Un'atmosfera inerte per la ricottura si riferisce a un ambiente controllato in cui i gas reattivi come l'ossigeno sono sostituiti da gas non reattivi (inerti) come l'azoto o l'argon. Questo ambiente impedisce l'ossidazione, la decarburazione e la contaminazione della superficie del metallo durante il processo di ricottura, garantendo risultati di alta qualità. Le atmosfere inerti sono particolarmente importanti per la ricottura degli acciai inossidabili e dei metalli non ferrosi, in quanto proteggono il materiale da reazioni chimiche che potrebbero comprometterne le proprietà. L'uso di gas inerti di elevata purezza (ad esempio, 99,99% di purezza) e di sistemi di controllo precisi nei forni aumenta ulteriormente l'efficacia del processo di ricottura.
Punti chiave spiegati:
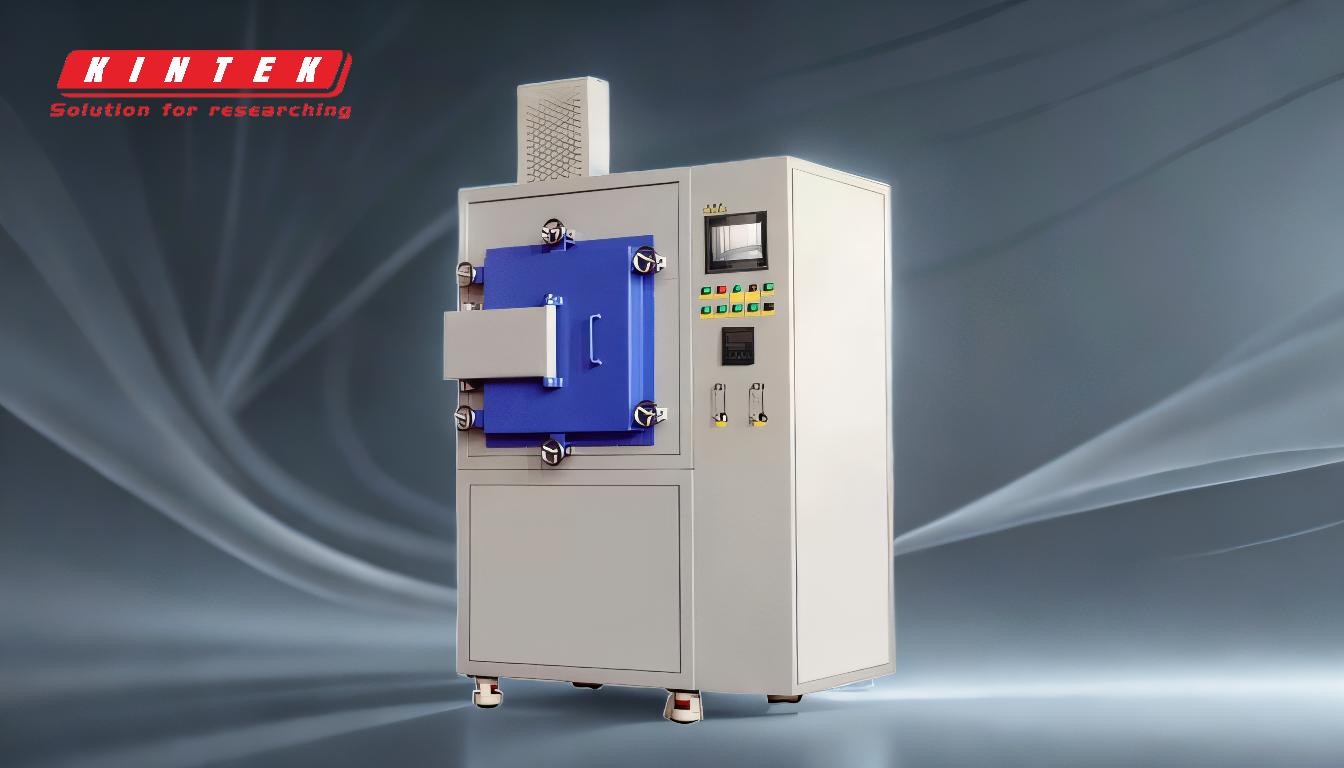
-
Definizione di atmosfera inerte:
- Un'atmosfera inerte è un ambiente controllato in cui i gas reattivi (ad esempio, l'ossigeno) sono sostituiti da gas non reattivi come azoto o argon.
- Questo ambiente è progettato per prevenire reazioni chimiche indesiderate, come l'ossidazione o la decarburazione, durante i processi di trattamento termico come la ricottura.
-
Scopo dell'utilizzo di un'atmosfera inerte nella ricottura:
- Prevenzione dell'ossidazione: L'ossidazione si verifica quando i metalli reagiscono con l'ossigeno, portando alla formazione di incrostazioni sulla superficie. Un'atmosfera inerte elimina l'ossigeno, impedendo questa reazione.
