Gli elementi riscaldanti perdono potenza nel tempo a causa di diversi fattori, tra cui l'ossidazione, l'allungamento e le variazioni di resistenza.Questi fattori sono influenzati dalle condizioni operative, come la temperatura, l'atmosfera, la densità di watt e le modalità di utilizzo.Con il tempo, la resistenza dell'elemento riscaldante aumenta, portando a una riduzione della potenza erogata e a un eventuale guasto.Si tratta di una parte naturale del ciclo di vita dell'elemento e i produttori tengono conto di queste variabili quando progettano e garantiscono i loro prodotti.
Punti chiave spiegati:
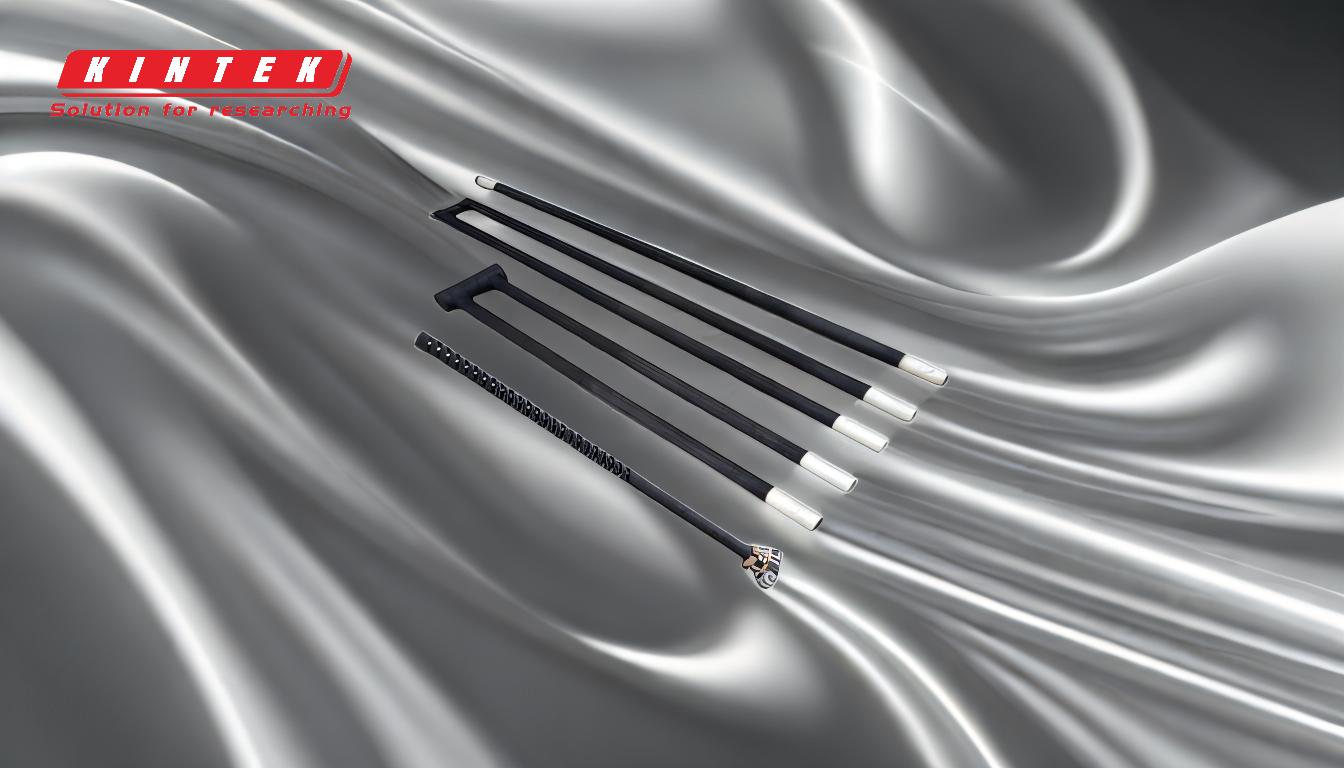
-
La resistenza aumenta nel tempo:
- Quando gli elementi riscaldanti invecchiano, la loro resistenza aumenta a causa dell'ossidazione, che riduce l'area della sezione trasversale dell'elemento.Questo processo di ossidazione è inevitabile e si verifica più rapidamente in determinati ambienti, come le atmosfere ad alta temperatura o riducenti.
- Inoltre, l'allungamento degli anelli dell'elemento riscaldante contribuisce ad aumentare la resistenza.Questo allungamento si verifica quando il materiale si espande e si contrae durante i cicli di riscaldamento e raffreddamento.
