Introduzione allo sputtering di magnetron
Panoramica dello sputtering con magnetron
Lo sputtering magnetronico è una sofisticata tecnica di preparazione di film sottili che prevede l'espulsione di atomi o molecole da un materiale target in un ambiente sotto vuoto. Le particelle espulse vengono poi depositate su un substrato, formando un film sottile. Il processo può essere classificato in tre tipi principali in base alla frequenza dell'alimentazione utilizzata: Sputtering in corrente continua, sputtering a media frequenza (MF) e sputtering a radiofrequenza (RF).
Il concetto fondamentale dello sputtering con magnetron è relativamente semplice, ma i meccanismi sottostanti sono piuttosto complessi. Una delle caratteristiche principali dello sputtering magnetronico, rispetto ai sistemi di base a diodi o a corrente continua, è l'introduzione di un forte campo magnetico vicino all'area del bersaglio. Questo campo magnetico svolge un ruolo cruciale nel processo, in quanto fa sì che gli elettroni si muovano a spirale lungo le linee di flusso magnetico, confinando così il plasma in una regione molto vicina al bersaglio. Questo confinamento impedisce al plasma di danneggiare il film sottile che si sta formando sul substrato.
In una tipica configurazione di sputtering magnetronico, una camera viene prima evacuata ad alto vuoto per ridurre al minimo il gas di fondo e i potenziali contaminanti. Successivamente, un gas di sputtering, che forma il plasma, viene introdotto nella camera e la pressione viene regolata al milliTorr. Il plasma, generato dall'interazione del gas di sputtering con il materiale del bersaglio, provoca l'erosione della superficie del bersaglio da parte di ioni ad alta energia. Gli atomi liberati attraversano il vuoto e si depositano sul substrato, formando il film sottile desiderato.
L'aggiunta di un campo magnetico nello sputtering magnetronico non solo aumenta l'efficienza del processo, ma consente anche una deposizione del film più controllata e uniforme. Ciò rende lo sputtering magnetronico il metodo preferito per le applicazioni che richiedono film sottili di alta qualità, uniformi e densi.
Tipi di tecniche di sputtering
Sputtering in corrente continua
Lo sputtering in corrente continua è una tecnica fondamentale nell'ambito dei processi di rivestimento a film sottile con deposizione fisica da vapore (PVD). Funziona utilizzando un'alimentazione a corrente continua (DC) per ionizzare il materiale target, generando così un plasma sulla sua superficie. Questo plasma è fondamentale perché facilita l'accelerazione degli ioni, che successivamente bombardano il materiale bersaglio. Questo bombardamento energetico provoca il rilascio di atomi o molecole dal bersaglio, che poi si condensano su un substrato vicino per formare un film sottile.
Una delle caratteristiche principali dello sputtering in corrente continua è la sua semplicità ed economicità, che lo rende una scelta ideale per la preparazione di film di base e per le applicazioni in cui il controllo preciso della velocità di deposizione non è fondamentale. Questa tecnica è ampiamente utilizzata in diversi settori industriali, tra cui quello dei semiconduttori per i circuiti dei microchip e in applicazioni decorative come i rivestimenti d'oro su gioielli e orologi. Inoltre, lo sputtering in corrente continua è utile per creare rivestimenti non riflettenti su vetro e componenti ottici, nonché per la produzione di plastica da imballaggio metallizzata.
