I forni a resistenza e i forni a induzione vengono entrambi utilizzati per riscaldare i materiali, ma funzionano secondo principi fondamentalmente diversi. I forni a resistenza utilizzano la resistenza elettrica per generare calore, che viene poi trasferito al materiale attraverso conduzione, convezione o irraggiamento. I forni ad induzione, invece, sfruttano l’induzione elettromagnetica per generare calore direttamente all’interno del materiale stesso. Questa differenza fondamentale porta a variazioni in termini di efficienza, velocità di riscaldamento, controllo e applicazioni. I forni a resistenza sono generalmente più semplici ed economici per il riscaldamento stazionario, mentre i forni a induzione offrono un riscaldamento più rapido, una migliore efficienza energetica e un controllo preciso della temperatura, rendendoli ideali per applicazioni che richiedono un riscaldamento rapido o localizzato.
Punti chiave spiegati:
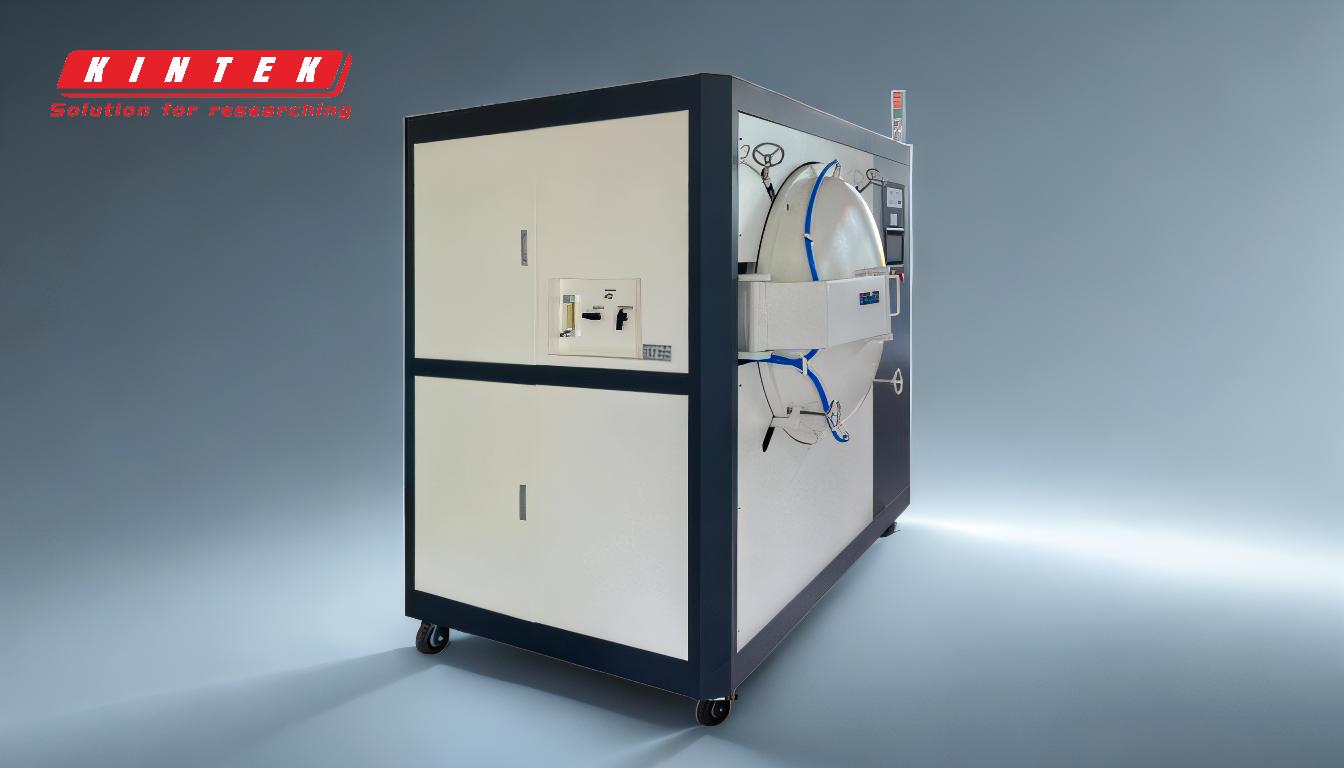
-
Meccanismo di riscaldamento:
- Fornace a resistenza: Il calore viene generato facendo passare una corrente elettrica attraverso un elemento resistivo, come una bobina o un filo riscaldante. Il calore viene quindi trasferito al materiale attraverso conduzione, convezione o irraggiamento. Questo metodo è indiretto, poiché il materiale viene riscaldato da una fonte esterna.
