I rivestimenti diamantati (DLC) sono applicati con tecniche di deposizione avanzate, principalmente la deposizione fisica da vapore (PVD) e la deposizione chimica da vapore (CVD).Questi metodi prevedono la creazione di uno strato sottile e durevole di carbonio simile al diamante (DLC) sulla superficie di utensili o componenti.La PVD prevede l'evaporazione di un materiale di partenza e la sua condensazione sull'utensile, formando un monostrato di DLC dello spessore tipico di 0,5-2,5 micron.La CVD, invece, utilizza gas di idrogeno e metano in una camera, dove fili di tungsteno riscaldati a oltre 2.300°C decompongono i gas, consentendo agli atomi di carbonio di ricombinarsi e formare un film di diamante puro sulla superficie dell'utensile.Entrambi i metodi richiedono un controllo preciso della temperatura, della pressione e della composizione del gas per ottenere risultati ottimali.
Punti chiave spiegati:
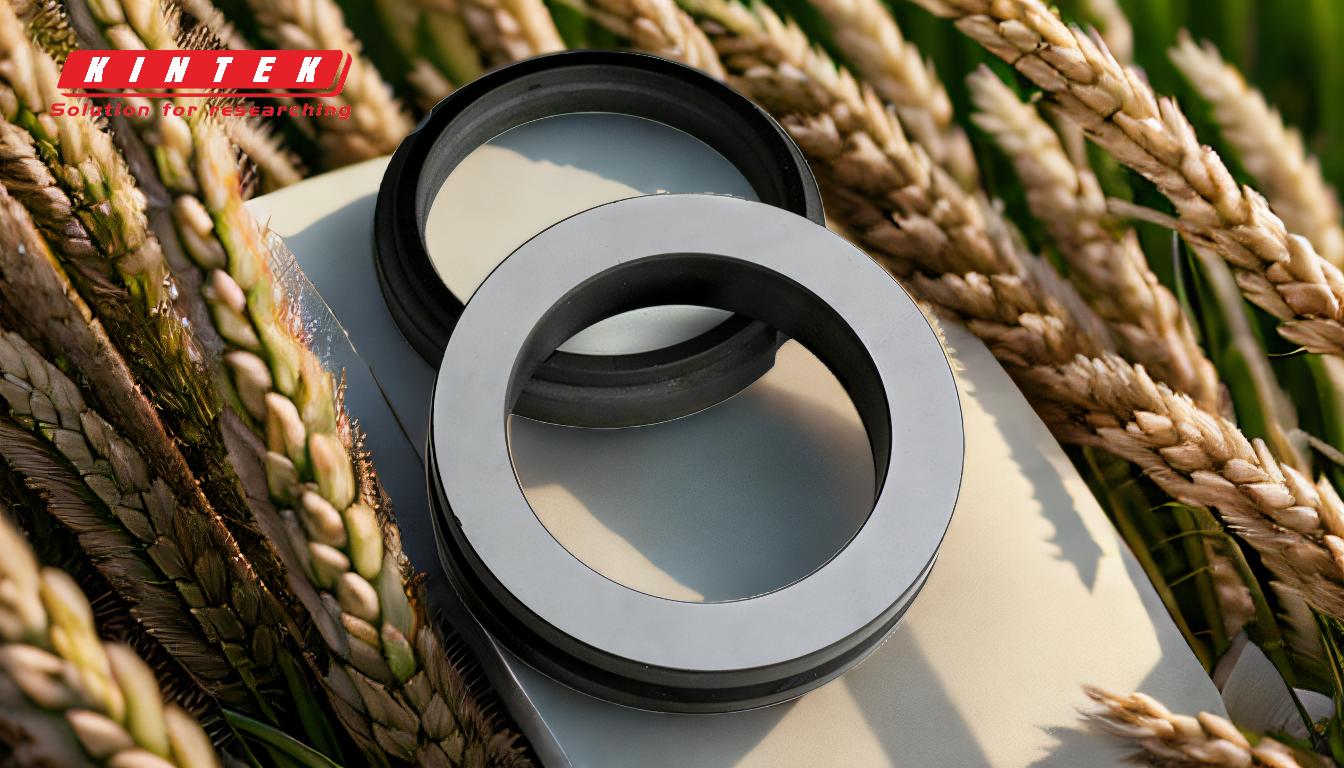
-
Panoramica dei rivestimenti diamantati (DLC):
- I rivestimenti DLC sono strati sottili, duri e resistenti all'usura applicati a utensili o componenti per migliorarne le prestazioni e la durata.
- Questi rivestimenti sono amorfi, cioè privi di una struttura cristallina, ma presentano proprietà simili al diamante, come l'elevata durezza e il basso attrito.
-
Metodi di rivestimento primari:
-
Deposizione fisica da vapore (PVD):
- Il PVD è un metodo ampiamente utilizzato per l'applicazione di rivestimenti DLC.
- Il processo prevede l'evaporazione di un materiale di partenza (spesso a base di carbonio) in una camera a vuoto.
- Il materiale evaporato si condensa sulla superficie dell'utensile, formando uno strato sottile e uniforme di DLC.
- Lo spessore del rivestimento varia in genere da 0,5 a 2,5 micron.
