La rifusione ad arco sottovuoto (VAR) è un processo metallurgico specializzato utilizzato per affinare e migliorare la qualità di metalli e leghe, in particolare quelli utilizzati in applicazioni ad alte prestazioni come il settore aerospaziale, gli impianti medici e la generazione di energia.Il processo prevede la fusione di un elettrodo consumabile in condizioni di vuoto, utilizzando un arco elettrico che aiuta a rimuovere le impurità, a controllare la microstruttura e a migliorare le proprietà meccaniche del materiale.I vantaggi del VAR includono una maggiore purezza del materiale, una riduzione del contenuto di gas, una migliore omogeneità e un miglioramento delle proprietà meccaniche come la forza, la resistenza alla fatica e la duttilità.Questi vantaggi rendono il VAR un processo essenziale per la produzione di materiali ad alta integrità che soddisfano i rigorosi standard industriali.
Spiegazione dei punti chiave:
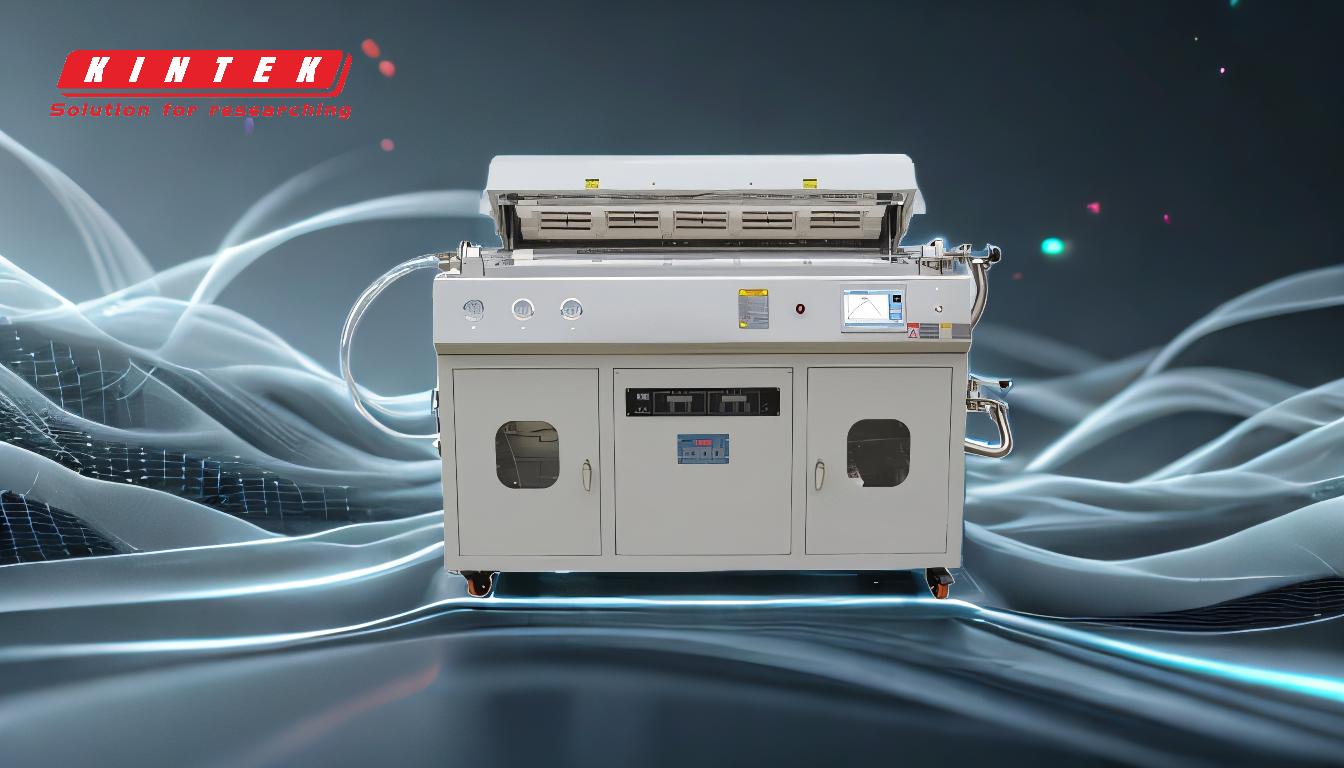
-
Migliore purezza del materiale:
- Il VAR elimina impurità come ossidi, solfuri e altre inclusioni non metalliche fondendo il metallo in un ambiente sotto vuoto.Il risultato è un materiale più pulito e con meno difetti, un aspetto fondamentale per le applicazioni che richiedono affidabilità e prestazioni elevate.
