Introduzione alla deposizione da vapore di silicio-carbonio (VPD-SiC)
Vantaggi del VPD-SiC
Il VPD-SiC mostra miglioramenti sostanziali rispetto ai materiali convenzionali in diverse aree critiche, che lo rendono una scelta superiore per le applicazioni avanzate delle batterie. In primo luogo, l'efficienzaefficienza del primo giro del VPD-SiC è notevolmente superiore, il che si traduce in cicli iniziali di carica-scarica più efficaci e in una minore perdita di energia. Questo miglioramento è fondamentale per la rapida diffusione di batterie ad alte prestazioni in vari settori industriali.
Inoltre, il VPD-SiC aumenta significativamente ladensità energetica. Integrando le particelle di silicio in una matrice di carbonio poroso, il materiale può immagazzinare più energia per unità di volume o di massa, offrendo tempi operativi più lunghi e frequenze di ricarica ridotte. Ciò è particolarmente vantaggioso per l'elettronica portatile, i veicoli elettrici e i sistemi di accumulo di energia rinnovabile.
Leprestazioni ciclistiche del VPD-SiC è superiore, con una maggiore stabilità in caso di ripetuti cicli di carica e scarica. Questa durata è fondamentale per la longevità e l'affidabilità dei sistemi di batterie, garantendo prestazioni costanti per lunghi periodi senza degrado.
Inoltre, il VPD-SiC attenua in modo efficacel'espansione delle celle problemi di espansione delle celle comuni agli anodi tradizionali a base di silicio. La riduzione dell'espansione del volume durante i processi di carica e scarica contribuisce a mantenere l'integrità strutturale della batteria, aumentandone la durata e la sicurezza.
In termini diriduzione dei costiil VPD-SiC offre un promettente potenziale di industrializzazione. Il processo di sintesi semplificato, unito all'uso efficiente delle materie prime, può portare a metodi di produzione più convenienti. Questo vantaggio economico è essenziale per aumentare la produzione e rendere più accessibili le batterie ad alte prestazioni.
Nel complesso, i vantaggi completi del VPD-SiC in termini di efficienza al primo giro, densità energetica, prestazioni di ciclaggio, espansione delle celle e riduzione dei costi ne fanno un materiale trasformativo per la prossima generazione di tecnologie di batterie.
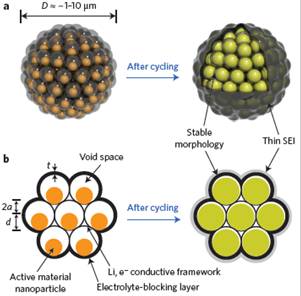
Fasi principali della tecnologia VPD-SiC
Il processo di deposizione in fase di vapore (VPD) per la creazione di materiali anodici in silicio-carbonio (SiC) è una procedura a più fasi che integra diversi passaggi critici per ottenere soluzioni di accumulo di energia ad alte prestazioni. La tecnologia può essere suddivisa in tre fasi principali: la preparazione di uno scheletro di carbonio poroso, la deposizione di particelle di silicio e l'applicazione di un rivestimento di carbonio.
-
Preparazione dello scheletro di carbonio poroso:
- La base del processo VPD-SiC, lo scheletro di carbonio poroso, viene realizzato meticolosamente per fornire una struttura robusta che migliora le prestazioni complessive del materiale. Questa fase è essenziale per creare una struttura con un'elevata area superficiale specifica e un'eccellente conduttività elettrica, fondamentali per migliorare la capacità dell'anodo e la stabilità del ciclo.
-
Deposizione di particelle di silicio:
- Una volta creato lo scheletro di carbonio poroso, la fase successiva prevede la deposizione di particelle di silicio all'interno dei pori. Questo processo si ottiene tipicamente attraverso l'uso di gas silano, che svolge un ruolo fondamentale nella formazione del silicio all'interno della matrice di carbonio. Il processo di deposizione è molto sensibile a parametri quali la temperatura e la portata del gas, che devono essere controllati con precisione per garantire una distribuzione uniforme delle particelle e proprietà ottimali del materiale.
-
Rivestimento dello strato di carbonio:
- La fase finale della tecnologia VPD-SiC consiste nel rivestimento del composito silicio-carbonio con uno strato di carbonio. Questo strato ha molteplici funzioni: protegge le particelle di silicio dalla degradazione, aumenta la conduttività elettrica del materiale e fornisce ulteriore stabilità meccanica. Il rivestimento di carbonio viene solitamente applicato mediante deposizione chimica da vapore (CVD) o altre tecniche simili, garantendo uno strato uniforme e continuo che incapsula efficacemente le particelle di silicio.
