Sviluppo storico della tecnologia di rivestimento sottovuoto
Le prime sfide e la tecnologia CVD
La tecnologia di rivestimento sotto vuoto ha compiuto i primi passi significativi negli anni '60 con l'avvento della deposizione chimica da vapore (CVD). Questa tecnica pionieristica, per quanto rivoluzionaria all'epoca, non era priva di sfide. Uno degli ostacoli più significativi era il requisito delle alte temperature, che limitava i tipi di substrati che potevano essere rivestiti in modo efficace. Gli elevati requisiti termici dei processi CVD significavano che solo i materiali con un'elevata stabilità termica potevano resistere alle condizioni di deposizione, restringendo significativamente il campo delle potenziali applicazioni.
Inoltre, la prima tecnologia CVD era limitata dalla varietà di rivestimenti che poteva produrre. La complessità e la specificità delle reazioni chimiche coinvolte nella CVD hanno fatto sì che solo pochi materiali potessero essere depositati in modo affidabile, limitandone ulteriormente l'utilità. Queste limitazioni hanno rappresentato una sfida significativa per lo sviluppo e l'adozione diffusa della tecnologia di rivestimento sotto vuoto, rendendo necessaria la ricerca di metodi alternativi in grado di superare queste barriere.
Nei decenni successivi, queste prime sfide avrebbero aperto la strada allo sviluppo di tecnologie di rivestimento più versatili ed efficienti, come la deposizione fisica da vapore (PVD), emersa negli anni '70 e in grado di offrire una soluzione più adattabile e rispettosa dell'ambiente.
L'emergere della tecnologia PVD
Negli anni '70, il panorama della tecnologia di rivestimento sotto vuoto ha subito una trasformazione significativa con l'avvento della tecnologia PVD (Physical Vapor Deposition). Questo nuovo metodo non solo ha affrontato alcuni dei problemi ambientali associati al suo predecessore, la deposizione chimica da vapore (CVD), ma ha anche introdotto una miriade di proprietà superficiali versatili, prima irraggiungibili. Il passaggio dalla CVD alla PVD è stato caratterizzato da una riduzione delle temperature operative e da un ampliamento della gamma di rivestimenti applicabili, ampliando così le applicazioni in vari settori.
I vantaggi ambientali della PVD sono stati particolarmente degni di nota. A differenza della CVD, che spesso richiedeva temperature elevate e sostanze chimiche potenzialmente pericolose, la PVD opera in condizioni più controllate, con conseguente riduzione del consumo energetico e delle emissioni. Questo rispetto dell'ambiente, unito alla capacità di produrre rivestimenti con durezza, resistenza all'usura e protezione dalla corrosione superiori, ha rapidamente attirato l'attenzione di ricercatori e industriali.
Il rapido sviluppo della tecnologia PVD in questo periodo può essere attribuito alla sua adattabilità e ai significativi miglioramenti apportati alla qualità e alla durata dei rivestimenti. Industrie come quella automobilistica e aerospaziale hanno iniziato ad adottare la PVD per la sua capacità di migliorare le prestazioni di strumenti e componenti, portando a una maggiore efficienza e a una maggiore durata dei prodotti. Questa adozione diffusa ha ulteriormente alimentato i progressi delle tecniche PVD, facendo progredire la tecnologia e consolidando il suo posto nel regno dei moderni processi industriali.
Stato attuale e sfide
Sviluppo sbilanciato
Nonostante l'adozione diffusa della tecnologia di rivestimento sottovuoto per scopi decorativi, l'applicazione di questi rivestimenti nella produzione di stampi industriali rimane irta di sfide. L'ostacolo principale risiede nei severi requisiti di adesione richiesti dagli stampi industriali, che richiedono un legame più solido e duraturo tra il rivestimento e il substrato. Questa esigenza non è facilmente soddisfatta dalle attuali tecnologie di rivestimento, che spesso privilegiano l'estetica rispetto alla durata funzionale.
