Principi di base del processo di rivestimento PVD
Evaporazione
In un ambiente sotto vuoto, il materiale solido, noto come target, subisce una trasformazione allo stato gassoso attraverso vari metodi, in primo luogo il riscaldamento. Questo processo, noto come evaporazione, è fondamentale per il processo di rivestimento PVD (Physical Vapor Deposition). Per ottenere questa trasformazione vengono impiegate diverse tecniche:
-
Evaporazione termica: Questo metodo prevede il riscaldamento del materiale target fino alla sua temperatura di evaporazione, utilizzando una resistenza elettrica o altri elementi riscaldanti. Una volta raggiunto il punto di vaporizzazione, il materiale si trasforma in un gas che si diffonde e si condensa sul substrato formando un film sottile.
-
Evaporazione a fascio di elettroni: In questo caso, un fascio di elettroni ad alta energia viene diretto verso il materiale target, facendolo evaporare. Questa tecnica è particolarmente utile per i materiali ad alto punto di fusione, poiché l'effetto di riscaldamento localizzato consente un controllo preciso del processo di evaporazione.
-
Evaporazione laser: Utilizzando impulsi laser ad alta energia, questo metodo vaporizza il materiale bersaglio. L'evaporazione laser è vantaggiosa per la preparazione di materiali complessi a film sottile, in quanto offre un'elevata precisione e può essere utilizzata per evaporare materiali difficili da trattare con i metodi tradizionali.
Ciascuno di questi metodi presenta vantaggi unici e viene scelto in base ai requisiti specifici del processo di rivestimento, come il tipo di materiale utilizzato e le proprietà desiderate del film risultante.
Trasporto
Il materiale gassoso, una volta trasformato in stato di vapore, subisce una diffusione all'interno della camera a vuoto. Questa diffusione è una fase critica del processo PVD, in quanto influenza direttamente l'uniformità e la qualità della successiva deposizione del film. Diversi fattori chiave hanno un impatto significativo su questa fase di trasporto:
-
Pressione del gas: La pressione all'interno della camera da vuoto gioca un ruolo fondamentale. Le pressioni più basse di solito migliorano l'efficienza di diffusione, garantendo che il materiale gassoso si diffonda in modo più uniforme sul substrato. Al contrario, pressioni più elevate possono portare a collisioni tra le molecole di gas, riducendo potenzialmente la velocità di diffusione complessiva e compromettendo l'uniformità del film.
-
Temperatura: La temperatura all'interno dell'ambiente del vuoto è un'altra variabile cruciale. Temperature più elevate possono accelerare il processo di diffusione, ma devono essere attentamente controllate per evitare danni termici al substrato o la formazione di depositi non uniformi. L'equilibrio tra la temperatura e gli altri parametri del processo è essenziale per ottenere una diffusione ottimale.
-
Posizione del substrato: Anche la disposizione spaziale del substrato rispetto alla sorgente del materiale gassoso è importante. Un allineamento corretto garantisce che il materiale gassoso raggiunga tutte le aree del substrato in modo uniforme, evitando una sovra-deposizione o una sotto-deposizione localizzata. Tecniche come la rotazione o l'inclinazione del substrato possono contribuire a ottenere una copertura più uniforme.
In sintesi, il trasporto di materiale gassoso nel vuoto è un processo complesso che richiede un controllo meticoloso della pressione del gas, della temperatura e del posizionamento del substrato per garantire il successo della deposizione di un film di alta qualità.
La deposizione
Durante la fase di deposizione, il materiale gassoso trasportato sul substrato inizia a raffreddarsi e a condensare. Questo processo di raffreddamento è fondamentale perché trasforma il gas in un film sottile solido che aderisce alla superficie del substrato. Il processo di deposizione non è solo un cambiamento fisico, ma anche trasformativo, che altera significativamente le proprietà del substrato in base all'applicazione specifica.
