I forni per trattamento termico utilizzano spesso gas inerti per proteggere i materiali dall'ossidazione e da altre reazioni chimiche durante il processo di riscaldamento. I gas inerti più comunemente utilizzati sono l'azoto e l'argon, dove l'azoto è il più diffuso grazie al suo rapporto costo-efficacia e alla sua natura non reattiva con l'acciaio. Anche l'argon è ampiamente utilizzato, soprattutto nei processi che richiedono una maggiore purezza o quando si tratta di metalli non ferrosi. Questi gas aiutano a mantenere l'integrità e le proprietà dei materiali trattati, garantendo risultati di alta qualità. I forni per trattamento termico dotati di atmosfere di gas inerte sono generalmente dotati di controlli avanzati della temperatura e isolamento ad alta efficienza energetica per ottimizzare le prestazioni e il risparmio sui costi.
Punti chiave spiegati:
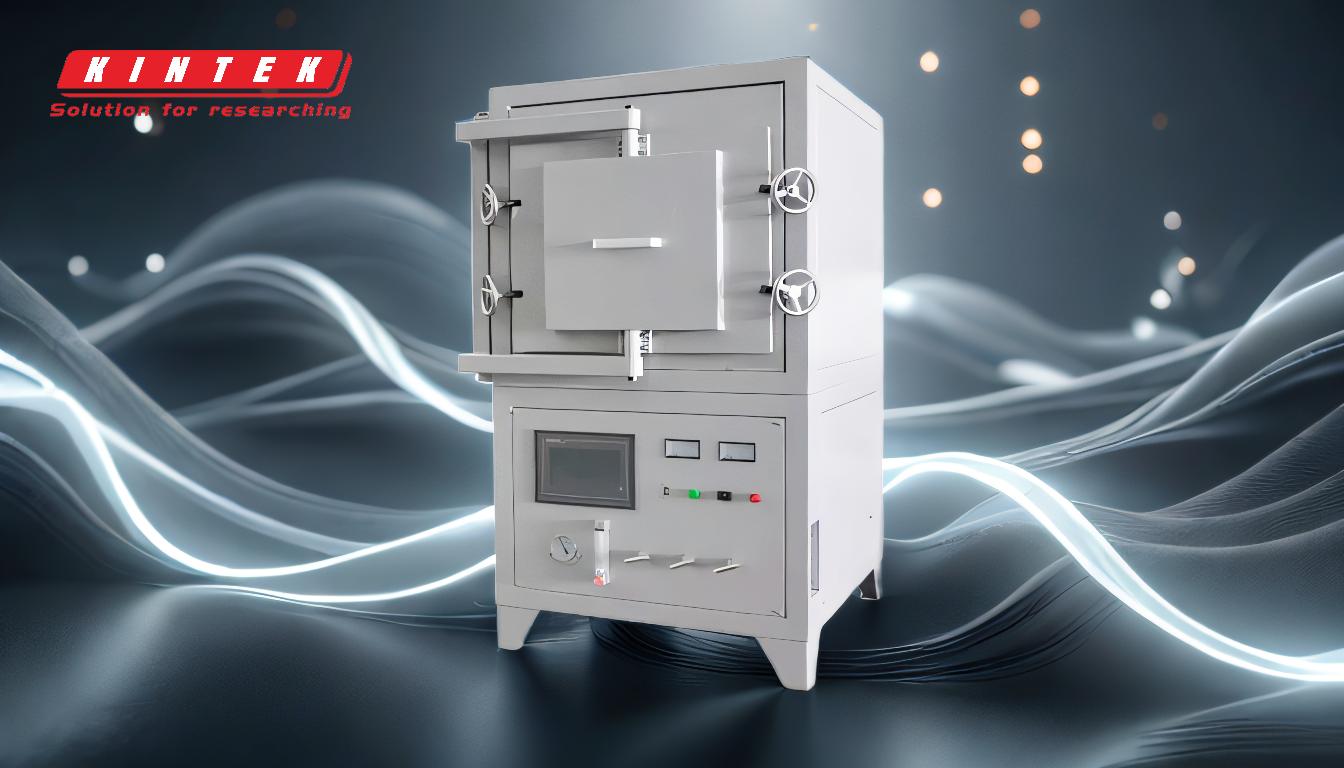
-
Scopo dei gas inerti nel trattamento termico:
- I gas inerti vengono utilizzati per creare un'atmosfera protettiva che previene l'ossidazione e altre reazioni chimiche durante il trattamento termico. Ciò è fondamentale per mantenere l'integrità del materiale e garantire risultati di alta qualità.
