La sinterizzazione è un processo critico nella produzione, in particolare nella metallurgia delle polveri e nella ceramica, dove trasforma i materiali in polvere in strutture solide e dense.Il processo prevede diverse fasi, tra cui la preparazione delle polveri, la compattazione e il riscaldamento controllato in un forno di sinterizzazione.Durante il riscaldamento, le particelle si legano per diffusione, formando una struttura coesiva senza fondere completamente il materiale.Il forno di sinterizzazione svolge un ruolo centrale, con l'atmosfera e il profilo di temperatura attentamente regolati per ottenere risultati specifici, come la rimozione del lubrificante, la riduzione degli ossidi e l'unione delle particelle.Il prodotto finale è un materiale durevole, ad alta resistenza e con una porosità ridotta.Di seguito è riportata una descrizione dettagliata del processo di sinterizzazione e delle sue fasi principali.
Punti chiave spiegati:
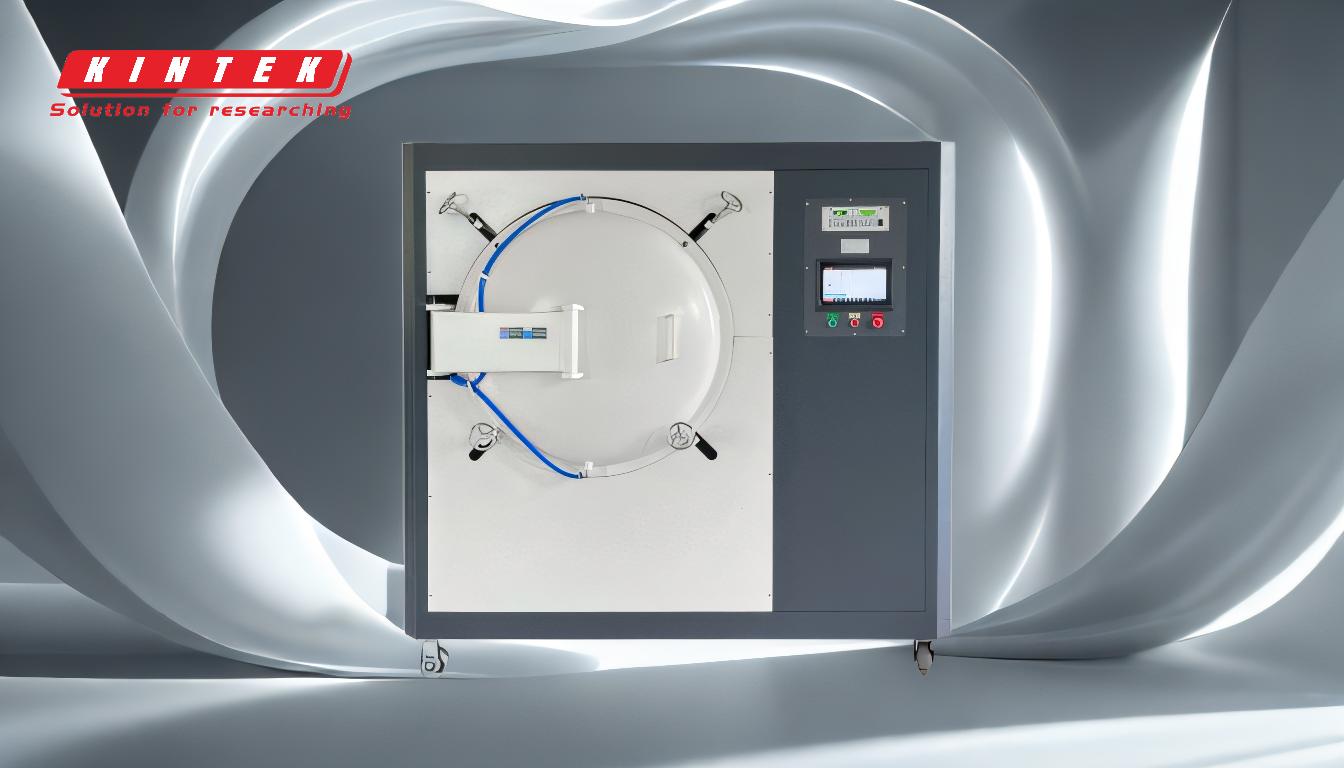
-
Fasi del processo di sinterizzazione:
- Preparazione della polvere:La materia prima, spesso in polvere, viene mescolata con additivi come leganti, deflocculanti e acqua per creare un impasto.Questa miscela viene essiccata a spruzzo per formare una polvere uniforme pronta per la compattazione.
- Compattazione:La polvere viene pressata in una forma specifica utilizzando metodi meccanici come la pressatura a freddo o a caldo.Questa fase elimina i vuoti e garantisce l'uniformità, dando vita a un "pezzo verde" che mantiene la forma ma non la resistenza.