Il tipo di gas utilizzato durante la deposizione gioca un ruolo fondamentale nel determinare la struttura e le caratteristiche finali del film. Ad esempio, i gas inerti come l'argon e l'elio sono spesso utilizzati per mantenere la purezza del film, garantendo che non si verifichino reazioni chimiche indesiderate. D'altro canto, gas reattivi come ossigeno, azoto e fluoro vengono introdotti per creare composti specifici come ossidi, nitruri e fluoruri, migliorando la funzionalità del film per particolari applicazioni.
Inoltre, la pressione del gas nella camera di deposizione è un parametro critico che influenza sia la velocità di deposizione che la qualità del film. Pressioni di gas più basse producono in genere film più densi e omogenei, che sono desiderabili per molte applicazioni. Al contrario, pressioni di gas più elevate possono portare a film più ruvidi, che potrebbero essere vantaggiosi in alcuni contesti, come quando è necessaria una maggiore area superficiale per una migliore adesione o reattività.
In sintesi, il processo di deposizione è una sofisticata interazione di raffreddamento, tipo di gas e pressione, ogni fattore controllato meticolosamente per ottenere le proprietà del film desiderate. Questa attenta orchestrazione garantisce che il film sottile risultante soddisfi gli standard esigenti richiesti da vari settori, dall'elettronica all'ottica e oltre.
Principali tipi di processo PVD
Deposizione per evaporazione
La deposizione per evaporazione è una tecnica sofisticata utilizzata per produrre film sottili riscaldando i materiali target fino al loro punto di vaporizzazione. Questo processo è particolarmente efficace per i metalli e alcune leghe, trasformandoli dallo stato solido a quello gassoso attraverso l'energia termica. Gli atomi vaporizzati si condensano quindi sul substrato, formando un film sottile uniforme e conforme. Questo metodo è tipicamente condotto in un ambiente ad alto vuoto per ridurre al minimo le collisioni e la contaminazione, garantendo la purezza e l'integrità del film depositato.
Uno dei vantaggi principali della deposizione per evaporazione è la capacità di creare film di alta qualità con uniformità e conformità eccellenti. Questa tecnica è versatile, in grado di depositare un'ampia gamma di materiali, tra cui metalli, ceramiche e semiconduttori. Tuttavia, il processo richiede un ambiente ad alto vuoto ed è molto sensibile ai fattori ambientali, il che può limitarne l'applicabilità in alcuni scenari.
Deposizione sputtering
La deposizione sputtering è una sofisticata tecnica di deposizione fisica da vapore (PVD) che prevede il bombardamento di un materiale target con particelle ad alta energia, in genere ioni provenienti da un plasma. Questo bombardamento provoca l'espulsione di atomi o molecole dal materiale bersaglio, che poi viaggiano attraverso il vuoto e si condensano su un substrato, formando un film sottile. Il processo è versatile e si applica a un ampio spettro di materiali, tra cui metalli, ossidi e nitruri.
Nella deposizione per sputtering, il materiale di destinazione è esposto a un plasma, spesso composto da ioni di argon ed elettroni. Queste particelle energetiche "staccano" gli atomi dal bersaglio, creando una nube di atomi di origine. Questa nube si condensa poi sul substrato, dove forma un film sottile. La scelta del materiale di destinazione e le condizioni del plasma influenzano in modo significativo le caratteristiche del film depositato.
Un aspetto notevole della deposizione per sputtering è il fenomeno del resputtering, in cui il materiale già depositato può essere riemesso da un successivo bombardamento di ioni o atomi. Questo fenomeno può influenzare l'uniformità e lo spessore del film, richiedendo un attento controllo dei parametri di deposizione per ottenere i risultati desiderati.
La deposizione per sputtering è ampiamente utilizzata in diversi settori industriali grazie alla sua capacità di produrre film densi e di alta qualità con un'eccellente adesione al substrato. È particolarmente apprezzata per la sua applicabilità a un'ampia gamma di materiali, che la rende uno strumento versatile nella fabbricazione di film sottili avanzati per l'elettronica, l'ottica e i componenti meccanici.
