I forni di sinterizzazione sono essenziali in diversi settori industriali per il consolidamento di materiali in polvere in componenti solidi e densi.Sono disponibili in diversi tipi, ciascuno progettato per applicazioni, materiali e requisiti di temperatura specifici.Tra i tipi più comuni vi sono i forni a spinta, i forni a trave mobile, i forni per sinterizzazione sotto vuoto, i forni per sinterizzazione a resistenza e i forni per sinterizzazione a induzione.Questi forni possono essere ulteriormente classificati in base ai metodi di riscaldamento (ad esempio, elementi in ceramica o microonde), agli intervalli di temperatura e ai livelli di vuoto.Inoltre, per ottenere le proprietà desiderate dei materiali, vengono utilizzate tecniche di sinterizzazione come la sinterizzazione allo stato solido, la sinterizzazione in fase liquida e la sinterizzazione a microonde.La comprensione di questi tipi e delle loro applicazioni è fondamentale per selezionare l'apparecchiatura giusta per le specifiche esigenze di produzione.
Punti chiave spiegati:
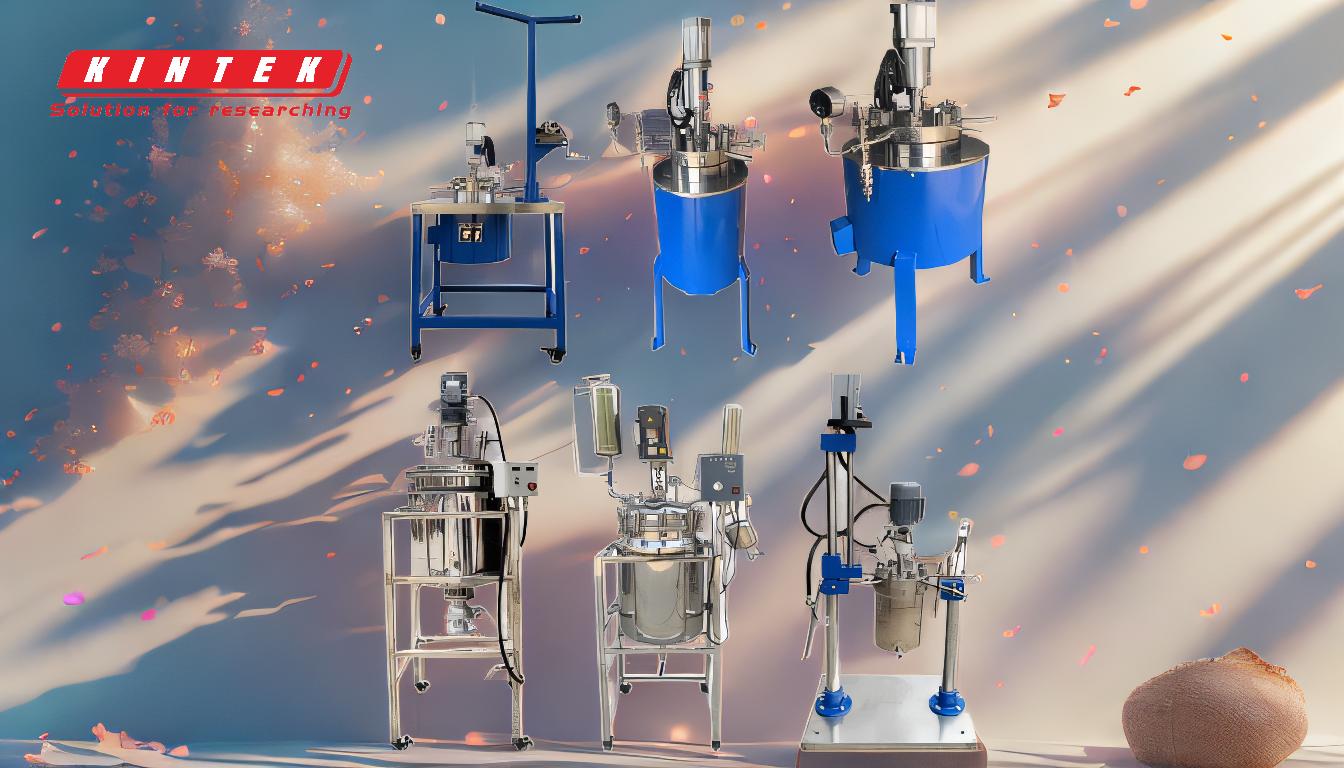
-
Forni a spinta e forni a trave mobile:
- Forni a spinta:Questi forni spostano i pezzi in lavorazione all'interno del forno su una serie di barche o piastre in un treno continuo.Sono ideali per la produzione di grandi volumi e sono comunemente utilizzati nei settori che richiedono un riscaldamento costante e uniforme.
