La temperatura di sinterizzazione gioca un ruolo fondamentale nel determinare la durezza di un materiale, poiché influenza direttamente la microstruttura, la densità e la dimensione dei grani del prodotto sinterizzato. Le temperature di sinterizzazione ottimali, come 1500 ℃ per la zirconia, massimizzano la resistenza e la durezza del materiale ottenendo una densificazione completa e una crescita controllata del grano. Deviazioni da questa temperatura, sia troppo alta che troppo bassa, possono portare a difetti come un'eccessiva crescita del grano o una densificazione insufficiente, che degradano la durezza e altre proprietà meccaniche. Comprendere la relazione tra temperatura di sinterizzazione e durezza è essenziale per ottenere le prestazioni desiderate del materiale in ceramica e metalli.
Punti chiave spiegati:
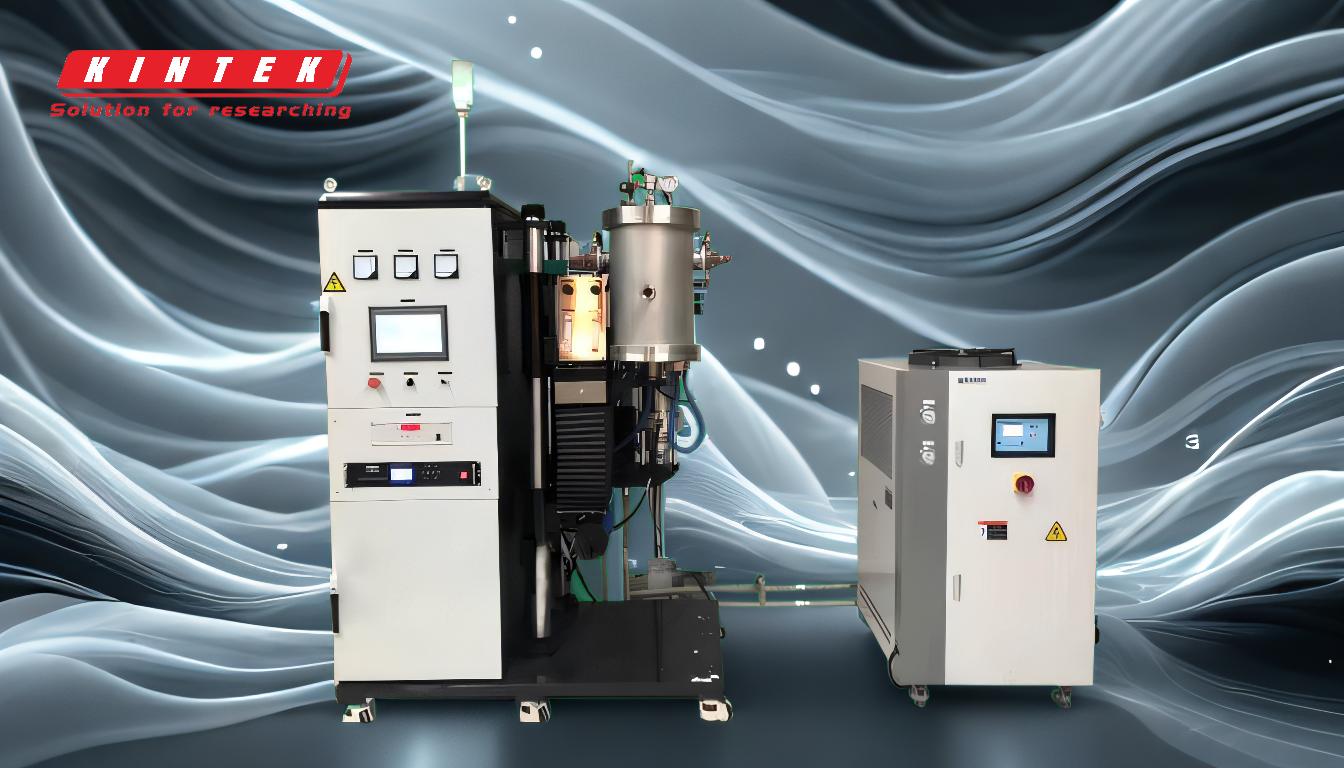
-
Temperatura di sinterizzazione e densità del materiale:
- La sinterizzazione è un processo termico che lega insieme le particelle, riducendo la porosità e aumentando la densità.
- Temperature di sinterizzazione più elevate generalmente favoriscono la densificazione migliorando la diffusione e il legame delle particelle.
