Introduzione: Che cos'è la pressatura isostatica?
La pressatura isostatica (IP)è un processo di produzione utilizzato per migliorare le proprietà meccaniche dei getti. Consiste nell'applicare una pressione uniforme da tutte le direzioni a un materiale utilizzando un mezzo liquido o gassoso. Questo processo contribuisce a ridurre la porosità e a migliorare la forza, la duttilità e la resistenza alla fatica dei getti. L'IP è comunemente utilizzato nell'industria aerospaziale, automobilistica e medica per produrre componenti di alta qualità. Esistono diversi tipi di IP, tra cui la pressatura isostatica a freddo (CIP), la pressatura isostatica a caldo (HIP) e la pressatura isostatica a caldo (WIP). Ogni tipo di IP presenta vantaggi e svantaggi unici, a seconda dell'applicazione.
Indice dei contenuti
Vantaggi della pressatura isostatica per le fusioni
La pressatura isostatica è un metodo collaudato per migliorare le proprietà meccaniche dei getti. In questa sezione, discuteremo alcuni dei vantaggi della pressatura isostatica per i getti.
Migliore densità e uniformità
La pressatura isostatica consiste nel sottoporre una colata a una pressione elevata da tutte le direzioni, che aiuta a eliminare eventuali vuoti interni o porosità nel materiale. Il risultato è una struttura più densa e uniforme, che a sua volta migliora la forza, la tenacità e la resistenza alla fatica della fusione. La densità e l'uniformità migliorate della colata contribuiscono anche a ridurre il rischio di cricche o distorsioni durante la lavorazione o il trattamento termico, che possono essere un problema importante per molti tipi di colata.
Miglioramento della finitura superficiale e della precisione dimensionale
La pressatura isostatica può anche contribuire a migliorare la finitura superficiale e la precisione dimensionale dei getti. La pressione uniforme applicata durante il processo aiuta a eliminare le irregolarità superficiali, con il risultato di una finitura superficiale più liscia e uniforme. Inoltre, l'eliminazione dei vuoti e delle porosità interne contribuisce a migliorare l'accuratezza dimensionale della colata, dando vita a un prodotto finale più preciso.
Maggiore resistenza alla corrosione e all'usura
La pressatura isostatica può anche aumentare la resistenza dei getti alla corrosione e all'usura. L'eliminazione dei vuoti e delle porosità interne contribuisce a creare una struttura più omogenea e meno soggetta a corrosione e usura. Inoltre, la pressatura isostatica può essere utilizzata per migliorare gli elementi di lega all'interno della colata, aumentandone ulteriormente la resistenza alla corrosione e all'usura.
Maggiore resistenza alla fatica
Uno dei vantaggi più significativi della pressatura isostatica per i getti è la maggiore resistenza alla fatica che offre. L'eliminazione dei vuoti e delle porosità interne contribuisce a creare una struttura più uniforme e meno soggetta a rotture per fatica. Ciò può essere particolarmente importante nelle applicazioni in cui la fusione è soggetta a carichi ciclici, come nelle applicazioni aerospaziali o automobilistiche.
Riduzione degli scarti e delle perdite
La pressatura isostatica può anche contribuire a ridurre gli scarti e le perdite durante il processo di produzione. Creando una struttura più uniforme e omogenea, la pressatura isostatica può contribuire a ridurre al minimo i difetti e a migliorare la qualità complessiva della colata. Questo, a sua volta, può contribuire a ridurre la quantità di scarti e perdite durante il processo di produzione, con il risultato di un processo produttivo più efficiente ed economico.
In conclusione, la pressatura isostatica è un metodo molto efficace per migliorare la qualità e le prestazioni dei getti. Il processo offre diversi vantaggi, tra cui una maggiore densità e uniformità, una migliore finitura superficiale e precisione dimensionale, una maggiore resistenza alla corrosione e all'usura, una maggiore resistenza alla fatica e una riduzione degli scarti e delle perdite. Questi vantaggi rendono la pressatura isostatica una scelta popolare per una serie di settori, tra cui quello aerospaziale, automobilistico e dei dispositivi medici.
Tipi di pressatura isostatica
La pressatura isostatica è un metodo efficace per migliorare le proprietà meccaniche dei getti. Esistono due tipi principali di pressatura isostatica: la pressatura isostatica a freddo (CIP) e la pressatura isostatica a caldo (HIP).
