Gli altiforni e i forni a induzione sono due tipi distinti di forni industriali utilizzati nella produzione di metalli, ciascuno con principi di funzionamento, applicazioni e vantaggi unici.Gli altiforni sono utilizzati principalmente per la produzione di ferro su larga scala e si basano sulla combustione e sulle reazioni chimiche per ridurre il minerale di ferro in ferro fuso.I forni a induzione, invece, utilizzano l'induzione elettromagnetica per fondere i metalli, offrendo un controllo preciso della temperatura, efficienza energetica e idoneità a lotti di dimensioni ridotte.Di seguito vengono spiegate in dettaglio le differenze principali tra questi due tipi di forni, concentrandosi sui principi di funzionamento, le caratteristiche strutturali, le fonti di combustibile, le applicazioni e l'impatto ambientale.
Punti chiave spiegati:
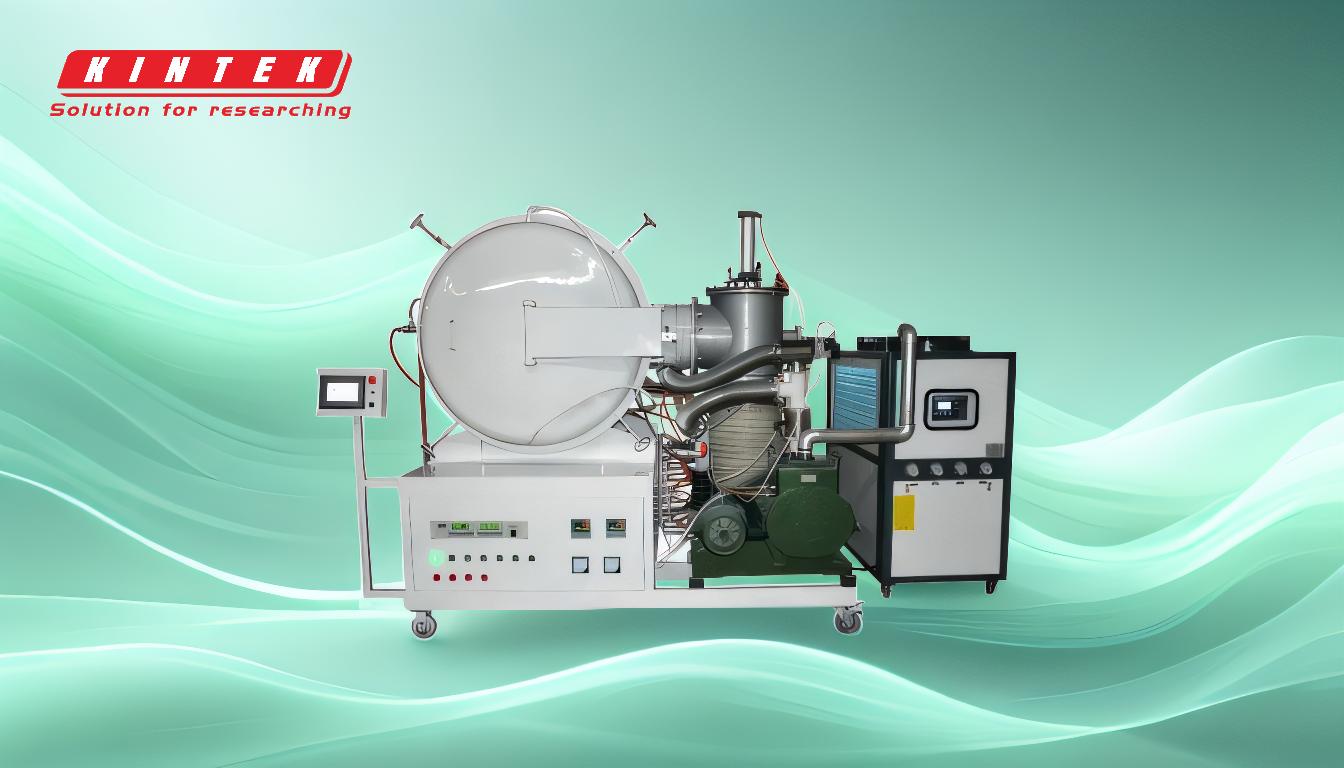
-
Principi di lavoro:
-
Altoforno:
- Funziona attraverso un processo continuo che prevede la riduzione del minerale di ferro utilizzando il coke (un combustibile ricco di carbonio) e il calcare come flusso.
- La combustione del coke genera calore e monossido di carbonio, che reagisce con gli ossidi di ferro per produrre ferro fuso e scorie.
- Il processo dipende fortemente dalle reazioni chimiche e richiede una fornitura costante di materie prime e combustibile.
-
Forno a induzione:
- Utilizza l'induzione elettromagnetica per generare calore all'interno del metallo stesso.