- Tuttavia, temperature eccessivamente elevate possono portare a una sinterizzazione eccessiva, causando difetti come una crescita esagerata del grano, che riduce la durezza.
-
Temperatura di sinterizzazione ottimale:
- Per materiali come la zirconia, una temperatura di sinterizzazione ottimale (ad esempio 1500 ℃) massimizza la resistenza e la durezza.
- A questa temperatura, il materiale raggiunge la completa densificazione senza una significativa crescita dei grani, bilanciando densità e microstruttura.
- Deviazioni da questa temperatura, anche di 150 ℃, possono comportare una riduzione della durezza a causa di una densificazione incompleta o di un'eccessiva crescita dei grani.
-
Crescita e durezza del grano:
- La crescita dei grani si verifica quando le temperature di sinterizzazione sono troppo elevate, portando a grani più grandi che indeboliscono il materiale.
- I grani più grandi riducono la durezza perché creano meno bordi di grano, che sono fondamentali per resistere alla deformazione e alla propagazione delle cricche.
- La sinterizzazione controllata previene la crescita eccessiva dei grani, mantenendo una microstruttura a grana fine che migliora la durezza.
-
Porosità e durezza:
- Basse temperature di sinterizzazione o tempi di riscaldamento insufficienti possono lasciare porosità residua nel materiale.
- La porosità agisce come concentratore di stress, riducendo la capacità del materiale di resistere alle forze esterne e abbassando la durezza.
- Le elevate temperature di sinterizzazione, se adeguatamente controllate, riducono al minimo la porosità, portando a una maggiore durezza.
-
Compromessi nei parametri di sinterizzazione:
- Il bilanciamento della temperatura e del tempo di sinterizzazione è fondamentale per ottenere una durezza ottimale.
- Le alte temperature e i lunghi tempi di sinterizzazione possono degradare le proprietà se non gestiti con attenzione, mentre le basse temperature potrebbero non riuscire a raggiungere la completa densificazione.
- L'obiettivo è trovare la giusta combinazione di temperatura e tempo per massimizzare la durezza senza introdurre difetti.
-
Considerazioni specifiche sui materiali:
- Materiali diversi hanno temperature di sinterizzazione ottimali uniche. Ad esempio, la zirconia offre prestazioni migliori a circa 1500 ℃, mentre altre ceramiche o metalli possono richiedere condizioni diverse.
- Comprendere il comportamento di sinterizzazione specifico del materiale è essenziale per personalizzare il processo e ottenere la durezza desiderata.
-
Implicazioni pratiche per gli acquirenti di attrezzature e materiali di consumo:
- Gli acquirenti devono garantire che le apparecchiature di sinterizzazione possano controllare con precisione la temperatura e il tempo per ottenere risultati ottimali.
- I materiali di consumo, come i forni di sinterizzazione, dovrebbero essere selezionati in base alla loro capacità di mantenere temperature costanti e precise.
- Dovrebbero essere implementate misure di controllo della qualità, come il monitoraggio della dimensione dei grani e della porosità, per verificare che il processo di sinterizzazione produca materiali con la durezza desiderata.
Controllando attentamente la temperatura di sinterizzazione e comprendendone gli effetti su microstruttura, densità e dimensione dei grani, i produttori possono ottimizzare la durezza dei materiali sinterizzati, garantendo che soddisfino i requisiti prestazionali per varie applicazioni.
Tabella riassuntiva:
Fattore chiave | Impatto sulla durezza |
---|---|
Temperatura di sinterizzazione ottimale | Massimizza la resistenza e la durezza (ad esempio, 1500 ℃ per la zirconia) bilanciando densità e dimensione dei grani. |
Rischi legati alle alte temperature | Una crescita eccessiva dei grani riduce la durezza indebolendo i bordi dei grani. |
Rischi dovuti alle basse temperature | Una densificazione insufficiente lascia porosità, riducendo la durezza. |
Granulometria | Le microstrutture a grana fine migliorano la durezza resistendo alla deformazione e alla fessurazione. |
Porosità | Ridurre al minimo la porosità attraverso la sinterizzazione controllata migliora la durezza. |
Esigenze specifiche del materiale | Materiali diversi richiedono temperature di sinterizzazione uniche per una durezza ottimale. |
Vuoi ottenere la durezza perfetta per i tuoi materiali? Contatta i nostri esperti oggi stesso per soluzioni di sinterizzazione su misura!