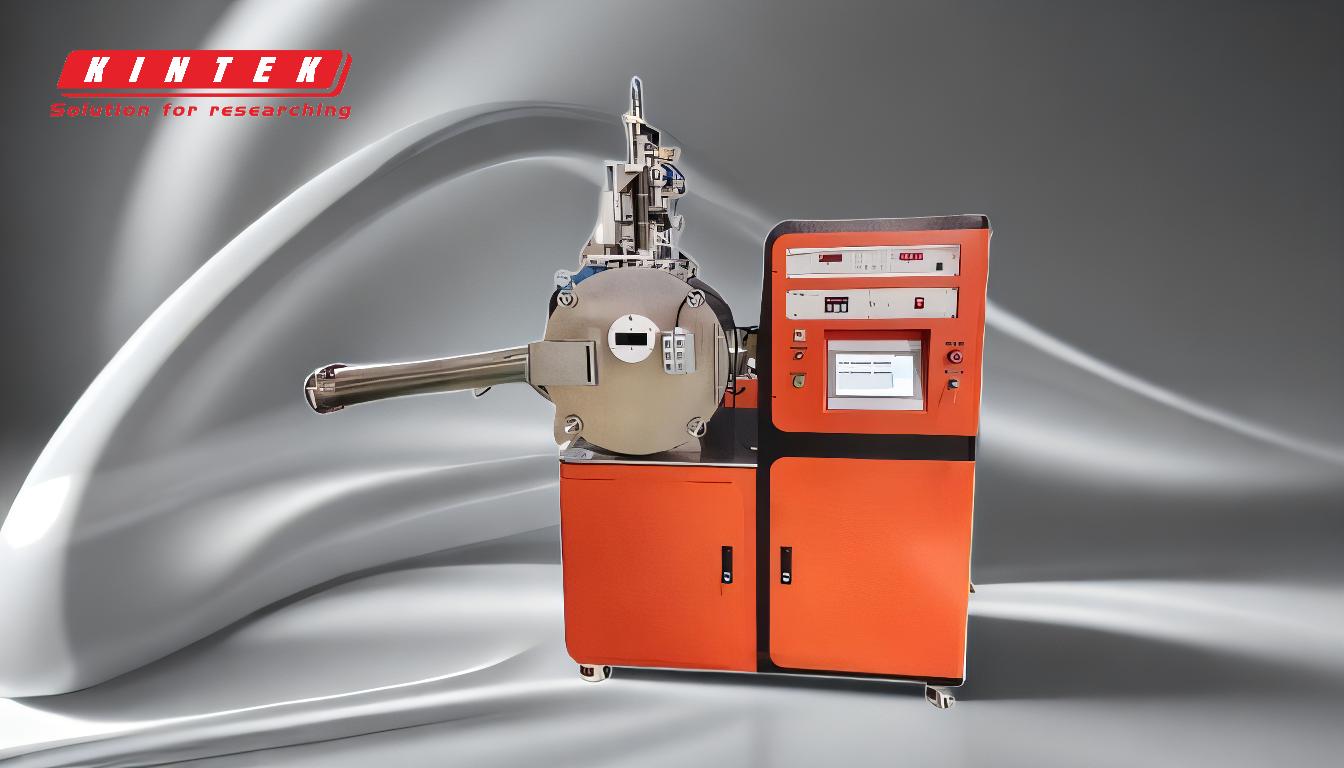
-
Gamma di spessori nella deposizione sotto vuoto:
- La deposizione sotto vuoto può produrre film con spessori che vanno da un singolo strato atomico (scala nanometrica) a diversi millimetri.
-
Ad esempio:
- Scala atomica/molecolare: In processi come la deposizione fisica da vapore (PVD) o la deposizione chimica da vapore a bassa pressione (LPCVD), gli strati vengono depositati atomo per atomo o molecola per molecola, ottenendo film estremamente sottili (nanometri).
- Scala macroscopica: In alcune applicazioni, come i rivestimenti protettivi o le finiture decorative, possono essere depositati strati più spessi (da micrometri a millimetri).
