Le operazioni di trattamento termico sono fondamentali per modificare le proprietà meccaniche, fisiche e chimiche dei materiali, ma sono soggette a guasti se non vengono eseguite correttamente.Questi errori possono derivare da un'impropria preparazione della superficie, da un errato controllo della temperatura, da una velocità di raffreddamento inadeguata o da una contaminazione durante il processo.Questi problemi possono portare a difetti come la pelatura del rivestimento, la formazione di bolle, il pitting o la variegatura, nonché a debolezze strutturali, a una riduzione della durata o a proprietà inconsistenti del materiale.La comprensione dei guasti più comuni e delle loro cause è essenziale per garantire la qualità e l'affidabilità dei componenti trattati termicamente.
Punti chiave spiegati:
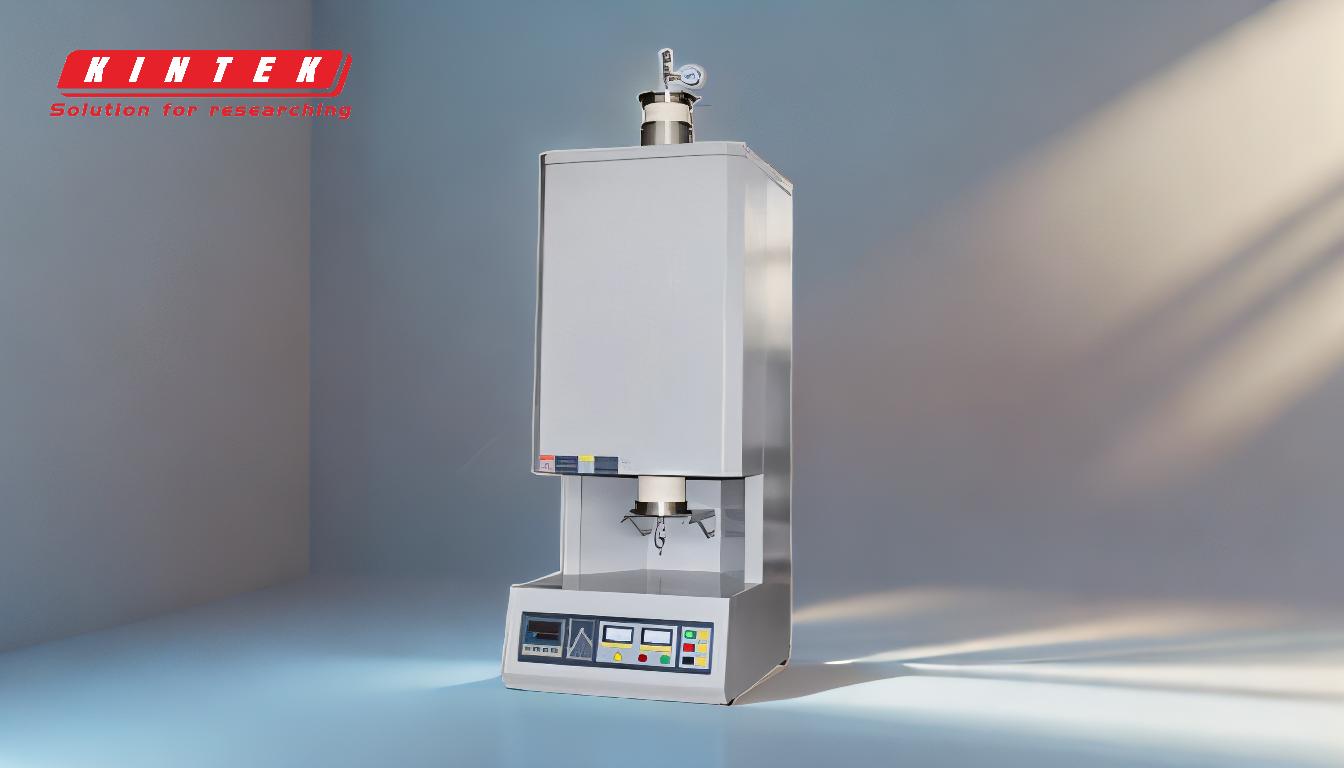
-
Preparazione non corretta della superficie:
- Edizione:Una preparazione inadeguata della superficie prima del trattamento termico può provocare difetti del rivestimento come peeling, bolle, pitting e variegature.
- Causa:Le superfici ruvide o non raffinate impediscono la formazione di rivestimenti forti, uniformi e anticorrosivi.
- Soluzione:Assicurare un'accurata pulizia, lucidatura e affinamento della superficie prima del trattamento termico per ottenere un'adesione e una qualità del rivestimento ottimali.
-
Errori nel controllo della temperatura:
- Edizione:Impostazioni di temperatura errate o fluttuazioni durante il trattamento termico possono portare a proprietà incoerenti del materiale.
- Causa:Il surriscaldamento o il surriscaldamento possono causare trasformazioni di fase improprie, con conseguenti punti morbidi, fragilità o durezza non uniforme.
- Soluzione:Utilizzare sistemi di controllo della temperatura precisi e calibrare regolarmente le apparecchiature per mantenere condizioni di riscaldamento costanti.
