La porosità della ceramica è influenzata da diversi fattori, tra cui la porosità iniziale del compatto verde, la temperatura di sinterizzazione, la durata del processo di sinterizzazione e l'applicazione della pressione durante la sinterizzazione.Le ceramiche a base di ossidi puri, in particolare, richiedono temperature più elevate e tempi di sinterizzazione più lunghi a causa della diffusione delle particelle allo stato solido.La comprensione di questi fattori è fondamentale per controllare la porosità finale dei prodotti ceramici, che influisce direttamente sulle loro proprietà meccaniche, termiche ed elettriche.
Punti chiave spiegati:
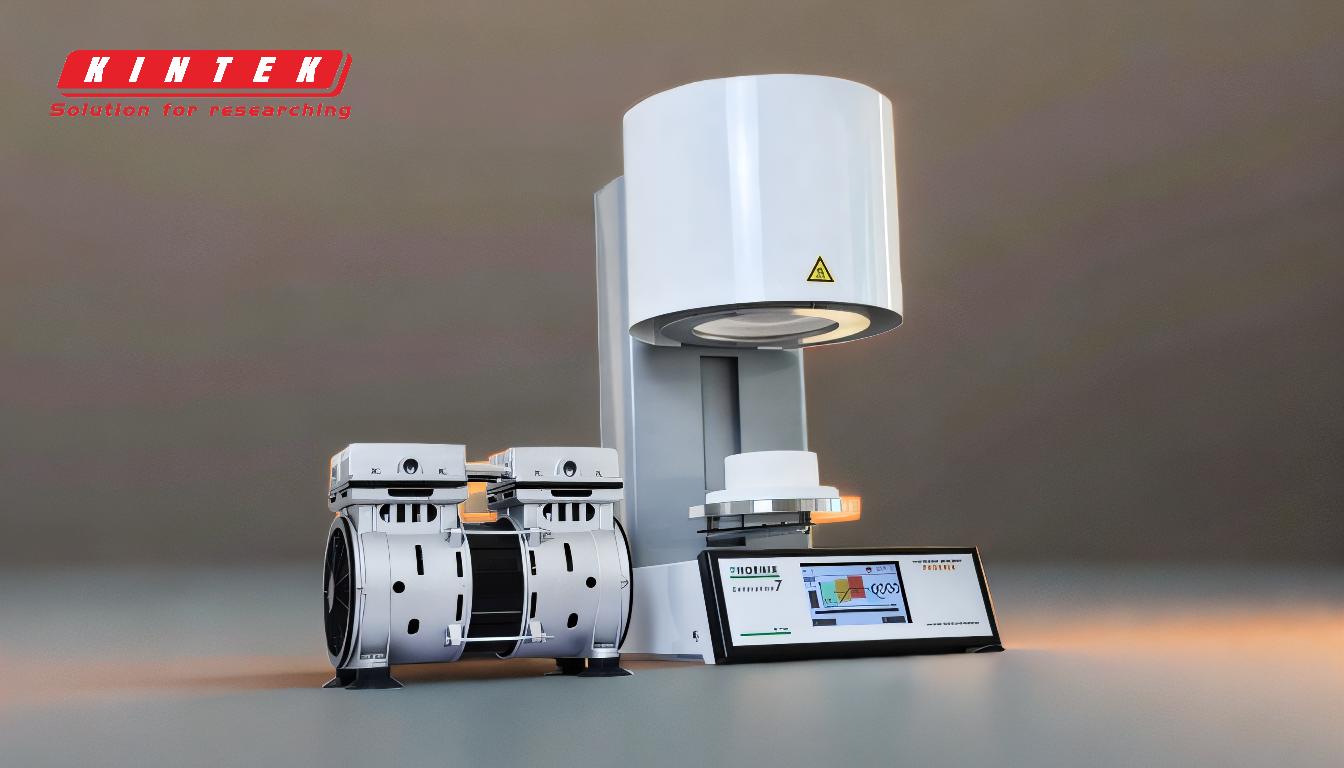
-
Porosità iniziale del compatto verde:
- Il compatto verde si riferisce al materiale ceramico prima di essere sottoposto a sinterizzazione.La porosità iniziale di questo compatto gioca un ruolo importante nel determinare la porosità finale della ceramica sinterizzata.