Deposizione laser pulsata (PLD)
La deposizione laser pulsata (PLD) è un sofisticato processo di evaporazione che impiega impulsi laser ad alta energia per vaporizzare un materiale target all'interno di una camera a vuoto. Questo metodo è particolarmente adatto alla preparazione di materiali complessi a film sottile, il che lo rende una scelta privilegiata in varie applicazioni scientifiche e industriali.
Il processo PLD inizia con un raggio laser che punta il materiale, provocandone la vaporizzazione e la formazione di un pennacchio di plasma. Questo plasma si deposita poi su un substrato, dove si condensa per formare un film sottile. La complessità di questo processo, che comprende evaporazione, ablazione, formazione di plasma ed esfoliazione, richiede un'attenta ottimizzazione. Nonostante l'aumento del tempo e degli sforzi necessari per gestire le numerose variabili coinvolte, la PLD offre diversi vantaggi.
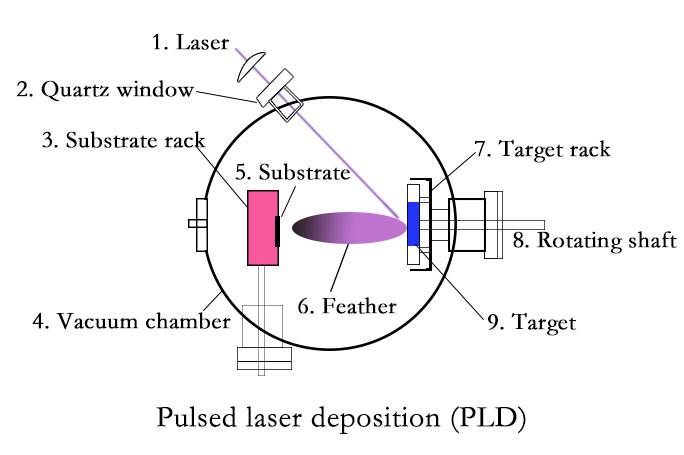
Uno dei vantaggi principali del PLD è l'elevata velocità di deposizione, che semplifica notevolmente il processo rispetto ad altri metodi. Inoltre, il PLD elimina la necessità di filamenti, semplificando la manutenzione e riducendo le potenziali fonti di contaminazione. Ciò rende il PLD particolarmente adatto ad applicazioni che richiedono elevata precisione e purezza, come ad esempio nei settori dell'elettronica e dell'ottica.
In sintesi, sebbene la complessità della PLD richieda un controllo meticoloso, la sua capacità di produrre film sottili complessi e di alta qualità in modo efficiente e con una manutenzione minima la rende uno strumento prezioso nel campo dei processi di rivestimento PVD.
Deposizione chimica da vapore (CVD)
Sebbene la deposizione chimica da vapore (CVD) differisca fondamentalmente dalla deposizione fisica da vapore (PVD), in alcuni casi queste due tecniche vengono combinate per ottenere proprietà superiori dei film. La CVD, un metodo di deposizione sotto vuoto, è rinomata per la produzione di materiali solidi di alta qualità e ad alte prestazioni, in particolare di film sottili utilizzati nell'industria dei semiconduttori. Il processo prevede l'esposizione di un wafer (substrato) a uno o più precursori volatili, che reagiscono e/o si decompongono sulla superficie del substrato per formare il deposito desiderato. Questo metodo è versatile, in grado di depositare materiali in varie forme, tra cui strutture monocristalline, policristalline, amorfe ed epitassiali.
A differenza della PVD, che si basa su processi fisici come l'evaporazione o lo sputtering, la CVD sfrutta le reazioni chimiche per depositare i materiali. Questo approccio chimico consente un maggiore controllo sulla composizione e sulle proprietà del film depositato. Tuttavia, in alcune applicazioni, l'uso complementare di CVD e PVD può produrre film con caratteristiche migliori, come una maggiore adesione, migliori proprietà meccaniche o rivestimenti più uniformi. Ad esempio, gli strati PVD preliminari possono essere utilizzati per creare una superficie più ricettiva per gli strati CVD successivi, ottimizzando così la qualità complessiva del film.
