Introduzione alle atmosfere dei forni
Le atmosfere dei forni svolgono un ruolo essenziale nel processo di trattamento termico dei materiali. L'atmosfera all'interno di un forno può avere un impatto significativo sulle proprietà del prodotto finale, come la resistenza e la durata. L'atmosfera è un gas o una miscela di gas che circonda il materiale da trattare in un forno. Le atmosfere più comunemente utilizzate nei forni sono aria, azoto, idrogeno e argon. La comprensione delle proprietà di ciascuna atmosfera e dei suoi effetti sul materiale è fondamentale per ottenere prodotti di alta qualità. L'uso di atmosfere inerti, come l'azoto e l'argon, è importante per prevenire reazioni indesiderate e ossidazioni durante il processo di trattamento termico.
Indice dei contenuti
- Introduzione alle atmosfere dei forni
- Che cos'è un'atmosfera inerte?
- Perché è importante utilizzare atmosfere inerti?
- Gas comuni nelle atmosfere dei forni
- Processi di trattamento termico che richiedono atmosfere inerti
- Come misurare l'atmosfera del forno
- Strumenti per la misurazione e il campionamento
- Conclusioni sull'importanza delle atmosfere inerti
Che cos'è un'atmosfera inerte?
Nel lavoro di laboratorio, è essenziale creare un ambiente controllato per determinate reazioni o processi. Uno di questi ambienti è l'atmosfera inerte, caratterizzata dall'assenza di gas reattivi che potrebbero interferire con il risultato desiderato. Per creare questo ambiente si utilizzano comunemente gas inerti come l'azoto, l'argon e l'elio, che possono essere ottenuti con tecniche come lo spurgo, il blanketing o l'uso di scatole a guanti.
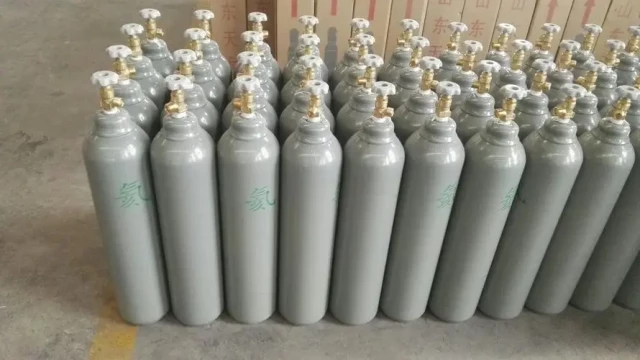
Definizione di atmosfera inerte
Un'atmosfera inerte è un ambiente controllato utilizzato per varie applicazioni di laboratorio e industriali, in cui l'atmosfera è priva di gas reattivi che potrebbero causare reazioni chimiche indesiderate. Per creare questo tipo di ambiente vengono comunemente utilizzati gas inerti, come azoto, argon ed elio. Questi gas sono considerati inerti in quanto non reagiscono chimicamente con altre sostanze e sono quindi ideali per creare un ambiente controllato.
Creazione di un'atmosfera inerte
Esistono diversi modi per creare un'atmosfera inerte, tra cui il purging, il blanketing e l'uso di glove box. Lo spurgo consiste nel rimuovere tutta l'aria da un contenitore o da un sistema e sostituirla con un gas inerte. Il blanketing consiste nel riempire un contenitore con un gas inerte per creare uno strato di gas che impedisca l'ingresso di aria o altri gas reattivi. I glove box sono spazi di lavoro chiusi che utilizzano un'atmosfera di gas inerte per creare un ambiente controllato.
Usi delle atmosfere inerti
Le atmosfere inerti sono utilizzate in varie applicazioni di laboratorio e industriali, compresi i processi di trattamento termico come la sinterizzazione, la ricottura brillante e la carbonitrurazione. Questi processi richiedono atmosfere altamente controllate per produrre pezzi di qualità in settori come quello aerospaziale, automobilistico e petrolchimico. Le atmosfere inerti sono utilizzate anche nella produzione di semiconduttori, dove la purezza è fondamentale.