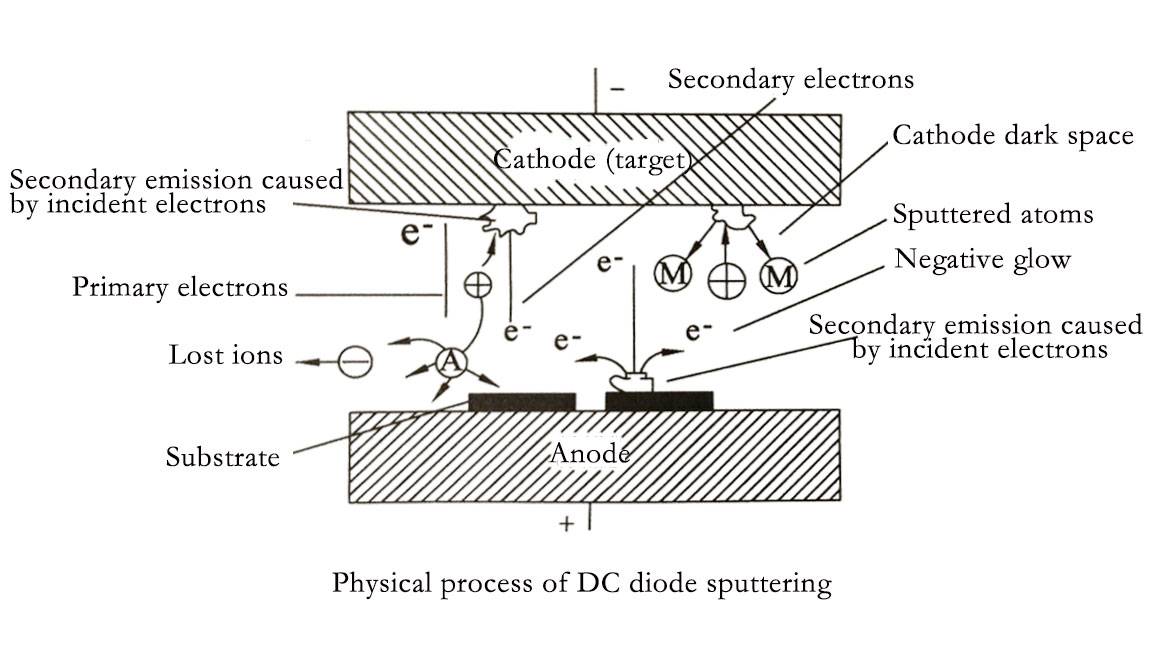
Il processo di sputtering in corrente continua inizia con l'applicazione di una tensione a un bersaglio metallico in un ambiente gassoso a bassa pressione, in genere argon. Gli ioni del gas, dopo la collisione con il bersaglio, espellono particelle microscopiche del materiale bersaglio, che vengono poi depositate sul substrato. Questo metodo garantisce un approccio semplice ed economico alla deposizione dei metalli, in particolare per il rivestimento di materiali target elettricamente conduttivi.
In sintesi, lo sputtering in corrente continua si distingue come metodo versatile e accessibile per la deposizione di film sottili, offrendo un mix equilibrato di semplicità, economicità e ampia applicabilità in diversi settori industriali.
Sputtering a media frequenza
Lo sputtering a media frequenza sfrutta un'alimentazione che opera a frequenze tipicamente comprese tra 50 kHz e 5 MHz per generare un ambiente di plasma stabile. Questa gamma di frequenze è stata scelta strategicamente perché consente un equilibrio tra le dinamiche degli ioni e degli elettroni, assicurando che gli ioni possano seguire il campo alternato mentre gli elettroni contribuiscono alla densità del plasma. Il risultato è un plasma con una maggiore energia di bombardamento ionico rispetto allo sputtering in corrente continua, che si traduce in un tasso di deposizione più controllato e uniforme.
Nello sputtering a media frequenza, il campo alternato accelera sia gli ioni che gli elettroni, ma a causa del minore rapporto carica/massa degli ioni, questi iniziano a ritardare a frequenze superiori a circa 50 kHz. Questo ritardo è vantaggioso perché aumenta il bombardamento ionico sul bersaglio, portando a un rilascio più efficiente di atomi o molecole. Gli elettroni, invece, oscillano all'interno del plasma, aumentando la frequenza di collisione con gli atomi di argon e quindi incrementando la velocità del plasma. Questo aumento della velocità del plasma consente di ridurre le pressioni operative, tipicamente nell'intervallo tra 10^-1 e 10^-2 Pa, pur mantenendo un'elevata velocità di sputtering.