L'integrazione di CVD e PVD è particolarmente vantaggiosa nei processi di microfabbricazione complessi, dove la combinazione di tecniche di deposizione chimica e fisica può affrontare sfide specifiche che nessuno dei due metodi potrebbe gestire da solo. Questo approccio ibrido non solo amplia la gamma di materiali che possono essere depositati, ma migliora anche la funzionalità e le prestazioni del prodotto finale.
Applicazione dei gas nel processo PVD
Gas inerti
I gas inerti, come l'argon (Ar) e l'elio (He), svolgono un ruolo cruciale nei processi di deposizione sputter agendo come gas carrier. Questi gas sono preferiti per la loro capacità di aumentare l'efficienza dello sputtering del materiale target senza causare alcuna reazione chimica. Questa natura non reattiva garantisce il mantenimento della purezza del film depositato, essenziale per ottenere rivestimenti di alta qualità.
L'uso di gas inerti non si limita alla deposizione sputter, ma viene impiegato anche per prevenire reazioni chimiche indesiderate che possono degradare un campione. In genere, queste reazioni indesiderate includono l'ossidazione e l'idrolisi, che sono tipicamente innescate dalla presenza di ossigeno e umidità nell'aria. Sostituendo questi elementi reattivi con gas inerti, si preserva l'integrità del campione.
L'argon, in particolare, è il gas inerte più comunemente utilizzato in varie applicazioni grazie alla sua elevata abbondanza naturale e al suo costo relativamente basso. Rappresenta circa l'1% dell'atmosfera terrestre, il che lo rende facilmente disponibile per l'uso industriale. Mentre l'argon è il più popolare, altri gas nobili come l'elio e il neon possono essere utilizzati a seconda dei requisiti specifici del processo.
Vale la pena notare che il termine "gas inerte" dipende dal contesto. Sebbene i gas nobili siano spesso considerati inerti, possono reagire in determinate condizioni, anche se con una bassa probabilità. Questa caratteristica è in gran parte dovuta ai gusci di valenza completi di questi gas, che li rendono generalmente non reattivi. Tuttavia, questa non è una regola assoluta, poiché anche i gas nobili possono formare composti in condizioni specifiche.
Quando si specifica la purezza dei gas inerti, è comune indicare il livello di contaminazione in parti per milione (ppm). Ad esempio, un livello di contaminazione di 100 ppm significa che su ogni milione di molecole del gas inerte, 100 sono molecole estranee. Questa misura è fondamentale per garantire l'efficacia del gas inerte nel mantenere la purezza del film depositato.
In sintesi, i gas inerti come l'argon e l'elio sono indispensabili nella deposizione sputter e in altri processi in cui è fondamentale mantenere la purezza e l'integrità dei materiali. La loro natura non reattiva e la loro disponibilità li rendono ideali per un'ampia gamma di applicazioni industriali.
Gas reattivi
I gas reattivi svolgono un ruolo fondamentale nella preparazione di vari film sottili nei processi PVD. Questi gas, che includono ossigeno (O₂), azoto (N₂) e fluoro (F₂), sono essenziali per la creazione di film di ossido, nitruro e fluoruro, rispettivamente. L'introduzione di questi gas reattivi è spesso necessaria per ottenere la composizione chimica e le proprietà desiderate nei film depositati.
Ad esempio, nella preparazione di film sottili di ossido di alluminio (Al₂O₃), l'ossigeno viene tipicamente introdotto come gas di reazione. Ciò garantisce che gli atomi di alluminio in fase di vapore reagiscano con l'ossigeno per formare un film di Al₂O₃ stabile e uniforme. L'uso di gas reattivi non si limita all'ossido di alluminio, ma si estende anche ad altri materiali, come il nitruro di silicio (Si₃N₄) e il biossido di titanio (TiO₂), dove vengono impiegati rispettivamente azoto e ossigeno.
