Un forno di tempra è un'apparecchiatura specializzata utilizzata nei processi metallurgici per raffreddare rapidamente un pezzo da una temperatura elevata, in genere per ottenere le proprietà desiderate del materiale come maggiore durezza o resistenza. Questo processo, noto come tempra, è fondamentale nel trattamento termico di metalli come l'acciaio, dove il rapido raffreddamento trasforma la microstruttura in martensite, una fase dura e fragile. I forni di tempra sono spesso abbinati ad altri tipi di forni, come forni discontinui o forni a suola a rulli, e richiedono un controllo preciso della temperatura per garantire un riscaldamento uniforme ed evitare difetti. I forni di tempra avanzati, come i forni di tempra a gas sotto vuoto, funzionano in un ambiente sotto vuoto, utilizzando gas inerti per raffreddare il pezzo, prevenendo l'ossidazione e la contaminazione, rendendoli ideali per parti di alta precisione come leghe e acciaio inossidabile.
Punti chiave spiegati:
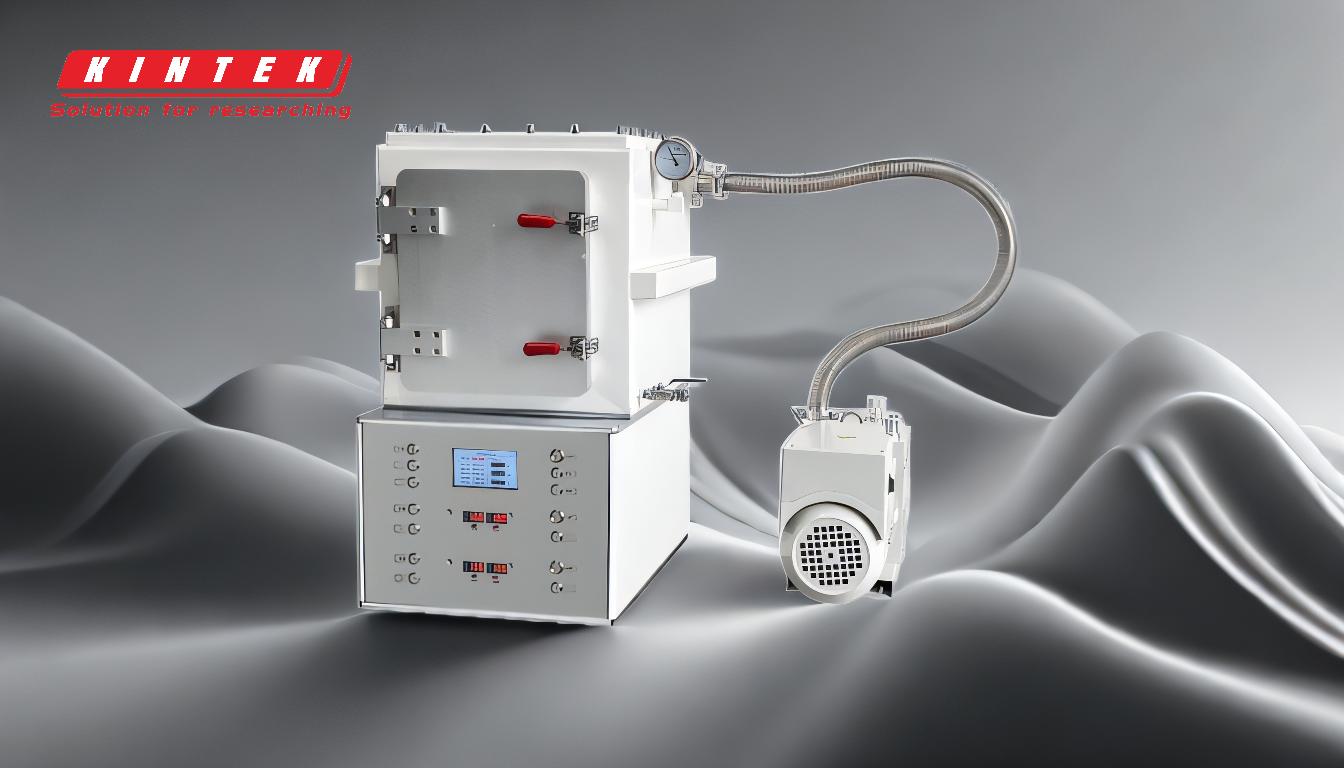
-
Definizione e scopo dei forni di tempra:
- Un forno di tempra è progettato per raffreddare rapidamente i metalli dalle alte temperature per ottenere proprietà specifiche del materiale, come durezza e resistenza.
- Il processo di tempra è fondamentale nei trattamenti termici, in particolare per gli acciai, dove trasforma la microstruttura in martensite.
-
Metodi di raffreddamento nella tempra:
- La tempra tradizionale utilizza mezzi di raffreddamento come acqua o olio per abbassare rapidamente la temperatura del pezzo.
