I forni di calcinazione sono progettati per operare ad alte temperature, che in genere vanno da 800°C a 1300°C, a seconda dell'applicazione specifica.L'intervallo di temperatura è influenzato dai materiali da lavorare, dalle trasformazioni chimiche o fisiche desiderate e dall'efficienza del forno.Fattori come il controllo della temperatura, la calibrazione e la progettazione del forno svolgono un ruolo fondamentale per ottenere risultati coerenti e accurati.Inoltre, la scelta di un forno con una temperatura massima leggermente superiore alla temperatura di utilizzo richiesta garantisce prestazioni ottimali e una lunga durata dell'apparecchiatura.
Punti chiave spiegati:
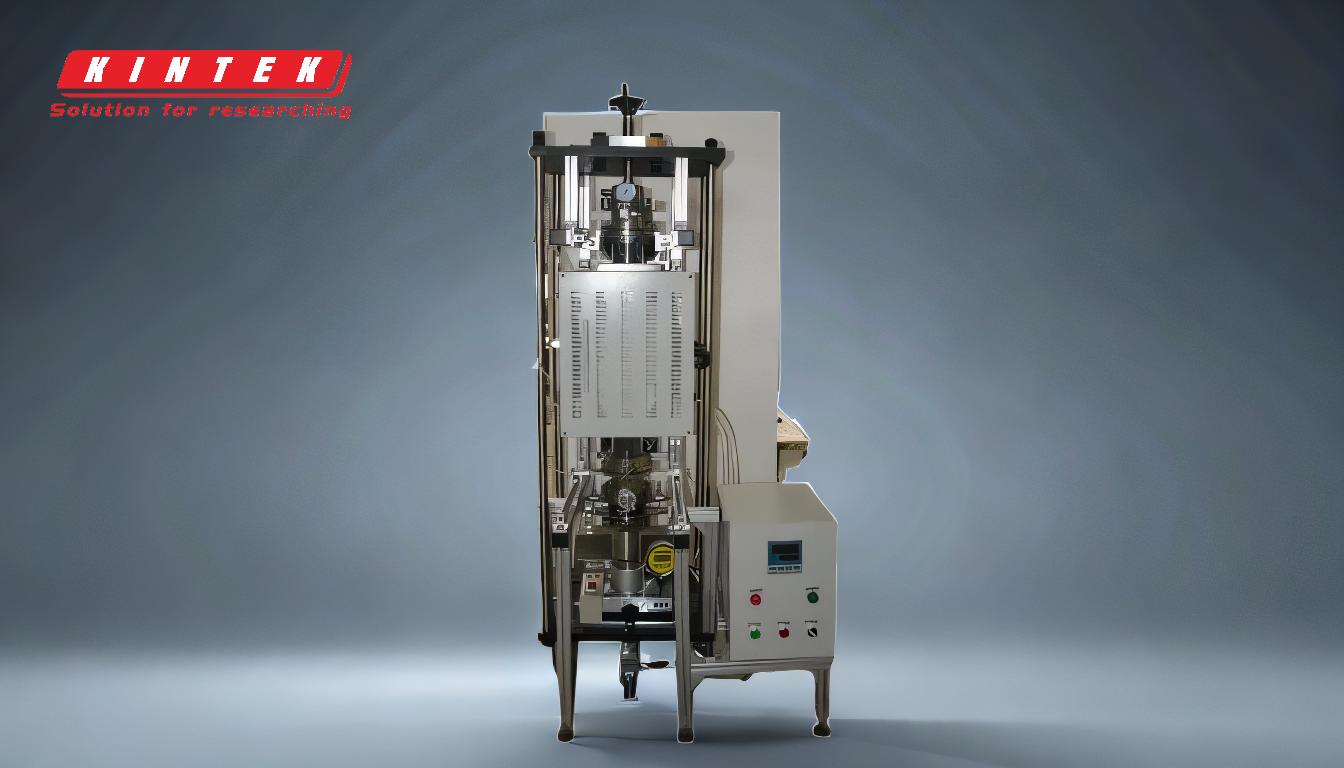
-
Intervallo di temperatura tipico per i forni di calcinazione:
- I forni di calcinazione operano generalmente a temperature comprese tra 800°C e 1300°C .
- Questo intervallo è adatto a processi come la decomposizione termica, la rimozione di componenti volatili o le trasformazioni di fase in materiali come ceramiche, metalli e minerali.
- La temperatura esatta dipende dall'applicazione specifica e dal materiale da trattare.
