La sinterizzazione in fase liquida, pur essendo vantaggiosa per migliorare la densificazione e ridurre le temperature di sinterizzazione, presenta diversi svantaggi.Tra questi, le difficoltà nel controllo della microstruttura, il potenziale di densificazione non uniforme e le limitazioni nella selezione dei materiali dovute alla necessità di una fase liquida compatibile.Inoltre, il processo può portare a problemi quali la crescita dei grani, le tensioni residue e l'anisotropia delle proprietà.Le alte temperature e il consumo di energia associati alla sinterizzazione in fase liquida contribuiscono ad aumentare i costi operativi e le preoccupazioni ambientali.La comprensione di questi inconvenienti è fondamentale per ottimizzare il processo e selezionare i materiali e i parametri giusti per le applicazioni specifiche.
Punti chiave spiegati:
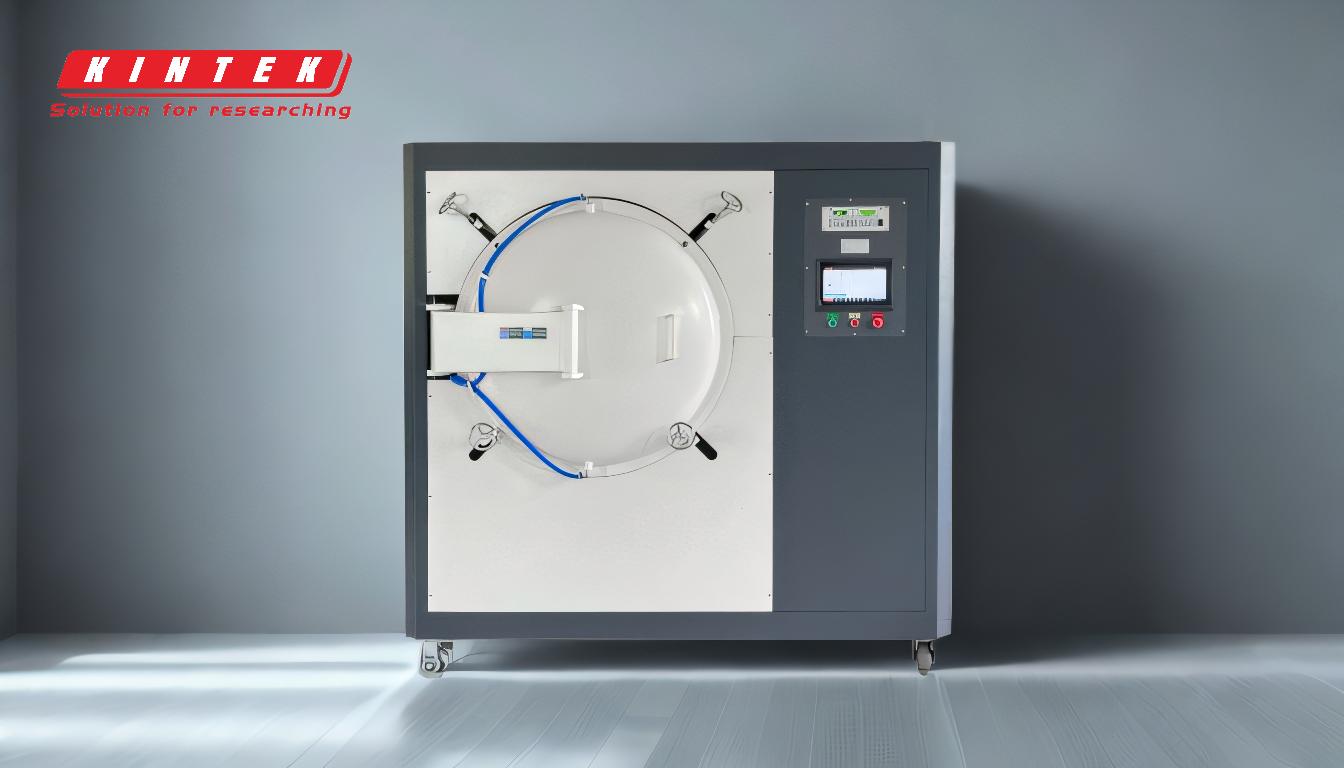
-
Sfide di controllo della microstruttura:
- La sinterizzazione in fase liquida può portare a un accrescimento e a una coartazione non uniformi dei grani, con conseguente microstruttura meno uniforme.