Inoltre, la mancanza di tecnologie di processo complete, studiate appositamente per il rivestimento di stampi industriali, aggrava ulteriormente queste sfide. A differenza dei rivestimenti decorativi, che possono permettersi metodi di applicazione meno rigorosi, i rivestimenti per stampi industriali richiedono processi precisi e controllati per garantire prestazioni e durata ottimali. Questa disparità nello sviluppo tecnologico ha portato a una crescita sbilanciata all'interno dell'industria dei rivestimenti sottovuoto, dove i progressi nei rivestimenti decorativi non sono stati adeguatamente rispecchiati nelle applicazioni industriali.
Per risolvere questi problemi, è necessario sviluppare tecnologie e metodologie specializzate in grado di soddisfare le esigenze specifiche del rivestimento di stampi industriali. Ciò include non solo il miglioramento delle proprietà di adesione dei rivestimenti, ma anche il perfezionamento dell'intera catena di processo, dal pretrattamento al controllo di qualità post-applicazione. Concentrandosi su queste aree, l'industria può colmare il divario tra rivestimenti decorativi e industriali, favorendo una traiettoria di sviluppo più equilibrata e completa.
Disparità tecniche
Nel campo delle tecnologie di rivestimento sotto vuoto, in particolare nel contesto della PVD (Physical Vapor Deposition), le capacità tecniche nazionali sono spesso inferiori agli standard internazionali. Questa disparità non è solo una questione di sofisticazione delle apparecchiature, ma comprende anche una gamma più ampia di fattori, tra cui l'ottimizzazione dei processi, i progressi della scienza dei materiali e le metodologie di controllo della qualità.
Per colmare questo divario, è necessario che l'industria nazionale non solo introduca attrezzature avanzate, ma anche che assorba e integri tecnologie all'avanguardia. Ciò implica un approccio su più fronti, che comprende
- Aggiornamento delle attrezzature: Investimenti in camere da vuoto, alimentatori e sistemi di immissione di gas all'avanguardia, in grado di gestire con precisione processi PVD complessi.
- Assorbimento tecnologico: Impegno in attività di ricerca e sviluppo in collaborazione con partner internazionali per comprendere e implementare le migliori pratiche nella tecnologia PVD.
- Ottimizzazione del processo: Affinamento dei processi esistenti per garantire l'uniformità della qualità del rivestimento, affrontando questioni come l'adesione e la consistenza dello strato.
Aspetto | Stato nazionale | Standard internazionali |
---|---|---|
Attrezzature | Di base o obsoleta | Avanzate e altamente precise |
Controllo del processo | Manuale o semi-automatico | Completamente automatizzato con supporto AI |
Scienza dei materiali | Ricerca limitata | Ricerca e innovazione estese |
Controllo qualità | Metodi ad hoc | Controllo qualità sistematico e rigoroso |
Il percorso verso la parità non prevede solo l'acquisizione di tecnologia, ma anche lo sviluppo di un solido ecosistema che supporti l'innovazione e il miglioramento continui. Questo approccio olistico è essenziale per elevare le capacità nazionali e garantire che possano competere su scala globale.
Concetti di base e caratteristiche del rivestimento PVD
Metodi e tecniche
La deposizione fisica da vapore (PVD) comprende diversi metodi avanzati, ciascuno con caratteristiche e applicazioni uniche. Due tecniche di spicco nell'ambito della PVD sono la placcatura ad arco multiplo e lo sputtering di magnetron.
La placcatura ad arco multiplo prevede l'evaporazione del materiale target mediante un arco elettrico, che ionizza il materiale e lo spinge verso il substrato. Questo metodo è noto per le sue elevate velocità di deposizione e per la capacità di rivestire geometrie complesse. Tuttavia, può soffrire di problemi quali la contaminazione da particelle e lo spessore non uniforme del rivestimento.