-
Impatto sulla potenza erogata:
- L'aumento della resistenza influisce direttamente sulla potenza erogata dall'elemento riscaldante.Secondo la legge di Ohm (P = V²/R), all'aumentare della resistenza (R) diminuisce la potenza (P) erogata al forno per una determinata tensione (V).
- Questa riduzione di potenza può portare a un riscaldamento inefficiente e a tempi di ciclo più lunghi, compromettendo in ultima analisi le prestazioni del forno o del sistema di riscaldamento.
-
Fattori che influenzano la durata dell'elemento:
- Forno Atmosfera:Gli elementi che operano in atmosfere riducenti o in ambienti con alti livelli di ossigeno o altri gas reattivi tendono a ossidarsi più rapidamente, riducendo la loro durata.
- Densità in Watt:Le densità di watt più elevate sollecitano maggiormente l'elemento riscaldante, accelerandone l'usura.
- Temperatura di esercizio:Le temperature più elevate aumentano il tasso di ossidazione e di degradazione del materiale.
- Modelli di utilizzo:Un servizio continuo o frequenti cicli di riscaldamento e raffreddamento possono portare a un degrado più rapido rispetto all'uso intermittente.
- Manutenzione:Una manutenzione regolare, come la pulizia e l'ispezione degli elementi, può contribuire a prolungarne la durata individuando e risolvendo tempestivamente i problemi.
-
Considerazioni specifiche sui materiali:
- Elementi di carburo di silicio:Questi elementi sono particolarmente sensibili all'atmosfera del forno e alla densità di watt.La loro aspettativa di vita è influenzata dall'ambiente operativo e dalla frequenza dei cicli termici.
- Elementi in ceramica:Le proprietà degli elementi riscaldanti in ceramica sono influenzate dalla composizione della lega, dalle dimensioni, dal carico in watt e dall'architettura del dispositivo.Questi fattori determinano la risposta dell'elemento alle sollecitazioni termiche e meccaniche nel tempo.
-
Ciclo di vita normale e guasti:
- L'aumento graduale della resistenza e l'eventuale guasto degli elementi riscaldanti sono considerati una parte normale del loro ciclo di vita.I produttori progettano gli elementi tenendo conto di questi fattori e forniscono garanzie che coprono i difetti di fabbricazione ma non l'usura dovuta alle condizioni operative.
- Quando un elemento si guasta, in genere è dovuto a una combinazione di fattori, tra cui l'ossidazione, l'allungamento e l'aumento della resistenza, che collettivamente riducono la sua potenza di uscita fino al punto in cui non può più funzionare efficacemente.
-
Strategie di mitigazione:
-
Per prolungare la durata degli elementi riscaldanti, gli utenti possono:
- Far funzionare il forno o il sistema di riscaldamento entro i limiti di temperatura e densità di watt raccomandati.
- Ridurre al minimo i cicli di riscaldamento e raffreddamento rapidi.
- Utilizzare atmosfere o rivestimenti protettivi per ridurre l'ossidazione.
- Eseguire una manutenzione regolare per identificare e risolvere i problemi prima che portino a un guasto.
-
Per prolungare la durata degli elementi riscaldanti, gli utenti possono:
In sintesi, gli elementi riscaldanti perdono potenza con il passare del tempo a causa dell'aumento della resistenza causato dall'ossidazione, dall'allungamento e da altri fattori operativi.La comprensione di questi fattori e l'attuazione di strategie per mitigarne gli effetti possono contribuire a prolungare la durata degli elementi riscaldanti e a mantenere un funzionamento efficiente del forno.
Tabella riassuntiva:
Fattori chiave | Impatto sugli elementi di riscaldamento |
---|---|
Aumento della resistenza | L'ossidazione e l'allungamento riducono l'area della sezione trasversale, aumentando la resistenza e riducendo la potenza. |
Atmosfera del forno | L'ossigeno elevato o i gas reattivi accelerano l'ossidazione, riducendo la durata di vita. |
Densità in watt | Densità di watt più elevate stressano gli elementi, causando un'usura più rapida. |
Temperatura di esercizio | Le temperature più elevate aumentano i tassi di ossidazione e di degradazione dei materiali. |
Schemi di utilizzo | Cicli frequenti di riscaldamento/raffreddamento degradano gli elementi più rapidamente rispetto all'uso intermittente. |
Manutenzione | Una pulizia e un'ispezione regolari possono identificare precocemente i problemi, prolungando la durata degli elementi. |
Avete bisogno di aiuto per la manutenzione o la sostituzione degli elementi di riscaldamento? Contattate i nostri esperti oggi stesso per soluzioni su misura!