Gas inerti comuni
I gas inerti più comunemente utilizzati per creare un'atmosfera inerte sono azoto, argon ed elio. L'azoto è il gas inerte più economico e più diffuso e viene spesso utilizzato in applicazioni in cui è necessario eliminare l'umidità e l'ossigeno. L'argon è un gas più denso e viene comunemente utilizzato in applicazioni che richiedono una barriera di gas inerte più consistente. L'elio è il gas inerte più leggero e viene utilizzato in applicazioni che richiedono una bassa densità e un'elevata conduttività termica.
In conclusione, un'atmosfera inerte è un ambiente controllato in cui l'atmosfera è priva di gas reattivi che potrebbero interferire con il risultato desiderato. Questo ambiente è fondamentale nelle applicazioni di laboratorio e industriali, dove precisione e controllo sono essenziali. L'uso di gas in atmosfera inerte, come azoto, argon ed elio, è fondamentale per creare questo ambiente e garantire la qualità, l'affidabilità e la riproducibilità degli esperimenti di laboratorio e dei processi industriali.
Perché è importante utilizzare atmosfere inerti?
I gas in atmosfera inerte sono essenziali per molti processi di trattamento termico grazie alla loro capacità di creare un ambiente controllato che impedisce reazioni chimiche indesiderate, ossidazione e contaminazione del prodotto. In questa sezione, discuteremo i motivi per cui è importante utilizzare atmosfere inerti nelle atmosfere dei forni.
Prevenzione delle reazioni chimiche indesiderate
Quando si lavora con il trattamento termico, la sinterizzazione o la brasatura, la presenza di alcuni gas come l'ossigeno o il vapore acqueo può causare ossidazione o altre reazioni chimiche indesiderate. I gas inerti, come l'azoto, l'argon e l'elio, vengono utilizzati per spostare l'ossigeno e il vapore acqueo dalla camera del forno, creando un'atmosfera priva di gas reattivi. In questo modo si garantisce il controllo del processo e il raggiungimento del risultato desiderato.
Miglioramento della qualità del prodotto
L'utilizzo di gas inerti può aumentare l'efficienza del processo, riducendo la quantità di energia necessaria per raggiungere la temperatura desiderata e accelerando il processo di raffreddamento. Inoltre, l'atmosfera inerte aiuta a prevenire l'ossidazione e la contaminazione del prodotto, garantendo un risultato finale di qualità superiore. Questo aspetto è particolarmente importante per i settori aerospaziale, automobilistico o petrolchimico, dove si producono parti critiche.
Precisione e ripetibilità
Per i processi di trattamento termico che richiedono un'atmosfera altamente controllata, come la ricottura brillante, la sinterizzazione e la carbonitrurazione, è essenziale ottenere precisione e ripetibilità. I forni utilizzati in questi processi devono supportare un'atmosfera controllata per ottenere risultati di successo, di alta precisione e ripetibili per questi pezzi. Per garantire il controllo del processo e l'ottenimento del risultato desiderato, si utilizzano atmosfere inerti.
Riduzione dei danni ai forni e degli infortuni dei dipendenti
Un'atmosfera non adeguatamente controllata può causare il danneggiamento di un forno o, peggio ancora, l'infortunio dei dipendenti. I gas inerti sono utilizzati per prevenire reazioni chimiche sulla superficie di un pezzo che ne comprometterebbero la qualità e le prestazioni, con conseguenti scarti. Questo, a sua volta, comporta perdite economiche, perdite di tempo e ripercussioni potenzialmente pericolose per coloro che utilizzano il pezzo se i problemi non vengono rilevati.
In conclusione, l'uso di gas in atmosfera inerte nei forni è essenziale per garantire un processo controllato ed efficiente, prevenire reazioni chimiche indesiderate e produrre prodotti di alta qualità. È importante capire perché li usiamo e qual è l'atmosfera migliore per un'applicazione specifica per ottenere risultati di successo, di alta precisione e ripetibili.
