La brasatura a induzione, pur essendo efficiente e precisa, presenta diverse limitazioni che possono influire sulla sua efficacia in alcune applicazioni.Queste limitazioni includono la necessità di materiali puliti e privi di ossidi, la potenziale perdita di elementi di lega a causa dell'ossidazione e le difficoltà con materiali come l'alluminio che formano strati di ossido stabili.Inoltre, il controllo preciso della temperatura e la distribuzione termica omogenea sono fondamentali, soprattutto quando si lavora con materiali che hanno intervalli di fusione molto simili.La comprensione di queste limitazioni è essenziale per selezionare il metodo di brasatura appropriato e garantire risultati di alta qualità.
Punti chiave spiegati:
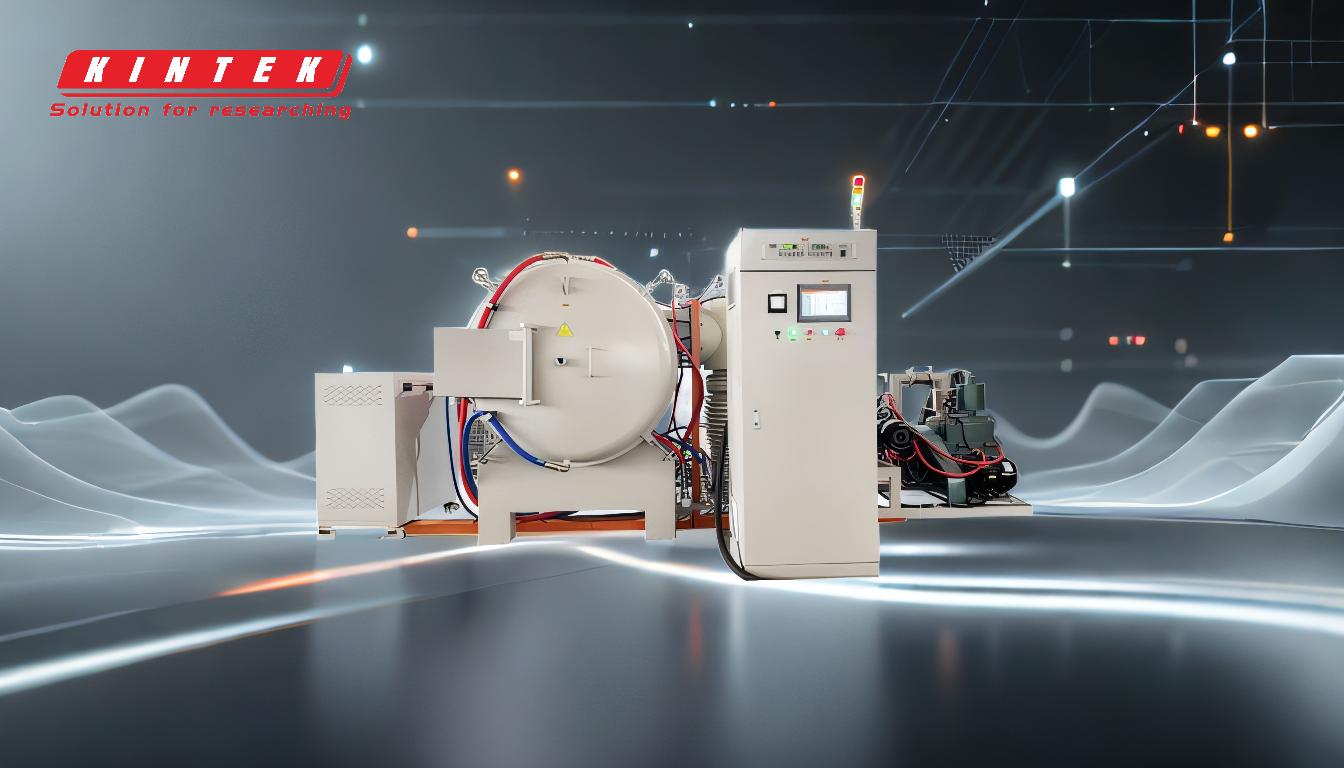
-
Mancanza di capacità di raffinazione:
- La brasatura a induzione richiede che i materiali di carica siano privi di ossidi e di composizione nota.Ciò significa che eventuali impurità o ossidi presenti nei materiali possono influire negativamente sul processo di brasatura.
