I forni di ricottura utilizzano principalmente gas inerti come azoto (N2), argon (Ar) ed elio (He) per creare un'atmosfera protettiva che impedisce l'ossidazione, la decarburazione e altre reazioni chimiche indesiderate durante il processo di ricottura. I gas inerti di elevata purezza (purezza > 99,99%) sono essenziali per mantenere l'integrità del materiale trattato. Inoltre, l'idrogeno (H2) è utilizzato in applicazioni specifiche, come i forni a vuoto a idrogeno, grazie alle sue proprietà riducenti. La scelta del gas dipende dal materiale, dai requisiti del processo e dai risultati desiderati, con una pressione tipicamente mantenuta tra 0,05 e 0,07 MPa per ottenere risultati ottimali.
Punti chiave spiegati:
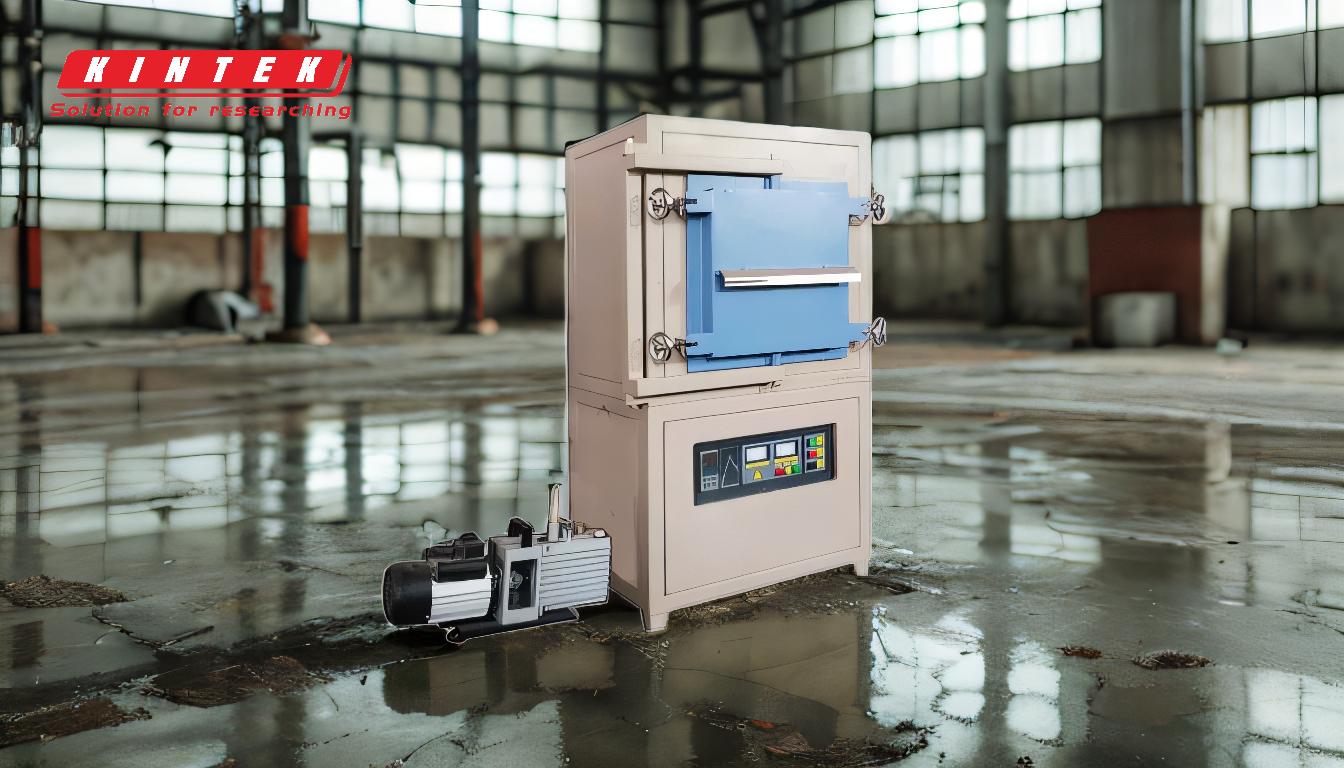
-
Gas primari utilizzati nei forni di ricottura:
- Azoto (N2): Un gas inerte economico e ampiamente utilizzato che impedisce l'ossidazione e la decarburazione. È adatto alla maggior parte dei processi di ricottura, soprattutto per metalli non reattivi come l'acciaio inossidabile.