L'ambiente a bassa pressione dello sputtering a media frequenza facilita la formazione di film sottili con microstrutture distinte, non ottenibili a pressioni più elevate. Questo metodo è particolarmente vantaggioso per la preparazione di film di alta qualità con proprietà quali alta velocità di deposizione, eccellente uniformità e stress interno minimo. Queste caratteristiche rendono lo sputtering a media frequenza ideale per applicazioni in film ottici, film magnetici e film conduttivi trasparenti, dove precisione e uniformità sono fondamentali.
Parametro | Sputtering a media frequenza |
---|---|
Frequenza di alimentazione | 50 kHz - 5 MHz |
Energia di bombardamento degli ioni | Più alta rispetto allo sputtering in corrente continua |
Velocità di deposizione | Più stabile e uniforme |
Pressione operativa | Da 10^-1 a 10^-2 Pa |
Applicazioni | Film ottici, film magnetici, film conduttivi trasparenti |
Sputtering a radiofrequenza
Lo sputtering a radiofrequenza (RF Sputtering) è una tecnica sofisticata che impiega un'alimentazione a radiofrequenza, tipicamente operante a 13,56 MHz, per creare un ambiente di plasma stabile. Questo metodo è particolarmente vantaggioso per la deposizione di materiali isolanti, che sono intrinsecamente non conduttivi. Il processo prevede l'alternanza del potenziale elettrico a frequenze radio, che "pulisce" efficacemente la superficie del materiale bersaglio impedendo l'accumulo di cariche. Durante il ciclo positivo, gli elettroni sono attratti dal bersaglio, dandogli una polarizzazione negativa, mentre durante il ciclo negativo il bombardamento di ioni continua senza sosta.
Questa tecnica garantisce che il materiale del bersaglio rimanga libero dall'accumulo di cariche, il che è fondamentale per mantenere l'uniformità e la densità dei film depositati. L'uso dello sputtering a radiofrequenza è molto vantaggioso negli ambienti in cui è necessario rivestire materiali isolanti senza compromettere la qualità del film. La capacità di controllare con precisione il plasma e l'energia del bombardamento ionico consente di ottenere film non solo uniformi ma anche eccezionalmente densi, rendendo lo sputtering RF ideale per le applicazioni che richiedono film di alta qualità e di elevata uniformità.
Lo sputtering a radiofrequenza è stato utilizzato fin dagli anni '60, con le prime applicazioni tra cui la deposizione di film di SiO₂ su substrati di silicio da parte della BM Company negli Stati Uniti. I progressi storici e tecnologici in questo campo sottolineano la sua affidabilità ed efficacia nella produzione di film ad alte prestazioni, come film metallici, film di leghe, film piezoelettrici, film ferroelettrici e film superconduttori ad alta temperatura.
Applicazioni e caratteristiche dei diversi metodi di sputtering
Applicazioni dello sputtering in corrente continua
Lo sputtering in corrente continua è una tecnica versatile che eccelle nella creazione di film sottili con proprietà specifiche per varie applicazioni industriali. Questi film presentano spesso strutture cristalline amorfe o microcristalline, che contribuiscono alle loro caratteristiche meccaniche e chimiche uniche.
Una delle caratteristiche principali dei film DC Sputtering è l'elevata tensione interna. Questa proprietà li rende particolarmente adatti ai rivestimenti resistenti all'usura, dove la durata e la resistenza all'abrasione meccanica sono fondamentali. Per esempio, nell'industria dei semiconduttori, lo Sputtering DC viene utilizzato per creare circuiti di microchip a livello molecolare, assicurando che i film possano resistere ai rigori della produzione e del funzionamento.