- Forni a trave mobile:Utilizzano un meccanismo di spinta per spostare le imbarcazioni attraverso il forno su travi che si sollevano, spingono in avanti e si abbassano per far "camminare" l'imbarcazione attraverso il forno.Questo design riduce l'attrito e l'usura, rendendolo adatto a componenti delicati o di alta precisione.
-
Forni di sinterizzazione sotto vuoto:
-
Classificazione per temperatura:
- Forni di sinterizzazione ordinari:Funzionano a temperature fino a 1300℃.
- Forni di sinterizzazione a media temperatura:Funzionano tra 1300℃ e 1600℃.
- Forni di sinterizzazione ad alta temperatura:Funziona tra 1600℃ e 2400℃.
-
Classificazione per livello di vuoto:
- Basso vuoto:Adatto per materiali che richiedono un controllo minimo dell'ossidazione.
- Alto vuoto:Utilizzato per materiali che richiedono un controllo rigoroso dell'ossidazione e della contaminazione.
- Ultra-alto vuoto:Ideale per materiali avanzati che richiedono la massima purezza e una contaminazione minima.
-
Tipi basati sull'applicazione:
- Forni di sinterizzazione sottovuoto per ceramica:Progettati per materiali ceramici.
- Forni di sinterizzazione sotto vuoto per metalli:Su misura per i materiali metallici.
- Forni di sinterizzazione sottovuoto per materiali compositi:Utilizzato per i materiali compositi.
-
Classificazione per temperatura:
-
Metodi di riscaldamento:
- Elementi in ceramica:Comunemente realizzati con materiali come il disiliciuro di molibdeno (MoSi2) o il carburo di silicio (SiC), questi elementi forniscono un riscaldamento costante e affidabile.
- Sinterizzazione a microonde:Un metodo più recente che utilizza le microonde per ottenere un riscaldamento rapido e uniforme, spesso con tempi di sinterizzazione più rapidi e proprietà del materiale migliori.
-
Forni di sinterizzazione a resistenza e a induzione:
- Forni di sinterizzazione a resistenza:Convertono l'energia elettrica in energia termica attraverso elementi riscaldanti elettrici.Sono versatili e ampiamente utilizzati in vari settori industriali.
- Forni di sinterizzazione a induzione:Utilizza l'induzione elettromagnetica per eccitare correnti elettriche nel metallo, generando calore.Questo metodo è efficiente e adatto ai materiali conduttivi.
-
Tecniche di sinterizzazione:
- Sinterizzazione allo stato solido:Consiste nel riscaldare il materiale in polvere appena al di sotto del suo punto di fusione per legare le particelle attraverso la diffusione atomica.Questo metodo è comune per ceramiche e metalli.
- Sinterizzazione in fase liquida:Utilizza un liquido solvente per indurre una bassa porosità e un legame, che viene poi allontanato dal riscaldamento.Questa tecnica è spesso utilizzata per materiali che richiedono alta densità e resistenza.
- Sinterizzazione reattiva:Comporta una reazione chimica delle particelle di polvere durante il riscaldamento, che porta alla formazione di nuovi composti o fasi.
- Sinterizzazione a microonde:Utilizza le microonde per il riscaldamento e l'integrazione rapidi, spesso con il risultato di migliorare le proprietà dei materiali e ridurre i tempi di lavorazione.
- Sinterizzazione al plasma a scintilla:Impiega la corrente elettrica e la compressione fisica per ottenere una sinterizzazione rapida, spesso utilizzata per i materiali avanzati.
- Pressatura isostatica a caldo:Applica alta pressione e temperatura per formare e fondere le particelle di polvere, ottenendo componenti ad alta densità con eccellenti proprietà meccaniche.
Conoscere i diversi tipi di forni di sinterizzazione e le loro applicazioni è fondamentale per selezionare l'apparecchiatura giusta in base alle proprietà del materiale, al volume di produzione e ai risultati desiderati.Ogni tipo offre vantaggi unici, che li rendono adatti a specifiche esigenze industriali.
Tabella riassuntiva:
Tipo di forno di sinterizzazione | Caratteristiche principali | Applicazioni |
---|---|---|
Forni a spinta | Treno continuo, produzione di grandi volumi | Riscaldamento uniforme per ceramica e metalli |
Forni a trave mobile | Basso attrito, alta precisione | Componenti delicati o di alta precisione |
Forni di sinterizzazione sotto vuoto | Intervalli di temperatura (fino a 2400℃), livelli di vuoto | Ceramica, metalli, compositi |
Forni di sinterizzazione a resistenza | Elementi riscaldanti elettrici | Uso industriale versatile |
Forni di sinterizzazione a induzione | Induzione elettromagnetica | Materiali conduttivi |
Sinterizzazione a microonde | Riscaldamento rapido e uniforme | Materiali avanzati, lavorazione più rapida |
Avete bisogno di aiuto per scegliere il forno di sinterizzazione giusto? Contattate oggi stesso i nostri esperti per soluzioni su misura!