Ognuna di queste fasi è interdipendente e la loro integrazione è fondamentale per la produzione di materiali anodici silicio-carbonio di alta qualità che soddisfino i severi requisiti delle moderne applicazioni di stoccaggio dell'energia.
Sintesi dei materiali di carbonio poroso
Importanza del carbonio poroso
I materiali di carbonio poroso svolgono un ruolo fondamentale nell'ottimizzazione degli anodi di silicio-carbonio, migliorandone significativamente le prestazioni complessive. Questo miglioramento è attribuito principalmente a diverse proprietà chiave inerenti al carbonio poroso.
In primo luogo, l'elevata superficie specifica del carbonio poroso fornisce un'ampia piattaforma per la deposizione di particelle di silicio. Questa ampia superficie garantisce una distribuzione uniforme delle particelle di silicio, fondamentale per mantenere l'integrità strutturale e le prestazioni dell'anodo.
In secondo luogo, l'eccellente conduttività elettrica del carbonio poroso facilita un efficiente trasferimento di elettroni all'interno del materiale anodico. Questa proprietà è fondamentale per mantenere un'elevata efficienza energetica e ridurre la resistenza interna, elementi essenziali per le prestazioni e la durata a lungo termine dell'anodo.
Infine, la buona stabilità meccanica del carbonio poroso contribuisce alla resilienza strutturale dell'anodo. Questa stabilità è particolarmente importante durante i ripetuti cicli di carica e scarica, in quanto aiuta a mitigare i cambiamenti di volume che le particelle di silicio subiscono, prevenendo così la degradazione e prolungando la durata dell'anodo.
In sintesi, la combinazione di elevata area superficiale specifica, eccellente conducibilità elettrica e buona stabilità meccanica rende i materiali di carbonio poroso indispensabili per il progresso degli anodi di silicio-carbonio nella tecnologia delle batterie.
Considerazioni sulla sintesi
Quando si sintetizzano materiali di carbonio poroso per anodi di silicio-carbonio, è necessario considerare meticolosamente diversi fattori critici per garantire prestazioni ottimali e scalabilità. La progettazione della struttura dei pori è fondamentale, poiché influenza direttamente la capacità del materiale di adattarsi alle variazioni di volume durante i cicli di litizzazione e delitizzazione. Una struttura dei pori ben progettata può migliorare significativamente la stabilità del ciclo e la conservazione della capacità dell'anodo.
La selezione del precursore è un altro aspetto fondamentale. La scelta del precursore influisce non solo sulle proprietà finali del carbonio poroso, ma anche sulla facilità di sintesi e sul costo del materiale. In genere si preferiscono precursori con un'elevata resa in carbonio e un basso contenuto di ceneri, che facilitano la formazione di una matrice di carbonio uniforme e conduttiva. Inoltre, il precursore deve essere compatibile con tecniche di produzione scalabili per garantire la fattibilità della produzione su larga scala.
La scalabilità per la produzione su larga scala è una considerazione non negoziabile. Il processo di sintesi deve essere adattabile ai reattori su scala industriale, garantendo qualità e resa costanti. Ciò comporta l'ottimizzazione delle condizioni di reazione, come la temperatura, la pressione e le concentrazioni dei reagenti, per ottenere una deposizione uniforme delle particelle di silicio all'interno del carbonio poroso. Inoltre, il processo dovrebbe ridurre al minimo il consumo di energia e la produzione di rifiuti, allineandosi alle pratiche di produzione sostenibile.
In sintesi, la sintesi di materiali di carbonio poroso per anodi di silicio-carbonio richiede un approccio olistico, che bilanci la progettazione della struttura dei pori, la selezione dei precursori e la scalabilità per soddisfare le esigenze di prestazioni e applicazioni industriali.
Silano e processo di deposizione
Ruolo del gas silano
Il gas silano (SiH₄) svolge un ruolo fondamentale nella deposizione di particelle di silicio all'interno della struttura porosa del carbonio, una fase critica nella fabbricazione di materiali anodici in silicio-carbonio. L'efficacia di questo processo dipende dall'attenta gestione delle proprietà del silano e dall'intricato equilibrio dei parametri di deposizione.