- L'ossidazione può degradare la qualità della parte, portando a problemi come la decarburazione, che indebolisce il materiale. I gas inerti mitigano questi rischi.
-
Gas inerti comuni utilizzati:
- Azoto (N2): Il gas inerte più comunemente utilizzato grazie al suo rapporto costo-efficacia e alle proprietà non reattive con l'acciaio. È ampiamente utilizzato in varie applicazioni di trattamento termico.
- Argon (Ar): Spesso utilizzato in processi che richiedono una maggiore purezza o quando si trattano metalli non ferrosi come rame, ottone e alluminio. L'argon è anche preferito in processi specializzati come la pressatura isostatica a caldo (HIP) per garantire che non si verifichino reazioni chimiche.
- Elio (Lui): A volte utilizzato in combinazione con argon o azoto, soprattutto in applicazioni che richiedono un raffreddamento rapido o proprietà termiche specifiche.
-
Applicazioni delle atmosfere di gas inerte:
- Incollaggio e polimerizzazione: I gas inerti vengono utilizzati per creare un ambiente controllato per i processi di incollaggio e polimerizzazione, garantendo risultati costanti.
- Trattamento termico: Essenziale per processi come ricottura, tempra e rinvenimento, dove il mantenimento delle proprietà del materiale è fondamentale.
- Processi specializzati: Come l'HIP, dove l'argon viene utilizzato per prevenire reazioni chimiche e mantenere l'integrità del materiale.
-
Vantaggi dei forni in atmosfera di gas inerte:
- Controllo di precisione: I forni moderni dotati di atmosfere di gas inerte sono spesso dotati di controlli di temperatura di precisione basati su microprocessore, che consentono un trattamento termico accurato e coerente.
- Efficienza energetica: Questi forni sono progettati con isolamento ad alta efficienza energetica, riducendo i costi operativi pur mantenendo prestazioni elevate.
- Prestazioni di qualità: L'uso di gas inerti garantisce che le proprietà del materiale siano preservate, portando a prodotti finali di qualità superiore.
-
Combinazione di gas:
- In alcune applicazioni viene utilizzata una combinazione di gas inerti per ottenere risultati specifici. Le combinazioni comuni includono Ar/He, Ar/He/N2 e N2/He. Queste miscele sono adattate ai requisiti specifici del materiale e del processo di trattamento termico.
-
Considerazioni per la scelta di un gas inerte:
- Tipo materiale: La scelta del gas inerte può dipendere dal tipo di materiale da trattare. Ad esempio, l'argon è spesso preferito per i metalli non ferrosi.
- Requisiti del processo: Processi specifici di trattamento termico possono richiedere gas o miscele di gas particolari per ottenere i risultati desiderati.
- Costo e disponibilità: L'azoto è generalmente più conveniente e ampiamente disponibile, il che lo rende una scelta popolare per molte applicazioni.
In sintesi, l’utilizzo di gas inerti come azoto e argon nei forni per trattamenti termici è fondamentale per proteggere i materiali dall’ossidazione e garantire risultati di alta qualità. La scelta del gas dipende dal materiale, dai requisiti del processo e da considerazioni sui costi, con design di forni avanzati che forniscono controllo preciso ed efficienza energetica.
Tabella riassuntiva:
Gas Inerte | Caratteristiche principali | Applicazioni comuni |
---|---|---|
Azoto (N2) | Economico, non reattivo con l'acciaio | Trattamenti termici generali, lavorazione dell'acciaio |
Argon (Ar) | Elevata purezza, ideale per metalli non ferrosi | Processi HIP, trattamento metalli non ferrosi |
Elio (Lui) | Raffreddamento rapido, proprietà termiche specifiche | Applicazioni specializzate, combinate con Ar/N2 |
Hai bisogno di aiuto per scegliere il gas inerte giusto per il tuo processo di trattamento termico? Contatta i nostri esperti oggi stesso per una consulenza personalizzata!