Il processo di deposizione fisica da vapore (PVD) è un metodo sofisticato utilizzato per depositare film sottili di materiale su un substrato.Comporta la trasformazione di un materiale solido in una fase di vapore, che viene poi depositata su un substrato per formare un rivestimento sottile e uniforme.Il processo viene generalmente eseguito in un ambiente sotto vuoto per garantire la purezza e il controllo della deposizione.Il PVD è ampiamente utilizzato in vari settori industriali per applicazioni quali il miglioramento della resistenza all'usura, l'aumento della resistenza alla corrosione e la realizzazione di finiture decorative.Il processo prevede diverse fasi chiave, tra cui la vaporizzazione del materiale di rivestimento, la migrazione delle particelle vaporizzate e la deposizione sul substrato.
Spiegazione dei punti chiave:
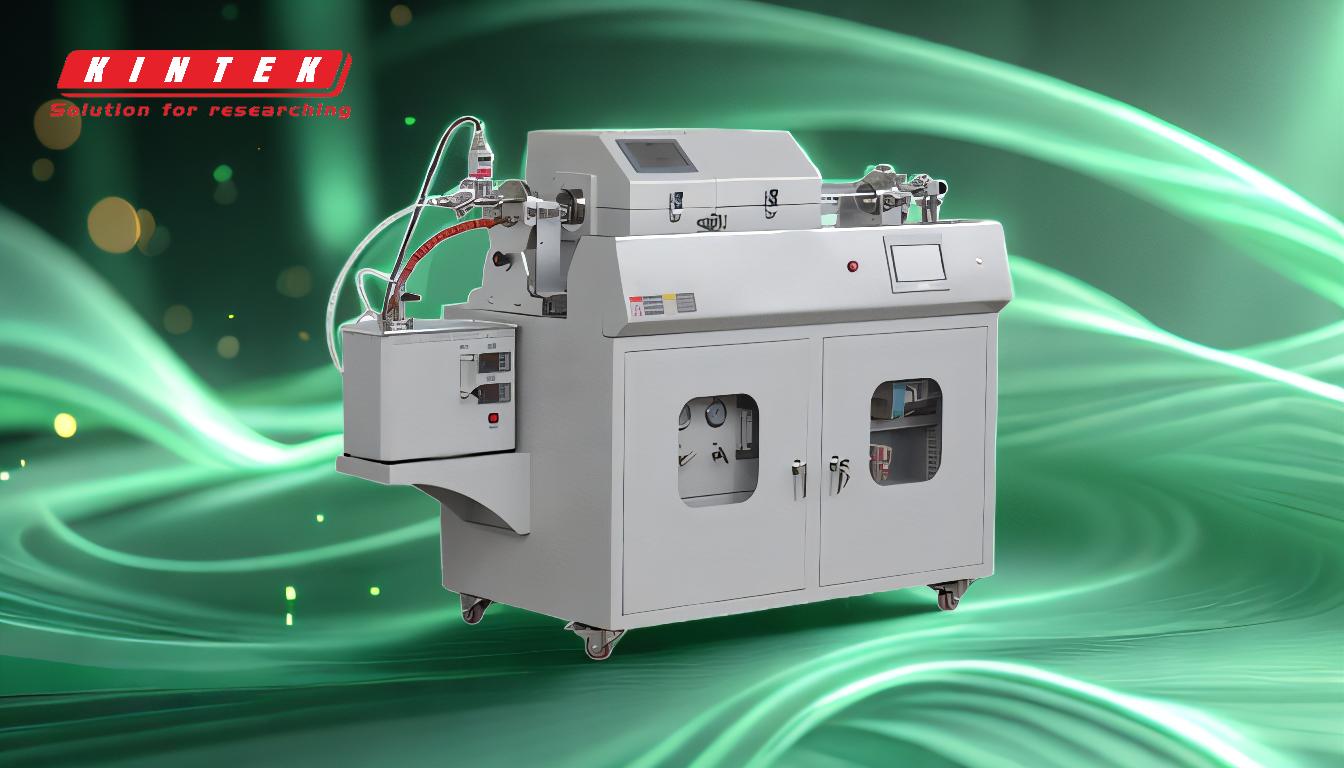
-
Vaporizzazione del materiale di rivestimento:
- La prima fase del processo PVD consiste nella vaporizzazione del materiale di rivestimento.Questa può essere ottenuta con diversi metodi, tra cui l'evaporazione, lo sputtering o l'ablazione laser.
- Evaporazione:Il materiale viene riscaldato ad alta temperatura fino alla vaporizzazione.Spesso si utilizza un fascio di elettroni o un riscaldamento resistivo.
- Sputtering:Gli ioni ad alta energia vengono utilizzati per bombardare il materiale bersaglio, provocando l'espulsione degli atomi dalla superficie e l'ingresso nella fase di vapore.
- Ablazione laser:Un laser ad alta potenza viene utilizzato per vaporizzare direttamente il materiale.
