La brasatura a resistenza e la brasatura a induzione sono due metodi distinti per unire i metalli utilizzando un materiale d'apporto, ma differiscono notevolmente nei meccanismi di riscaldamento, nelle applicazioni e nelle caratteristiche operative. La brasatura a resistenza si basa sulla resistenza elettrica per generare calore direttamente sul giunto, il che la rende adatta a un riscaldamento localizzato e a un controllo preciso. La brasatura a induzione, invece, utilizza l'induzione elettromagnetica per riscaldare il pezzo, offrendo tassi di riscaldamento più rapidi e una migliore idoneità per geometrie complesse o per la produzione di grandi volumi. Entrambi i metodi presentano vantaggi e limiti unici, che li rendono adatti a diverse applicazioni industriali.
Punti chiave spiegati:
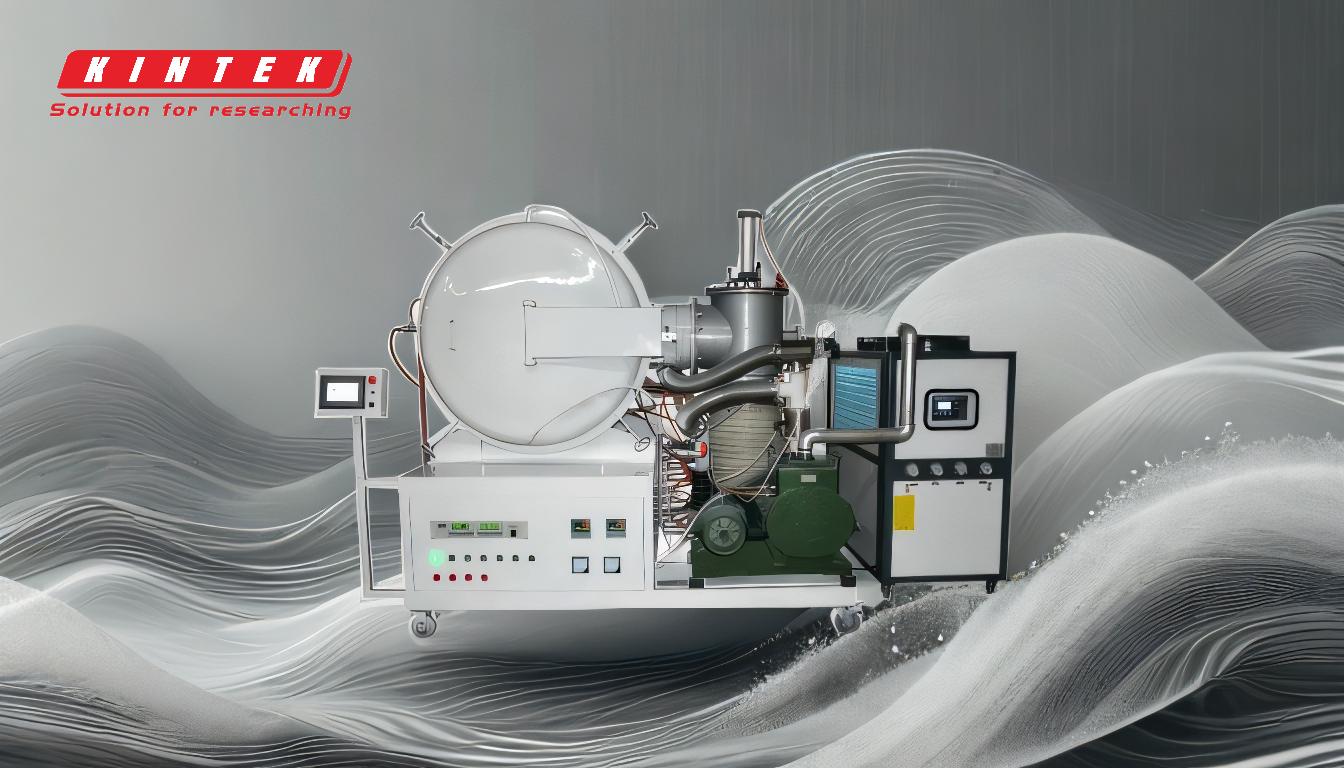
-
Meccanismo di riscaldamento:
-
Brasatura a resistenza:
- Il calore è generato dal passaggio di una corrente elettrica attraverso il giunto, che crea resistenza e produce un riscaldamento localizzato.
- Il calore si concentra sul giunto, riducendo al minimo le zone colpite dal calore nelle aree circostanti.
-
Brasatura a induzione:
- Il calore viene generato inducendo correnti parassite nel pezzo in lavorazione mediante un campo magnetico alternato.
- Il riscaldamento è più uniforme e può penetrare in profondità nel materiale, rendendolo adatto a pezzi più grandi o più complessi.
-
Brasatura a resistenza:
-
Efficienza energetica:
-
Brasatura a resistenza:
- Altamente efficiente dal punto di vista energetico per giunti piccoli e localizzati, grazie alla generazione diretta di calore sul giunto.
- Richiede un controllo preciso della corrente e della pressione per evitare il surriscaldamento o un riscaldamento insufficiente.