Una delle sfide principali nell'utilizzo del silano è la sua sensibilità alle condizioni ambientali. Ad esempio, l'introduzione di ossigeno nella camera di deposizione può portare alla formazione di SiOH, che compromette la qualità del film di silicio. Al contrario, in assenza di ossigeno, si possono ottenere film di silicio amorfo, puro e adatto alla deposizione. Ciò evidenzia la necessità di un controllo preciso dell'ambiente di deposizione per evitare reazioni chimiche indesiderate.
Inoltre, il costo e la disponibilità del silano sono fattori significativi che influenzano la fattibilità della produzione su larga scala. Il materiale deve essere maneggiato con cura a causa della sua natura reattiva, che richiede attrezzature specializzate e protocolli di sicurezza per ridurre i rischi. Inoltre, il processo di deposizione richiede un delicato equilibrio tra silano e altri gas, come ossigeno e xeno, per ottenere il composito silicio-carbonio desiderato.
Per ottimizzare il processo di deposizione, è essenziale mantenere tassi medi di introduzione del silano. Un eccesso di silano può portare alla formazione di SIH, mentre un eccesso di ossigeno può portare alla formazione di SiOH, entrambi i quali degradano la qualità del prodotto finale. Raggiungere il giusto equilibrio è fondamentale per ottenere film di silicio amorfi e duri, che migliorano le caratteristiche prestazionali dell'anodo.
In sintesi, il ruolo del gas silano nel processo di deposizione è multiforme e richiede una profonda comprensione delle sue proprietà chimiche e un'attenta gestione dei parametri di deposizione per garantire la produzione di materiali anodici silicio-carbonio di alta qualità.
Parametri del processo di deposizione
I parametri del processo di deposizione svolgono un ruolo fondamentale nel determinare la qualità e le prestazioni dei materiali anodici silicio-carbonio (Si-C). I parametri chiave includono la temperatura di deposizione, le condizioni di reazione e le rigorose misure di sicurezza, ognuno dei quali influenza in modo significativo le caratteristiche del prodotto finale.
Influenza della temperatura
La temperatura di deposizione è un fattore critico che influenza direttamente l'uniformità e la densità delle particelle di silicio all'interno della matrice di carbonio poroso. Temperature più elevate possono migliorare la diffusione del gas silano nei pori del carbonio, portando a una deposizione più uniforme. Tuttavia, temperature troppo elevate possono anche causare la degradazione termica della struttura del carbonio, riducendone la stabilità meccanica e l'area superficiale specifica. Pertanto, l'ottimizzazione della temperatura di deposizione è essenziale per bilanciare questi effetti contrastanti.
Condizioni di reazione
Le condizioni di reazione, come la portata e la pressione del gas, sono altrettanto importanti. Queste condizioni determinano il tempo di permanenza dei reagenti all'interno della camera di deposizione e la velocità di formazione delle particelle di silicio. Ad esempio, un flusso di gas più elevato può portare a tempi di permanenza più brevi, riducendo potenzialmente l'uniformità della deposizione di silicio. Al contrario, una portata inferiore può migliorare il processo di deposizione, ma può anche aumentare il rischio di intasamento o altri problemi operativi. Pertanto, è necessario un controllo preciso di queste condizioni per ottenere proprietà ottimali del materiale silicio-carbonio.
Misure di sicurezza
Data la pericolosità del gas silano, sono indispensabili misure di sicurezza rigorose durante il processo di deposizione. Queste misure includono l'uso di sistemi avanzati di rilevamento del gas, protocolli di spegnimento di emergenza e solidi sistemi di ventilazione per ridurre il rischio di perdite o esplosioni. Garantire un ambiente di lavoro sicuro non solo protegge il personale, ma assicura anche l'affidabilità e la coerenza del processo di deposizione, che è fondamentale per la produzione su scala industriale.
In sintesi, i parametri del processo di deposizione - temperatura, condizioni di reazione e misure di sicurezza - sono strettamente legati alle prestazioni e alla qualità dei materiali anodici silicio-carbonio. L'ottimizzazione di questi parametri è essenziale per migliorare le proprietà elettrochimiche del materiale e garantirne la fattibilità per applicazioni su larga scala.
Apparecchiature di deposizione
Tipi di apparecchiature di deposizione
I forni rotativi e i letti fluidizzati sono i principali tipi di apparecchiature utilizzate nel processo di deposizione dei materiali anodici al silicio-carbonio. Ogni tipo di apparecchiatura offre vantaggi e sfide distinte, che sono considerazioni cruciali per ottenere proprietà ottimali del materiale e scalabilità.
