Informazioni sul forno fusorio a induzione a levitazione sotto vuoto
Esplora i componenti di un forno fusorio a induzione a levitazione sottovuoto, tra cui il corpo del forno, l'alimentazione a media frequenza, il sistema a vuoto, il sistema di raffreddamento e il sistema di controllo elettrico. Scoprite come ogni elemento contribuisce all'efficienza e alla precisione dei processi di fusione dei metalli.
I forni di fusione a induzione sotto vuoto (VIM) si sono evoluti dalla lavorazione specializzata di leghe esotiche all'uso più comune in vari settori, compresa la produzione di acciai inossidabili e altri metalli. Questi forni operano in condizioni di vuoto, offrendo un controllo preciso sul processo di fusione.
Come funziona un forno a induzione sotto vuoto?
Il materiale viene caricato nel forno a induzione sotto vuoto, dove viene applicata la corrente per avviare la fusione. Vengono aggiunte altre cariche per raggiungere la capacità di fusione desiderata. Il metallo fuso viene raffinato in condizioni di vuoto, con regolazioni effettuate per ottenere una chimica di fusione precisa.
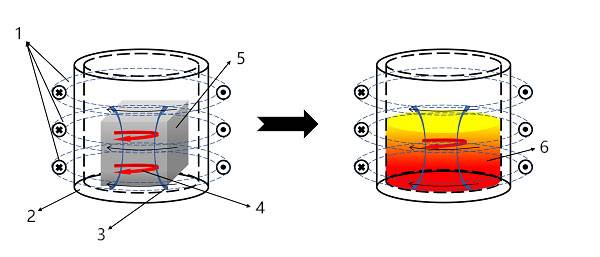
Componenti e funzioni principali
Oltre al corpo del forno e al sistema di vuoto, un forno di fusione a induzione sottovuoto è dotato di componenti essenziali come l'alimentatore a media frequenza, il sistema di controllo elettrico e il sistema di raffreddamento. Questi componenti lavorano insieme per fornire l'energia necessaria alla fusione, evitando il surriscaldamento e garantendo l'integrità strutturale.
In base ai requisiti specifici del processo, possono essere aggiunti componenti ausiliari come carrelli di trasmissione, meccanismi delle porte del forno e finestre di osservazione. Per le applicazioni con alti livelli di impurità, un sistema di filtraggio dei gas è essenziale per mantenere la purezza del metallo.
Vantaggi dei forni fusori a induzione sottovuoto
La struttura compatta dei forni VIM, con solo la parte di fusione racchiusa nella camera a vuoto, consente un migliore controllo dei livelli di vuoto e tempi di evacuazione più rapidi. Caratteristiche come l'agitazione elettromagnetica assicurano una miscelazione uniforme degli elementi aggiunti in tutto il bagno fuso, mantenendo una temperatura costante.
L'inclusione di setti filtranti e di altre misure migliora la purezza del metallo, attenuando l'impatto delle impurità. Il rilevamento e la riparazione delle perdite da vuoto sono semplificati grazie al volume ridotto del forno, riducendo i tempi di inattività per la manutenzione.
Precisione e controllo
I forni fusori a induzione sottovuoto offrono un controllo preciso della temperatura grazie a sistemi di controllo elettrico avanzati. Gli utenti possono monitorare il processo di fusione in tempo reale, garantendo precisione e coerenza. Il sistema di raffreddamento centralizzato regola le temperature di fusione, migliorando il controllo del processo e la qualità del prodotto.
Applicazioni e flessibilità
I forni VIM sono disponibili in un'ampia gamma di dimensioni, dalle piccole unità adatte agli esperimenti su scala di grammo ai modelli più grandi per la produzione industriale. Questa versatilità consente agli utenti di regolare le dimensioni dei lotti in base alle loro esigenze specifiche.
Eliminazione dei gas e prevenzione dell'ossidazione
Uno dei principali vantaggi della fusione a induzione sotto vuoto è la rimozione dei gas dai metalli fusi. Questo processo impedisce una rapida ossidazione, garantendo la purezza e la qualità del prodotto finale.
In conclusione, i forni fusori a induzione sottovuoto svolgono un ruolo fondamentale nei moderni processi di fusione dei metalli, offrendo un controllo preciso, una maggiore purezza e flessibilità nella produzione.
