La brasatura a induzione, pur essendo efficiente e precisa, presenta diversi svantaggi che possono comprometterne l'idoneità per alcune applicazioni.Tra questi, le sfide legate alle proprietà dei materiali, come la necessità di un controllo preciso della temperatura a causa degli stretti intervalli di fusione dei metalli base e d'apporto, e il potenziale di riduzione della durezza del materiale dopo la brasatura.Inoltre, il processo può essere tecnicamente impegnativo, richiedendo operatori qualificati e attrezzature specializzate, il che può comportare un maggiore consumo energetico e tempi di lavorazione più lunghi.Anche i costi ambientali e di pulizia prima della saldatura si aggiungono alla spesa complessiva.Questi fattori devono essere considerati attentamente quando si sceglie la brasatura a induzione per un progetto.
Punti chiave spiegati:
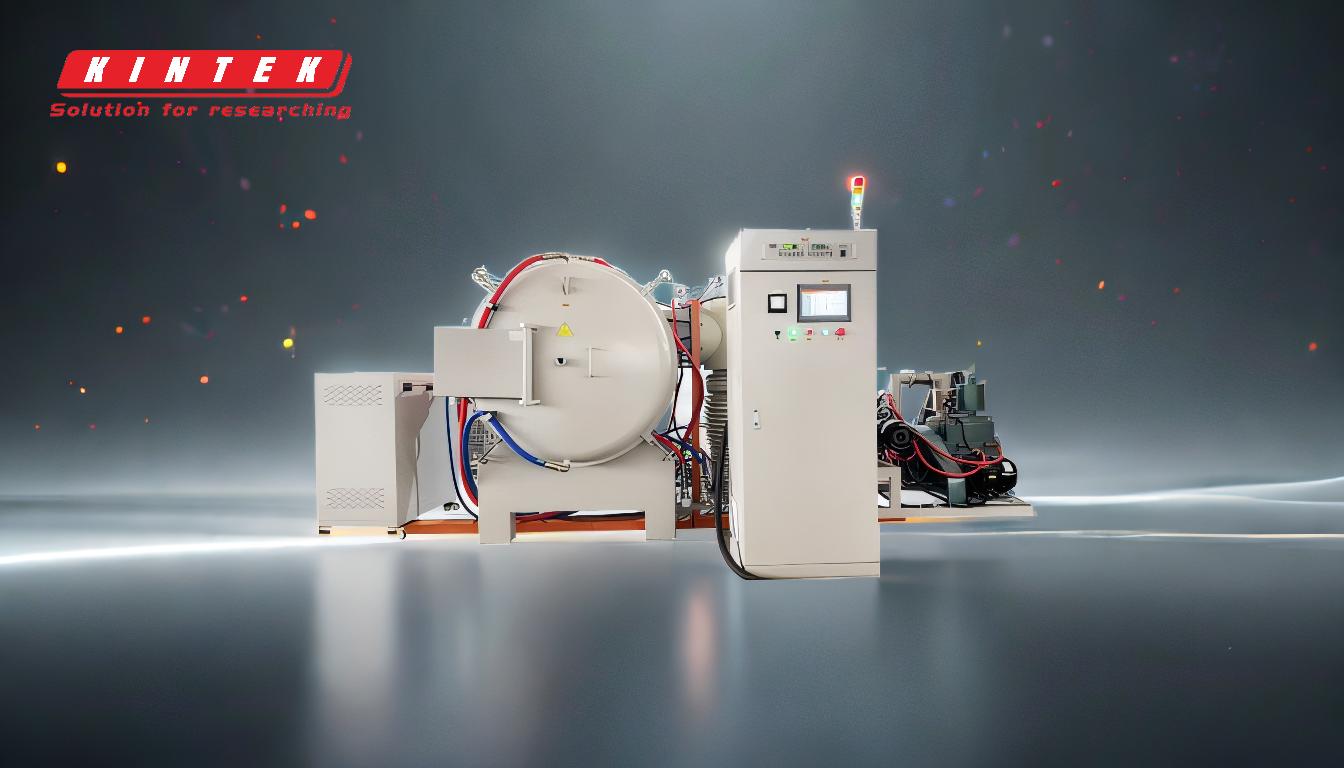
-
Controllo preciso della temperatura e distribuzione termica omogenea:
- La brasatura a induzione richiede un controllo preciso della temperatura perché gli intervalli di fusione del metallo base e del metallo d'apporto sono spesso molto vicini.Questa precisione è fondamentale per evitare surriscaldamenti o surriscaldamenti insufficienti, che possono compromettere la qualità del giunto.Il raggiungimento di una distribuzione termica omogenea è un'altra sfida, soprattutto per le geometrie complesse, poiché un riscaldamento non uniforme può portare a giunti deboli o a danni al materiale.
