Il processo di evaporazione nella deposizione fisica da vapore (PVD) è un passaggio fondamentale nella formazione di film sottili sui substrati. Implica la trasformazione di un materiale solido o liquido in una fase vapore, che viene poi trasportata nel substrato dove si condensa formando una pellicola sottile. Questo processo è influenzato da fattori quali materiali target, tecnologia di deposizione, pressione della camera e temperatura del substrato. Comprendere il processo di evaporazione nel PVD è essenziale per ottimizzare la deposizione di film sottili di alta qualità per varie applicazioni.
Punti chiave spiegati:
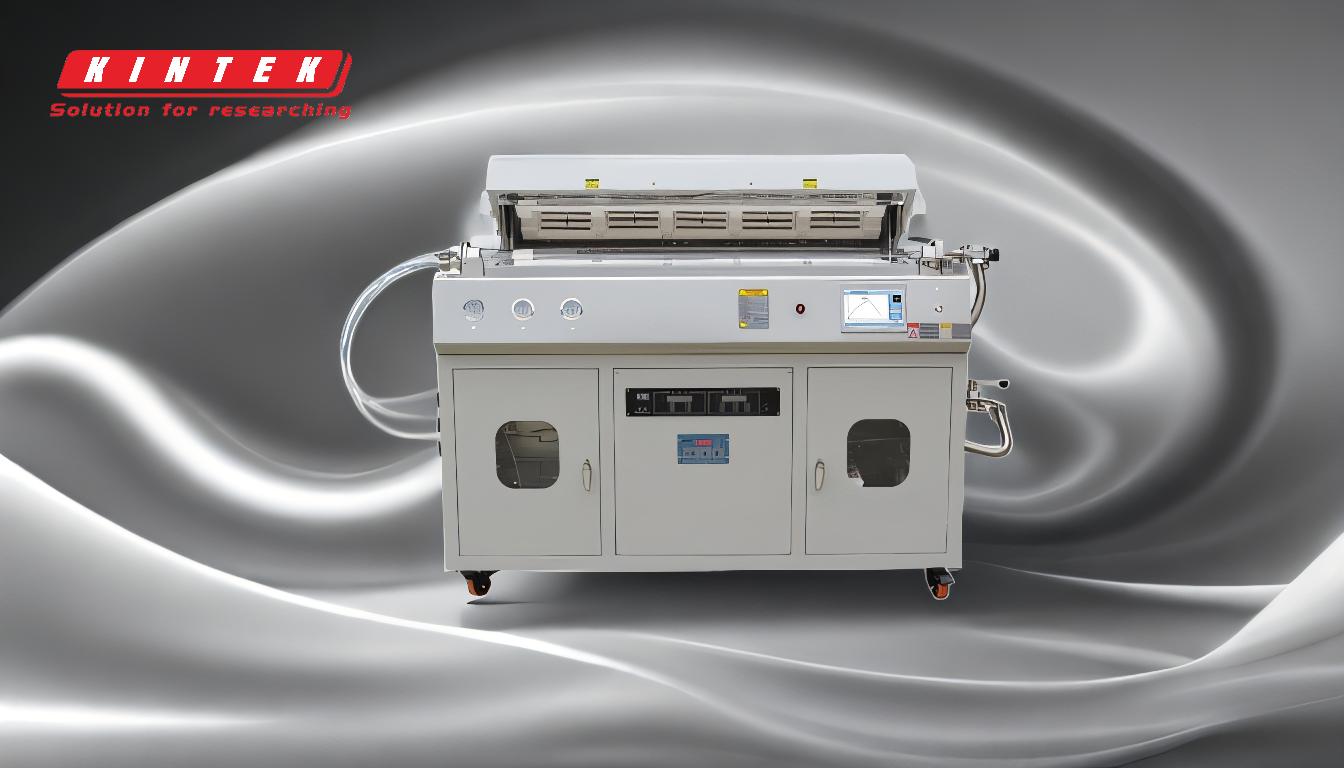
-
Evaporazione del materiale target:
- Il primo passo nel processo PVD è l'evaporazione del materiale target. Ciò può essere ottenuto attraverso vari metodi come l'evaporazione termica, l'evaporazione con fascio di elettroni o lo sputtering. Il materiale target viene riscaldato fino a raggiungere la fase vapore, consentendone il trasporto al substrato.
- Nell'evaporazione termica, il materiale viene riscaldato in una camera a vuoto finché non evapora. L'evaporazione del fascio di elettroni utilizza un fascio di elettroni focalizzato per riscaldare il materiale, mentre lo sputtering comporta il bombardamento del materiale bersaglio con ioni ad alta energia per rimuovere gli atomi, che poi formano un vapore.