Efficienza e flessibilità
Approfondite la gamma di forni sottovuoto disponibili, dalle unità su piccola scala adatte a lotti di livello grammo ai forni più grandi che possono ospitare lotti di diverse dimensioni. Scoprite come questa versatilità consenta agli utenti di ottimizzare i processi produttivi.
Automazione e controllo avanzati:
I nostri forni sottovuoto sono dotati di sistemi di automazione e controllo avanzati, che consentono di gestire e monitorare con precisione i processi. L'interfaccia di facile utilizzo consente di programmare e regolare senza problemi i vari parametri, garantendo prestazioni ed efficienza ottimali. Grazie ai dati e alla diagnostica in tempo reale, è possibile prendere decisioni informate, rilevare le anomalie e ottimizzare i processi produttivi per ottenere la massima resa.
Efficienza energetica e sostenibilità:
Progetti per il vuoto
I forni a vuoto per la lavorazione a bassa temperatura possono essere batch o continui, indipendenti, integrati in sistemi di forni a vuoto continui o un "modulo" separato incorporato in un sistema cellulare. Ad esempio, il funzionamento di base di un forno a vuoto batch è il seguente:
- Le pompe da vuoto meccaniche, opzionalmente dotate di soffianti, producono livelli di vuoto fino a 1,3 x 10-3 mbar (0,001 torr) con 6,7 x 10-3 mbar (0,005 torr) comuni. Questo risultato viene normalmente raggiunto entro 10-30 minuti dall'inizio del ciclo, a seconda delle dimensioni dei sistemi di pompaggio e della natura di eventuali contaminanti presenti sul carico di lavoro.
- L'unità viene quindi riempita con una pressione negativa compresa tra 66,7 x 101 mbar (500 torr) e una pressione positiva di 0,10 bar (1,5 psig) con un gas inerte come azoto, argon o una miscela di azoto/idrogeno (3% al massimo) e inizia il riscaldamento.
- I doppi cicli di pompaggio sono spesso vantaggiosi per accelerare il tempo complessivo del ciclo. Dopo aver raggiunto il setpoint e l'immersione in temperatura, viene avviato il ciclo di raffreddamento.
Caratteristiche del forno a vuoto
I forni a vuoto KinTek offrono un controllo preciso della temperatura, un'eccellente uniformità della temperatura e un'ampia gamma di applicazioni per laboratori, università e qualsiasi applicazione di produzione su piccola scala che utilizza modelli di forni industriali.
Ogni forno a vuoto standard e personalizzato offre le seguenti caratteristiche e vantaggi:
- Eccellente precisione e uniformità della temperatura
- Isolamento in fibra ceramica ad alta efficienza energetica
- Funzione di sicurezza per lo spegnimento automatico
Forni a vuoto personalizzati
Ottenete un forno per vuoto ad alta temperatura costruito appositamente per soddisfare le vostre esigenze applicative. I rappresentanti esperti e competenti di KinTek possono aiutarvi a progettare o costruire un forno personalizzato per soddisfare le vostre esatte specifiche o esigenze applicative.
Questa gamma completa di caratteristiche e opzioni assicura che i nostri forni per vuoto forniscano l'efficienza e la flessibilità necessarie per un'ampia varietà di applicazioni di laboratorio e di produzione su piccola scala.
Controllo di precisione della temperatura
Scoprite come il sistema di controllo elettrico dei forni fusori a induzione sottovuoto assicura un controllo preciso della temperatura durante tutto il processo di fusione. Scoprite il ruolo del sistema di raffreddamento nel mantenere le temperature di fusione ottimali e nel prevenire l'ossidazione.
Il riscaldamento a induzione è un processo in cui le correnti parassite indotte riscaldano i materiali conduttori. Questo riscaldamento può essere utilizzato per fondere metalli e produrre leghe. La fusione a induzione sotto vuoto offre un'interessante combinazione di atmosfera controllata (vuoto o gas inerte) e controllo preciso del processo di fusione.
Descrizione del forno di sinterizzazione sotto vuoto
Un forno di sinterizzazione sotto vuoto è un tipo di forno in cui gli articoli riscaldati vengono sottoposti a sinterizzazione in un ambiente sotto vuoto. Questo forno è fondamentale in diversi processi industriali, in particolare nella metallurgia delle polveri.
