Un forno calcinatore è un tipo specializzato di forno rotante utilizzato principalmente per il processo di calcinazione, che prevede il riscaldamento dei materiali ad alte temperature per indurre la dissociazione chimica o rimuovere l'umidità legata.È ampiamente utilizzato in settori quali la produzione di cemento, la metallurgia e il trattamento chimico.Il forno di calcinazione funziona esponendo i materiali ad alte temperature controllate, assicurando che le reazioni chimiche desiderate avvengano in modo efficiente.Il suo design comprende componenti chiave come il guscio del forno, il rivestimento refrattario, i pneumatici di supporto e l'ingranaggio di trasmissione, che lavorano insieme per facilitare il movimento dei materiali, il trasferimento di calore e la combustione.Le opzioni di personalizzazione consentono al forno di soddisfare requisiti industriali specifici, anche se questo spesso aumenta i costi.
Punti chiave spiegati:
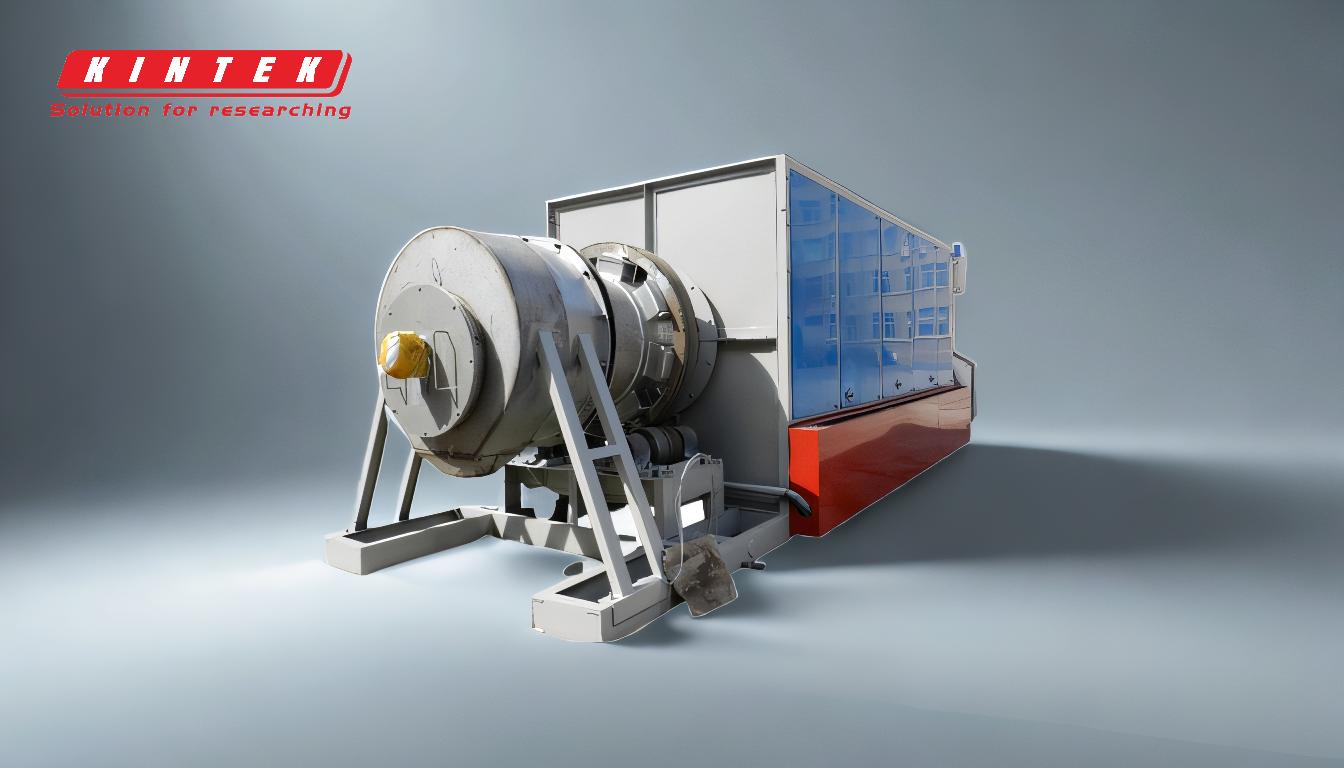
-
Definizione e scopo di un forno calcinatore:
- Un forno di calcinazione è un forno rotante progettato specificamente per la calcinazione, un processo termico che riscalda i materiali ad alte temperature per ottenere la dissociazione chimica o rimuovere l'umidità.