- Forno ad induzione: Il calore viene generato direttamente all'interno del materiale mediante induzione elettromagnetica. Una corrente alternata passa attraverso una bobina, creando un campo magnetico che induce correnti parassite nel materiale, provocandone il riscaldamento. Questo metodo è diretto e altamente efficiente.
-
Efficienza energetica:
- Fornace a resistenza: Meno efficiente dal punto di vista energetico rispetto ai forni a induzione perché il calore viene generato esternamente e poi trasferito al materiale, con conseguenti perdite di energia.
- Forno ad induzione: Maggiore efficienza energetica poiché il calore viene generato direttamente all'interno del materiale, riducendo al minimo le perdite di energia. Ciò è particolarmente vantaggioso per le applicazioni ad alta temperatura.
-
Velocità e controllo del riscaldamento:
- Fornace a resistenza: Velocità di riscaldamento più lente e controllo della temperatura meno preciso. Adatto per applicazioni in cui è richiesto il riscaldamento stazionario.
- Forno ad induzione: Velocità di riscaldamento più elevate e controllo preciso della temperatura, che lo rendono ideale per processi che richiedono un riscaldamento rapido o localizzato. L'uso di Forno ad induzione IGBT la tecnologia migliora ulteriormente il controllo e l’efficienza.
-
Applicazioni:
- Fornace a resistenza: Comunemente utilizzato in applicazioni quali ricottura, rinvenimento ed essiccazione, dove è necessario un riscaldamento uniforme su un'ampia area.
- Forno ad induzione: Utilizzato in applicazioni come fusione, forgiatura e indurimento superficiale, dove è richiesto un riscaldamento rapido, localizzato o ad alta temperatura.
-
Costo e complessità:
- Fornace a resistenza: Generalmente più semplice nel design e più conveniente per le applicazioni di riscaldamento di base. La manutenzione è semplice.
- Forno ad induzione: Più complesso e costoso a causa della necessità di componenti avanzati come bobine di induzione e alimentatori. Tuttavia, il costo iniziale più elevato è spesso compensato dal risparmio energetico e dal miglioramento delle prestazioni.
-
Compatibilità dei materiali:
- Fornace a resistenza: Può gestire un'ampia gamma di materiali, inclusi metalli, ceramica e vetro. Tuttavia potrebbe non essere adatto per materiali che richiedono un riscaldamento rapido o localizzato.
- Forno ad induzione: Utilizzato principalmente per materiali conduttivi come i metalli. I materiali non conduttivi non possono essere riscaldati mediante induzione.
-
Impatto ambientale:
- Fornace a resistenza: Un maggiore consumo energetico e una maggiore perdita di calore possono comportare un impatto ambientale maggiore.
- Forno ad induzione: Il minor consumo di energia e la ridotta perdita di calore lo rendono un'opzione più rispettosa dell'ambiente.
Comprendendo queste differenze chiave, gli acquirenti possono prendere decisioni informate in base alle loro specifiche esigenze di riscaldamento, tipi di materiali e obiettivi operativi.
Tabella riassuntiva:
Aspetto | Fornace a resistenza | Forno ad induzione |
---|---|---|
Meccanismo di riscaldamento | Riscaldamento indiretto tramite resistenza elettrica (conduzione, convezione o irraggiamento). | Riscaldamento diretto tramite induzione elettromagnetica all'interno del materiale. |
Efficienza energetica | Meno efficiente a causa della generazione di calore esterno e delle perdite di trasferimento. | Più efficiente poiché il calore viene generato direttamente all'interno del materiale. |
Velocità/controllo del riscaldamento | Riscaldamento più lento, controllo meno preciso; ideale per il riscaldamento stazionario. | Riscaldamento più veloce, controllo preciso; ideale per riscaldamenti rapidi o localizzati. |
Applicazioni | Ricottura, rinvenimento, essiccazione (riscaldamento uniforme su grandi superfici). | Fusione, forgiatura, indurimento superficiale (riscaldamento rapido o localizzato). |
Costo e complessità | Design più semplice ed economico per il riscaldamento di base; manutenzione semplice. | Costo iniziale più complesso e più elevato; compensato dal risparmio energetico e dal miglioramento delle prestazioni. |
Compatibilità dei materiali | Ampia gamma (metalli, ceramica, vetro); non ideale per il riscaldamento rapido/localizzato. | Materiali principalmente conduttivi (metalli); i materiali non conduttivi non possono essere riscaldati. |
Impatto ambientale | Maggiore consumo energetico e perdita di calore; maggiore impronta ambientale. | Minori consumi energetici, ridotte perdite di calore; più rispettoso dell'ambiente. |
Hai bisogno di aiuto per scegliere il forno giusto per la tua applicazione? Contatta i nostri esperti oggi stesso per una consulenza personalizzata!