I forni elettrici ad arco (EAF) sono ampiamente utilizzati nella produzione di metalli grazie alla loro efficienza e flessibilità. Tuttavia, presentano diversi svantaggi che possono influire sull'efficienza operativa, sui costi e sulla qualità del prodotto. Tra questi, l'elevato consumo di energia, che mette a dura prova i sistemi elettrici, e le sfide specifiche legate ai forni ad arco con elettrodi non autoconsumanti, come i rischi di contaminazione, le difficoltà operative e le limitazioni nel controllo della composizione delle leghe. Inoltre, i forni elettrici ad arco sono spesso limitati alla produzione su piccola scala, il che li rende meno convenienti per le operazioni su larga scala, a meno che i costi dell'elettricità non siano eccezionalmente bassi.
Punti chiave spiegati:
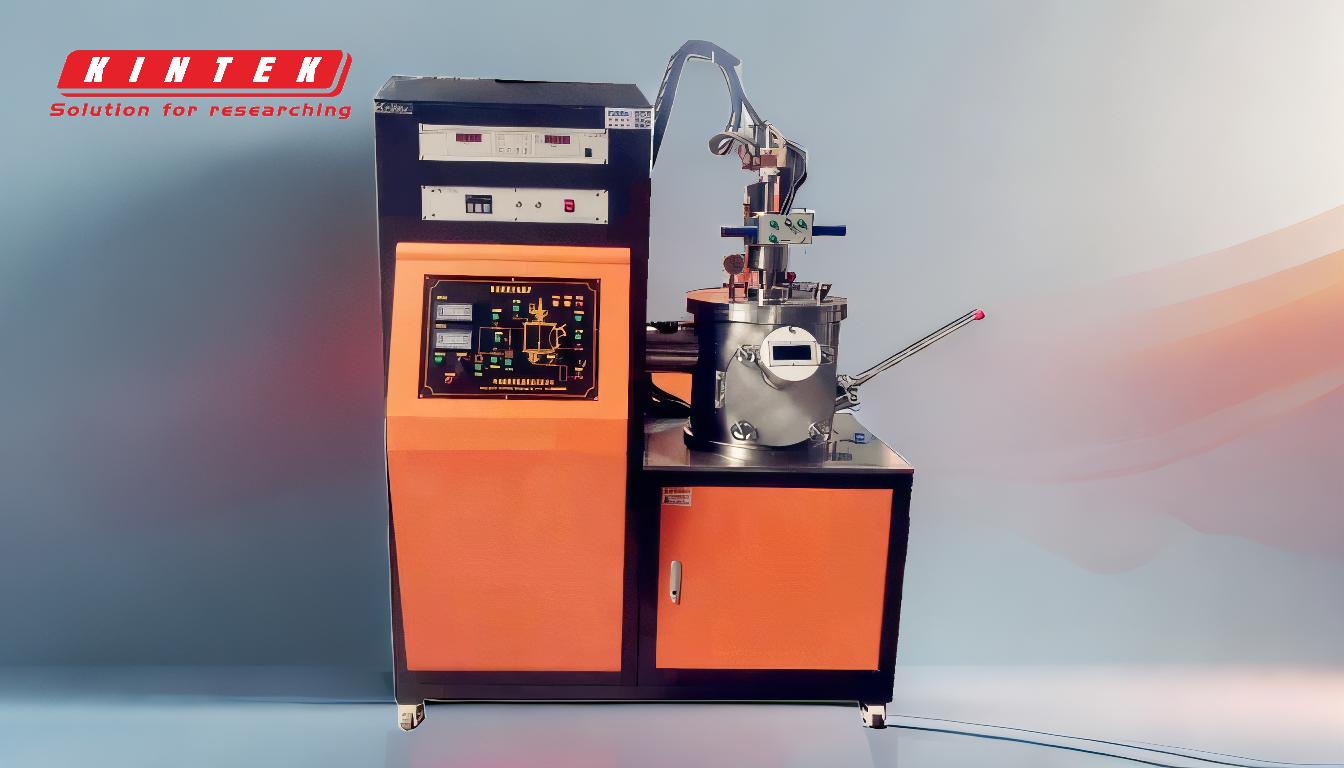
-
Alto consumo di energia
- I forni elettrici ad arco richiedono una quantità significativa di energia elettrica per generare il calore necessario alla fusione dei metalli. Questa elevata richiesta di energia può mettere a dura prova le reti elettriche locali, soprattutto nelle regioni con infrastrutture elettriche limitate.