- Evitare la decarburazione: La decarburazione è la perdita di carbonio dalla superficie dell'acciaio, che può indebolire il materiale. I gas inerti prevengono questo fenomeno creando un ambiente non reattivo.
- Riduzione della contaminazione: Le atmosfere inerti riducono al minimo il rischio di contaminazione da impurità, garantendo che il metallo mantenga le proprietà desiderate.
- Migliorare la riproducibilità: Mantenendo un ambiente costante, le atmosfere inerti garantiscono risultati di ricottura affidabili e ripetibili.
-
Tipi di gas inerti utilizzati:
- Azoto: È il gas inerte più comunemente utilizzato grazie alla sua economicità e alla sua non reattività con l'acciaio. È ampiamente disponibile e fornisce un'eccellente protezione contro l'ossidazione.
- Argon: Un'altra scelta popolare, soprattutto per le applicazioni che richiedono una maggiore purezza o quando l'azoto potrebbe reagire con alcuni materiali. L'argon è più denso dell'azoto e in alcuni casi offre una protezione migliore.
- Idrogeno: Occasionalmente utilizzato in combinazione con l'argon per applicazioni specifiche, come la ricottura degli acciai inossidabili, per migliorare la pulizia della superficie e ridurre la formazione di ossidi.
-
Applicazioni delle atmosfere inerti per la ricottura:
- Acciai inossidabili: L'atmosfera inerte è essenziale per la ricottura degli acciai inossidabili per evitare la formazione di ossido di cromo, che può degradare la resistenza alla corrosione.
- Metalli non ferrosi: Metalli come rame, alluminio e titanio beneficiano di atmosfere inerti per evitare l'ossidazione e mantenere la qualità della superficie.
- Trattamenti termici specializzati: Le atmosfere inerti sono utilizzate in processi come l'incollaggio, la polimerizzazione e il trattamento termico per garantire un controllo preciso delle proprietà dei materiali.
-
Apparecchiature e sistemi di controllo:
- Forni a gas inerte in atmosfera: Questi forni sono progettati con controlli di precisione della temperatura basati su microprocessore e isolamento ad alta efficienza energetica per mantenere condizioni costanti.
- Gas di elevata purezza: Vengono utilizzati gas inerti con una purezza superiore al 99,99% per garantire una contaminazione minima e prestazioni ottimali.
- Controllo della pressione: La pressione del gas inerte viene tipicamente mantenuta entro un intervallo specifico (ad esempio, da 0,05 a 0,07 MPa) per ottenere l'ambiente protettivo desiderato.
-
Vantaggi dell'utilizzo di un'atmosfera inerte:
- Miglioramento della qualità della superficie: Previene la formazione di calcare e mantiene una superficie pulita e priva di ossido.
- Proprietà del materiale migliorate: Conserva il contenuto di carbonio e altri elementi critici, garantendo la resistenza e la durata del materiale.
- Sicurezza: Riduce il rischio di incendi ed esplosioni eliminando i gas reattivi.
- Risparmio sui costi: I forni ad alta efficienza energetica e i precisi sistemi di controllo ottimizzano l'utilizzo delle risorse, riducendo i costi operativi.
-
Sfide e considerazioni:
- Costo dei gas inerti: I gas ad alta purezza come l'argon possono essere costosi e incidere sul costo complessivo del processo di ricottura.
- Manutenzione delle apparecchiature: I forni a gas inerte in atmosfera richiedono una manutenzione regolare per garantire prestazioni costanti e prevenire le perdite.
- Compatibilità dei materiali: Non tutti i materiali richiedono atmosfere inerti, quindi è essenziale valutare le esigenze specifiche del materiale da ricuocere.
Comprendendo questi punti chiave, gli acquirenti di apparecchiature e materiali di consumo possono prendere decisioni informate sull'implementazione di atmosfere inerti nei loro processi di ricottura, garantendo risultati di alta qualità e operazioni economicamente vantaggiose.
Tabella riassuntiva:
Aspetto | Dettagli |
---|---|
Definizione | Ambiente controllato con gas non reattivi (ad es. azoto, argon). |
Scopo | Previene l'ossidazione, la decarburazione e la contaminazione e garantisce la riproducibilità. |
Gas inerti utilizzati | Azoto (economico), Argon (ad alta purezza), Idrogeno (specializzato). |
Applicazioni | Acciai inossidabili, metalli non ferrosi, trattamenti termici specializzati. |
Attrezzatura | Forni a gas inerte con controlli di precisione e gas ad alta purezza. |
Vantaggi | Miglioramento della qualità della superficie, miglioramento delle proprietà dei materiali, sicurezza e risparmio. |
Sfide | Costo dei gas inerti, manutenzione delle apparecchiature, compatibilità dei materiali. |
Avete bisogno di aiuto per creare un'atmosfera inerte per la ricottura? Contattate i nostri esperti oggi stesso per soluzioni su misura!