L'incollaggio per diffusione è un processo di giunzione allo stato solido che avviene a temperature elevate, in genere comprese tra il 50% e il 75% del punto di fusione dei materiali da incollare.Questo processo si basa sulla diffusione atomica attraverso l'interfaccia dei materiali, facilitata da temperature elevate.La temperatura esatta dipende dai materiali specifici coinvolti, ma in genere rientra nell'intervallo tra 900 e 1400 ℃, come si vede in processi come la CVD (Chemical Vapor Deposition), dove il controllo della diffusione si ottiene a temperature elevate.
Punti chiave spiegati:
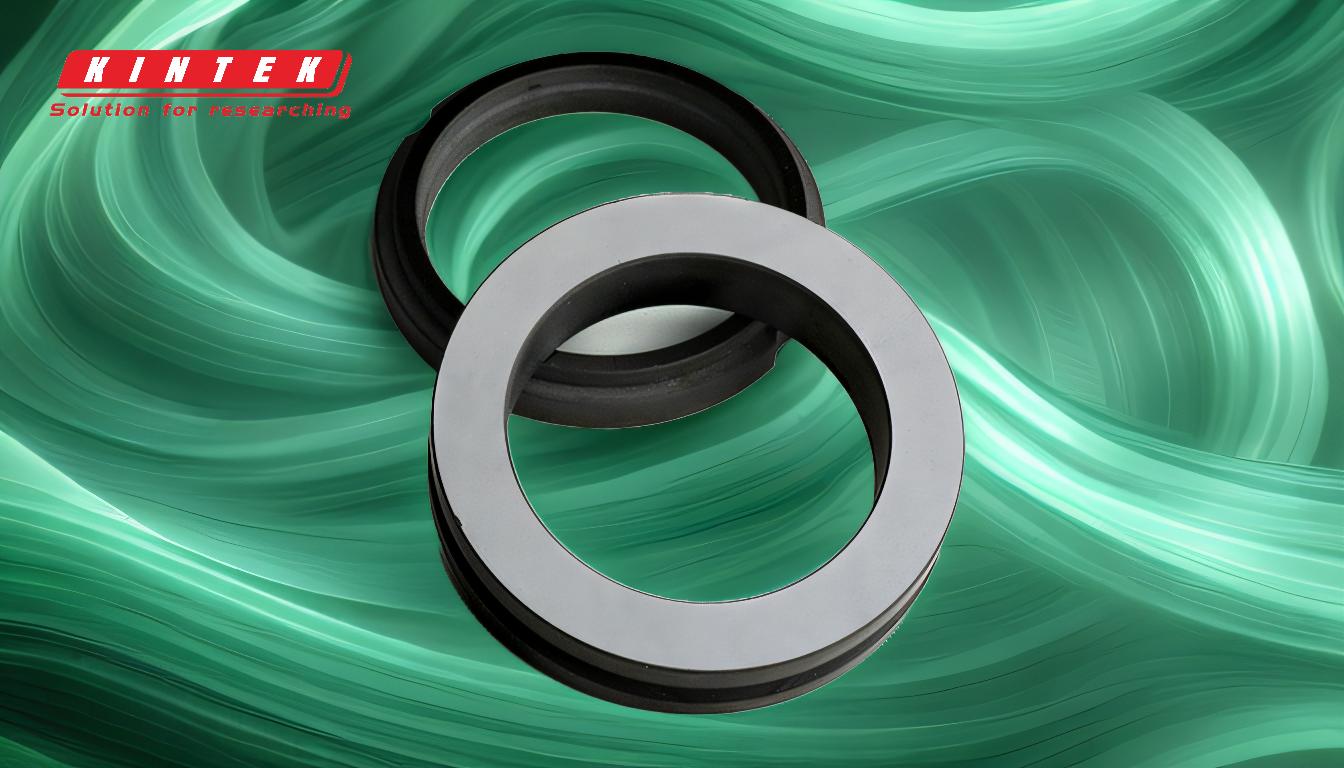
-
Intervallo di temperatura per il legame per diffusione:
- L'incollaggio per diffusione avviene tipicamente a temperature elevate, spesso tra il 50% e il 75% del punto di fusione dei materiali da incollare.Per molti metalli, ciò si traduce in un intervallo compreso tra circa 900 e 1400 ℃.
- Questo intervallo di temperatura garantisce che la diffusione atomica sia sufficientemente attiva da permettere ai materiali di legarsi senza raggiungere il loro punto di fusione.
-
Ruolo della temperatura nel controllo della diffusione:
- Alle alte temperature, la mobilità atomica aumenta, il che è essenziale per il legame per diffusione.Il processo si basa sul movimento degli atomi attraverso l'interfaccia dei materiali per creare un legame forte.
- Nella tecnologia CVD, ad esempio, il controllo della diffusione si ottiene a temperature elevate (da 900 a 1400 ℃), che corrispondono alle condizioni necessarie per un legame efficace per diffusione.
-
Considerazioni specifiche sul materiale:
- La temperatura esatta per l'incollaggio per diffusione varia a seconda dei materiali coinvolti.Ad esempio, le leghe di titanio possono richiedere temperature intorno ai 900-1000 ℃, mentre le superleghe a base di nichel possono richiedere temperature più vicine ai 1200-1400 ℃.
- La comprensione dei punti di fusione e delle caratteristiche di diffusione dei materiali è fondamentale per determinare la temperatura di legame ottimale.
-
Controllo cinetico e controllo della diffusione:
- Il controllo cinetico, che si effettua tipicamente a temperature più basse, si concentra sulla velocità delle reazioni chimiche.Al contrario, il controllo della diffusione, che avviene a temperature più elevate, enfatizza il movimento degli atomi attraverso le interfacce dei materiali.
- Per l'incollaggio per diffusione, il regime ad alta temperatura (da 900 a 1400 ℃) è necessario per garantire che i processi di diffusione dominino, portando a un legame forte e duraturo.
-
Implicazioni pratiche per gli acquirenti di apparecchiature e materiali di consumo:
- Quando si scelgono le apparecchiature per l'incollaggio per diffusione, è essenziale scegliere sistemi in grado di mantenere costantemente alte temperature nell'intervallo richiesto (da 900 a 1400 ℃).
- Anche i materiali di consumo, come le atmosfere protettive o i materiali di riempimento, devono essere scelti in base alla loro compatibilità con l'ambiente ad alta temperatura richiesto dall'incollaggio per diffusione.
Comprendendo questi punti chiave, gli acquirenti possono prendere decisioni informate sulle attrezzature e sui materiali necessari per il successo dei processi di incollaggio per diffusione.
Tabella riassuntiva:
Aspetto | Dettagli |
---|---|
Intervallo di temperatura | Da 900 a 1400 ℃ (50%-75% del punto di fusione del materiale) |
Ruolo dell'alta temperatura | Aumenta la diffusione atomica per un legame forte |
Esempi specifici di materiali | Leghe di titanio:900-1000 ℃, superleghe a base di nichel:1200-1400 ℃ |
Cinetica vs. Diffusione | Il controllo della diffusione richiede temperature elevate per il movimento degli atomi. |
Considerazioni sulle apparecchiature | I sistemi devono mantenere temperature elevate e costanti (900-1400 ℃). |
Avete bisogno di aiuto per scegliere l'attrezzatura giusta per l'incollaggio per diffusione? Contattate i nostri esperti oggi stesso !