- Le applicazioni più comuni includono la dissociazione del carbonato di calcio (CaCO₃) in ossido di calcio (CaO) e anidride carbonica (CO₂) nella produzione di cemento, nonché la rimozione dell'umidità legata da materiali come il borace.
-
Componenti chiave di un forno di calcinazione:
- Guscio del forno:La struttura esterna che ospita i componenti interni e resiste alle alte temperature.
- Rivestimento refrattario:Un rivestimento resistente al calore all'interno dell'involucro del forno che lo protegge da temperature estreme e reazioni chimiche.
- Pneumatici di supporto (anelli di guida) e rulli:Questi componenti sostengono il peso del forno e ne consentono la rotazione regolare.
- Ingranaggio di trasmissione:Alimenta la rotazione del forno, garantendo un movimento costante del materiale.
- Scambiatori di calore interni:Facilitano un efficiente trasferimento di calore ai materiali in lavorazione.
-
Principio di funzionamento:
- Il forno di calcinazione funziona attraverso una combinazione di flusso di gas, combustione del combustibile, trasferimento di calore e movimento del materiale.
- Il combustibile viene bruciato per generare calore, che viene trasferito al materiale all'interno del forno.
- Mentre il forno ruota, il materiale passa attraverso diverse zone di temperatura, subendo cambiamenti fisici e chimici per formare il prodotto desiderato.
-
Considerazioni sulla personalizzazione e sui costi:
- I forni di calcinazione possono essere personalizzati per soddisfare specifiche esigenze industriali, come la lavorazione di materiali unici o il raggiungimento di particolari profili di temperatura.
- La personalizzazione spesso comporta la modifica di componenti come il mantello del forno, il rivestimento refrattario o gli scambiatori di calore, con conseguente aumento dei costi.
-
Applicazioni nell'industria:
- Produzione di cemento:I forni di calcinazione sono essenziali per la produzione di clinker, un ingrediente chiave del cemento.
- Metallurgia:Utilizzato per arrostire i minerali e rimuovere le impurità.
- Trattamento chimico:Impiegato nella produzione di materiali inorganici e nella rimozione dell'umidità dai composti chimici.
-
Vantaggi dell'utilizzo di un forno calcinatore:
- Trasferimento di calore efficiente:Il design assicura una distribuzione ottimale del calore, riducendo il consumo energetico.
- Versatilità:Può gestire un'ampia gamma di materiali e processi.
- Scalabilità:Adatto sia per l'uso in laboratorio su piccola scala che per la produzione industriale su larga scala.
-
Confronto con altri tipi di forno:
- A differenza dei forni rotativi standard, i forni calcinatori sono specificamente ottimizzati per le reazioni chimiche ad alta temperatura.
- Spesso includono caratteristiche aggiuntive come scambiatori di calore avanzati o rivestimenti refrattari specializzati per migliorare le prestazioni.
Comprendendo il design, i componenti e i principi operativi di un forno di calcinazione, le industrie possono utilizzare efficacemente questa apparecchiatura per ottenere una lavorazione termica precisa e ottimizzare i risultati di produzione.
Tabella riassuntiva:
Aspetto | Dettagli |
---|---|
Definizione | Un forno rotante ottimizzato per la calcinazione, che riscalda i materiali per indurre cambiamenti chimici o rimuovere l'umidità. |
Componenti chiave | Guscio del forno, rivestimento refrattario, pneumatici di supporto, ingranaggi di trasmissione, scambiatori di calore interni. |
Principio di funzionamento | Combina flusso di gas, combustione del combustibile, trasferimento di calore e movimento del materiale per una lavorazione termica precisa. |
Applicazioni | Produzione di cemento, metallurgia, lavorazione chimica. |
Vantaggi | Trasferimento di calore efficiente, versatilità, scalabilità. |
Personalizzazione | Progetti su misura per specifiche esigenze industriali, anche se i costi possono aumentare. |
Scoprite come un forno di calcinazione può ottimizzare i vostri processi industriali. contattate i nostri esperti oggi stesso !