Il processo di sinterizzazione è una tecnica di produzione fondamentale utilizzata per trasformare materiali in polvere in corpi solidi e densi applicando calore e pressione al di sotto del punto di fusione del materiale.Comporta diverse fasi, tra cui la preparazione di una miscela di polveri con un agente legante, la modellazione del materiale nella forma desiderata, il riscaldamento per rimuovere l'agente legante e la fusione delle particelle primarie per creare una massa unificata a bassa porosità.Questo processo è ampiamente utilizzato in settori come la metallurgia delle polveri e la ceramica per produrre componenti durevoli e ad alta resistenza.Le fasi principali comprendono la composizione, la compressione, il riscaldamento, la fusione delle particelle e la solidificazione, ognuna delle quali contribuisce alle proprietà del materiale finale.
Punti chiave spiegati:
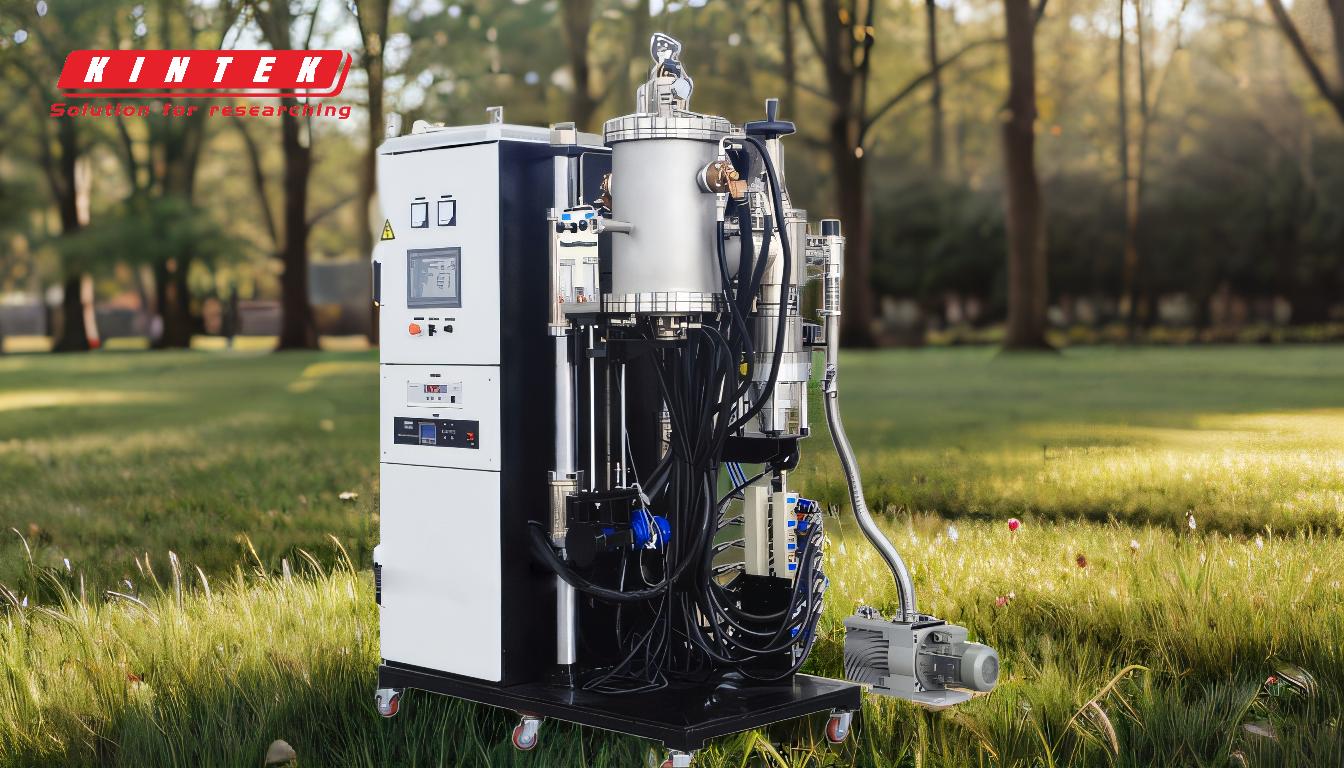
-
Preparazione della miscela di polveri:
- Composizione:Il processo inizia con la miscelazione di materiali primari (come polveri metalliche o ceramiche) con un agente legante (ad esempio, cera o polimero).L'agente legante aiuta le particelle di polvere ad aderire l'una all'altra, formando una miscela coesiva.