Forni rotativi
- Semplicità operativa: I forni rotativi hanno un funzionamento relativamente semplice, che li rende una scelta preferenziale per gli esperimenti iniziali e la produzione su piccola scala.
- Efficienza in termini di costi: Sono generalmente più convenienti sia in termini di investimento di capitale che di costi operativi, il che può essere vantaggioso per i progetti su scala pilota.
- Flessibilità: I forni rotativi offrono flessibilità nella gestione di vari materiali precursori e possono essere adattati a diverse condizioni di deposizione.
Letti fluidizzati
- Uniformità ed efficienza: I letti fluidizzati sono noti per la loro superiore uniformità nella distribuzione delle particelle e per i più alti tassi di utilizzo del gas silano. Ciò si traduce in proprietà più uniformi dei materiali e in un miglioramento delle prestazioni complessive.
- Misure di sicurezza migliorate: L'uso dei letti fluidizzati richiede protocolli di sicurezza rigorosi a causa dell'elevata reattività del gas silano. Sistemi di sicurezza avanzati e monitoraggio continuo sono essenziali per ridurre i rischi associati a perdite di gas e altri pericoli.
- Complessità e affidabilità: Nonostante i vantaggi, i letti fluidizzati sono più complessi e richiedono un'elevata affidabilità per garantire un funzionamento continuo e stabile. Questa complessità può porre problemi di scalabilità per la produzione su scala industriale.
In sintesi, mentre i forni rotativi offrono una soluzione più semplice ed economica, i letti fluidizzati offrono una maggiore uniformità ed efficienza, anche se con una maggiore complessità e requisiti di sicurezza. La scelta dell'apparecchiatura dipende dalle esigenze specifiche e dalla scala del processo produttivo.
Le sfide dell'industrializzazione
La produzione su larga scala di materiali anodici al silicio-carbonio utilizzando letti fluidi presenta diverse sfide significative. Queste sfide ruotano principalmente attorno alla garanzia di un funzionamento continuo, al mantenimento dell'uniformità del processo di deposizione e al raggiungimento di un elevato utilizzo del gas silano.
Uno degli ostacoli principali è la necessità diottimizzazione delle apparecchiature e del processo. I letti fluidizzati, pur offrendo un'uniformità e un utilizzo del silano superiori, richiedono un controllo meticoloso di vari parametri come la temperatura, la portata del gas e la distribuzione delle dimensioni delle particelle. Qualsiasi deviazione da queste condizioni ottimali può portare a proprietà incoerenti del materiale, che sono dannose per le prestazioni complessive dell'anodo.
Inoltre, l'affidabilità e la sicurezzaaffidabilità e sicurezza del sistema a letto fluido sono fondamentali. L'uso del gas silano, altamente reattivo e potenzialmente esplosivo, richiede solide misure di sicurezza e un monitoraggio continuo. Ciò aggiunge un ulteriore livello di complessità al processo di industrializzazione, richiedendo sistemi di automazione e controllo avanzati per garantire un funzionamento sicuro ed efficiente.
Inoltre, lascalabilità del processo a letto fluido è un problema significativo. Il passaggio da esperimenti su scala di laboratorio a una produzione industriale su scala reale richiede un'attenta valutazione di come mantenere lo stesso livello di controllo e uniformità su volumi più grandi. Ciò comporta spesso un significativo investimento di capitale per l'aggiornamento delle apparecchiature e il miglioramento del processo.
In sintesi, sebbene i letti fluidizzati offrano vantaggi promettenti per la produzione di anodi di silicio-carbonio, la loro industrializzazione richiede il superamento di importanti sfide tecniche e operative. Tra queste, l'ottimizzazione delle apparecchiature e del processo, la garanzia di affidabilità e sicurezza e la risoluzione dei problemi di scalabilità per ottenere una produzione continua su larga scala.
CONTATTATECI PER UNA CONSULENZA GRATUITA
I prodotti e i servizi di KINTEK LAB SOLUTION sono stati riconosciuti da clienti di tutto il mondo. Il nostro personale sarà lieto di assistervi per qualsiasi richiesta. Contattateci per una consulenza gratuita e parlate con uno specialista del prodotto per trovare la soluzione più adatta alle vostre esigenze applicative!