La saldatura a induzione, sebbene vantaggiosa in molte applicazioni industriali, presenta numerosi notevoli svantaggi. Questi includono elevati costi iniziali, complessità operativa, limitazioni dei materiali e sfide legate al perfezionamento e al mantenimento della composizione dei materiali. Di seguito, esploriamo questi svantaggi in dettaglio, fornendo una comprensione completa delle limitazioni associate alla saldatura a induzione.
Punti chiave spiegati:
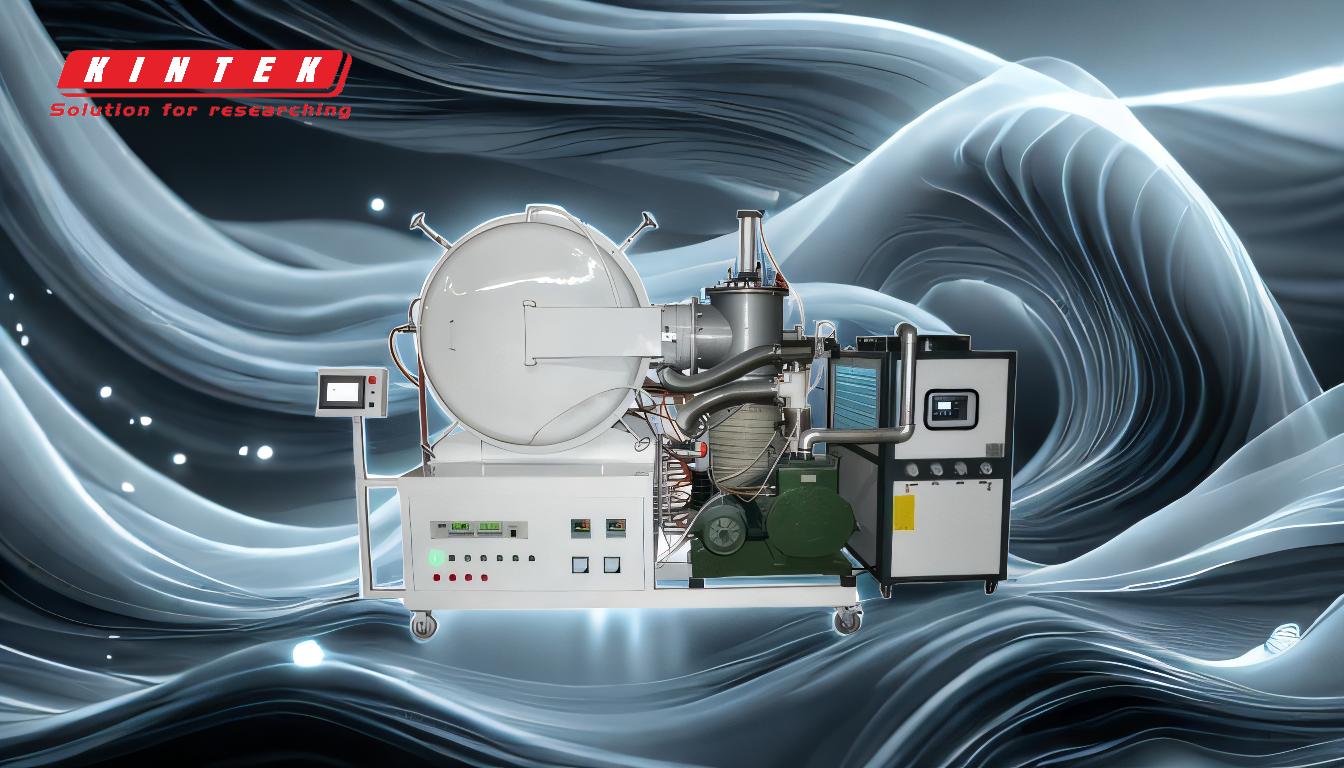
-
Costo iniziale elevato
- Le attrezzature per la saldatura a induzione sono significativamente più costose rispetto ai metodi di saldatura tradizionali.
- Il costo comprende non solo la macchina stessa ma anche le infrastrutture associate, come alimentatori e sistemi di raffreddamento.
- Per le operazioni su piccola scala o le aziende con budget limitati, questo elevato investimento iniziale può rappresentare un grave ostacolo all’adozione.