- La PVD è nota per la sua capacità di produrre rivestimenti aderenti di alta qualità con un'eccellente resistenza all'usura.
-
Deposizione chimica da vapore (CVD):
- La CVD è un altro metodo comune per l'applicazione di rivestimenti DLC.
- In questo processo, l'utensile viene posto in una camera riempita di gas idrogeno e metano.
- Fili di tungsteno riscaldati a oltre 2.300°C forniscono l'energia necessaria per rompere le molecole di gas.
- Gli atomi di carbonio attivati si ricombinano sulla superficie dell'utensile, formando un film di diamante puro.
- La CVD è particolarmente efficace per creare rivestimenti più spessi e durevoli.
-
Deposizione fisica da vapore (PVD):
-
Fasi del processo di applicazione dei rivestimenti DLC:
-
Preparazione:
- L'utensile o il componente da rivestire deve essere accuratamente pulito e preparato per garantire una corretta adesione del rivestimento.
- Ciò comporta spesso la rimozione di eventuali contaminanti superficiali, come oli o ossidi, con mezzi chimici o meccanici.
-
Caricamento nella camera:
- Gli strumenti preparati vengono caricati nella camera di deposizione.
- In PVD, la camera viene evacuata per creare il vuoto, mentre in CVD la camera viene riempita con i gas appropriati.
-
Deposizione:
- Per la PVD, il materiale di partenza viene fatto evaporare e il vapore si condensa sulla superficie dell'utensile.
- Per la CVD, i gas vengono attivati e gli atomi di carbonio si depositano sull'utensile.
-
Raffreddamento e finitura:
- Dopo la deposizione, gli utensili rivestiti vengono lasciati raffreddare lentamente per evitare stress termici.
- Il rivestimento finale viene ispezionato per verificarne la qualità, lo spessore e l'adesione.
-
Preparazione:
-
Parametri e considerazioni chiave:
-
Temperatura:
- Sia il processo PVD che quello CVD richiedono temperature elevate, che in genere vanno da 750°C a oltre 2.300°C, a seconda del metodo.
- Un adeguato controllo della temperatura è fondamentale per garantire la qualità e l'adesione del rivestimento.
-
Composizione del gas:
- Nella CVD, la composizione dei gas idrogeno e metano deve essere attentamente controllata per ottenere la deposizione di carbonio desiderata.
-
Spessore del rivestimento:
- Lo spessore del rivestimento DLC è un fattore critico nel determinare le sue prestazioni.
- I rivestimenti più spessi possono offrire una migliore resistenza all'usura, ma potrebbero anche essere più inclini a crepe o delaminazioni.
-
Adesione:
- Garantire una forte adesione tra il rivestimento e il substrato è essenziale per la durata del rivestimento.
- Ciò comporta spesso un pretrattamento del substrato o l'uso di strati intermedi.
-
Temperatura:
-
Applicazioni dei rivestimenti DLC:
- I rivestimenti DLC sono utilizzati in un'ampia gamma di settori, tra cui quello automobilistico, aerospaziale, dei dispositivi medici e degli utensili da taglio.
- Sono particolarmente apprezzati per la loro capacità di ridurre l'attrito, resistere all'usura e prolungare la vita dei componenti sottoposti a condizioni difficili.
-
Vantaggi e limiti:
-
Vantaggi:
- Elevata durezza e resistenza all'usura.
- Basso coefficiente di attrito, che riduce il consumo di energia e migliora l'efficienza.
- Eccellente resistenza alla corrosione.
- Capacità di rivestire geometrie complesse.
-
Limitazioni:
- Costo elevato delle attrezzature e del processo.
- Spessore limitato a causa del potenziale di stress interno e di cricche.
- Richiede un controllo preciso dei parametri di processo.
-
Vantaggi:
-
Tendenze future:
- La ricerca in corso si concentra sul miglioramento dell'adesione, dello spessore e dell'uniformità dei rivestimenti DLC.
- Si prevede che i progressi nelle nanotecnologie e nei metodi di rivestimento ibridi miglioreranno ulteriormente le prestazioni e l'applicabilità dei rivestimenti DLC in vari settori industriali.
Comprendendo questi punti chiave, gli acquirenti di attrezzature e materiali di consumo possono prendere decisioni informate sull'applicazione dei rivestimenti diamantati, assicurandosi di scegliere il metodo e i parametri più appropriati per le loro esigenze specifiche.
Tabella riassuntiva:
Aspetto | Dettagli |
---|---|
Metodi primari | PVD (Physical Vapor Deposition), CVD (Chemical Vapor Deposition) |
Spessore del rivestimento | Da 0,5 a 2,5 micron (PVD), più spesso per il CVD |
Parametri chiave | Temperatura (da 750°C a 2.300°C), composizione del gas, adesione, spessore del rivestimento |
Applicazioni | Automotive, aerospaziale, dispositivi medici, utensili da taglio |
Vantaggi | Elevata durezza, basso attrito, resistenza alla corrosione, geometrie complesse |
Limitazioni | Costo elevato, spessore limitato, necessità di un controllo preciso dei parametri |
Ottimizzate i vostri utensili con i rivestimenti DLC avanzati... contattate oggi i nostri esperti per soluzioni su misura!