Il magnetron sputtering, invece, impiega un campo magnetico per aumentare la ionizzazione degli atomi bersaglio, che vengono poi accelerati verso il substrato. Questa tecnica offre un migliore controllo delle proprietà del rivestimento, tra cui la densità e l'uniformità, rendendola ideale per le applicazioni che richiedono rivestimenti precisi. Nonostante questi vantaggi, lo sputtering magnetronico può essere più lento e richiedere più energia rispetto alla placcatura multiarco.
Metodo | Vantaggi | Svantaggi |
---|---|---|
Placcatura multiarco | Elevata velocità di deposizione, adatta a geometrie complesse | Contaminazione da particelle, spessore del rivestimento non uniforme |
Sputtering con magnetron | Eccellente controllo delle proprietà del rivestimento, alta densità e uniformità | Processo più lento, maggiore consumo energetico |
La comprensione di questi metodi e dei rispettivi pro e contro è fondamentale per selezionare la tecnica PVD più appropriata per specifiche applicazioni industriali.
Combinazione di tecnologie
L'integrazione delle tecnologie multi-arco e magnetron rappresenta un progresso significativo nel campo del rivestimento sotto vuoto. Questa combinazione non è una semplice somma di parti, ma un approccio sinergico che massimizza i vantaggi di entrambe le tecnologie, garantendo la produzione di rivestimenti stabili e di alta qualità.
La placcatura ad arco multiplo, nota per le sue elevate velocità di deposizione e per la capacità di produrre rivestimenti densi, è complementare allo sputtering magnetronico, che eccelle nella produzione di rivestimenti uniformi e conformali con un riscaldamento minimo del substrato. Combinando questi metodi, i produttori possono raggiungere un equilibrio tra velocità di deposizione e uniformità del rivestimento, fondamentale per le applicazioni che richiedono efficienza e precisione.
Inoltre, l'ibridazione di queste tecnologie consente di ottimizzare le proprietà del rivestimento. Ad esempio, l'incorporazione di ioni multi-arco nel processo di sputtering magnetronico può migliorare l'adesione e la durezza dei rivestimenti, affrontando sfide comuni nel rivestimento degli stampi industriali, dove sono fondamentali una maggiore adesione e durata.
Questa integrazione apre anche nuove strade per la selezione dei materiali e il controllo del processo. Sfruttando i punti di forza di entrambe le tecnologie, è possibile depositare una gamma più ampia di materiali con proprietà personalizzate, da rivestimenti duri e resistenti all'usura a strutture multistrato più complesse. Il risultato è una soluzione di rivestimento più versatile e robusta, in grado di soddisfare le diverse esigenze delle varie applicazioni industriali.
In sintesi, la combinazione delle tecnologie multi-arco e magnetron non solo migliora la qualità e la stabilità dei rivestimenti, ma amplia anche l'ambito delle proprietà dei materiali e delle efficienze di processo ottenibili. Questo progresso è fondamentale per spingere i confini di ciò che la tecnologia di rivestimento sotto vuoto può raggiungere, rendendola una pietra miliare nell'evoluzione dei rivestimenti industriali.
Apparecchiature e processi di rivestimento moderni
Componenti e sistemi
Le moderne apparecchiature di rivestimento sono un insieme sofisticato di componenti essenziali, ognuno dei quali svolge un ruolo cruciale nel processo di deposizione sotto vuoto. Il cuore di questo sistema è lacamera del vuotoun ambiente sigillato che isola il substrato dalle condizioni atmosferiche, garantendo una superficie incontaminata per il rivestimento. La camera da vuoto è in genere costruita con materiali come l'acciaio inossidabile, noti per la loro durata e resistenza alla corrosione.
Per raggiungere i livelli di vuoto necessari,parti che ottengono il vuoto per ottenere il vuoto. Queste includono pompe per vuoto, come le pompe rotative a palette e le pompe turbo-molecolari, che lavorano in tandem per ridurre la pressione della camera ai livelli ultra-bassi richiesti per i processi PVD. L'efficienza di queste pompe è fondamentale, poiché influisce direttamente sulla qualità e sull'uniformità del rivestimento.