-
Errata gestione del tasso di raffreddamento:
- Edizione:Velocità di raffreddamento inadeguate possono causare tensioni termiche, deformazioni o crepe nel materiale.
- Causa:Il raffreddamento rapido (tempra) o lento (ricottura) deve essere attentamente controllato per ottenere la microstruttura e le proprietà meccaniche desiderate.
- La soluzione:Selezionare i mezzi di raffreddamento appropriati (ad esempio, olio, acqua, aria) e monitorare le velocità di raffreddamento per evitare difetti.
-
Contaminazione durante il trattamento termico:
- Edizione:Contaminanti come olio, grasso o ossidi sulla superficie del materiale possono causare difetti superficiali o una distribuzione non uniforme del calore.
- Causa:La contaminazione interferisce con il processo di trasferimento del calore e può causare un surriscaldamento o un surriscaldamento localizzato.
- Soluzione:Pulire accuratamente il materiale prima del trattamento termico e garantire un'atmosfera controllata (ad esempio, gas inerte o vuoto) per evitare la contaminazione.
-
Proprietà del materiale incoerenti:
- Edizione:Le variazioni di durezza, resistenza o duttilità del materiale possono essere dovute a un trattamento termico non uniforme.
- Causa:Un riscaldamento o un raffreddamento non uniforme può provocare trasformazioni di fase e proprietà meccaniche incoerenti.
- Soluzione:Utilizzare metodi di riscaldamento uniformi (ad esempio, riscaldamento a induzione) e garantire un raffreddamento uniforme per ottenere risultati omogenei.
-
Fallimenti del trattamento delle sollecitazioni:
- Edizione:Un'errata riduzione delle tensioni può lasciare tensioni residue nel materiale, con conseguenti deformazioni o cricche durante la lavorazione o l'uso.
- Causa:Un riscaldamento o un raffreddamento inadeguati durante i processi di distensione possono non eliminare le tensioni interne.
- Soluzione:Seguire precisi protocolli di distensione, tra cui un riscaldamento adeguato e un raffreddamento lento, per ridurre al minimo le tensioni residue.
-
Difetti di cementazione:
- Edizione:Durante i processi di cementazione, come la carburazione o la nitrurazione, possono verificarsi profondità o durezza superficiale incoerenti.
- Causa:La diffusione non uniforme del carbonio o dell'azoto può essere causata da un controllo improprio della temperatura o da un tempo di processo insufficiente.
- Soluzione:Monitorare e controllare attentamente il processo di diffusione per ottenere una profondità e una durezza uniformi.
-
Fallimenti di ricottura:
- Edizione:Una ricottura non corretta può portare a un eccessivo rammollimento o a un'insufficiente riduzione delle tensioni nel materiale.
- Causa:Temperature di ricottura o velocità di raffreddamento errate possono non consentire di ottenere la microstruttura desiderata.
- Soluzione:Seguire le linee guida per la ricottura specifiche per il materiale e l'applicazione per garantire un adeguato ammorbidimento e l'eliminazione delle tensioni.
Affrontando questi guasti comuni e implementando le migliori pratiche, i produttori possono migliorare la qualità e l'affidabilità dei componenti trattati termicamente, garantendo il rispetto degli standard prestazionali richiesti.
Tabella riassuntiva:
Tipo di guasto | Problema | Causa | Soluzione |
---|---|---|---|
Preparazione della superficie non corretta | Difetti del rivestimento (sfogliatura, bolle, pitting, variegatura) | Superfici ruvide o non raffinate | Pulizia approfondita, lucidatura e affinamento della superficie |
Guasti al controllo della temperatura | Proprietà del materiale incoerenti | Surriscaldamento o surriscaldamento | Utilizzare sistemi di controllo della temperatura precisi e calibrare le apparecchiature. |
Errata gestione della velocità di raffreddamento | Sollecitazioni termiche, deformazioni o crepe | Velocità di raffreddamento inadeguate | Selezionare mezzi di raffreddamento appropriati e monitorare le velocità di raffreddamento |
Contaminazione | Difetti della superficie o distribuzione irregolare del calore | Olio, grasso o ossidi sulla superficie del materiale | Pulire accuratamente e utilizzare un'atmosfera controllata |
Proprietà del materiale incoerenti | Variazioni di durezza, resistenza o duttilità | Riscaldamento o raffreddamento non uniforme | Utilizzare metodi di riscaldamento uniformi e garantire un raffreddamento uniforme |
Fallimenti da sollecitazione | Tensioni residue che causano deformazioni o fessurazioni | Riscaldamento o raffreddamento inadeguato durante la distensione | Seguire protocolli precisi di distensione con un riscaldamento adeguato e un raffreddamento lento. |
Difetti di cementazione | Profondità della cassa o durezza superficiale incoerente | Diffusione non uniforme di carbonio o azoto | Monitorare e controllare attentamente il processo di diffusione |
Fallimenti da ricottura | Eccessivo rammollimento o insufficiente scarico delle tensioni | Temperature di ricottura o velocità di raffreddamento non corrette | Seguire le linee guida specifiche per la ricottura |
Assicuratevi che i processi di trattamento termico siano impeccabili. contattate oggi stesso i nostri esperti per soluzioni su misura!