- Sinterizzazione (cottura):La parte verde viene riscaldata in un forno di sinterizzazione in condizioni controllate.La temperatura viene mantenuta al di sotto del punto di fusione del materiale per facilitare il legame delle particelle attraverso la diffusione, la formazione di colli tra le particelle e la densificazione della struttura.
- Raffreddamento:Dopo la sinterizzazione, il materiale viene raffreddato gradualmente per solidificarsi in una struttura rigida e coesa.
-
Ruolo del forno di sinterizzazione:
-
Il forno è progettato con più zone, ognuna delle quali ha uno scopo specifico:
- Zona di rimozione del lubrificante:Rimuove i lubrificanti utilizzati durante la compattazione.
- Zona di riduzione dell'ossido:Riduce gli ossidi superficiali per migliorare l'adesione delle particelle.
- Zona di sinterizzazione:Facilita la diffusione e l'adesione delle particelle alle alte temperature.
- Zona di raffreddamento:Abbassa gradualmente la temperatura per solidificare il materiale.
- L'atmosfera del forno (ad esempio, idrogeno, azoto o vuoto) è attentamente controllata per prevenire l'ossidazione e garantire condizioni di sinterizzazione ottimali.
-
Il forno è progettato con più zone, ognuna delle quali ha uno scopo specifico:
-
Meccanismi di sinterizzazione:
- Diffusione:Gli atomi si muovono attraverso i confini delle particelle, formando colli e riducendo la porosità.
- Formazione del collo:Il legame iniziale tra le particelle crea una rete di strutture interconnesse.
- Densificazione:Con il passare del tempo, il materiale diventa più denso, poiché i pori si restringono e le particelle si fondono.
-
Tipi di sinterizzazione:
- Sinterizzazione allo stato solido:Si verifica senza fasi liquide, affidandosi esclusivamente alla diffusione.
- Sinterizzazione in fase liquida:Coinvolge una fase liquida che favorisce l'adesione delle particelle, spesso utilizzata per materiali con punti di fusione elevati.
- Sinterizzazione in fase liquida transitoria:Durante il riscaldamento si forma una fase liquida temporanea che si solidifica durante il raffreddamento.
-
Applicazioni della sinterizzazione:
- Metallurgia delle polveri:Utilizzata per produrre parti metalliche ad alta resistenza e durata, come ingranaggi, cuscinetti e componenti automobilistici.
- Ceramica:Utilizzati per creare prodotti ceramici come piastrelle, isolanti e materiali avanzati per l'elettronica.
- Materiali ad alto punto di fusione:Ideale per materiali come il tungsteno e il molibdeno, difficili da lavorare con i metodi di fusione tradizionali.
-
Vantaggi della sinterizzazione:
- Economico:Riduce lo spreco di materiale e il consumo di energia rispetto ai processi di fusione.
- Alta precisione:Consente la produzione di forme complesse con tolleranze ristrette.
- Proprietà del materiale:Migliora la forza, la durata e la resistenza all'usura del prodotto finale.
-
Sfide e considerazioni:
- Controllo della temperatura:Una regolazione precisa è essenziale per evitare la fusione o l'incollaggio incompleto.
- Gestione dell'atmosfera:L'atmosfera del forno deve essere attentamente controllata per evitare contaminazioni o ossidazioni.
- Selezione del materiale:Non tutti i materiali sono adatti alla sinterizzazione, in particolare quelli con basso punto di fusione o scarse proprietà di diffusione.
Grazie alla comprensione di questi punti chiave, gli acquirenti di apparecchiature e materiali di consumo possono prendere decisioni informate sui forni di sinterizzazione e sui relativi materiali, garantendo risultati ottimali per le loro applicazioni specifiche.
Tabella riassuntiva:
Aspetto chiave | Dettagli |
---|---|
Fasi della sinterizzazione | Preparazione della polvere, compattazione, sinterizzazione (cottura), raffreddamento |
Ruolo del forno di sinterizzazione | Rimozione del lubrificante, riduzione degli ossidi, zona di sinterizzazione, zona di raffreddamento |
Meccanismi | Diffusione, formazione del collo, densificazione |
Tipi di sinterizzazione | Allo stato solido, in fase liquida, in fase liquida transitoria. |
Applicazioni | Metallurgia delle polveri, ceramica, materiali ad alto punto di fusione |
Vantaggi | Economicità, alta precisione, migliori proprietà del materiale |
Sfide | Controllo della temperatura, gestione dell'atmosfera, selezione dei materiali |
Siete pronti a ottimizzare il vostro processo produttivo con il forno di sinterizzazione giusto? Contattateci oggi stesso per una guida esperta!