- Una bobina che trasporta corrente alternata crea un campo magnetico, inducendo correnti parassite nel metallo, che lo riscalda e lo fonde.
- Questo metodo garantisce un controllo preciso della temperatura e un riscaldamento uniforme, rendendolo ideale per la fusione e la raffinazione di metalli come acciaio, alluminio e leghe.
-
Altoforno:
-
Caratteristiche strutturali:
-
Altoforno:
- Una grande struttura verticale, in genere alta più di 30 metri, progettata per gestire elevati volumi di materie prime.
- È costituita da un camino, un focolare e da tuyeres per iniettare aria calda nel forno.
- Costruito per resistere a temperature e pressioni estreme, con rivestimenti refrattari per proteggere dall'usura e dalla corrosione.
-
Forno a induzione:
- Compatto e modulare, con un crogiolo o una camera di riscaldamento circondata da bobine a induzione.
- Progettati per lotti di dimensioni ridotte e per un controllo preciso delle condizioni di fusione.
- Spesso sono dotati di sistemi di raffreddamento e isolamento avanzati per mantenere efficienza e sicurezza.
-
Altoforno:
-
Fonti di carburante:
-
Altoforno:
- Si basa sul coke come combustibile primario e agente riducente.
- Richiede un rifornimento continuo di coke, minerale di ferro e calcare, il che lo rende ad alta intensità di risorse.
-
Forno a induzione:
- Alimentato dall'elettricità, elimina la necessità di combustibili.
- Più efficiente dal punto di vista energetico ed ecologico, in quanto produce meno emissioni e può utilizzare fonti di energia rinnovabili.
-
Altoforno:
-
Applicazioni:
-
Altoforno:
- Utilizzato principalmente per la produzione di ferro su larga scala in impianti siderurgici integrati.
- Adatto alla produzione di ghisa, che viene ulteriormente raffinata in acciaio nei forni a ossigeno di base o nei forni elettrici ad arco.
-
Forno a induzione:
- Ideale per la fusione e la raffinazione dei metalli in piccoli lotti, come nelle fonderie e nella produzione di acciai speciali.
- Comunemente utilizzato per la produzione di acciai legati di alta qualità, metalli non ferrosi e fusioni di precisione.
-
Altoforno:
-
Impatto ambientale:
-
Altoforno:
- Genera emissioni significative, tra cui anidride carbonica, ossidi di zolfo e particolato.
- Richiede ampie misure di controllo dell'inquinamento per mitigare l'impatto ambientale.
-
Forno a induzione:
- Produce meno emissioni e ha una minore impronta di carbonio, soprattutto se alimentato da energia rinnovabile.
- Più sostenibile e in linea con le moderne normative ambientali.
-
Altoforno:
-
Costi ed efficienza:
-
Altoforno:
- Costi operativi e di capitale elevati a causa della grande scala e del funzionamento continuo.
- Economico per la produzione di massa, ma meno flessibile per le applicazioni su piccola scala o specializzate.
-
Forno a induzione:
- Investimento iniziale e costi operativi inferiori per lotti di dimensioni ridotte.
- Altamente efficiente e conveniente per la produzione di metalli di alta qualità con scarti minimi.
-
Altoforno:
In sintesi, gli altiforni e i forni a induzione hanno scopi diversi nella produzione di metalli: gli altiforni eccellono nella produzione di ferro su larga scala, mentre i forni a induzione offrono precisione ed efficienza per le operazioni su scala ridotta.La scelta tra i due dipende da fattori quali la scala di produzione, i requisiti dei materiali e le considerazioni ambientali.
Tabella riassuntiva:
Aspetto | Altoforno | Forno a induzione |
---|---|---|
Principio di funzionamento | Utilizza la combustione del coke e le reazioni chimiche per ridurre il minerale di ferro in ferro fuso. | Utilizza l'induzione elettromagnetica per fondere i metalli con un controllo preciso della temperatura. |
Struttura | Grande struttura verticale (alta più di 30 metri) per la produzione di grandi volumi. | Compatto e modulare, progettato per lotti più piccoli. |
Fonte di combustibile | Coke (combustibile ricco di carbonio) e calcare. | Elettricità, che lo rende efficiente dal punto di vista energetico ed ecologico. |
Applicazioni | Produzione di ferro su larga scala nelle acciaierie. | Fusione e raffinazione dei metalli nelle fonderie e nella produzione di acciai speciali. |
Impatto ambientale | Elevate emissioni (CO2, SOx, particolato); richiede un controllo dell'inquinamento. | Emissioni e impronta di carbonio inferiori, soprattutto con le energie rinnovabili. |
Costo ed efficienza | Costi operativi e di capitale elevati; economici per la produzione di massa. | Costi inferiori per piccoli lotti; efficiente e conveniente per metalli di alta qualità. |
Avete bisogno di aiuto per scegliere il forno giusto per la vostra produzione di metalli? Contattate i nostri esperti oggi stesso!