Gas comuni nelle atmosfere dei forni
I gas in atmosfera inerte svolgono un ruolo fondamentale nelle atmosfere dei forni per prevenire reazioni chimiche indesiderate o l'ossidazione dei materiali durante la lavorazione ad alta temperatura. I gas più comuni utilizzati per le applicazioni in atmosfera inerte sono azoto, argon ed elio.
L'azoto
L'azoto è il gas più comunemente utilizzato per la sua disponibilità e convenienza. È un gas non reattivo che fornisce un'atmosfera protettiva. Il suo contenuto di carbonio, ossigeno e azoto non reagisce con l'acciaio, rendendolo un gas ideale per le atmosfere dei forni. L'azoto è utilizzato per prevenire l'ossidazione nelle applicazioni di trattamento termico ed è efficace nel sostituire l'ossigeno dall'atmosfera.
Argon
L'argon è spesso utilizzato per processi che richiedono un livello di purezza più elevato o un periodo prolungato di lavorazione ad alta temperatura. L'argon è un gas "nobile" completamente inerte e non reagisce con nessun materiale con cui viene a contatto. Si sostituisce all'ossigeno ed è quindi un gas ideale per le applicazioni in cui l'ossidazione è indesiderata. L'argon è più costoso dell'azoto, ma ha il vantaggio di poter essere utilizzato a temperature superiori a 1800°C senza alcun rischio di reazione.
Elio
L'elio viene utilizzato quando è richiesta una bassa solubilità, in quanto è il gas meno reattivo. La sua bassa densità e l'elevata conducibilità termica lo rendono un gas ideale per alcune applicazioni. L'elio è spesso utilizzato nella gascromatografia, nel rilevamento di perdite e nelle applicazioni di raffreddamento.
In sintesi, questi gas creano un ambiente privo di ossigeno che protegge i materiali in lavorazione e garantisce risultati coerenti e accurati. Senza l'uso di gas in atmosfera inerte, possono verificarsi reazioni indesiderate, con conseguenti difetti del prodotto, diminuzione della qualità e persino danni alle apparecchiature. La scelta del gas dipende dai requisiti specifici del processo di trattamento termico e il tipo di atmosfera richiesta determina il tipo di forno necessario per eseguirlo.
Processi di trattamento termico che richiedono atmosfere inerti
I processi di trattamento termico che richiedono temperature elevate e atmosfere controllate si affidano spesso a gas in atmosfera inerte come azoto, argon ed elio. Questi gas svolgono un ruolo cruciale nel creare un ambiente privo di ossigeno e di altri gas reattivi che potrebbero causare reazioni chimiche o l'ossidazione dei materiali trattati.
Perché le atmosfere inerti sono essenziali
L'assenza di ossigeno e di altri gas reattivi nell'atmosfera del forno contribuisce a mantenere la purezza dei materiali e a prevenire contaminazioni o reazioni indesiderate. Le atmosfere inerti sono essenziali per un'ampia gamma di applicazioni, tra cui il trattamento termico dei metalli, la ricottura del vetro e la sinterizzazione della ceramica. L'uso di gas inerti nelle atmosfere dei forni è fondamentale per garantire la qualità e la coerenza dei prodotti finali. Qualsiasi deviazione nell'atmosfera del forno può avere un impatto significativo sulle proprietà del prodotto finale, rendendo essenziale mantenere un controllo rigoroso sull'ambiente del forno.
Gas inerti utilizzati nei processi di trattamento termico
Argon, elio e azoto sono i gas inerti più comunemente utilizzati nei processi di trattamento termico. La scelta del gas inerte dipende dal tipo di materiale da trattare e dai requisiti specifici del processo di trattamento termico. In generale, l'argon e l'elio sono più inerti dell'idrogeno. Un'atmosfera di azoto puro fornisce una copertura della parte da trattare termicamente e può essere utilizzata per spurgare l'atmosfera esistente o come gas di trasporto per le atmosfere a controllo di carbonio.