Pressatura isostatica a freddo (CIP)
La pressatura isostatica a freddo (CIP) prevede l'applicazione di una pressione a un materiale a temperatura ambiente. In genere viene utilizzata per consolidare le polveri in forme solide. Nel CIP, la miscela di polveri viene compattata e incapsulata utilizzando una pressione isostatica, applicata uniformemente da tutte le direzioni. Questo metodo è particolarmente utile per materiali come ceramica, metalli, plastica e carbonio. Il processo CIP offre diversi vantaggi, tra cui una densità elevata e uniforme, la possibilità di formare forme di prodotto con tolleranze precise e un utilizzo efficiente del materiale.
Pressatura isostatica a caldo (WIP)
La pressatura isostatica a caldo (WIP) è simile alla pressatura isostatica a freddo, ma le forme vengono pressate a una temperatura calda di circa 100°C. Questo metodo è utile per i materiali che richiedono temperature di lavorazione più elevate rispetto a quelle tipicamente utilizzate nel CIP.
Pressatura isostatica a caldo (HIP)
La pressatura isostatica a caldo (HIP) viene eseguita a temperature e pressioni elevate ed è utilizzata per rimuovere porosità e difetti dai getti diffondendo gli atomi di gas dal materiale. L'HIP è particolarmente efficace per migliorare le proprietà delle superleghe utilizzate in applicazioni ad alte prestazioni come i componenti aerospaziali. In questo processo, i pezzi vengono riscaldati in un gas inerte, generalmente argon, che applica una pressione "isostatica" uniforme in tutte le direzioni. In questo modo il materiale diventa "plastico" e i vuoti collassano sotto la pressione differenziale. Le superfici dei vuoti si legano per diffusione, eliminando efficacemente i difetti e raggiungendo una densità vicina a quella teorica, migliorando al contempo le proprietà meccaniche dei pezzi, come ad esempio le fusioni a rivestimento.
In conclusione, la pressatura isostatica è una tecnica preziosa per migliorare la resistenza e la qualità dei getti e trova numerose applicazioni in un'ampia gamma di settori. La pressatura isostatica offre diversi vantaggi, tra cui una densità elevata e uniforme, la capacità di formare forme del prodotto con tolleranze precise e un utilizzo efficiente del materiale. La scelta del tipo di pressatura isostatica da utilizzare dipende dal materiale da lavorare e dal risultato finale desiderato.
Funzionamento della pressa isostatica
La pressatura isostatica è un processo di formatura della metallurgia delle polveri che prevede l'applicazione di una pressione uguale in tutte le direzioni a una polvere compatta. Viene utilizzata per ottenere la massima uniformità di densità e microstruttura senza le limitazioni geometriche della pressatura monoassiale.
Il funzionamento di una pressa isostatica prevede le seguenti fasi:
Fase 1: collocazione del getto in un recipiente ad alta pressione
Il getto viene posto in un recipiente ad alta pressione riempito con un liquido o un gas. Il recipiente è progettato per resistere all'alta pressione ed è sigillato per evitare perdite.
Fase 2: pressurizzazione del recipiente
Il recipiente viene quindi pressurizzato a un livello predeterminato. Ciò comporta l'applicazione di pressione alla colata da tutte le direzioni. La pressione viene mantenuta per un periodo specifico, durante il quale il materiale viene compresso e densificato.
Fase 3: Compressione e densificazione
Durante il processo di pressurizzazione, il materiale viene compresso e densificato. Ciò comporta una significativa riduzione della porosità e un aumento della densità. La pressione uniforme applicata da tutte le direzioni assicura che il materiale abbia le stesse dimensioni in tutte le direzioni.
Fase 4: rimozione della colata
Una volta completato il processo di pressurizzazione, il recipiente viene depressurizzato e la colata viene rimossa. La colata risultante ha proprietà meccaniche migliorate, come una maggiore forza, tenacità e resistenza all'usura e alla fatica.
La pressatura isostatica è particolarmente vantaggiosa per i getti realizzati con materiali difficili da densificare con altri metodi. È utile anche per creare forme e componenti complessi che richiedono alti livelli di accuratezza e precisione.
In conclusione, la pressatura isostatica è un metodo molto efficace per migliorare le proprietà meccaniche dei getti. Il processo consente di ottenere getti più forti, più durevoli e più resistenti all'usura e alla fatica. È una scelta popolare per i produttori che necessitano di componenti di alta qualità per applicazioni impegnative.
Vantaggi della pressatura isostatica
La pressatura isostatica è una tecnica utilizzata per migliorare le proprietà meccaniche dei getti. Questo processo offre diversi vantaggi rispetto ai metodi di fusione tradizionali. In questa sezione analizzeremo in dettaglio i vantaggi della pressatura isostatica.