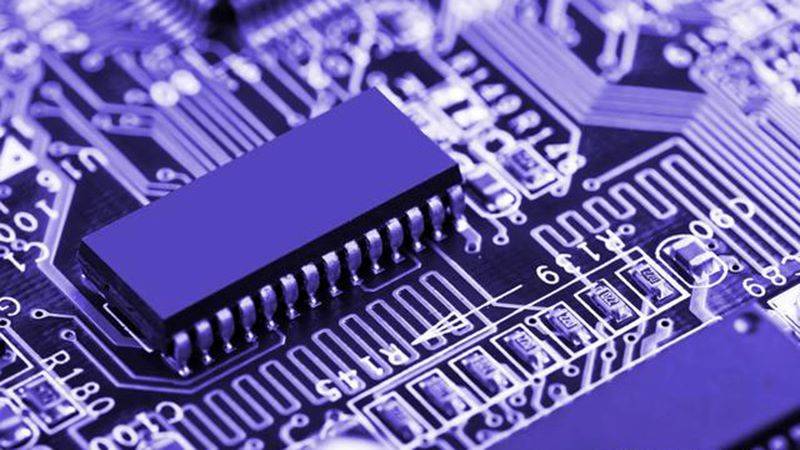
Oltre alla resistenza all'usura, il DC Sputtering è anche in grado di produrre film antiossidanti. Questi film sono fondamentali negli ambienti in cui i materiali sono esposti a condizioni ossidative, come in alcune applicazioni di lavorazione chimica o ad alta temperatura. La capacità di creare film superficiali con microstrutture specifiche ne aumenta ulteriormente l'utilità, rendendoli ideali per una serie di applicazioni di ingegneria superficiale.
Lo sputtering in corrente continua non si limita agli usi industriali, ma trova applicazione anche nei beni di consumo. Ad esempio, viene utilizzato per i rivestimenti di oro sputtering su gioielli, orologi e altri oggetti decorativi, fornendo una finitura lucida che è sia durevole che esteticamente piacevole. Analogamente, i rivestimenti non riflettenti su vetro e componenti ottici sono un'altra area in cui lo sputtering CC brilla, migliorando la funzionalità e le prestazioni di questi prodotti.
Inoltre, lo Sputtering DC è impiegato nella creazione di plastiche da imballaggio metallizzate, essenziali per il confezionamento degli alimenti e per altre applicazioni che richiedono una barriera contro l'umidità e i gas. La capacità di controllare e ottimizzare il processo di deposizione con l'alimentazione in corrente continua lo rende una scelta economica e affidabile per queste applicazioni.
In sintesi, la capacità dello sputtering in corrente continua di produrre film con sollecitazioni interne controllate, microstrutture personalizzate e proprietà meccaniche specifiche lo rende uno strumento prezioso in diversi settori, dai semiconduttori ai beni di consumo.
Applicazioni dello sputtering a media frequenza
Lo sputtering a media frequenza si distingue per la sua capacità di produrre film di alta qualità con un'elevata velocità di deposizione, un'eccezionale uniformità e uno stress interno minimo. Questa tecnica è particolarmente indicata per una serie di applicazioni avanzate di film, tra cui film ottici, film magnetici e film conduttivi trasparenti.
Uno dei vantaggi principali dello sputtering a media frequenza è la capacità di gestire materiali che richiedono un controllo preciso del processo di deposizione. Ad esempio, i film ottici richiedono un alto grado di uniformità e basse sollecitazioni interne per garantire prestazioni ottimali in dispositivi come lenti e specchi. I film magnetici, utilizzati per l'archiviazione dei dati e i sensori magnetici, traggono vantaggio dall'elevata velocità di deposizione e dalle basse sollecitazioni, che contribuiscono alla loro durata e alle loro prestazioni. Allo stesso modo, i film conduttivi trasparenti, essenziali negli schermi tattili e nelle celle solari, richiedono sia un'elevata trasparenza che una conduttività che lo sputtering a media frequenza è in grado di fornire efficacemente.