La scelta del gas reattivo e la sua concentrazione possono influenzare significativamente le proprietà del film, tra cui la densità, la durezza e la stabilità chimica. Ad esempio, concentrazioni di ossigeno più elevate possono portare a film più porosi e meno densi, mentre concentrazioni più basse possono portare a un'ossidazione incompleta, compromettendo la qualità complessiva del film.
In sintesi, l'uso oculato dei gas reattivi è un aspetto critico dei processi PVD, che consente di creare film sottili ad alte prestazioni con proprietà personalizzate per varie applicazioni.
Gas organici
In alcune applicazioni specializzate, i gas organici come l'etilene e il propilene svolgono un ruolo cruciale nella preparazione di film polimerici e compositi. Questi gas vengono spesso introdotti nel processo PVD per facilitare la formazione di specifiche strutture di film che non sono ottenibili con i soli gas inerti o reattivi.
L'uso di gas organici nei processi PVD è particolarmente vantaggioso per la creazione di film polimerici che richiedono funzionalità chimiche specifiche. Ad esempio, l'etilene può essere utilizzato per formare film di polietilene, noti per le loro eccellenti proprietà meccaniche e la resistenza chimica. Allo stesso modo, il propilene può essere utilizzato per creare film di polipropilene, altamente resistenti al calore e agli agenti chimici.
Inoltre, i gas organici possono essere combinati con altri gas per creare film compositi che presentano una miscela di proprietà derivanti da componenti organici e inorganici. Questo approccio ibrido consente di personalizzare le proprietà delle pellicole, rendendole adatte ad applicazioni specifiche in settori quali l'elettronica, l'ottica e l'ingegneria meccanica.
In sintesi, l'incorporazione di gas organici nei processi PVD apre nuove possibilità per la creazione di film e compositi polimerici avanzati, consentendo lo sviluppo di materiali con proprietà uniche e migliorate.
Regolazione della pressione del gas
La pressione del gas all'interno del processo PVD gioca un ruolo fondamentale nel determinare sia la velocità di deposizione che la qualità del film. Questo parametro influenza direttamente il comportamento del materiale gassoso nel passaggio dal target al substrato.
A pressioni di gas più basse, il materiale gassoso tende a diffondersi in modo più uniforme, migliorando la densificazione e l'omogeneità del film. Questo perché la pressione ridotta riduce al minimo le collisioni tra le molecole di gas, consentendo un processo di deposizione più ordinato. Di conseguenza, il film risultante presenta meno difetti e una struttura più coerente.
Al contrario, pressioni di gas più elevate possono portare a un aumento della rugosità del film. In queste condizioni, il materiale gassoso subisce collisioni più frequenti, che possono interrompere il processo di deposizione ordinato. Il risultato è un film meno uniforme con una rugosità superficiale potenzialmente più elevata. Tuttavia, vale la pena notare che pressioni più elevate possono anche aumentare la velocità di deposizione, anche se a scapito della qualità del film.
Pressione del gas | Qualità del film | Velocità di deposizione |
---|---|---|
Minore | Migliore densificazione e omogeneità | Più lento |
Più alta | Aumento della rugosità | Più veloce |
La pressione ottimale del gas è spesso determinata dai requisiti specifici dell'applicazione, bilanciando la necessità di film di alta qualità con il desiderio di velocità di deposizione efficienti. Questo delicato equilibrio è fondamentale per ottenere le proprietà desiderate nel prodotto finale.
Aree di applicazione del processo di rivestimento PVD
Industria elettronica
Nel settore dei dispositivi a semiconduttore, dei circuiti integrati e dei display, il processo di deposizione fisica da vapore (PVD) svolge un ruolo fondamentale nella produzione di vari film. In particolare, il PVD viene utilizzato per preparare tre tipi principali di film: film conduttivi, film isolanti e film ottici.
Pellicole conduttive
I film conduttivi sono essenziali per garantire il flusso di corrente elettrica all'interno dei dispositivi elettronici. Queste pellicole sono tipicamente realizzate con metalli come alluminio, rame e oro, che vengono depositati con tecniche come l'evaporazione termica o lo sputtering. La scelta del metallo e del metodo di deposizione può avere un impatto significativo sulla conduttività, sull'adesione e sulle prestazioni complessive del film.