-
Riduzione della durezza del materiale:
- I processi ad alta temperatura come la brasatura a induzione possono ridurre la durezza di alcuni materiali, in particolare dei metalli sottoposti a ricottura o rammollimento a temperature elevate.Questa riduzione della durezza può influire sulle proprietà meccaniche del prodotto finale, rendendolo meno adatto per le applicazioni che richiedono un'elevata resistenza all'usura.
-
Difficoltà tecniche e manodopera qualificata:
- La brasatura a induzione è un processo tecnicamente impegnativo che richiede operatori qualificati per gestire l'apparecchiatura e garantire la corretta formazione del giunto.La complessità dell'impostazione e della manutenzione delle bobine a induzione, insieme alla necessità di un controllo preciso dei parametri di riscaldamento, lo rende meno accessibile agli utenti inesperti.
-
Elevato consumo di energia:
- Il processo può essere ad alta intensità energetica, soprattutto per operazioni su larga scala o continue.Le bobine a induzione richiedono una notevole potenza elettrica per generare i campi elettromagnetici necessari al riscaldamento, con conseguenti costi operativi più elevati rispetto ad alcuni metodi di brasatura alternativi.
-
Tempi di lavorazione lunghi:
- Sebbene la brasatura a induzione sia generalmente più veloce della brasatura in forno, può comunque comportare tempi di lavorazione più lunghi rispetto ad altri metodi come la brasatura a fiamma.Ciò è particolarmente vero per gli assemblaggi complessi o quando è necessario brasare più giunti in sequenza, il che può rallentare i ritmi di produzione.
-
Elevati costi di pulizia e ambientali:
- Prima della brasatura a induzione, i componenti richiedono spesso una pulizia approfondita per rimuovere ossidi, oli e altri contaminanti che possono interferire con il processo di brasatura.Questo processo di pulizia può essere costoso e richiedere molto tempo.Inoltre, è necessario considerare l'impatto ambientale dell'uso dei flussanti o dei detergenti, che possono richiedere metodi di smaltimento speciali o contribuire all'inquinamento.
-
Vincoli di progettazione:
- La brasatura a induzione richiede accoppiamenti stretti tra i componenti per facilitare l'azione capillare, essenziale per il corretto flusso del metallo d'apporto.Questo requisito può imporre vincoli di progettazione, in quanto i pezzi devono essere prodotti con tolleranze molto strette.Inoltre, la posizione del materiale di brasatura deve essere attentamente pianificata durante la fase di progettazione, aggiungendo complessità al processo.
Comprendendo questi svantaggi, gli acquirenti e gli ingegneri possono decidere con cognizione di causa se la brasatura a induzione è la scelta giusta per la loro specifica applicazione, valutando i pro e i contro rispetto ad altri metodi di brasatura.
Tabella riassuntiva:
Svantaggio | Descrizione |
---|---|
Controllo preciso della temperatura | Richiede un attento monitoraggio per evitare il surriscaldamento o il surriscaldamento. |
Riduzione della durezza dei materiali | Le alte temperature possono ammorbidire i metalli, riducendo la forza e la resistenza all'usura. |
Difficoltà tecniche e manodopera specializzata | Richiede operatori qualificati e attrezzature specializzate. |
Elevato consumo di energia | Processo ad alta intensità energetica, con conseguenti costi operativi più elevati. |
Tempi di lavorazione lunghi | Più lenti rispetto ad alcune alternative, soprattutto per assemblaggi complessi. |
Alti costi di pulizia e ambientali | Richiede una pulizia accurata e può comportare l'uso di flussanti dannosi per l'ambiente. |
Vincoli di progettazione | I pezzi devono avere tolleranze strette, il che aggiunge complessità alla progettazione e alla produzione. |
Avete bisogno di aiuto per decidere se la brasatura a induzione è adatta al vostro progetto? Contattate i nostri esperti oggi stesso per una consulenza personalizzata!