La brasatura sottovuoto è un processo specializzato utilizzato per unire i metalli in un ambiente sottovuoto, garantendo giunti puliti e privi di ossidazione.La temperatura della brasatura sottovuoto varia in genere tra i 500°C e i 1200°C, a seconda dei materiali da unire e del metallo d'apporto utilizzato.Il processo prevede l'inserimento di parti assemblate in un forno di brasatura sotto vuoto Il forno è stato costruito con un sistema di aspirazione a vuoto, evacuando la camera per rimuovere i gas residui e riscaldando gradualmente fino a raggiungere la temperatura di brasatura.In questo modo il metallo d'apporto si fonde, scorre e si lega ai metalli di base, creando un giunto forte e duraturo.La temperatura e il profilo di riscaldamento precisi sono fondamentali per ottenere risultati ottimali e i moderni forni a vuoto sono dotati di sistemi di controllo avanzati per garantire uniformità e precisione.
Punti chiave spiegati:
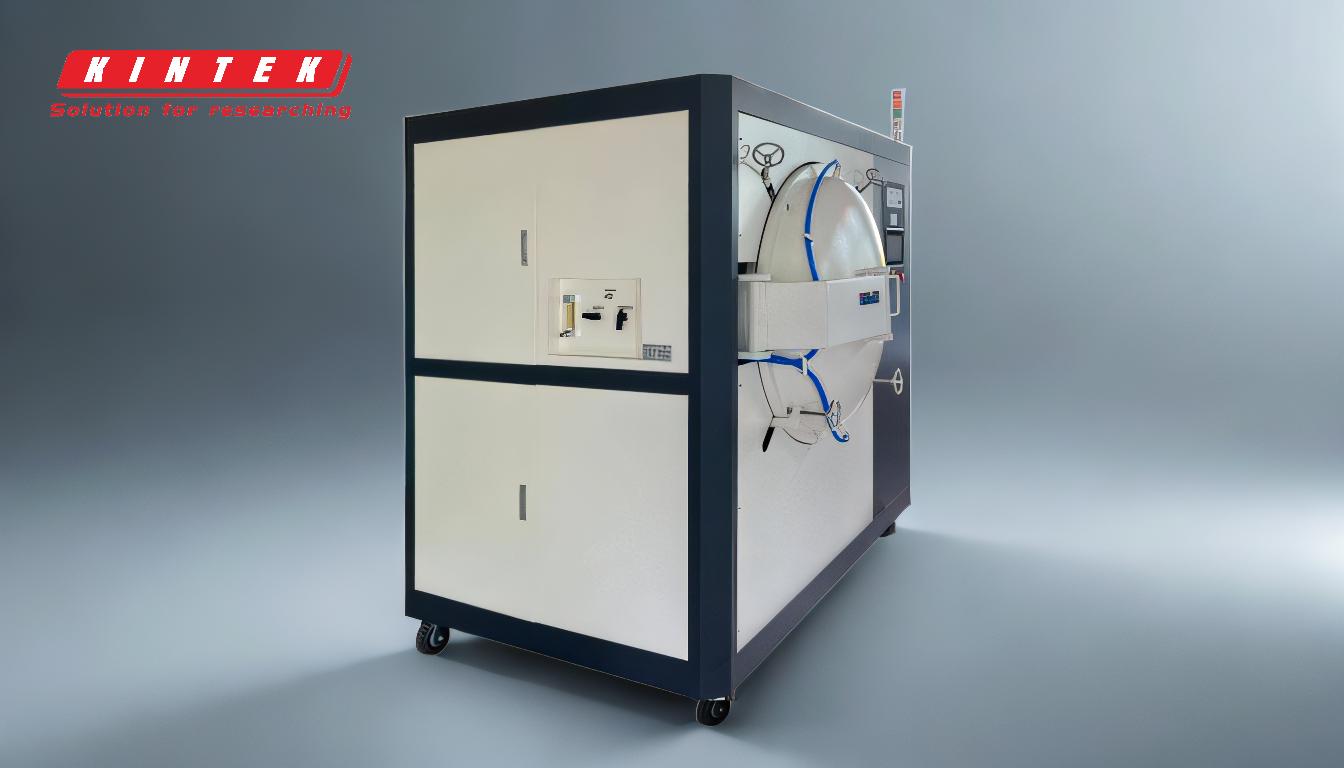
-
Intervallo di temperatura per la brasatura sottovuoto:
- L'intervallo di temperatura tipico per la brasatura sottovuoto è compreso tra 500°C e 1200°C.Questo intervallo viene scelto in base al punto di fusione del metallo d'apporto e alle proprietà termiche dei materiali di base.
- Ad esempio, le leghe di alluminio sono tipicamente brasate a temperature più basse (circa 500°C - 600°C), mentre le leghe a base di nichel possono richiedere temperature fino a 1200°C.