- Modellazione:La miscela di polveri viene quindi modellata nella forma desiderata utilizzando tecniche come la pressatura a freddo, la stampa 3D o altri metodi di formatura.In questo modo si crea una "parte verde", ovvero una struttura preliminare che mantiene la forma ma non è ancora completamente densa.
-
Compressione e formatura:
- Compressione:La parte verde viene compressa per ottenere la forma e la densità richieste.Questa fase assicura che le particelle siano strettamente impacchettate, riducendo la porosità e preparando il materiale per la fase di riscaldamento.
- Atmosfera controllata:In alcuni casi, la compressione avviene in atmosfera controllata per evitare l'ossidazione o la contaminazione che potrebbero influire sulle proprietà del materiale.
-
Riscaldamento e rimozione dell'agente legante:
- Riscaldamento iniziale:La parte verde viene riscaldata a una temperatura in cui l'agente legante evapora o brucia.Questa fase è fondamentale per eliminare eventuali materiali organici che potrebbero interferire con il processo di sinterizzazione.
- Controllo della temperatura:La temperatura viene controllata attentamente per garantire che l'agente legante venga completamente rimosso senza danneggiare il materiale primario.
-
Fusione e fusione delle particelle:
-
Temperatura di sinterizzazione:La temperatura viene quindi portata appena al di sotto del punto di fusione del materiale.A questo punto si verifica uno dei due processi:
- Sinterizzazione allo stato solido:Le particelle primarie iniziano a fondersi in superficie a causa della diffusione atomica, creando una struttura più densa.
- Sinterizzazione in fase liquida (LPS):Un agente legante intermedio, come il bronzo, fonde e scorre tra le particelle, legandole insieme mentre il materiale primario rimane solido.
- Densificazione:Le particelle si densificano e si fondono, riducendo la porosità e aumentando la resistenza e la durata del materiale.
-
Temperatura di sinterizzazione:La temperatura viene quindi portata appena al di sotto del punto di fusione del materiale.A questo punto si verifica uno dei due processi:
-
Solidificazione e raffreddamento:
- Fase di raffreddamento:Al termine del processo di sinterizzazione, il materiale viene lasciato raffreddare e solidificare in una massa unificata.Questa fase garantisce che il materiale mantenga la sua forma e le sue proprietà.
- Proprietà finali:Il prodotto finale è un materiale denso e a bassa porosità con proprietà meccaniche migliorate, come durezza, resistenza e durata.
-
Applicazioni e vantaggi:
- Uso industriale:La sinterizzazione è ampiamente utilizzata nella metallurgia delle polveri per la produzione di componenti metallici e nella produzione di ceramica per creare prodotti ceramici durevoli.
- Materiali ad alto punto di fusione:Questo processo è particolarmente utile per i materiali con punti di fusione estremamente elevati, come il tungsteno e il molibdeno, difficili da lavorare con le tecniche di fusione tradizionali.
- Personalizzazione:La sinterizzazione consente di produrre forme complesse e componenti personalizzati, rendendola un metodo di produzione versatile.
Seguendo queste fasi, il processo di sinterizzazione trasforma le polveri sfuse in materiali forti e densi, adatti a un'ampia gamma di applicazioni industriali.L'attento controllo di temperatura, pressione e atmosfera assicura che il prodotto finale soddisfi le specifiche e le prestazioni desiderate.
Tabella riassuntiva:
Fase | Dettagli chiave |
---|---|
Preparazione | Miscelare i materiali primari con un agente legante e modellarli in un "pezzo verde". |
Compressione | Comprimere la parte verde per ridurre la porosità e raggiungere la densità desiderata. |
Riscaldamento | Riscaldare per rimuovere l'agente legante e preparare la fusione delle particelle. |
Fusione delle particelle | Aumentare la temperatura per fondere le particelle tramite sinterizzazione allo stato solido o in fase liquida. |
Solidificazione | Raffreddare e solidificare in un materiale denso e a bassa porosità con proprietà migliorate. |
Applicazioni | Utilizzata nella metallurgia delle polveri e nella ceramica per ottenere componenti durevoli e ad alta resistenza. |
Scoprite come la sinterizzazione può migliorare il vostro processo di produzione... contattateci oggi stesso per una guida esperta!