Il processo di sinterizzazione è molto sensibile alle variazioni di temperatura. Una deviazione di pochi gradi Celsius può avere un impatto significativo sulla qualità del prodotto finale. Per questo motivo, è indispensabile un controllo rigoroso della temperatura di sinterizzazione, con deviazioni che in genere non superano un intervallo specificato compreso tra ±3℃ e ±5℃.
Vantaggi delle apparecchiature a induzione sottovuoto
Rispetto ai metodi di fusione tradizionali, le apparecchiature a induzione sottovuoto offrono notevoli vantaggi nel controllo del processo. Grazie ai progressi della tecnologia informatica, i moderni forni a induzione sottovuoto integrano sistemi di controllo intelligenti che semplificano le operazioni, riducono i costi di manodopera e migliorano la precisione.
I futuri sviluppi dei sistemi di controllo intelligenti miglioreranno ulteriormente le capacità delle apparecchiature a induzione sottovuoto. Questi sistemi consentiranno un controllo preciso delle temperature di fusione, faciliteranno l'aggiunta automatica di leghe a intervalli predeterminati e snelliranno l'intero processo di fusione. Inoltre, l'integrazione di una raccolta dati completa e di analisi in tempo reale consentirà agli operatori di prendere decisioni informate e di ottimizzare i parametri di processo durante la fusione.
Componenti del forno fusorio a induzione sottovuoto
Il forno fusorio a induzione sottovuoto comprende diversi componenti essenziali, tra cui:
- Corpo del forno a vuoto: Fornisce la camera in cui avviene la fusione sotto vuoto o in atmosfera controllata.
- Potenza a media frequenza: Fornisce l'energia necessaria per il riscaldamento a induzione.
- Sistema a vuoto: Mantiene il livello di vuoto desiderato all'interno della camera del forno.
- Sistema di raffreddamento: Previene il surriscaldamento e mantiene le temperature di fusione ottimali.
- Sistema di controllo elettrico: Consente un controllo preciso della temperatura e del funzionamento complessivo del forno.
Caratteristiche e vantaggi principali
- Controllo preciso della temperatura: Il sistema di controllo elettrico assicura una regolazione precisa delle temperature di fusione, migliorando la qualità e la consistenza del prodotto finale.
- Rimozione del gas: L'ambiente sottovuoto elimina i gas dai metalli fusi, impedendo una rapida ossidazione e preservando l'integrità della lega.
- Dimensioni flessibili dei lotti: I forni sottovuoto sono disponibili in varie dimensioni, per adattarsi a una gamma di lotti di dimensioni diverse, dalla piccola scala alle grandi applicazioni industriali.
- Sistema di raffreddamento centralizzato: Il sistema di raffreddamento dissipa efficacemente il calore, mantenendo stabili le temperature di esercizio e prolungando la durata delle apparecchiature.
In conclusione, i forni fusori a induzione sottovuoto offrono una precisione e un controllo senza pari nei processi di fusione dei metalli. Sfruttando tecnologie avanzate e sistemi di controllo intelligenti, questi forni facilitano una produzione efficiente, garantiscono la qualità del prodotto e aprono la strada a futuri progressi nella lavorazione metallurgica.
Principio di funzionamento e significato storico
Scoprite le radici storiche della tecnologia di fusione a induzione sotto vuoto, risalendo alle sue origini nell'industria aerospaziale e metallurgica. Scoprite come questa tecnologia si è evoluta fino a diventare una pietra miliare nella produzione di leghe ad alte prestazioni per diverse applicazioni.
Fusione a induzione sotto vuoto: Un percorso verso i materiali avanzati
La fusione a induzione sotto vuoto (VIM) è una tecnologia fondamentale nel campo della metallurgia, in particolare nella produzione di leghe specializzate ed esotiche. Inizialmente sviluppata per la lavorazione delle superleghe, la sua gamma di applicazioni si è estesa fino a comprendere gli acciai inossidabili e vari altri metalli. Questa espansione è dovuta in gran parte alla crescente domanda di materiali avanzati in diversi settori industriali.
Il processo di fusione a induzione sottovuoto
Alla base del VIM c'è il principio della fusione dei metalli sotto vuoto, con l'induzione elettromagnetica che funge da fonte di energia primaria. Il processo prevede la generazione di correnti elettriche parassite all'interno del metallo, agevolate da una bobina di induzione che trasporta corrente alternata. Queste correnti, a loro volta, inducono effetti di riscaldamento, portando infine alla fusione della carica metallica.