Processi di trattamento termico che utilizzano atmosfere inerti
Le atmosfere inerti sono utilizzate in un'ampia gamma di processi di trattamento termico, tra cui:
- ricottura (metalli non ferrosi, acciai legati e decarburazione)
- Tempra neutra
- rinvenimento
- Nitrurazione (acciai legati, acciai inossidabili e acciai da nitrurazione)
- Sinterizzazione
- Brasatura (l'azoto funge da gas vettore)
- Processi sotto vuoto
Combinazioni di gas inerti
In alcuni casi, nei processi di trattamento termico si può utilizzare una combinazione di gas inerti. Ad esempio, un'atmosfera di idrogeno + azoto funziona bene per la ricottura lucida, la ricottura di acciaio inossidabile, acciaio legato e non ferroso, la tempra neutra e la sinterizzazione. L'utilizzo di un'atmosfera di idrogeno + argon funziona con la ricottura brillante, la ricottura di acciaio inossidabile, acciaio legato e non ferroso e la sinterizzazione.
Conclusioni
In sintesi, i gas in atmosfera inerte svolgono un ruolo fondamentale nei processi di trattamento termico che richiedono temperature elevate e atmosfere controllate. L'uso di questi gas aiuta a mantenere la purezza dei materiali e a prevenire contaminazioni o reazioni indesiderate. La scelta del gas inerte dipende dallo specifico processo di trattamento termico e dal tipo di materiale da trattare. Le atmosfere inerti sono essenziali per garantire prodotti finali di alta qualità nell'industria del trattamento termico.
Come misurare l'atmosfera del forno
La misurazione dell'atmosfera del forno è una fase cruciale per garantire che i gas dell'atmosfera inerte funzionino correttamente e che il processo si svolga senza intoppi. Di seguito sono descritte le fasi di misurazione dell'atmosfera del forno.
Fase 1: Determinare il tipo di analizzatore
Esistono diversi metodi per misurare l'atmosfera del forno, tra cui gli analizzatori a conducibilità termica, a infrarossi e a zirconia. Ogni metodo ha i suoi punti di forza e di debolezza e la scelta dell'analizzatore appropriato dipende dall'applicazione specifica e dal tipo di gas utilizzati.
Fase 2: calibrazione dell'analizzatore
Prima di utilizzare l'analizzatore, è importante calibrarlo per garantire una lettura accurata. La calibrazione consiste nell'esporre l'analizzatore a una miscela di gas nota e nel regolarlo finché non legge i valori corretti.
Fase 3: Installazione dell'analizzatore
Installare l'analizzatore nel forno o nel punto di campionamento del flusso di gas di scarico, a seconda del tipo di analizzatore.
Fase 4: Eseguire la misurazione
Una volta installato l'analizzatore, effettuare la misurazione. La frequenza delle misurazioni dipende dall'applicazione specifica, ma è importante monitorare regolarmente l'atmosfera del forno per mantenerne l'integrità e garantire una qualità costante del prodotto.
Fase 5: Interpretare i risultati
Interpretare i risultati ottenuti dall'analizzatore e, se necessario, adottare misure correttive. Se i risultati indicano che l'atmosfera del forno non funziona correttamente, regolare i gas dell'atmosfera inerte per mantenere il corretto equilibrio.
Seguendo questi passaggi, i produttori possono ottimizzare i loro processi e produrre prodotti di alta qualità con precisione ed efficienza.
Strumenti per la misurazione e il campionamento
I gas in atmosfera inerte sono componenti cruciali delle atmosfere dei forni e garantire la loro sicurezza ed efficacia durante le operazioni ad alta temperatura è essenziale. La misurazione e il campionamento di questi gas è quindi un compito critico in laboratorio.
Analizzatori di gas
Gli analizzatori di gas sono strumenti sofisticati che eseguono analisi precise di campioni di gas, rilevando impurità e variazioni di concentrazione. Vengono utilizzati per misurare un'ampia gamma di parametri, tra cui ossigeno, anidride carbonica e vapore acqueo. Gli analizzatori di gas sono altamente sensibili e possono rilevare anche le minime variazioni nella composizione del gas, il che li rende ideali per il monitoraggio dei gas in atmosfera inerte.