Film isolanti
I film isolanti, invece, sono fondamentali per prevenire i cortocircuiti elettrici e proteggere i componenti sensibili. Materiali come il biossido di silicio (SiO₂) e il nitruro di silicio (Si₃N₄) sono comunemente utilizzati per creare questi film. Il processo PVD consente un controllo preciso dello spessore e dell'uniformità del film, fondamentale per mantenere l'integrità e l'affidabilità del dispositivo.
Pellicole ottiche
I film ottici sono progettati per gestire l'interazione della luce con la superficie del dispositivo, migliorando la chiarezza del display e riducendo i riflessi. Questi film includono spesso rivestimenti antiriflesso e strati di miglioramento della trasmittanza. Il processo PVD consente di creare questi film con proprietà ottiche specifiche, come l'indice di rifrazione e la trasmittanza, su misura per soddisfare i requisiti del dispositivo.
In sintesi, il processo PVD è indispensabile nell'industria elettronica, in quanto offre un metodo versatile e preciso per la produzione di film conduttivi, isolanti e ottici fondamentali per i moderni dispositivi elettronici.
Dispositivi ottici
Il processo PVD (Physical Vapor Deposition) svolge un ruolo cruciale nella produzione di rivestimenti ottici, essenziali per migliorare le prestazioni di vari dispositivi ottici. Questi rivestimenti comprendono rivestimenti antiriflesso, pellicole di miglioramento della trasmittanza e strati protettivi, tutti progettati per ottimizzare l'interazione della luce con la superficie del dispositivo.
Tipi di rivestimenti ottici
-
Rivestimenti antiriflesso: Questi rivestimenti sono progettati per ridurre al minimo la riflessione della luce, aumentando così la quantità di luce che passa attraverso la superficie ottica. Questo aspetto è particolarmente importante in applicazioni come le lenti delle macchine fotografiche, gli occhiali e i pannelli solari.
-
Pellicole per il miglioramento della trasmittanza: Queste pellicole sono progettate per aumentare la trasmissione di specifiche lunghezze d'onda della luce, un aspetto cruciale in dispositivi come filtri ottici e sensori.
-
Strati protettivi: Questi rivestimenti proteggono il materiale sottostante da fattori ambientali quali umidità, polvere e danni meccanici, garantendo la longevità e le prestazioni del dispositivo ottico.
Vantaggi del PVD nel rivestimento ottico
- Precisione: Il processo PVD consente un controllo preciso dello spessore del film, fondamentale per ottenere le proprietà ottiche desiderate.
- Durata: I dispositivi ottici rivestiti in PVD hanno una durata superiore rispetto a quelli rivestiti con altri metodi, il che li rende ideali per l'uso a lungo termine in vari ambienti.
- Versatilità: Il processo PVD può essere adattato per creare un'ampia gamma di rivestimenti, in grado di soddisfare le esigenze specifiche di diverse applicazioni ottiche.
Applicazioni nei dispositivi ottici
Tipo di dispositivo | Scopo del rivestimento |
---|---|
Obiettivi per fotocamere | Rivestimenti antiriflesso per migliorare le immagini |
Occhiali da vista | Strati antiriflesso e antigraffio |
Pannelli solari | Rivestimenti antiriflesso per massimizzare la cattura di energia |
Filtri ottici | Miglioramento della trasmittanza per specifiche lunghezze d'onda |
Sensori | Strati protettivi per garantire prestazioni costanti |
Il processo PVD non solo migliora la funzionalità di questi dispositivi, ma ne prolunga anche la durata operativa, rendendolo una tecnologia indispensabile nell'industria ottica.
Componenti meccanici
Nel campo del trattamento delle superfici dei componenti meccanici, i processi di deposizione fisica da vapore (PVD) svolgono un ruolo fondamentale nel migliorare la loro longevità operativa e le loro prestazioni. Le tecniche PVD vengono impiegate meticolosamente per aumentare la resistenza all'usura, alla corrosione e all'ossidazione di questi componenti. Ciò si traduce in un significativo prolungamento della loro vita utile, rendendoli più affidabili e durevoli negli ambienti industriali più esigenti.