-
Ruolo del forno di brasatura sotto vuoto:
- A forno di brasatura sottovuoto è progettato per creare un ambiente controllato privo di ossigeno e altri gas reattivi.Ciò impedisce l'ossidazione e garantisce giunti puliti e di alta qualità.
- Il forno viene evacuato per rimuovere i gas residui e la temperatura viene gradualmente aumentata fino alla temperatura di brasatura.Questo processo di riscaldamento controllato è essenziale per il corretto scorrimento del metallo d'apporto e l'incollaggio.
-
Processo di riscaldamento e raffreddamento:
- Il processo di riscaldamento in un forno di brasatura sottovuoto è attentamente controllato per garantire una distribuzione uniforme della temperatura.A tal fine si utilizzano zone di riscaldamento multiple e sistemi avanzati di controllo della temperatura, come i controllori PID o i sistemi PLC.
- Dopo la brasatura, il forno viene raffreddato lentamente per evitare stress termici e deformazioni.Alcuni forni offrono anche opzioni di spegnimento a gas per un raffreddamento più rapido, se necessario.
-
Uniformità e controllo della temperatura:
- L'uniformità della temperatura è fondamentale nella brasatura sotto vuoto per garantire una qualità costante dei giunti.Fattori come il design dell'isolamento, la configurazione della zona di riscaldamento e i modelli di flusso del gas influenzano l'uniformità.
- I moderni forni a vuoto sono dotati di termocoppie e regolatori di temperatura per monitorare e regolare accuratamente la temperatura.In genere è necessario un minimo di tre zone di riscaldamento per una corretta regolazione della potenza assorbita.
-
Temperatura massima di funzionamento:
- La temperatura massima di esercizio di un forno di brasatura sottovuoto può variare notevolmente, in genere da 1.500°F (815°C) a 5.400°F (2.982°C).Tuttavia, la maggior parte dei processi di brasatura viene condotta all'estremità inferiore di questo intervallo.
- Ad esempio, un tipico forno per la brasatura sottovuoto può avere una temperatura operativa massima di 1400°C, sufficiente per la maggior parte delle applicazioni di brasatura.
-
Monitoraggio del processo e sicurezza:
- Gli operatori devono monitorare i parametri chiave come la pressione, il flusso e la temperatura dell'acqua durante il processo di riscaldamento per garantire un funzionamento sicuro ed efficiente.
- In caso di interruzione dell'erogazione dell'acqua, è necessario attivare immediatamente un sistema di backup per evitare danni al forno e garantire un raffreddamento continuo.
-
Programma di riscaldamento tipico:
- Un programma standard di brasatura sottovuoto prevede il pompaggio del sistema alla pressione di base, l'aumento della temperatura della zona calda a 800°C e il suo mantenimento per 20 minuti.La temperatura viene poi gradualmente aumentata a 1100°C nell'arco di un'ora e mantenuta per 1,5 ore.
- Questo processo di riscaldamento graduale assicura la corretta fusione e l'incollaggio del metallo d'apporto, riducendo al minimo lo stress termico sui componenti.
-
Applicazioni e specifiche:
- La brasatura sottovuoto è ampiamente utilizzata in settori come quello aerospaziale, automobilistico ed elettronico, dove sono richieste giunzioni ad alta resistenza e prive di ossidazione.
- Un tipico forno per brasatura sottovuoto può avere una zona di lavoro di 1200 x 1200 x 1200 mm, un carico lordo massimo di 1500 kg e la capacità di operare con pressioni parziali di azoto, argon o idrogeno.Queste specifiche lo rendono adatto a un'ampia gamma di applicazioni.
Comprendendo questi punti chiave, gli acquirenti di apparecchiature e materiali di consumo possono prendere decisioni informate quando scelgono un forno di brasatura sottovuoto e ottimizzare il processo di brasatura per le loro esigenze specifiche.
Tabella riassuntiva:
Aspetto chiave | Dettagli |
---|---|
Intervallo di temperatura | Da 500°C a 1200°C, a seconda dei materiali e del metallo d'apporto. |
Processo di riscaldamento | Riscaldamento controllato e graduale in un forno a vuoto per una distribuzione uniforme. |
Processo di raffreddamento | Raffreddamento lento per evitare stress termici; sono disponibili opzioni di spegnimento a gas. |
Temperatura massima di esercizio | Fino a 1400°C per la maggior parte delle applicazioni di brasatura. |
Programma di riscaldamento tipico | Pompare alla pressione di base, riscaldare a 800°C, mantenere, poi aumentare a 1100°C. |
Applicazioni | Aerospaziale, automotive, elettronica per giunti ad alta resistenza e privi di ossidazione. |
Siete pronti a ottimizzare il vostro processo di brasatura sottovuoto? Contattate i nostri esperti oggi stesso per soluzioni su misura!