Migliori proprietà meccaniche
La pressatura isostatica produce getti con proprietà meccaniche migliorate, come una maggiore forza, durezza e resistenza all'usura. Ciò rende la pressatura isostatica una tecnica ideale per la produzione di componenti che richiedono elevata resistenza e durata, come quelli utilizzati nelle applicazioni aerospaziali e automobilistiche.
Densità uniforme
La pressatura isostatica consente di produrre getti con densità uniforme, cosa che non è possibile con i metodi di fusione tradizionali. La pressione applicata in modo uniforme da tutte le direzioni rimuove qualsiasi porosità o vuoto che possa essersi formato durante il processo di fusione. Il risultato è una struttura più densa e uniforme, che a sua volta migliora le proprietà meccaniche del getto.
Produzione di forme complesse
La pressatura isostatica consente di produrre forme complesse con elevata precisione e accuratezza, cosa che non è possibile con i metodi di fusione tradizionali. Questa tecnica può essere utilizzata per produrre forme difficili che non possono essere realizzate con altri metodi. Inoltre, può essere utilizzata per produrre materiali di grandi dimensioni. L'unica limitazione alle dimensioni dei materiali prodotti con questo metodo è la dimensione del recipiente in pressione.
Coerenza e ripetibilità
La pressatura isostatica può essere utilizzata per produrre pezzi con un elevato grado di coerenza e ripetibilità. Ciò la rende una scelta popolare per la produzione di massa. Il processo può essere automatizzato per la produzione di grandi volumi, come nel caso della produzione di isolatori per candele.
Resistenza alla corrosione
La pressatura isostatica migliora la resistenza alla corrosione di un materiale. Pertanto, i materiali sottoposti a questo processo hanno una durata maggiore rispetto alla maggior parte degli altri materiali.
Vantaggi nella metallurgia delle polveri
La pressatura isostatica è utilizzata nella metallurgia delle polveri. Viene utilizzata per la fase di compattazione della metallurgia delle polveri che precede la fase di sinterizzazione. Nella metallurgia delle polveri, la CIP è spesso utilizzata per produrre forme e dimensioni complesse.
Metalli refrattari
La pressatura isostatica viene utilizzata per produrre metalli refrattari. Questi includono tungsteno, molibdeno e tantalio. Il tungsteno, ad esempio, viene utilizzato per produrre fili per filamenti nell'industria delle lampade. In genere, i metalli refrattari hanno un elevato punto di fusione e sono resistenti all'usura.
In conclusione, la pressatura isostatica è una tecnica valida per migliorare le proprietà meccaniche dei getti e offre diversi vantaggi rispetto ai metodi di fusione tradizionali. Questa tecnica può produrre getti con migliori proprietà meccaniche, densità uniforme, forme complesse, consistenza e ripetibilità, resistenza alla corrosione ed è vantaggiosa nella metallurgia delle polveri e nei metalli refrattari.
Pressatura isostatica a caldo per il trattamento di densificazione
La pressatura isostatica a caldo (HIP) è un processo utilizzato per migliorare le proprietà meccaniche dei getti eliminando la porosità e densificando il materiale. Il processo HIP prevede che la colata sia sottoposta a temperatura e pressione elevate in un ambiente con gas inerte, che favorisce la diffusione e il consolidamento del materiale. Il risultato è un materiale più uniforme e omogeneo, con una maggiore forza, resistenza alla fatica e tenacità.
Il processo HIP
Il processo HIP può essere suddiviso in quattro fasi chiave: preparazione della polvere, degasaggio e sigillatura, pressatura isostatica a caldo e post-trattamento.
Preparazione della polvere
La prima fase del processo HIP prevede la preparazione di una colata o di un materiale in polvere. Il materiale è spesso sotto forma di polvere o colata ed è progettato per soddisfare le proprietà specifiche richieste per il prodotto finale.
Degassificazione e sigillatura
Una volta preparato, il materiale viene sottoposto a un processo di degassificazione per rimuovere eventuali gas intrappolati che potrebbero causare porosità. Il materiale in colata o in polvere viene quindi sigillato in un contenitore metallico mediante una chiusura saldata o brasata.
Pressatura isostatica a caldo
Dopo la sigillatura, il materiale viene posto in una pressa isostatica a caldo. La pressa contiene un gas inerte, di solito argon, che viene pressurizzato a 100MPa a 1000°C. Il gas pressurizzato agisce come mezzo di trasferimento della pressione e il materiale in colata o in polvere è sottoposto a una pressione uguale da tutte le direzioni. Ciò favorisce la diffusione e il consolidamento del materiale, ottenendo un materiale più uniforme e omogeneo con proprietà meccaniche migliori.