L'applicazione del PVD nei componenti meccanici non consiste semplicemente nell'aggiungere uno strato protettivo, ma nell'integrare la scienza dei materiali avanzati per creare superfici in grado di resistere a condizioni estreme. Ad esempio, i componenti dei motori automobilistici, delle turbine aerospaziali e dei macchinari industriali sono spesso sottoposti a condizioni rigorose che possono portare a un rapido degrado. Applicando i rivestimenti PVD, questi componenti vengono rafforzati contro l'usura causata da attrito, reazioni chimiche ed esposizione ad alte temperature.
Inoltre, i rivestimenti PVD possono essere personalizzati per soddisfare i requisiti specifici di diversi componenti meccanici. Che si tratti di un utensile di alta precisione nel settore manifatturiero o di una parte critica in un dispositivo medico, la possibilità di personalizzare il rivestimento garantisce che ogni componente funzioni in modo ottimale nelle sue condizioni specifiche. Questo livello di personalizzazione si ottiene variando i parametri di deposizione, come il tipo di materiale target, la pressione del gas e la temperatura, per mettere a punto le proprietà del film risultante.
In sintesi, l'uso dei processi PVD nel trattamento superficiale dei componenti meccanici è un investimento strategico per migliorarne la durata e le prestazioni, contribuendo in ultima analisi all'efficienza e all'affidabilità di varie applicazioni industriali.
Rivestimenti decorativi
Il processo PVD è fondamentale per la creazione di pellicole decorative che migliorano l'estetica di vari prodotti. Questi film, caratterizzati da lucentezza metallica e colori vivaci, sono ampiamente utilizzati in settori come la gioielleria, gli orologi e gli articoli per la casa. Il processo consente di controllare con precisione lo spessore e l'uniformità del film, garantendo che il prodotto finale soddisfi gli elevati standard di estetica e durata richiesti in questi settori.
Nel campo della gioielleria, i rivestimenti PVD forniscono una finitura sofisticata che può imitare l'aspetto dei metalli preziosi a una frazione del costo. Questo è particolarmente vantaggioso per la produzione di grandi volumi, dove è fondamentale mantenere un aspetto lussuoso. Gli orologi, invece, beneficiano di rivestimenti PVD che non solo ne migliorano l'aspetto estetico, ma offrono anche resistenza ai graffi e alla corrosione, prolungando la durata di questi segnatempo.
Anche i prodotti per la casa, come le stoviglie e gli oggetti decorativi, sfruttano i rivestimenti PVD per ottenere un aspetto moderno ed elegante. La possibilità di incorporare vari colori e motivi nei rivestimenti apre un'ampia gamma di possibilità di design, rendendo il PVD uno strumento versatile nella produzione di beni di consumo.
Inoltre, il processo PVD è ecologico, in quanto opera in condizioni di vuoto, riducendo al minimo gli scarti e l'impatto ambientale associato ai metodi di rivestimento tradizionali. Questo aspetto di sostenibilità rafforza ulteriormente la sua attrattiva nei settori in cui sia l'estetica che la responsabilità ambientale sono di primaria importanza.
Vantaggi e sfide del processo PVD
I vantaggi
I processi di rivestimento PVD offrono numerosi vantaggi che li rendono una scelta privilegiata in diversi settori. Uno dei vantaggi più significativi è la produzione difilm di alta qualità. Questi film presentano un'eccezionaleadesione,uniformitàeintegrità strutturaleche sono fondamentali per migliorare le prestazioni dei materiali rivestiti. Ad esempio, nell'industria elettronica, i film conduttivi rivestiti in PVD assicurano una conduttività elettrica superiore e una perdita di segnale minima, mentre nei dispositivi ottici i rivestimenti forniscono proprietà ottiche precise che migliorano le prestazioni del dispositivo.