Gli alimentatori sono un altro componente critico, in quanto forniscono l'energia elettrica necessaria per vaporizzare il materiale di rivestimento. I sistemi moderni utilizzano spessoalimentatori a frequenza intermedia otecnologia a impulsiche offrono un controllo preciso del processo di deposizione, consentendo di ottenere rivestimenti di qualità superiore. Questi alimentatori avanzati aiutano a mitigare problemi come l'arco elettrico e la deposizione non uniforme, problemi comuni nelle configurazioni PVD tradizionali.
Infine, isistemi di ingresso del gas di processo sono parte integrante del funzionamento. Questi sistemi introducono gas reattivi nella camera da vuoto, consentendo la formazione di rivestimenti complessi con proprietà personalizzate. Il controllo preciso delle portate e della composizione dei gas consente di creare rivestimenti con specifiche caratteristiche meccaniche, chimiche e ottiche, aumentando la versatilità e l'applicabilità della tecnologia.
In sintesi, la moderna apparecchiatura di rivestimento è una complessa interazione di camere da vuoto, parti che ottengono il vuoto, alimentatori e sistemi di immissione del gas di processo, ognuno dei quali contribuisce alla precisione e alla qualità del processo PVD.
Tecniche avanzate
Nel campo della tecnologia di rivestimento sotto vuoto, sono emerse diverse tecniche avanzate che hanno migliorato in modo significativo la qualità e l'applicabilità dei rivestimenti. Una di queste tecniche è l'utilizzo dicampi magnetici non in equilibrio. Questi campi permettono un controllo più preciso del processo di deposizione, consentendo la creazione di rivestimenti con uniformità e adesione superiori. Ciò è particolarmente vantaggioso nelle applicazioni industriali, dove la durata e le prestazioni del rivestimento sono fondamentali.
Un altro progresso fondamentale è l'introduzione di alimentatori aalimentatori a frequenza intermedia. A differenza degli alimentatori tradizionali, questi sistemi a frequenza intermedia offrono maggiore stabilità ed efficienza. Essi facilitano la deposizione di rivestimenti più spessi e robusti senza compromettere l'integrità del materiale sottostante. Questa innovazione è particolarmente utile nei settori che richiedono rivestimenti ad alte prestazioni per stampi e utensili.
Inoltre,tecnologia a impulsi ha rivoluzionato il processo di rivestimento. Fornendo energia in brevi e controllate esplosioni, la tecnologia a impulsi riduce al minimo lo stress termico sul substrato, evitando deformazioni e degradazioni. Questo metodo è particolarmente vantaggioso per i materiali delicati o che richiedono trattamenti superficiali complessi. L'erogazione precisa di energia garantisce inoltre un'adesione più efficace del rivestimento, con risultati più duraturi e affidabili.
Queste tecniche avanzate contribuiscono all'evoluzione della tecnologia di rivestimento sotto vuoto, rendendola più versatile ed efficace in diverse applicazioni industriali. L'integrazione di campi magnetici non in equilibrio, alimentatori a frequenza intermedia e tecnologia a impulsi non solo migliora la qualità dei rivestimenti, ma ne amplia anche l'applicabilità, soddisfacendo le esigenze sempre più stringenti delle industrie moderne.
Applicazione e controllo di qualità della PVD per stampi
Processi di pretrattamento e rivestimento
I metodi di pretrattamento sono fasi cruciali nella preparazione delle superfici per il rivestimento con deposizione fisica da vapore (PVD). Questi metodi includono la pulizia con vapore ad alta temperatura, che rimuove efficacemente i contaminanti e garantisce un substrato pulito. La sabbiatura è un'altra tecnica fondamentale, in quanto fornisce una superficie ruvida che migliora l'adesione del rivestimento. Il processo di rivestimento PVD stesso si basa molto sul controllo preciso della temperatura e sul riscaldamento uniforme per ottenere risultati ottimali.