-
Riduzione del contenuto di gas:
- L'ambiente sottovuoto del VAR riduce significativamente i livelli di gas disciolti come idrogeno, ossigeno e azoto nel metallo.La riduzione del contenuto di gas minimizza il rischio di porosità e migliora la resistenza del materiale alle cricche e all'infragilimento.
-
Maggiore controllo della microstruttura:
- Il VAR consente di controllare con precisione il processo di solidificazione, ottenendo una microstruttura uniforme e a grana fine.Questa uniformità migliora le proprietà meccaniche del materiale, come la forza, la tenacità e la resistenza alla fatica.
-
Migliore omogeneità:
- Il processo di rifusione assicura una composizione chimica coerente in tutto il materiale, riducendo la segregazione e migliorando la qualità complessiva della lega.Ciò è particolarmente importante per le leghe utilizzate in applicazioni critiche, dove la coerenza è fondamentale.
-
Migliori proprietà meccaniche:
- La combinazione di impurità ridotte, minore contenuto di gas e microstruttura controllata consente di ottenere materiali con proprietà meccaniche superiori.Queste includono una maggiore resistenza alla trazione, una migliore durata a fatica e una maggiore duttilità, rendendo i materiali lavorati al VAR ideali per gli ambienti più difficili.
-
Applicazioni nelle industrie ad alte prestazioni:
- Il VAR è ampiamente utilizzato in settori come quello aerospaziale, medico e della generazione di energia, dove i materiali devono resistere a condizioni estreme.Ad esempio, le leghe lavorate al VAR sono utilizzate nei componenti dei motori a reazione, negli impianti chirurgici e nelle pale delle turbine, dove il fallimento non è un'opzione.
-
Conformità agli standard industriali:
- La VAR aiuta i produttori a soddisfare i severi standard e le specifiche del settore, garantendo che i materiali prodotti siano della massima qualità e adatti ad applicazioni critiche.
In sintesi, la rifusione sotto vuoto offre vantaggi significativi in termini di purezza del materiale, controllo della microstruttura e proprietà meccaniche, rendendolo un processo indispensabile per la produzione di leghe ad alte prestazioni utilizzate in applicazioni critiche.
Tabella riassuntiva:
Prestazioni | Descrizione |
---|---|
Migliore purezza dei materiali | Elimina impurità come ossidi e solfuri, ottenendo materiali più puliti. |
Riduzione del contenuto di gas | Riduce i gas disciolti, riducendo la porosità e migliorando la resistenza alle cricche. |
Microstruttura migliorata | Assicura una microstruttura uniforme e a grana fine per migliorare le proprietà meccaniche. |
Migliore omogeneità | Garantisce una composizione chimica coerente, riducendo la segregazione. |
Proprietà meccaniche superiori | Aumenta la resistenza alla trazione, alla fatica e alla duttilità. |
Applicazioni ad alte prestazioni | Utilizzati nei settori aerospaziale, medico e della generazione di energia. |
Conformità agli standard | Soddisfa le rigorose specifiche industriali per le applicazioni critiche. |
Scoprite come la rifusione ad arco sottovuoto può elevare la qualità dei vostri materiali... contattate i nostri esperti oggi stesso !