-
Migrazione delle particelle vaporizzate:
- Una volta che il materiale è in fase di vapore, le particelle (atomi, molecole o ioni) migrano attraverso la camera a vuoto.Questa migrazione è influenzata dall'ambiente del vuoto, che riduce al minimo le collisioni con altre particelle e garantisce una deposizione pulita.
- Durante questa fase, le particelle vaporizzate possono subire reazioni, soprattutto se nella camera vengono introdotti gas reattivi (come azoto o ossigeno).Queste reazioni possono formare composti che vengono poi depositati sul substrato.
-
Deposizione sul substrato:
- La fase finale consiste nella deposizione del materiale vaporizzato sul substrato.Questo avviene quando le particelle vaporizzate si condensano sulla superficie più fredda del substrato, formando un film sottile e uniforme.
- Il substrato è in genere mantenuto a una temperatura inferiore rispetto al materiale vaporizzato, il che favorisce la condensazione e l'adesione del rivestimento.
- Lo spessore del film depositato può essere controllato con precisione grazie a tecniche come il monitoraggio della velocità a cristalli di quarzo, che misura la velocità di deposizione e la regola in base alle esigenze.
-
Uso del plasma e dei gas reattivi:
- In molti processi PVD, il plasma viene utilizzato per migliorare il processo di vaporizzazione e deposizione.Il plasma viene creato ionizzando un gas, spesso utilizzando una sorgente di plasma ad accoppiamento induttivo (ICP).
- Il plasma ad alta energia può contribuire a dissociare le molecole di gas in specie reattive, che possono poi reagire con il materiale vaporizzato per formare composti.Ciò è particolarmente utile per creare rivestimenti duri e resistenti all'usura come il nitruro di titanio (TiN) o il nitruro di cromo (CrN).
- L'introduzione di gas reattivi (ad esempio, azoto e ossigeno) consente la formazione di rivestimenti composti, che possono avere proprietà superiori rispetto ai rivestimenti metallici puri.
-
Ambiente sotto vuoto:
-
L'intero processo PVD viene eseguito in un ambiente ad alto vuoto.Questo aspetto è fondamentale per diversi motivi:
- Purezza:Il vuoto riduce al minimo la presenza di contaminanti, garantendo una deposizione pulita.
- Controllo:La bassa pressione consente un controllo preciso del processo di deposizione, compresa la velocità e l'uniformità del rivestimento.
- Controllo della reazione:L'ambiente sotto vuoto aiuta a controllare le reazioni tra il materiale vaporizzato e i gas reattivi, garantendo proprietà di rivestimento costanti.
-
L'intero processo PVD viene eseguito in un ambiente ad alto vuoto.Questo aspetto è fondamentale per diversi motivi:
-
Applicazioni dei rivestimenti PVD:
-
I rivestimenti PVD sono utilizzati in un'ampia gamma di applicazioni, tra cui:
- Resistenza all'usura:Rivestimenti come TiN e CrN sono utilizzati per migliorare la resistenza all'usura di utensili da taglio, stampi e altri componenti.
- Resistenza alla corrosione:I rivestimenti PVD possono costituire una barriera contro la corrosione, prolungando la vita dei componenti esposti ad ambienti difficili.
- Finiture decorative:Il PVD è utilizzato per creare rivestimenti decorativi con un'ampia gamma di colori e finiture, spesso presenti nell'elettronica di consumo e nella gioielleria.
- Rivestimenti ottici:Il processo PVD è utilizzato per depositare film sottili con proprietà ottiche specifiche, come i rivestimenti antiriflesso delle lenti.
-
I rivestimenti PVD sono utilizzati in un'ampia gamma di applicazioni, tra cui:
In sintesi, il processo PVD è un metodo altamente controllato e versatile per depositare film sottili di materiale su un substrato.Comporta la vaporizzazione del materiale di rivestimento, la migrazione delle particelle vaporizzate e la deposizione sul substrato, il tutto in un ambiente sotto vuoto.L'uso di plasma e gas reattivi consente di creare rivestimenti composti con proprietà migliorate, rendendo la PVD una tecnica preziosa in diverse applicazioni industriali.
Tabella riassuntiva:
Passi chiave | Descrizione |
---|---|
Vaporizzazione | Il materiale di rivestimento viene vaporizzato tramite evaporazione, sputtering o ablazione laser. |
Migrazione | Le particelle vaporizzate si muovono nel vuoto, riducendo al minimo le collisioni. |
Deposizione | Le particelle si condensano sul substrato, formando un film sottile e uniforme. |
Plasma e gas reattivi | Migliora le proprietà del rivestimento, ad esempio formando TiN o CrN per la resistenza all'usura. |
Ambiente sotto vuoto | Garantisce purezza, controllo e uniformità di reazione durante la deposizione. |
Applicazioni | Resistenza all'usura, protezione dalla corrosione, finiture decorative e rivestimenti ottici. |
Scoprite come i rivestimenti PVD possono migliorare i vostri prodotti... contattate i nostri esperti oggi stesso !