Il riscaldamento uniforme è essenziale perché garantisce un riscaldamento uniforme del substrato, che a sua volta consente una deposizione uniforme del materiale di rivestimento. Il controllo della temperatura è altrettanto importante, poiché le deviazioni possono portare a incongruenze nello spessore e nella qualità del rivestimento. Per mantenere condizioni di riscaldamento stabili e costanti si ricorre spesso a tecniche avanzate come gli alimentatori a frequenza intermedia e la tecnologia a impulsi, migliorando così la qualità complessiva del rivestimento PVD.
Questi processi di pretrattamento e rivestimento sono parte integrante del successo delle applicazioni PVD negli stampi industriali. Non solo migliorano la durata e le prestazioni degli stampi, ma ne prolungano anche la vita operativa, rendendoli indispensabili negli ambienti di produzione ad alta precisione.
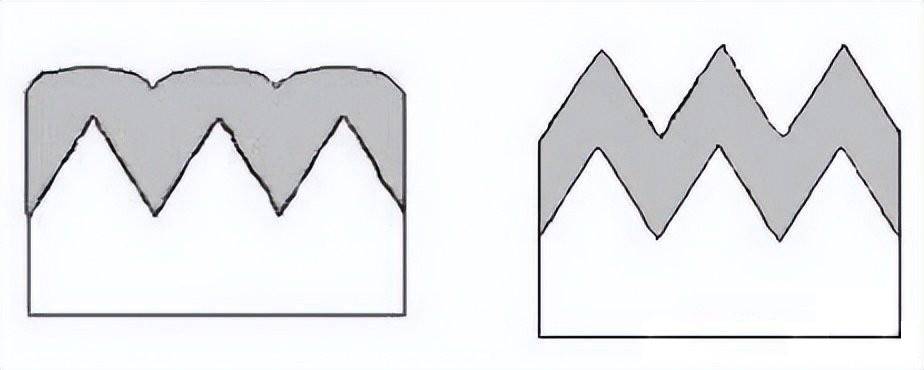
Misure di controllo della qualità
Il controllo della qualità funzionale (FQC) è un aspetto fondamentale per garantire l'affidabilità e le prestazioni degli stampi rivestiti. Questo processo comprende diverse ispezioni meticolose per garantire che i rivestimenti soddisfino gli standard richiesti.
Uno dei metodi principali del CQA è l'ispezione dell'aspetto.ispezione dell'aspetto. Si tratta di un esame visivo approfondito per individuare eventuali imperfezioni della superficie, come graffi, buchi o scolorimenti. Questi difetti possono avere un impatto significativo sulla funzionalità e sulla durata dello stampo, rendendo questa fase indispensabile.
Un altro metodo fondamentale è l'ispezioneispezione della profondità dello strato. Questa tecnica misura lo spessore degli strati di rivestimento per garantire che rispettino i parametri specificati. Per determinare con precisione la profondità e l'uniformità del rivestimento si utilizzano diversi strumenti, come profilometri e microscopi elettronici a scansione.
L'ispezioneispezione dell'adesione è altrettanto cruciale. Questo processo valuta la forza di adesione tra il rivestimento e il substrato dello stampo. I metodi più comuni includono test di graffiatura, test di trazione e test di taglio trasversale. Questi test aiutano a identificare eventuali problemi di delaminazione o distacco, garantendo la durata e l'efficacia del rivestimento.
Integrando questi metodi FQC, i produttori possono garantire che i loro stampi rivestiti non solo soddisfino, ma superino gli standard industriali, fornendo strumenti affidabili e ad alte prestazioni per varie applicazioni industriali.
CONTATTATECI PER UNA CONSULENZA GRATUITA
I prodotti e i servizi di KINTEK LAB SOLUTION sono stati riconosciuti da clienti di tutto il mondo. Il nostro personale sarà lieto di assistervi per qualsiasi richiesta. Contattateci per una consulenza gratuita e parlate con uno specialista del prodotto per trovare la soluzione più adatta alle vostre esigenze applicative!