-
Trasporto del vapore al substrato:
- Una volta che il materiale target è nella fase vapore, viene trasportato al substrato. Questo trasporto avviene in un ambiente sottovuoto o a bassa pressione per ridurre al minimo le collisioni con altre molecole di gas, garantendo che il vapore raggiunga il substrato con una perdita di energia minima.
- La distanza tra il materiale target e il substrato, nonché la pressione della camera, svolgono un ruolo cruciale nel determinare l'efficienza del trasporto del vapore. Pressioni più basse generalmente determinano percorsi liberi medi più lunghi per le particelle di vapore, consentendo loro di viaggiare più direttamente verso il substrato.
-
Condensazione e formazione di film:
- Una volta raggiunto il substrato, il vapore si condensa formando una pellicola sottile. Il processo di condensazione è influenzato dalla temperatura del supporto, che influisce sull'adesione e sull'uniformità del film. Temperature del substrato più elevate possono migliorare la mobilità degli atomi depositati, portando a una migliore qualità della pellicola.
- La nucleazione e la crescita del film dipendono dall'interazione tra le particelle di vapore e la superficie del substrato. La diffusione superficiale degli atomi depositati nei siti di crescita è essenziale per la formazione di una pellicola continua e uniforme.
-
Ruolo della pressione della camera e della temperatura del substrato:
- La pressione della camera e la temperatura del substrato sono parametri critici nel processo PVD. La pressione della camera influenza il percorso libero medio delle particelle di vapore, mentre la temperatura del substrato influenza la condensazione e la crescita del film.
- La pressione ottimale della camera garantisce un trasporto efficiente del vapore al substrato, mentre la giusta temperatura del substrato favorisce la formazione di pellicole di alta qualità con buona adesione e uniformità.
-
Confronto con la deposizione chimica da fase vapore (CVD):
- Mentre il PVD implica la trasformazione fisica del materiale target in una fase vapore, deposizione chimica di vapore al plasma a microonde (MPCVD) si basa su reazioni chimiche per depositare film sottili. Nel MPCVD, un composto volatile viene vaporizzato e poi decomposto o fatto reagire con altri gas per formare la pellicola desiderata sul substrato.
- Sia il PVD che il CVD hanno i loro vantaggi e vengono scelti in base ai requisiti specifici dell'applicazione, come composizione del film, spessore e velocità di deposizione.
-
Applicazioni e considerazioni:
- Il processo di evaporazione nel PVD è ampiamente utilizzato nella deposizione di film sottili per applicazioni quali semiconduttori, rivestimenti ottici e rivestimenti protettivi. La scelta del materiale target, della tecnologia di deposizione e dei parametri di processo sono personalizzati per soddisfare le esigenze specifiche di ciascuna applicazione.
- Per gli acquirenti di apparecchiature e materiali di consumo, comprendere il processo di evaporazione nel PVD è fondamentale per selezionare i materiali e le tecnologie giuste. Fattori come la purezza del materiale target, l'efficienza del metodo di evaporazione e il controllo sulla pressione della camera e sulla temperatura del substrato sono considerazioni chiave.
In sintesi, il processo di evaporazione nel PVD è un passaggio fondamentale che prevede la trasformazione di un materiale target in una fase vapore, il suo trasporto al substrato e la sua condensazione per formare un film sottile. Il processo è influenzato da vari fattori, tra cui il metodo di evaporazione, la pressione della camera e la temperatura del substrato. Controllando attentamente questi parametri, è possibile depositare film sottili di alta qualità per un'ampia gamma di applicazioni.
Tabella riassuntiva:
Fare un passo | Descrizione |
---|---|
Evaporazione | Il materiale target viene riscaldato fino alla fase vapore utilizzando metodi termici, a fascio di elettroni o sputtering. |
Trasporto | Il vapore viaggia verso il substrato in un ambiente sottovuoto o a bassa pressione. |
Condensazione | Il vapore si condensa sul substrato per formare una pellicola sottile, influenzata dalla temperatura del substrato. |
Fattori chiave | La pressione della camera e la temperatura del substrato sono fondamentali per la qualità e l'uniformità della pellicola. |
Applicazioni | Utilizzato in semiconduttori, rivestimenti ottici e rivestimenti protettivi. |
Ottimizza il tuo processo PVD per film sottili di alta qualità— contatta i nostri esperti oggi stesso !