La rapida evoluzione della tecnologia VIM affonda le sue radici nella ricerca di materiali in lega ad alta temperatura da parte dell'industria aerospaziale. Questi materiali, essenziali per le apparecchiature aerospaziali, missilistiche, missilistiche e per l'energia atomica, richiedevano innovazioni nei processi di fusione. I forni VIM sono emersi come soluzione, consentendo la fusione di leghe a base di nichel, ferro e cobalto in condizioni di vuoto. Questo ambiente riduce efficacemente la presenza di elementi di gap come O2, N2 e H2, garantendo la rimozione di inclusioni non metalliche e impurità dannose come Pb, Bi, Sb, Cu, Sn e Te.
Applicazioni della fusione a induzione sottovuoto
La versatilità della VIM si estende a diverse applicazioni nel panorama metallurgico:
- Raffinazione di metalli e leghe di elevata purezza.
- Produzione di elettrodi per processi di rifusione.
- Produzione di master stick di lega, fondamentali in procedure come la microfusione.
- Fusione di componenti critici per i motori degli aerei.
Evoluzione storica
La genesi della fusione a induzione sotto vuoto risale al 1920, quando è stato realizzato il primo prototipo. Nella sua essenza, la VIM sfrutta l'induzione elettromagnetica per indurre correnti parassite all'interno dei conduttori, riscaldando e fondendo il metallo. Nel corso dei decenni, questa tecnologia ha trovato un'utilità indispensabile sia nel settore aerospaziale che in quello nucleare, guidando i progressi nella scienza e nell'ingegneria dei materiali.
In sintesi, la fusione a induzione sotto vuoto è una testimonianza dell'ingegno umano, che facilita la produzione di materiali che alimentano le moderne meraviglie tecnologiche. Dalle sue umili origini al suo attuale status di pietra miliare dell'innovazione metallurgica, la VIM continua a plasmare il panorama della produzione di materiali avanzati.
Applicazioni in tutti i settori
Esplorate le vaste applicazioni della tecnologia di fusione a induzione sotto vuoto nei settori aerospaziale, elettronico, energetico e altro ancora. Scoprite come questa tecnologia migliora le proprietà e la qualità dei materiali essenziali per l'ingegneria e la produzione avanzate.
La tecnologia di fusione a induzione sottovuoto (VIM) si è evoluta in modo significativo: originariamente sviluppata per la lavorazione di leghe specializzate ed esotiche, oggi è diventata sempre più comune, in quanto i materiali avanzati trovano applicazioni più ampie. Inizialmente utilizzata per materiali come le superleghe, la VIM ha esteso la sua utilità agli acciai inossidabili e a vari altri metalli.
Il rapido sviluppo della tecnologia VIM è strettamente legato alla domanda di materiali in lega ad alta temperatura in settori come quello aerospaziale, missilistico, missilistico e dell'energia atomica. Le superleghe, fondamentali per queste applicazioni, traggono grande vantaggio dalle capacità dei forni VIM.
Come funzionano i forni a induzione sottovuoto
In un forno a induzione sotto vuoto, il materiale viene caricato sotto vuoto e l'energia viene applicata per fondere la carica. Vengono effettuate cariche aggiuntive per raggiungere la capacità di fusione desiderata e il metallo fuso viene raffinato sotto vuoto. Questo processo consente di regolare con precisione la chimica della fusione fino a raggiungere la composizione desiderata.
Vantaggi della fusione a induzione sotto vuoto
-
Alta purezza e qualità: Il VIM eccelle nella produzione di materiali di elevata purezza e qualità. L'ambiente sottovuoto elimina il rischio di contaminazione da ossigeno, azoto e altri gas presenti nell'atmosfera. Il risultato è una fusione più pulita e omogenea, priva di inclusioni e impurità dannose che potrebbero compromettere le proprietà meccaniche.
-
Atmosfera controllata: All'interno della camera da vuoto, l'atmosfera è strettamente controllata, con l'introduzione solo di gas specifici a pressioni precise. Questo livello di controllo consente di gestire con precisione la composizione chimica del materiale fuso e di evitare ossidazioni o reazioni indesiderate con i gas ambientali.
I forni fusori a induzione sottovuoto sono fondamentali nel campo della metallurgia sottovuoto, in quanto svolgono un ruolo significativo nella produzione di leghe e acciai speciali cruciali per l'industria aerospaziale, missilistica, missilistica, dell'energia atomica e dell'elettronica. In particolare, una parte considerevole dei prodotti di questi settori è realizzata con la tecnologia VIM.