Un altro vantaggio notevole è larispetto dell'ambiente dei processi PVD. A differenza di altri metodi di rivestimento, il PVD opera in condizioni di vuoto, riducendo al minimo il rilascio di sostanze nocive nell'ambiente. Ciò rende il PVD un'opzione sostenibile, in particolare nei settori in cui le normative ambientali sono molto severe. Inoltre, l'uso di gas inerti come l'argon e l'elio garantisce il mantenimento della purezza dei film senza introdurre sottoprodotti reattivi che potrebbero danneggiare l'ambiente.
Laversatilità dei processi PVD è un altro punto di forza. La PVD può essere applicata a un'ampia gamma di materiali, tra cui metalli, ceramiche e polimeri, rendendola adatta a diverse applicazioni. Che si tratti di preparare film sottili per i semiconduttori, di migliorare la durata dei componenti meccanici o di creare rivestimenti decorativi per i prodotti di consumo, la PVD offre una soluzione flessibile che può essere personalizzata per soddisfare esigenze specifiche. Ad esempio, l'uso di gas reattivi come l'ossigeno e l'azoto consente di creare film complessi di ossidi e nitruri, ampliando ulteriormente la gamma di applicazioni possibili.
In sintesi, la combinazione di produzione di film di alta qualità, sostenibilità ambientale e ampia applicabilità rende i processi di rivestimento PVD una tecnologia estremamente vantaggiosa in diversi settori.
Le sfide
Una delle sfide principali associate ai processi di deposizione fisica da vapore (PVD) è il costo significativo delle attrezzature.costo delle attrezzature. I sistemi PVD avanzati, come quelli che utilizzano l'evaporazione a fascio di elettroni o la deposizione laser pulsata, richiedono macchinari sofisticati e sistemi di controllo precisi, che possono essere proibitivi per le piccole aziende. Inoltre, la manutenzione e la calibrazione di questi sistemi richiedono competenze specialistiche, che contribuiscono ulteriormente al costo complessivo.
Un'altra sfida critica è rappresentata daii tassi di deposizione. Il raggiungimento di tassi di deposizione ottimali è fondamentale per una produzione efficiente, ma può essere influenzato da una miriade di fattori, tra cui la pressione del gas, la temperatura del substrato e il tipo di materiale target utilizzato. Velocità di deposizione più basse possono portare a tempi di lavorazione più lunghi, aumentando i costi operativi e potenzialmente compromettendo la qualità del film depositato. Al contrario, velocità di deposizione più elevate possono dare origine a film con proprietà non ottimali, come una densità ridotta o una maggiore rugosità.
Il controllo dello spessore del film è un altro ostacolo significativo nei processi PVD. Garantire uno spessore uniforme del film sul substrato è essenziale per le prestazioni e l'affidabilità del prodotto finale. Tuttavia, mantenere un controllo preciso sullo spessore del film può essere impegnativo, soprattutto quando si ha a che fare con geometrie complesse o substrati di grandi dimensioni. Variazioni nello spessore possono portare a incoerenze nelle proprietà del film, come le caratteristiche ottiche, meccaniche o elettriche, che possono essere dannose per l'applicazione prevista.
Per affrontare queste sfide, la ricerca e i progressi tecnologici in corso si concentrano sullo sviluppo di apparecchiature più economiche, sull'ottimizzazione dei parametri di deposizione e sul miglioramento dei meccanismi di controllo dello spessore del film. Questi sforzi mirano a migliorare l'efficienza e l'affidabilità dei processi PVD, rendendoli più accessibili ed efficaci in diversi settori industriali.
CONTATTATECI PER UNA CONSULENZA GRATUITA
I prodotti e i servizi di KINTEK LAB SOLUTION sono stati riconosciuti da clienti di tutto il mondo. Il nostro personale sarà lieto di assistervi per qualsiasi richiesta. Contattateci per una consulenza gratuita e parlate con uno specialista del prodotto per trovare la soluzione più adatta alle vostre esigenze applicative!