- Il processo non è in grado di raffinare o purificare i materiali durante la brasatura, il che può essere uno svantaggio significativo quando si lavora con materiali inclini all'ossidazione o alla contaminazione.
-
Ossidazione e perdita di elementi di lega:
- Durante il processo di brasatura a induzione, alcuni elementi di lega possono andare persi a causa dell'ossidazione.È quindi necessario aggiungere nuovamente questi elementi alla massa fusa per ottenere la composizione desiderata.
- La perdita di elementi di lega può portare a incongruenze nel prodotto finale, richiedendo un attento monitoraggio e una regolazione durante il processo di brasatura.
-
Sfide con l'alluminio e altri materiali ossidabili:
- L'alluminio, in particolare, è altamente ossidabile e forma uno strato stabile di ossido di alluminio (Al2O3) che può impedire ai metalli d'apporto di bagnare la superficie.Questo strato di ossido deve essere soppresso prima della brasatura e impedito di riformarsi fino alla solidificazione del metallo d'apporto.
- La necessità di gestire questo strato di ossido aggiunge complessità al processo di brasatura, richiedendo ulteriori fasi e precauzioni per garantire un legame di successo.
-
Controllo preciso della temperatura e distribuzione termica omogenea:
- La brasatura a induzione richiede un controllo preciso della temperatura, soprattutto quando gli intervalli di fusione dei metalli base e d'apporto sono molto vicini.Qualsiasi deviazione di temperatura può portare a una brasatura incompleta o a danni ai materiali.
- Anche il raggiungimento di una distribuzione termica omogenea è fondamentale per garantire che l'intero giunto raggiunga la temperatura necessaria in modo uniforme.Un riscaldamento incoerente può provocare giunti deboli o surriscaldamenti localizzati, che possono compromettere l'integrità dell'assemblaggio brasato.
-
Compatibilità dei materiali:
- Non tutti i materiali sono adatti alla brasatura a induzione.I materiali altamente reattivi o con composizioni complesse possono richiedere metodi di brasatura alternativi per ottenere i risultati desiderati.
- La compatibilità dei metalli di base e d'apporto deve essere attentamente valutata per garantire che possano formare un legame forte e duraturo senza reazioni avverse.
-
Complessità dell'apparecchiatura e del processo:
- Le apparecchiature per la brasatura a induzione possono essere complesse e costose e richiedono operatori qualificati per gestire il processo in modo efficace.
- Il processo stesso può essere più complesso di altri metodi di brasatura e richiede una conoscenza approfondita dei materiali, delle attrezzature e delle tecniche coinvolte.
In sintesi, la brasatura a induzione offre molti vantaggi, tra cui il riscaldamento rapido e il controllo preciso, ma presenta anche diverse limitazioni che devono essere gestite con attenzione.Tra questi, la necessità di materiali puliti e privi di ossidi, la potenziale perdita di elementi di lega, le difficoltà con materiali ossidabili come l'alluminio e la necessità di un controllo preciso della temperatura e di una distribuzione termica omogenea.La comprensione di queste limitazioni è fondamentale per selezionare il metodo di brasatura appropriato e garantire risultati di alta qualità.
Tabella riassuntiva:
Limitazioni | Sfide principali |
---|---|
Mancanza di capacità di raffinazione | Richiede materiali puliti e privi di ossidi; nessuna raffinazione durante la brasatura. |
Ossidazione e perdita di elementi di lega | Gli elementi di lega possono ossidarsi, richiedendo una nuova aggiunta e un attento monitoraggio. |
Sfide con l'alluminio | Lo strato di ossido di alluminio deve essere soppresso e gestito per garantire il successo della brasatura. |
Controllo preciso della temperatura | È fondamentale per i materiali con intervalli di fusione molto simili. |
Compatibilità dei materiali | Non tutti i materiali sono adatti; i metalli base e d'apporto devono essere compatibili. |
Complessità delle attrezzature e del processo | Richiede operatori qualificati e attrezzature complesse e costose. |
Avete bisogno di aiuto per superare le sfide della brasatura a induzione? Contattate oggi stesso i nostri esperti per soluzioni su misura!