Diversi materiali, tra cui l'acciaio inossidabile, l'acciaio resistente al calore, l'acciaio ultraresistente, l'acciaio per utensili, l'acciaio per cuscinetti, i materiali magnetici, le leghe elastiche e le leghe di espansione, vengono fusi con forni di fusione a induzione sotto vuoto per garantire prestazioni e qualità ottimali. Questi forni migliorano la lavorabilità a caldo e le proprietà meccaniche delle superleghe a base di nichel, cobalto e ferro, rendendole indispensabili nei processi di ingegneria e produzione avanzati.
Vantaggi rispetto ai metodi tradizionali
La tecnologia di fusione a induzione sottovuoto si distingue come metodo principale per la fusione dei metalli grazie ai suoi numerosi vantaggi rispetto agli approcci tradizionali. Confrontando l'efficienza, la sostenibilità e la purezza dei materiali con i metodi tradizionali, risulta evidente perché la fusione a induzione sottovuoto è sempre più favorita in vari settori industriali.
Efficienza energetica e sostenibilità ambientale
La tecnologia di fusione a induzione sottovuoto (VIM) rappresenta un significativo balzo in avanti in termini di efficienza energetica e sostenibilità ambientale rispetto ai metodi di fusione tradizionali. A differenza degli approcci convenzionali, la VIM opera in un ambiente sottovuoto, che minimizza la perdita di calore e riduce il consumo energetico. Questo utilizzo efficiente dell'energia non solo abbassa i costi di produzione, ma contribuisce anche a rendere più ecologico il processo produttivo, riducendo le emissioni di carbonio e gli sprechi energetici.
Purezza e qualità dei materiali
Uno dei principali vantaggi del VIM è la capacità di produrre materiali di eccezionale purezza e qualità. L'ambiente sotto vuoto elimina la presenza di ossigeno, azoto e altri gas che potrebbero contaminare il metallo fuso. Di conseguenza, il VIM produce fusioni più pulite e omogenee, prive di impurità e inclusioni dannose. Questa purezza migliora le proprietà meccaniche e le prestazioni complessive dei materiali risultanti, rendendoli altamente desiderabili per varie applicazioni.
Atmosfera controllata
Nella camera a vuoto delle apparecchiature VIM, l'atmosfera è meticolosamente controllata, consentendo una regolazione precisa della composizione e della pressione dei gas. Introducendo solo gas specifici a pressioni precise, VIM assicura uno stretto controllo sulla composizione chimica del materiale fuso, riducendo al minimo il rischio di ossidazioni o reazioni indesiderate con i gas ambientali. Questo livello di controllo è fondamentale per produrre leghe con proprietà costanti e ridurre al minimo gli sprechi di materiale.
Efficienza e flessibilità del processo
Oltre ai vantaggi ambientali e qualitativi, il VIM offre un'efficienza e una flessibilità di processo senza pari. I suoi cicli di riscaldamento rapidi e il riscaldamento uniforme delle cariche metalliche aumentano significativamente i tassi di produzione e riducono i tassi di difettosità. Inoltre, la versatilità del VIM consente di fondere con facilità diversi metalli e leghe, facilitando il passaggio rapido da un materiale all'altro e consentendo l'arresto immediato, se necessario. Questa agilità nella produzione migliora l'efficienza operativa e l'adattabilità alle mutevoli esigenze produttive.
Applicazioni e prospettive future
L'adozione diffusa della tecnologia di fusione a induzione sottovuoto in tutti i settori industriali sottolinea il suo immenso potenziale e la sua versatilità. Dalla ricerca sperimentale su piccola scala alla produzione industriale su larga scala, la VIM ha dimostrato la sua efficacia e affidabilità. La semplicità di funzionamento e le rapide temperature di fusione ne fanno una scelta privilegiata per i produttori che cercano precisione e coerenza nei loro processi produttivi. Con l'avanzare della tecnologia, si prevede che l'applicazione della VIM si espanderà ulteriormente, promuovendo l'innovazione e l'efficienza nei processi di fusione e raffinazione dei metalli.