- La presenza di una fase liquida può causare una densificazione localizzata, con conseguenti variazioni della densità e delle proprietà meccaniche nel pezzo sinterizzato.
-
Anisotropia delle proprietà:
- Il flusso della fase liquida durante la sinterizzazione può causare un allineamento direzionale dei grani, con conseguente anisotropia delle proprietà meccaniche, termiche ed elettriche.
- Questa anisotropia può essere problematica per le applicazioni che richiedono un comportamento isotropo.
-
Limitazioni nella selezione dei materiali:
- La sinterizzazione in fase liquida richiede la formazione di una fase liquida compatibile, il che limita la gamma di materiali che possono essere efficacemente sinterizzati con questo metodo.
- La necessità di additivi specifici per la formazione della fase liquida può complicare la formulazione del materiale e aumentare i costi.
-
Sollecitazioni residue e difetti:
- Il processo di raffreddamento dopo la sinterizzazione in fase liquida può indurre tensioni residue dovute al ritiro differenziale tra la fase solida e quella liquida.
- Queste tensioni possono causare cricche, deformazioni o altri difetti nel prodotto finale.
-
Elevato consumo di energia:
- La sinterizzazione in fase liquida richiede spesso temperature elevate per ottenere la formazione della fase liquida necessaria, con conseguente aumento del consumo energetico.
- Ciò contribuisce ad aumentare i costi operativi e l'impatto ambientale.
-
Crescita e sgrossamento dei grani:
- La fase liquida può accelerare la crescita dei grani, che può degradare le proprietà meccaniche del materiale sinterizzato.
- Il controllo della dimensione dei grani diventa più impegnativo e richiede un controllo preciso dei parametri di sinterizzazione.
-
Costi e complessità:
- Le attrezzature e il controllo del processo necessari per la sinterizzazione in fase liquida sono più complessi e costosi rispetto alla sinterizzazione allo stato solido.
- La necessità di stampi specializzati, additivi e forni ad alta temperatura aumenta il costo complessivo.
-
Restringimento e controllo dimensionale:
- I pezzi sinterizzati con una fase liquida spesso subiscono un maggiore ritiro, che deve essere tenuto in considerazione durante il processo di progettazione e produzione.
- Ciò può complicare la produzione di pezzi con tolleranze dimensionali ristrette.
-
Problemi ambientali e di sicurezza:
- Le alte temperature e l'uso potenziale di materiali pericolosi nella sinterizzazione in fase liquida possono comportare rischi per la sicurezza e sfide ambientali.
- Per ridurre questi problemi è necessario gestire e smaltire correttamente i materiali e i sottoprodotti.
Comprendendo questi svantaggi, i produttori possono valutare meglio l'idoneità della sinterizzazione in fase liquida per le loro applicazioni specifiche e adottare misure per mitigare i potenziali problemi attraverso un'attenta progettazione del processo e la selezione dei materiali.
Tabella riassuntiva:
Svantaggio | Dettagli chiave |
---|---|
Controllo della microstruttura | Crescita irregolare dei grani, densificazione localizzata e proprietà non uniformi. |
Anisotropia delle proprietà | Allineamento direzionale dei grani che porta a un comportamento meccanico/termico incoerente. |
Limitazioni nella selezione dei materiali | Richiede una fase liquida compatibile, limitando le opzioni di materiale e aumentando i costi. |
Sollecitazioni residue e difetti | Il ritiro differenziale provoca fessurazioni, deformazioni o altri difetti. |
Elevato consumo di energia | Le alte temperature aumentano il consumo di energia e i costi operativi. |
Crescita e sgrossamento dei grani | La crescita accelerata dei grani degrada le proprietà meccaniche. |
Costi e complessità | Attrezzature e additivi specializzati aumentano i costi e la complessità del processo. |
Restringimento e controllo dimensionale | Un maggiore restringimento complica la produzione con tolleranze strette. |
Problemi ambientali e di sicurezza | Le alte temperature e i materiali pericolosi comportano rischi e problemi ambientali. |
Avete bisogno di aiuto per ottimizzare il vostro processo di sinterizzazione? Contattate oggi stesso i nostri esperti per soluzioni su misura!