- La dipendenza dall'elettricità rende i forni ad arco vulnerabili alle fluttuazioni della fornitura di energia elettrica, che possono interrompere la produzione e aumentare i costi operativi.
- Per le industrie che operano in aree con alti costi di elettricità, il consumo energetico dei forni elettrici ad arco può avere un impatto significativo sulla redditività complessiva.
-
Rischi di contaminazione nei forni ad arco a elettrodi non autoconsumanti
- Nei forni ad arco con elettrodi non autoconsumanti, il metallo fuso è a rischio di contaminazione da parte del materiale dell'elettrodo. Sebbene tale contaminazione sia solitamente localizzata e rara, può compromettere la qualità del prodotto finale.
- La contaminazione è particolarmente problematica nei settori che richiedono metalli di elevata purezza, come l'aerospaziale o la produzione di elettronica, dove anche piccole impurità possono portare al fallimento del prodotto.
-
Sfide operative nei forni ad arco con elettrodo non autoconsumante
- I forni ad arco non autoconsumanti sottovuoto soffrono spesso di una scarsa stabilità dell'arco, che ne rende difficile il funzionamento costante. Questa instabilità può portare a un riscaldamento e a una fusione non uniformi, con ripercussioni sulla qualità del metallo prodotto.
- Il processo richiede la formazione di un pool fuso prima del degassamento, che aggiunge complessità e tempo al processo di produzione.
- Queste sfide operative possono aumentare i costi di manodopera e ridurre l'efficienza complessiva.
-
Limiti della scala di produzione
- I forni ad arco con elettrodi non autoconsumanti sono tipicamente limitati alla produzione su piccola scala, con quantità di lega da fondere che vanno da decine a centinaia di grammi. Questo li rende inadatti ad applicazioni industriali su larga scala.
- La piccola capacità produttiva limita anche la loro redditività economica, poiché il costo per unità di metallo prodotto può essere significativamente più alto rispetto alle alternative su larga scala.
-
Difficoltà nel controllo della composizione della lega
- Controllare la proporzione dei componenti delle leghe nei forni ad arco con elettrodi non autoconsumanti è una sfida. Il metodo di caricamento dei materiali può portare a incongruenze nella composizione delle leghe, con conseguenze sulle proprietà del prodotto finale.
- Questa mancanza di precisione è uno svantaggio significativo nei settori in cui le composizioni specifiche delle leghe sono critiche, come nella produzione di leghe ad alte prestazioni per applicazioni specializzate.
-
Problemi di redditività economica
- I forni elettrici ad arco, in particolare quelli che utilizzano torce al plasma o elettrodi non autoconsumanti, sono spesso limitati alla gestione di poche tonnellate di scorie o di metallo alla volta. Questo funzionamento su piccola scala non è economicamente conveniente, a meno che l'energia elettrica non sia eccezionalmente economica.
- Per le operazioni su larga scala, metodi alternativi come gli altiforni o i forni a induzione possono essere più convenienti, soprattutto nelle regioni con alti costi di elettricità.
In sintesi, se da un lato i forni elettrici ad arco offrono diversi vantaggi, tra cui la flessibilità e l'efficienza, dall'altro è necessario considerare attentamente i loro svantaggi, come l'elevato consumo energetico, i rischi di contaminazione, le sfide operative e le limitazioni nella scala di produzione e nel controllo delle leghe. Questi fattori possono influire sia sulla qualità del prodotto finale sia sul rapporto costo-efficacia complessivo dell'uso dei forni elettrici ad arco nelle applicazioni industriali.
Tabella riassuntiva:
Svantaggio | Impatto chiave |
---|---|
Alto consumo di energia | Affatica i sistemi elettrici, aumenta i costi operativi e riduce la redditività. |
Rischi di contaminazione | Compromette la qualità del prodotto, soprattutto nelle industrie dei metalli ad alta purezza. |
Sfide operative | Scarsa stabilità dell'arco, riscaldamento non uniforme e aumento dei costi di manodopera. |
Limiti della scala di produzione | Limitata alla produzione su piccola scala, riduce la redditività economica. |
Difficoltà nel controllo della composizione della lega | Proporzioni di lega incoerenti, che influiscono sulle proprietà del prodotto finale. |
Problemi di redditività economica | Le operazioni su piccola scala sono meno convenienti se l'elettricità non è a buon mercato. |
Avete bisogno di aiuto per scegliere il forno giusto per la vostra produzione di metallo? Contattate i nostri esperti oggi stesso per soluzioni su misura!