-
Fattori che influenzano lo spessore:
-
Lo spessore del film depositato è influenzato da diversi fattori chiave:
- Durata del processo: Tempi di deposizione più lunghi producono generalmente film più spessi.
- Livelli di energia: Livelli di energia più elevati delle particelle di rivestimento (ad esempio, da decine a migliaia di elettronvolt nello sputtering) possono aumentare la velocità di deposizione e influire sullo spessore.
- Proprietà del materiale: La massa e il peso molecolare del materiale di partenza influenzano la velocità con cui evapora o schizza, incidendo sullo spessore.
- Pressione del vuoto: Un grado di vuoto più elevato migliora il percorso libero delle molecole del materiale di partenza, portando a una deposizione più uniforme e controllata.
- Preparazione del substrato: La rugosità e la pulizia della superficie del substrato possono influenzare l'uniformità e l'adesione del film depositato.
-
Lo spessore del film depositato è influenzato da diversi fattori chiave:
-
Considerazioni specifiche sul processo:
- Sputtering: Lo spessore del metallo depositato nello sputtering dipende dalla durata del ciclo e dalla potenza applicata al bersaglio. Una potenza maggiore e cicli più lunghi producono film più spessi.
- Evaporazione termica: In questo processo, la velocità di evaporazione del materiale di partenza, insieme alla pressione del vuoto e alla velocità di rotazione del substrato, determina lo spessore e l'uniformità del film.
- Deposizione chimica da vapore (CVD): Nell'LPCVD, la velocità di deposizione e lo spessore sono influenzati dalle reazioni chimiche che avvengono sulla superficie del substrato, nonché dalle condizioni di temperatura e pressione.
-
Qualità e prestazioni dei film sottili:
-
La qualità del film depositato è fondamentale per le sue prestazioni nelle applicazioni. I fattori chiave che influenzano la qualità sono:
- Purezza del materiale di partenza: Le impurità possono causare difetti nel film.
- Temperatura e pressione di deposizione: Un controllo adeguato garantisce film uniformi e di alta qualità.
- Preparazione della superficie del substrato: Una superficie liscia e pulita del substrato favorisce una deposizione uniforme e una forte adesione.
-
La qualità del film depositato è fondamentale per le sue prestazioni nelle applicazioni. I fattori chiave che influenzano la qualità sono:
-
Applicazioni e implicazioni:
-
La deposizione sotto vuoto è utilizzata in un'ampia gamma di settori, tra cui:
- Elettronica: Per la creazione di transistor a film sottile, dispositivi semiconduttori e strati conduttivi.
- Ottica: Per rivestimenti antiriflesso, specchi e filtri ottici.
- Rivestimenti: Per finiture resistenti all'usura, alla corrosione e decorative.
- La capacità di controllare lo spessore del film a livello atomico rende la deposizione sotto vuoto una tecnologia fondamentale per la produzione e la ricerca avanzata.
-
La deposizione sotto vuoto è utilizzata in un'ampia gamma di settori, tra cui:
Comprendendo questi punti chiave, gli acquirenti di apparecchiature e materiali di consumo possono prendere decisioni informate sui materiali e sui processi necessari per ottenere spessori e proprietà specifici per le loro applicazioni.
Tabella riassuntiva:
Aspetto | Dettagli |
---|---|
Gamma di spessore | Da nanometri (scala atomica) a millimetri (scala macroscopica) |
Fattori chiave | Durata del processo, livelli di energia, proprietà del materiale, pressione del vuoto, preparazione del substrato |
Esempi di processo | Sputtering, evaporazione termica, deposizione chimica da vapore (CVD) |
Applicazioni | Elettronica (transistor, semiconduttori), Ottica (specchi, filtri), Rivestimenti (antiusura, decorativi) |
Avete bisogno di soluzioni precise per la deposizione sotto vuoto? Contattate i nostri esperti oggi stesso per discutere le vostre esigenze!