- Una porosità iniziale più elevata porta generalmente a una porosità finale più elevata, a meno che il processo di sinterizzazione non la riduca efficacemente.
- La densità e l'uniformità del compatto verde sono fondamentali.Un compatto verde più denso, con meno vuoti, determina una minore porosità finale dopo la sinterizzazione.
-
Temperatura di sinterizzazione:
- La temperatura di sinterizzazione è un fattore critico per ridurre la porosità.Temperature più elevate facilitano la diffusione delle particelle, portando a strutture ceramiche più dense.
- Per le ceramiche a base di ossidi puri, sono necessarie temperature di sinterizzazione più elevate perché la diffusione delle particelle avviene allo stato solido, che è più lento rispetto alla sinterizzazione in fase liquida.
- Tuttavia, temperature troppo elevate possono portare a effetti indesiderati come la crescita dei grani, che potrebbe avere un impatto negativo sulle proprietà meccaniche della ceramica.
-
Durata del processo di sinterizzazione:
- Anche la durata del processo di sinterizzazione influisce sulla porosità finale.Tempi di sinterizzazione più lunghi consentono una diffusione e una densificazione delle particelle più completa.
- Nel caso delle ceramiche a base di ossidi puri, sono necessari tempi di sinterizzazione più lunghi per ottenere la riduzione desiderata della porosità, a causa della più lenta diffusione allo stato solido.
- Bilanciare il tempo di sinterizzazione con la temperatura è essenziale per ottenere una porosità ottimale senza causare un'eccessiva crescita dei grani o altri difetti.
-
Applicazione della pressione:
- L'applicazione di pressione durante il processo di sinterizzazione può ridurre significativamente sia il tempo di sinterizzazione che la porosità finale.Questa tecnica è nota come sinterizzazione assistita da pressione o pressatura a caldo.
- La pressione aiuta a chiudere i pori e a favorire il riarrangiamento delle particelle, dando vita a una struttura ceramica più densa.
- Questo metodo è particolarmente utile per i materiali difficili da sinterizzare in condizioni normali, come alcune ceramiche di ossido puro.
-
Composizione del materiale:
- Anche il tipo di materiale ceramico influenza la porosità.Le ceramiche a base di ossido puro, ad esempio, hanno un comportamento di sinterizzazione diverso rispetto alle ceramiche composite.
- Per modificare il comportamento di sinterizzazione e ridurre la porosità si possono usare additivi o droganti.Questi additivi possono abbassare la temperatura di sinterizzazione o aumentare la velocità di diffusione.
-
Dimensione e distribuzione delle particelle:
- La dimensione e la distribuzione delle particelle ceramiche nel green compact influenzano il processo di sinterizzazione e la porosità finale.
- Le particelle più piccole hanno un rapporto superficie/volume più elevato, che favorisce una sinterizzazione e una densificazione più rapide.
- Una distribuzione uniforme delle dimensioni delle particelle aiuta a ottenere una microstruttura più omogenea con una porosità controllata.
Controllando attentamente questi fattori, i produttori possono personalizzare la porosità dei prodotti ceramici per soddisfare i requisiti di applicazioni specifiche, che si tratti di componenti strutturali, isolanti termici o substrati elettronici.
Tabella riassuntiva:
Fattore | Impatto sulla porosità |
---|---|
Porosità iniziale del compatto verde | Una porosità iniziale più elevata comporta una porosità finale più elevata, a meno che la sinterizzazione non la riduca. |
Temperatura di sinterizzazione | Temperature più elevate riducono la porosità, ma un calore eccessivo può causare la crescita dei grani. |
Durata della sinterizzazione | Tempi di sinterizzazione più lunghi riducono la porosità, soprattutto per le ceramiche di ossido puro. |
Applicazione della pressione | La sinterizzazione assistita dalla pressione riduce la porosità e il tempo di sinterizzazione. |
Composizione del materiale | Le ceramiche di ossido puro richiedono temperature più elevate e tempi di sinterizzazione più lunghi. |
Dimensione e distribuzione delle particelle | Le particelle più piccole e uniformi favoriscono una sinterizzazione più rapida e una porosità controllata. |
Avete bisogno di aiuto per ottimizzare la porosità della ceramica per il vostro progetto? Contattate i nostri esperti oggi stesso !