Gascromatografi
I gascromatografi sono strumenti potenti in grado di separare e analizzare i singoli componenti di un campione di gas. Sono in grado di rilevare tracce di impurità e di misurare con precisione le concentrazioni di vari gas. I gascromatografi sono ampiamente utilizzati in laboratorio e possono essere impiegati per analizzare i gas in atmosfera inerte a fini di sicurezza e controllo qualità.
Apparecchiature di campionamento
Un'adeguata attrezzatura di campionamento è essenziale per misurare e monitorare i gas in atmosfera inerte. Le sacche di campionamento dei gas, ad esempio, sono utilizzate per raccogliere campioni di gas da analizzare, mentre le siringhe per gas sono utilizzate per estrarre i campioni direttamente da un flusso di gas. Altri tipi di apparecchiature di campionamento comprendono i rilevatori di gas, che possono rilevare la presenza di gas specifici, e i sensori di gas, che possono misurare le concentrazioni di gas in tempo reale.
Apparecchiature di calibrazione
Le apparecchiature di calibrazione sono essenziali per garantire l'accuratezza degli analizzatori di gas e di altri strumenti di misurazione dei gas. I gas di calibrazione, come l'azoto e l'ossigeno, sono utilizzati per calibrare gli analizzatori di gas e garantire letture accurate. Le apparecchiature di calibrazione sono utilizzate anche per verificare l'accuratezza dei sensori di gas e di altri strumenti di misura dei gas.
Vantaggi della misurazione e del campionamento di gas in atmosfera inerte
La misurazione e il campionamento dei gas in atmosfera inerte sono importanti per mantenere la sicurezza e la qualità dei processi di trattamento termico. Il campionamento e l'analisi regolari dei gas dell'atmosfera inerte possono aiutare a identificare potenziali problemi nelle operazioni del forno e a prevenire costosi danni alle apparecchiature. Inoltre, può aiutare i professionisti del laboratorio e gli ingegneri a ottimizzare i processi di trattamento termico, migliorando la qualità dei prodotti e riducendo i costi di produzione.
In conclusione, la misurazione e il campionamento dei gas in atmosfera inerte è un'attività critica in laboratorio. Analizzatori di gas, gascromatografi, apparecchiature di campionamento, apparecchiature di calibrazione e altri strumenti sono tutti componenti essenziali di questo processo. Misurando e monitorando regolarmente i gas in atmosfera inerte, i professionisti del laboratorio possono garantire la sicurezza e l'efficacia dei processi di trattamento termico e mantenere la qualità dei loro prodotti.
Conclusioni sull'importanza delle atmosfere inerti
Le atmosfere inerti svolgono un ruolo cruciale nel processo di trattamento termico dei materiali. Aiutano a prevenire l'ossidazione, la decarburazione o altre reazioni indesiderate che possono verificarsi in presenza di ossigeno o altri gas reattivi. Utilizzando gas inerti, come azoto o argon, nelle atmosfere dei forni, i materiali possono essere riscaldati e raffreddati in un ambiente controllato, garantendo risultati coerenti e affidabili. È importante misurare e monitorare l'atmosfera del forno per garantire il mantenimento delle condizioni desiderate. L'uso corretto delle atmosfere inerti può portare a un miglioramento della qualità del prodotto, a una riduzione degli scarti e a un aumento della produttività nell'industria del trattamento termico.
CONTATTATECI PER UNA CONSULENZA GRATUITA
I prodotti e i servizi di KINTEK LAB SOLUTION sono stati riconosciuti da clienti di tutto il mondo. Il nostro personale sarà lieto di assistervi per qualsiasi richiesta. Contattateci per una consulenza gratuita e parlate con uno specialista del prodotto per trovare la soluzione più adatta alle vostre esigenze applicative!