Sinterizzazione sotto vuoto: Migliorare l'efficienza e la qualità
Oltre alla fusione a induzione sottovuoto, la sinterizzazione sottovuoto emerge come un altro processo fondamentale per migliorare l'efficienza e la qualità dei prodotti nella produzione dei metalli. Sinterizzando le polveri metalliche a temperature inferiori al punto di fusione in un ambiente sotto vuoto, la sinterizzazione sotto vuoto offre diversi vantaggi. Elimina le reazioni tra metalli e gas, migliora la densificazione e riduce le temperature di sinterizzazione, risparmiando energia e prolungando la vita dei forni di sinterizzazione. Il risultato è la produzione di prodotti metallici di alta qualità con proprietà meccaniche migliori e un consumo energetico ridotto.
In conclusione, la fusione a induzione e la sinterizzazione sottovuoto rappresentano tecnologie all'avanguardia che offrono numerosi vantaggi rispetto ai metodi di fusione tradizionali. Dall'efficienza energetica alla purezza dei materiali, dalla flessibilità dei processi alla sostenibilità ambientale, queste tecniche avanzate stanno guidando l'innovazione e ridisegnando il panorama della produzione dei metalli. Poiché le industrie continuano a dare priorità alla sostenibilità e alla qualità, l'adozione di processi basati sul vuoto come il VIM e la sinterizzazione sottovuoto è destinata ad accelerare, inaugurando una nuova era di efficienza ed eccellenza nella produzione dei metalli.
Caratteristiche principali dei forni fusori a induzione sottovuoto
I forni fusori a induzione sottovuoto sono fondamentali per i processi metallurgici e offrono una serie di caratteristiche studiate su misura per un controllo preciso e una maggiore produttività. Ecco un'esplorazione completa dei loro componenti chiave e dei loro progressi:
Componenti strutturali
Il forno comprende una camicia d'acciaio ermetica raffreddata ad acqua, progettata per sostenere le condizioni di vuoto richieste durante il processo. All'interno di questo involucro, il metallo viene fuso in un crogiolo all'interno di una bobina di induzione raffreddata ad acqua. Inoltre, l'interno del forno è tipicamente rivestito con refrattari adatti a resistere a temperature estreme.
Miglioramenti del processo
1. Controllo ambientale
- La colata di metallo fuso può essere eseguita sotto vuoto o in ambienti con gas inerte, garantendo condizioni ottimali per la formazione della lega e il mantenimento della purezza.
2. Caratteristiche aggiuntive
- I forni possono integrare meccanismi di inclinazione e colata, camere di colata e porte di campionamento per facilitare le diverse esigenze di produzione.
- Le strutture di movimentazione degli stampi consentono una lavorazione automatizzata o semi-automatizzata, talvolta incorporando sistemi di interblocco del vuoto per un funzionamento senza interruzioni.
Tendenze di sviluppo future
L'evoluzione delle apparecchiature di fusione a induzione sottovuoto riflette una transizione verso strutture multifunzionali in grado di accogliere diversi processi tecnologici. Si prevede che le configurazioni modulari domineranno, consentendo combinazioni personalizzate di componenti per soddisfare in modo efficiente i requisiti di processo specifici.
Controllo e automazione di precisione
L'integrazione di tecnologie avanzate come i sistemi informatici e l'acquisizione intelligente dei segnali consente un controllo preciso dei processi. Le interfacce uomo-macchina semplificano il funzionamento, riducendo i costi di manodopera e migliorando la semplicità operativa.
Sistemi ausiliari
Oltre ai componenti principali, i sistemi ausiliari come gli alimentatori, le unità di controllo e i sistemi di raffreddamento svolgono un ruolo fondamentale. Questi sistemi garantiscono l'apporto di energia per la fusione e prevengono il surriscaldamento dei componenti critici.
Considerazioni strutturali
L'attenzione alla progettazione strutturale è fondamentale per evitare lo scarico del vuoto. L'isolamento di tutti i corpi carichi all'interno del guscio del forno e l'eliminazione degli spigoli vivi nella progettazione dell'induttore sono fondamentali per garantire un funzionamento ininterrotto.
Vantaggi chiave
- Fusione di alcune leghe di titanio: Le condizioni di vuoto consentono la fusione di leghe di titanio, ampliando le possibilità di applicazione del forno.
- Prevenzione delle reazioni chimiche: Gli ambienti sotto vuoto proteggono i metalli e le leghe fuse da reazioni chimiche indesiderate con inclusioni non metalliche.