-
Processo e funzionamento complessi
- La saldatura a induzione richiede conoscenze e formazione specializzate per funzionare in modo efficace.
- Il processo prevede un controllo preciso di parametri quali frequenza, potenza e tempo di riscaldamento, il che può rappresentare una sfida per gli operatori inesperti.
- Anche la manutenzione delle apparecchiature richiede competenze tecniche, che si aggiungono alla complessità operativa.
-
Limitazioni materiali
- La saldatura a induzione non è adatta a tutti i materiali. Funziona meglio con metalli conduttivi come rame, ottone e acciaio.
- I materiali non conduttivi o quelli con scarsa conduttività termica potrebbero non riscaldarsi in modo uniforme o efficiente, portando a risultati incoerenti.
- Alcuni materiali possono anche degradarsi o ossidarsi alle alte temperature generate dal riscaldamento a induzione.
-
Mancanza di capacità di raffinazione
- La saldatura a induzione non ha la capacità di affinare o purificare i materiali durante il processo.
- I materiali utilizzati devono essere preventivamente privi di ossidi e contaminanti, poiché questi possono influire negativamente sulla qualità del giunto di saldatura.
- Questa limitazione richiede ulteriori fasi di pre-elaborazione, aumentando tempi e costi.
-
Ossidazione e perdita di elementi di lega
- Le alte temperature durante la saldatura a induzione possono causare l'ossidazione di alcuni materiali, in particolare quelli con elementi di lega reattivi.
- L'ossidazione può portare alla perdita di elementi leganti critici, che potrebbero dover essere aggiunti nuovamente per mantenere le proprietà del materiale desiderate.
- Questo problema può compromettere l'integrità e le prestazioni del prodotto finale.
-
Consumo ed efficienza energetica
- I sistemi di saldatura a induzione possono essere ad alta intensità energetica, soprattutto quando funzionano a frequenze o livelli di potenza elevati.
- Sebbene il riscaldamento a induzione sia generalmente efficiente, il consumo energetico complessivo può comunque essere maggiore rispetto ad altri metodi di saldatura, a seconda dell’applicazione.
-
Flessibilità limitata per parti piccole o complesse
- La saldatura a induzione è meno efficace per parti piccole, complesse o di forma irregolare a causa delle difficoltà nel raggiungere un riscaldamento uniforme.
- Potrebbero essere necessari progetti di bobine personalizzati per applicazioni specifiche, aumentando la complessità e i costi.
-
Preoccupazioni per la sicurezza
- Le alte temperature e i campi elettromagnetici generati durante la saldatura a induzione pongono rischi per la sicurezza degli operatori.
- Per mitigare questi rischi sono necessarie misure di sicurezza adeguate, come schermature e dispositivi di protezione.
In sintesi, sebbene la saldatura a induzione offra vantaggi quali velocità, precisione e riscaldamento localizzato, i suoi svantaggi, tra cui costi elevati, limitazioni dei materiali e complessità operativa, devono essere attentamente considerati. Questi fattori lo rendono meno adatto a determinate applicazioni o aziende con risorse limitate. Comprendere queste limitazioni è fondamentale per prendere decisioni informate sul fatto che la saldatura a induzione sia la scelta giusta per un caso d'uso specifico.
Tabella riassuntiva:
Svantaggio | Dettagli |
---|---|
Costo iniziale elevato | Attrezzature e infrastrutture costose; barriera per le operazioni su piccola scala. |
Processo e funzionamento complessi | Richiede una formazione specializzata e un controllo preciso dei parametri. |
Limitazioni materiali | Ideale per metalli conduttivi; sfide con materiali non conduttivi. |
Mancanza di capacità di raffinazione | Nessuna purificazione del materiale durante il processo; è necessaria la pre-elaborazione. |
Ossidazione e perdita di lega | Le alte temperature causano l'ossidazione e la perdita di elementi leganti critici. |
Consumo energetico | Può essere ad alta intensità energetica, soprattutto alle alte frequenze. |
Flessibilità limitata | Meno efficace per parti piccole o complesse; potrebbero essere necessarie bobine personalizzate. |
Preoccupazioni per la sicurezza | Le alte temperature e i campi elettromagnetici rappresentano rischi per gli operatori. |
Hai bisogno di aiuto per decidere se la saldatura a induzione è adatta alla tua applicazione? Contatta i nostri esperti oggi stesso per una consulenza personalizzata!