-
Brasatura a induzione:
- Più efficiente dal punto di vista energetico per i pezzi più grandi o per la produzione di grandi volumi, perché riscalda direttamente il pezzo da lavorare senza significative perdite di energia.
- I tassi di riscaldamento più rapidi riducono il consumo energetico complessivo per le attività ripetitive.
-
Brasatura a resistenza:
-
Controllo e precisione:
-
Brasatura a resistenza:
- Offre un eccellente controllo sul processo di riscaldamento, rendendolo ideale per lavori delicati o di precisione.
- Richiede un attento allineamento degli elettrodi e una pressione costante per garantire la corretta formazione del giunto.
-
Brasatura a induzione:
- Fornisce un riscaldamento rapido e costante, ma il controllo dipende maggiormente dal design della bobina a induzione e dalle impostazioni di frequenza.
- Adatto a linee di produzione automatizzate o ad alta velocità.
-
Brasatura a resistenza:
-
Applicazioni:
-
Brasatura a resistenza:
- Comunemente utilizzato per piccoli componenti, come contatti elettrici, gioielli o dispositivi medici.
- Ideale per applicazioni che richiedono un riscaldamento localizzato e una distorsione termica minima.
-
Brasatura a induzione:
- Ampiamente utilizzato nella produzione automobilistica, aerospaziale e industriale per assemblaggi più grandi o complessi.
- Adatto alla produzione di grandi volumi e di pezzi con geometrie complesse.
-
Brasatura a resistenza:
-
Attrezzatura e allestimento:
-
Brasatura a resistenza:
- Richiede elettrodi e dispositivi specializzati per applicare pressione e corrente.
- Le apparecchiature sono generalmente più semplici e meno costose rispetto ai sistemi a induzione.
-
Brasatura a induzione:
- Richiede una bobina di induzione e un alimentatore, che possono essere più complessi e costosi.
- Offre una maggiore flessibilità in termini di design del coil per adattarsi a forme e dimensioni diverse dei pezzi.
-
Brasatura a resistenza:
-
Compatibilità dei materiali:
-
Brasatura a resistenza:
- Funziona bene con materiali conduttivi come rame, ottone e acciaio.
- Limitato dalla necessità di un contatto elettrico diretto con il pezzo.
-
Brasatura a induzione:
- Compatibile con una gamma più ampia di materiali, compresi i metalli non conduttivi o a bassa conduttività quando si utilizzano i sonda.
- Può trattare materiali con proprietà termiche ed elettriche diverse.
-
Brasatura a resistenza:
-
Vantaggi e limiti:
-
Brasatura a resistenza:
- Vantaggi: Controllo preciso, riscaldamento localizzato e zone a bassa intensità di calore.
- Limitazioni: Limitata a giunti piccoli o semplici, richiede un contatto elettrico diretto ed è più lenta per la produzione di grandi volumi.
-
Brasatura a induzione:
- Vantaggi: Riscaldamento rapido, adatto a geometrie complesse e scalabile per la produzione di grandi volumi.
- Limitazioni: Costo iniziale dell'apparecchiatura più elevato, richiede un'attenta progettazione della bobina e può non essere ideale per pezzi molto piccoli o delicati.
-
Brasatura a resistenza:
Comprendendo queste differenze, gli acquirenti di apparecchiature e materiali di consumo possono decidere con cognizione di causa quale metodo di brasatura sia più adatto alle loro specifiche esigenze applicative.
Tabella riassuntiva:
Aspetto | Brasatura a resistenza | Brasatura a induzione |
---|---|---|
Meccanismo di riscaldamento | Calore generato dalla resistenza elettrica del giunto. | Calore generato dall'induzione elettromagnetica nel pezzo. |
Efficienza energetica | Altamente efficiente per piccole articolazioni localizzate. | Efficiente per i pezzi più grandi o per la produzione di grandi volumi. |
Controllo e precisione | Eccellente controllo per lavori delicati o di precisione. | Riscaldamento rapido, adatto alla produzione automatizzata o ad alta velocità. |
Applicazioni | Piccoli componenti (ad esempio, contatti elettrici, gioielli). | Assemblaggi più grandi o complessi (ad esempio, settore automobilistico, aerospaziale). |
Attrezzatura e allestimento | Attrezzature più semplici e meno costose. | Apparecchiature più complesse e costose con design flessibile delle bobine. |
Compatibilità dei materiali | Lavora con materiali conduttivi (ad es. rame, ottone). | Compatibile con una gamma più ampia di materiali, compresi i metalli non conduttivi. |
Vantaggi | Regolazione precisa, riscaldamento localizzato, zone a bassa intensità di calore. | Riscaldamento rapido, scalabile per la produzione di grandi volumi, adatto a geometrie complesse. |
Limitazioni | Limitato a piccoli giunti, richiede un contatto elettrico diretto. | Costo iniziale più elevato, richiede un'attenta progettazione della bobina. |
Non siete ancora sicuri di quale sia il metodo di brasatura migliore per la vostra applicazione? Contattate i nostri esperti oggi stesso per una consulenza personalizzata!