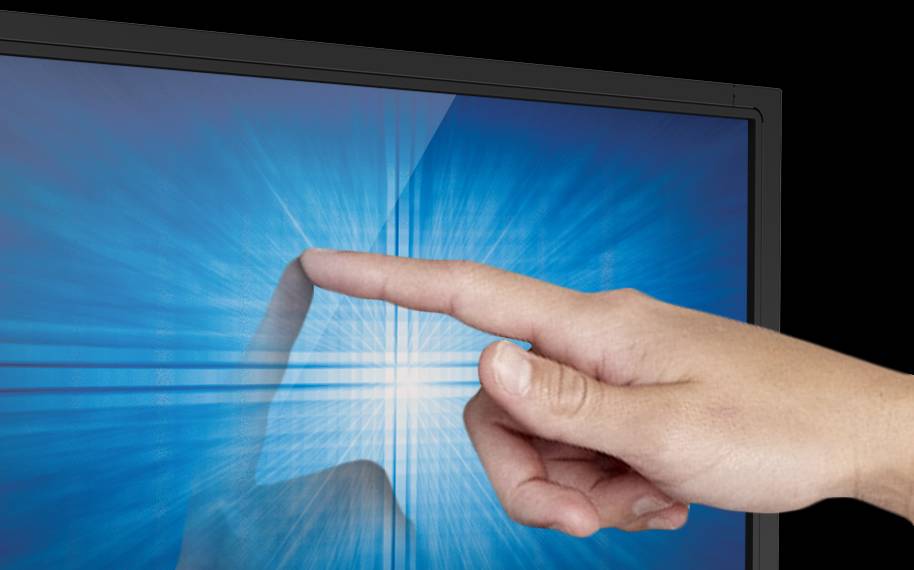
L'uso della potenza a media frequenza nello sputtering consente di ottenere un ambiente di plasma stabile, aumentando l'energia di bombardamento degli ioni e portando a una deposizione del film più controllata e uniforme. Questa stabilità è fondamentale per la preparazione di film che devono soddisfare criteri di prestazione rigorosi, rendendo lo sputtering a media frequenza uno strumento indispensabile per la produzione di film sottili avanzati.
Applicazioni dello sputtering RF
Lo sputtering a radiofrequenza è emerso come una tecnica versatile e indispensabile in diverse industrie high-tech, grazie alla sua capacità di produrre film ad alta densità e alta uniformità. Questo metodo è particolarmente apprezzato per la creazione di film di alta qualità e ad alte prestazioni, come film metallici, film di leghe, film piezoelettrici, film ferroelettrici e film superconduttori ad alta temperatura. I vantaggi unici dello sputtering a radiofrequenza, come la minore pressione in camera e l'uso di un'alimentazione a radiofrequenza, lo rendono ideale per la manipolazione di materiali target con qualità isolanti, che spesso sono difficili da gestire con metodi alternativi come lo sputtering a corrente continua.
Uno dei progressi più significativi dello sputtering RF è la sua applicazione nella deposizione di ossidi altamente isolanti. Questi ossidi, tra cui l'ossido di alluminio, l'ossido di tantalio e l'ossido di silicio, sono fondamentali per migliorare le prestazioni dei circuiti dei microchip nell'industria dei computer e dei semiconduttori. Controllando attentamente il processo di deposizione, lo sputtering a radiofrequenza garantisce che questi strati isolanti siano applicati in modo uniforme tra le superfici metalliche di destinazione, migliorando così l'efficienza e l'affidabilità complessiva dei dispositivi.
Si prevede che la domanda di film sputterati a radiofrequenza aumenterà nei prossimi anni, spinta dalla crescente necessità di miniaturizzazione dei dispositivi a film sottile e dai progressi nelle applicazioni nanotecnologiche. Questa crescita non si limita al settore dei semiconduttori, ma si estende a diversi campi come l'energia, l'optoelettronica, le scienze della vita, la meccanica e l'industria chimica. L'adattabilità e la precisione dello sputtering a radiofrequenza ne fanno una tecnica di elezione per un'ampia gamma di applicazioni, consolidando la sua posizione di tecnologia fondamentale nei moderni processi produttivi.
CONTATTATECI PER UNA CONSULENZA GRATUITA
I prodotti e i servizi di KINTEK LAB SOLUTION sono stati riconosciuti da clienti di tutto il mondo. Il nostro personale sarà lieto di assistervi per qualsiasi richiesta. Contattateci per una consulenza gratuita e parlate con uno specialista del prodotto per trovare la soluzione più adatta alle vostre esigenze applicative!