-
Fattori che influenzano il controllo della temperatura:
-
Il controllo della temperatura nei forni può essere influenzato da:
- Influenze chimiche e fisiche:Le reazioni che avvengono all'interno del forno possono alterare il profilo della temperatura.
- Sporcizia e depositi:I residui di materiali come ceramiche, leghe o materiali di saldatura possono influire sulla distribuzione del calore e sulla precisione della temperatura.
- Processi di calibrazione:Le variazioni nei metodi di calibrazione dei produttori possono portare a differenze tra le temperature effettive e quelle impostate.
-
Il controllo della temperatura nei forni può essere influenzato da:
-
Importanza della progettazione e della configurazione del forno:
-
Quando si sceglie o si configura un forno di calcinazione, occorre considerare:
- Massa della zona calda:influisce sulla distribuzione del calore e sull'efficienza energetica.
- Intervallo di temperatura di esercizio:Assicurarsi che il forno sia in grado di gestire le temperature richieste.
- Distribuzione del flusso di gas e strategia di carico:influenzano l'uniformità del riscaldamento e i risultati del processo.
- Per ottenere prestazioni ottimali, la temperatura massima del forno dovrebbe essere da 100 a 200°C più alta rispetto alla temperatura di utilizzo effettiva.
-
Quando si sceglie o si configura un forno di calcinazione, occorre considerare:
-
Requisiti di temperatura specifici del materiale:
-
La temperatura e la durata della calcinazione dipendono da:
- Il materiale da lavorare (ad esempio, ceramica, metalli o minerali).
- La densità o le proprietà desiderate del prodotto finale.
- Ad esempio, i forni di sinterizzazione utilizzati nelle applicazioni dentali richiedono un controllo preciso della temperatura per ottenere la densità e la resistenza desiderate nei componenti in ceramica o in lega.
-
La temperatura e la durata della calcinazione dipendono da:
-
Forni continui e forni discontinui:
- I forni continui Sono ideali per i processi che richiedono condizioni di temperatura costanti e permanenti, come la ricottura o la tempra.
- I forni batch sono più versatili e possono gestire materiali e profili di temperatura diversi, rendendoli adatti a processi di calcinazione con requisiti specifici di temperatura e tempo.
-
Impatto della precisione della temperatura sui risultati:
- L'accuratezza della temperatura effettiva nel forno è fondamentale per ottenere risultati coerenti.
- Le variazioni di temperatura dovute a differenze di calibrazione o al tipo di costruzione del forno possono influire sulla qualità del prodotto finale.
- La manutenzione e la calibrazione regolari sono essenziali per mantenere l'accuratezza della temperatura e garantire prestazioni affidabili.
-
Considerazioni pratiche per gli acquirenti:
-
Quando si acquista un forno di calcinazione, valutare:
- La temperatura massima e se soddisfa i requisiti di processo.
- Il efficienza energetica e i costi di esercizio del forno.
- La durata e i requisiti di manutenzione dell'apparecchiatura.
- La scelta di un forno con una temperatura massima leggermente superiore a quella necessaria offre un margine di sicurezza e garantisce un'affidabilità a lungo termine.
-
Quando si acquista un forno di calcinazione, valutare:
Comprendendo questi punti chiave, gli acquirenti possono prendere decisioni informate quando scelgono un forno di calcinazione, assicurandosi che soddisfi i loro requisiti specifici di temperatura e processo, mantenendo efficienza e affidabilità.
Tabella riassuntiva:
Aspetto | Dettagli |
---|---|
Intervallo di temperatura tipico | Da 800°C a 1300°C, a seconda dei materiali e dei processi. |
Fattori che influenzano il controllo | Reazioni chimico-fisiche, sporcizia, metodi di calibrazione. |
Progettazione del forno | Massa della zona calda, distribuzione del flusso di gas, strategia di caricamento. |
Esigenze specifiche del materiale | La temperatura e la durata variano a seconda del materiale (ceramica, metalli, minerali). |
Continuo vs. Batch | Continuo per temperature costanti; batch per profili variabili. |
Precisione della temperatura | Fondamentale per ottenere risultati coerenti; la calibrazione regolare è essenziale. |
Considerazioni sull'acquisto | Temperatura massima, efficienza energetica, durata e manutenzione. |
Siete pronti a ottimizzare i vostri processi ad alta temperatura? Contattateci oggi stesso per una guida esperta nella scelta del forno di calcinazione perfetto!