- Rimozione dei gas nocivi: Lo stato di vuoto facilita l'eliminazione di gas disciolti e inquinanti nocivi dal metallo fuso liquido, garantendo la purezza del materiale.
In conclusione, i forni fusori a induzione sottovuoto incarnano versatilità e precisione, guidando i progressi nei processi metallurgici attraverso un design innovativo e l'integrazione tecnologica.
Vantaggi ambientali e prestazionali
La fusione a induzione sottovuoto (VIM) offre significativi vantaggi ambientali e prestazionali, che la rendono il metodo preferito per la produzione di materiali di elevata purezza con proprietà superiori.
Alta purezza e qualità
La VIM eccelle nella produzione di materiali di eccezionale purezza e qualità. Operando in un ambiente sottovuoto, il VIM elimina il rischio di contaminazione da gas atmosferici come ossigeno e azoto. Ciò garantisce una fusione più pulita e omogenea, priva di inclusioni e impurità dannose che potrebbero compromettere l'integrità meccanica del materiale. Di conseguenza, le leghe ottenute presentano proprietà meccaniche e caratteristiche prestazionali migliori.
Atmosfera controllata
All'interno della camera da vuoto, l'atmosfera è meticolosamente controllata, consentendo una precisa regolazione della composizione e della pressione dei gas. Questo livello di controllo è fondamentale per ottenere la composizione chimica desiderata del materiale fuso, evitando al contempo ossidazioni o reazioni indesiderate con i gas ambientali. Di conseguenza, il VIM consente di produrre materiali con proprietà chimiche costanti e reattività minima, garantendo prestazioni superiori in varie applicazioni.
Vantaggi riassunti
I vantaggi dell'utilizzo di un forno fusorio a induzione sottovuoto sono molteplici:
-
Eliminazione dei gas: Il VIM opera a pressioni estremamente basse, in genere intorno a 0,000001 atmosfere. Questo ambiente facilita la rimozione di gas ed elementi volatili indesiderati dalle materie prime durante il processo di fusione, garantendo la produzione di leghe di elevata purezza.
-
Analisi chimiche precise: L'assenza di atmosfera nella camera a vuoto consente un controllo eccezionale e riproducibile della composizione chimica dei materiali fusi. Questa precisione consente di produrre leghe con composizioni personalizzate e proprietà desiderate, migliorando l'efficienza complessiva del processo e la qualità del prodotto.
-
Controllo di processo superiore: Il VIM offre un controllo indipendente su pressione, temperatura e agitazione induttiva, garantendo un controllo di processo senza precedenti. Questa flessibilità consente di sviluppare pratiche di fusione ottimizzate specifiche per ogni composizione di lega, migliorando ulteriormente le prestazioni e la consistenza dei materiali prodotti.
Oltre ai benefici ambientali, i vantaggi di un forno a induzione sottovuoto si estendono alla lavorazione di vari metalli e leghe:
- Miglioramento della purezza: L'assenza di inquinamento da aria e scorie nei forni a induzione sottovuoto contribuisce alla produzione di leghe relativamente pure con livelli di prestazioni elevati.
- Rimozione dei gas: Il funzionamento sotto vuoto consente di ridurre il contenuto di gas nell'acciaio fuso e nelle leghe, ottenendo materiali con concentrazioni di gas inferiori e proprietà migliori.
- Prevenzione dell'ossidazione: La lavorazione dei metalli in un ambiente sottovuoto riduce il rischio di ossidazione, preservando l'integrità del materiale lavorato.
- Evaporazione delle impurità: Impurità come il piombo (Pb) e il bismuto (Bi) possono evaporare più facilmente nel vuoto, facilitando la purificazione del materiale durante il processo di fusione.
In conclusione,i forni di fusione a induzione sotto vuoto offrono una soluzione completa per la produzione di materiali di elevata purezza con caratteristiche prestazionali superiori, riducendo al contempo l'inquinamento ambientale e garantendo l'efficienza del processo.
CONTATTATECI PER UNA CONSULENZA GRATUITA
I prodotti e i servizi di KINTEK LAB SOLUTION sono stati riconosciuti da clienti di tutto il mondo. Il nostro personale sarà lieto di assistervi per qualsiasi richiesta. Contattateci per una consulenza gratuita e parlate con uno specialista del prodotto per trovare la soluzione più adatta alle vostre esigenze applicative!