- Argon (Ar): Un gas inerte più pesante che offre un'eccellente protezione contro l'ossidazione e viene spesso utilizzato per la ricottura di materiali reattivi o di alto valore come il titanio e le leghe speciali.
- Elio (He): Un gas inerte più leggero con un'elevata conducibilità termica, che lo rende adatto ai processi che richiedono un rapido trasferimento di calore. È meno utilizzato a causa del suo costo più elevato.
- Idrogeno (H2): Utilizzato nei forni a vuoto a idrogeno per le sue proprietà riducenti, che aiutano a rimuovere gli ossidi dalle superfici metalliche. È particolarmente utile per la ricottura di materiali come l'acciaio al silicio.
-
Importanza della purezza del gas:
- I gas inerti di elevata purezza (purezza > 99,99%) sono fondamentali nei forni di ricottura per evitare la contaminazione e garantire risultati uniformi. Le impurità presenti nel gas possono causare ossidazione, decarburazione o altri difetti nel materiale trattato.
- Il livello di purezza garantisce che l'atmosfera protettiva rimanga stabile ed efficace durante tutto il processo di ricottura.
-
Requisiti di pressione:
- La pressione del gas inerte nel forno di ricottura è tipicamente mantenuta tra 0,05 e 0,07 MPa. Questo intervallo garantisce un'atmosfera protettiva stabile, riducendo al minimo il rischio di perdite di gas o di consumo eccessivo.
- Un adeguato controllo della pressione è essenziale per ottenere un trattamento termico uniforme ed evitare difetti nel materiale.
-
Ruolo dei gas inerti nella ricottura:
- I gas inerti creano un ambiente non reattivo che impedisce l'ossidazione, la decarburazione e altre reazioni chimiche durante il processo di ricottura.
- Contribuiscono a mantenere la qualità della superficie, le proprietà meccaniche e la stabilità dimensionale del materiale.
-
Applicazioni dei gas specifici:
- Azoto: Comunemente utilizzato per la ricottura di acciaio inossidabile, rame e altri metalli non reattivi.
- Argon: Preferito per la ricottura di metalli reattivi come titanio, zirconio e leghe speciali.
- Idrogeno: Utilizzato nei forni a vuoto a idrogeno per la ricottura di materiali che richiedono la rimozione dell'ossido, come l'acciaio al silicio.
-
Vantaggi dell'utilizzo di gas inerti:
- Precisione: I gas inerti consentono un controllo preciso del processo di ricottura, garantendo risultati costanti.
- Integrità del materiale: Proteggono il materiale da difetti superficiali e ne mantengono le proprietà meccaniche.
- Versatilità: È possibile selezionare diversi gas in base ai requisiti del materiale e del processo.
-
Considerazioni sulla selezione del gas:
- Compatibilità dei materiali: La scelta del gas dipende dal materiale da ricuocere. Ad esempio, l'argon è preferibile per i metalli reattivi, mentre l'azoto è adatto per i metalli non reattivi.
- Costo: L'azoto è più conveniente rispetto all'argon o all'elio, il che lo rende una scelta popolare per le operazioni su larga scala.
- Requisiti di processo: L'idrogeno viene utilizzato quando è necessaria la rimozione degli ossidi, mentre l'elio viene scelto per i processi che richiedono un rapido trasferimento di calore.
Comprendendo questi punti chiave, gli acquirenti di apparecchiature e materiali di consumo possono prendere decisioni informate sul tipo di gas da utilizzare nei forni di ricottura, garantendo risultati ottimali e un buon rapporto costi-benefici.
Tabella riassuntiva:
Gas | Proprietà chiave | Applicazioni |
---|---|---|
Azoto (N2) | Economico, previene l'ossidazione e la decarburazione | Acciaio inox, rame, metalli non reattivi |
Argon (Ar) | Gas inerte pesante, eccellente protezione dall'ossidazione | Titanio, zirconio, leghe speciali |
Elio (He) | Gas inerte leggero, alta conducibilità termica | Processi che richiedono un rapido trasferimento di calore |
Idrogeno (H2) | Proprietà riducenti, rimuove gli ossidi | Acciaio al silicio, forni a vuoto a idrogeno |
Avete bisogno di aiuto per scegliere il gas giusto per il vostro forno di ricottura? Contattate i nostri esperti oggi stesso per una guida personalizzata!