- Metodi di tempra avanzati, come quelli utilizzati in forni di sinterizzazione sotto vuoto , impiegano gas inerti (ad esempio azoto o argon) per raffreddare il pezzo in un ambiente controllato, prevenendo l'ossidazione e la contaminazione.
-
Tipi di forni di tempra:
- Forni batch con tempra: Sono comunemente utilizzati per pezzi di piccole e medie dimensioni, dove il forno viene caricato, riscaldato e quindi raffreddato in una camera separata.
- Forni a suola a rulli e a spinta: Si tratta di forni continui utilizzati per operazioni su larga scala, in cui i pezzi si muovono attraverso il forno e vengono raffreddati alla fine del ciclo di riscaldamento.
- Forni di tempra a gas sotto vuoto: Si tratta di sistemi avanzati che operano in ambiente sotto vuoto, utilizzando gas inerti ad alta pressione per il raffreddamento. Sono ideali per parti di alta precisione come leghe, acciaio inossidabile e titanio.
-
Caratteristiche principali dei forni per tempra a gas sotto vuoto:
- Intervallo di temperatura: In grado di funzionare fino a 2400°F (1315°C), rendendoli adatti per un'ampia gamma di materiali.
- Livelli di vuoto: Raggiungere livelli di vuoto massimi nell'intervallo 10^-6 torr, garantendo un ambiente privo di contaminazioni.
- Design modulare: Dispone di una zona calda modulare per una facile manutenzione e personalizzazione.
- Pressione di spegnimento del gas: Offre pressioni di raffreddamento del gas selezionabili da 2 bar a 10 bar, consentendo un controllo preciso del processo di raffreddamento.
-
Applicazioni dei forni di tempra:
- I forni di tempra vengono utilizzati in vari settori, tra cui quello automobilistico, aerospaziale e della produzione di utensili, per migliorare le proprietà meccaniche dei componenti metallici.
- I forni per tempra a gas sotto vuoto sono particolarmente adatti per parti di alta precisione, come acciai per stampi, acciai rapidi e leghe di titanio, dove l'ossidazione e la contaminazione devono essere ridotte al minimo.
-
Vantaggi della tempra sotto vuoto:
- Prevenzione dell'ossidazione: L'ambiente sottovuoto elimina il rischio di ossidazione, garantendo una finitura superficiale pulita e brillante.
- Raffreddamento uniforme: La tempra con gas inerte fornisce un raffreddamento uniforme, riducendo il rischio di distorsione o fessurazione del pezzo.
- Versatilità: Supporta molteplici processi di trattamento termico, tra cui tempra, ricottura e sinterizzazione, rendendolo uno strumento versatile nelle applicazioni metallurgiche.
-
Processo operativo di tempra:
- Nella tempra tradizionale, il pezzo viene riscaldato nel forno e quindi immerso rapidamente in un mezzo di raffreddamento, come acqua o olio.
- Nella tempra con gas sotto vuoto, il pezzo viene riscaldato sotto vuoto e viene introdotto gas inerte per assorbire il calore e raffreddare rapidamente il pezzo. Il gas viene quindi ricircolato dopo il raffreddamento.
-
Forni di tempra verticali e orizzontali:
- Forni di tempra verticali: Ideali per pezzi grandi e lunghi come alberi o piastre, poiché riducono al minimo la deformazione durante il processo di tempra.
- Forni di tempra orizzontali: Adatto a pezzi più piccoli o più compatti, offre flessibilità nella movimentazione e nella lavorazione.
Comprendendo questi punti chiave, un acquirente può prendere decisioni informate sul tipo di forno di tempra più adatto alle proprie esigenze, garantendo prestazioni e qualità ottimali nei processi di trattamento termico.
Tabella riassuntiva:
Aspetto | Dettagli |
---|---|
Scopo | Raffredda rapidamente i metalli per ottenere durezza, resistenza e formazione di martensite. |
Metodi di raffreddamento | Tradizionale (acqua/olio) o avanzato (gas inerte in ambiente sottovuoto). |
Tipi | Forni batch, a rulli, a spinta e per tempra a gas sotto vuoto. |
Caratteristiche principali | Temperatura fino a 2400°F, livelli di vuoto fino a 10^-6 torr, design modulare. |
Applicazioni | Settore automobilistico, aerospaziale, produzione di utensili e componenti di alta precisione. |
Vantaggi | Previene l'ossidazione, garantisce un raffreddamento uniforme e supporta più processi. |
Processo operativo | Riscaldamento seguito da un rapido raffreddamento in acqua, olio o gas inerte. |
Verticale contro orizzontale | Verticale per pezzi di grandi dimensioni; orizzontale per parti compatte. |
Scopri il forno di tempra perfetto per le tue esigenze— contatta i nostri esperti oggi stesso !