Post-lavorazione
Al termine del processo HIP, il materiale viene rimosso dalla pressa e sottoposto a una post-lavorazione, che può includere trattamento termico, lavorazione e finitura superficiale. Queste fasi sono essenziali per garantire che il prodotto finale soddisfi le specifiche e le proprietà meccaniche richieste.
Vantaggi del processo HIP
Il processo HIP offre diversi vantaggi rispetto ai processi tradizionali di fusione e metallurgia delle polveri.
Migliori proprietà del materiale
Il processo HIP consente di ottenere un materiale più uniforme e omogeneo con proprietà meccaniche migliorate, tra cui forza, resistenza alla fatica e tenacità.
Componenti di forma quasi netta
Il processo HIP può produrre componenti di forma quasi netta con geometrie complesse, riducendo la necessità di lavorazioni e processi aggiuntivi.
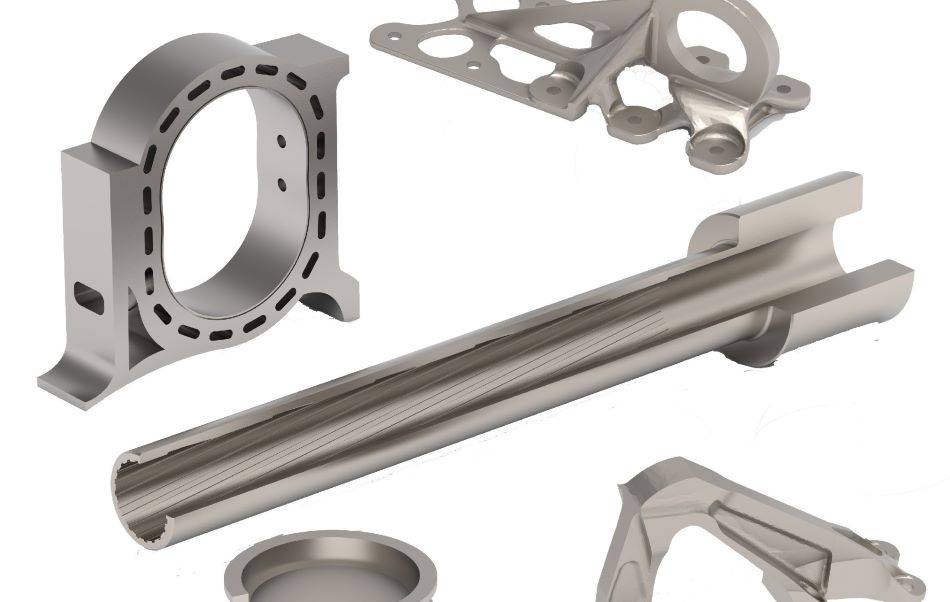
Riparazione dei difetti
Il processo HIP può essere utilizzato per trattamenti successivi alla colata per riparare i difetti e migliorare la finitura superficiale.
Riduzione della porosità
Il processo HIP riduce la porosità, ottenendo un materiale più denso e uniforme con proprietà meccaniche migliori.
In conclusione, la pressatura isostatica a caldo è una tecnologia cruciale per le industrie che richiedono componenti affidabili e ad alte prestazioni, in grado di resistere ad ambienti e carichi estremi. Il processo HIP migliora le proprietà meccaniche dei getti eliminando la porosità e densificando il materiale, ottenendo un materiale più uniforme e omogeneo con una maggiore forza, resistenza alla fatica e tenacità.
Conclusione
In conclusione,la pressatura isostatica è un metodo molto efficace per migliorare le proprietà meccaniche dei getti. Applicando una pressione uniforme in tutte le direzioni, la pressatura isostatica elimina la porosità e migliora la densità, ottenendo getti più resistenti e durevoli. Questa tecnica offre numerosi vantaggi rispetto ai metodi di lavorazione tradizionali, tra cui una maggiore efficienza, precisione e flessibilità. Grazie alla sua capacità di produrre getti di alta qualità con eccellenti proprietà meccaniche, la pressatura isostatica è ampiamente utilizzata in diversi settori, tra cui quello aerospaziale, automobilistico e medico. In generale, la pressatura isostatica è uno strumento prezioso per i produttori che cercano di migliorare la qualità e le prestazioni dei loro getti.
CONTATTATECI PER UNA CONSULENZA GRATUITA
I prodotti e i servizi di KINTEK LAB SOLUTION sono stati riconosciuti da clienti di tutto il mondo. Il nostro personale sarà lieto di assistervi per qualsiasi richiesta. Contattateci per una consulenza gratuita e parlate con uno specialista del prodotto per trovare la soluzione più adatta alle vostre esigenze applicative!