Lo sputtering DC, sebbene sia una tecnica ampiamente utilizzata nella deposizione di film sottili, presenta diversi svantaggi che possono limitarne l'efficacia in determinate applicazioni. Questi includono l’incapacità di spruzzare materiali non conduttivi, tassi di deposizione più bassi rispetto a tecniche più avanzate e sfide legate all’erosione del target e al controllo del processo. Comprendere queste limitazioni è fondamentale per selezionare il metodo di sputtering appropriato per esigenze industriali specifiche.
Punti chiave spiegati:
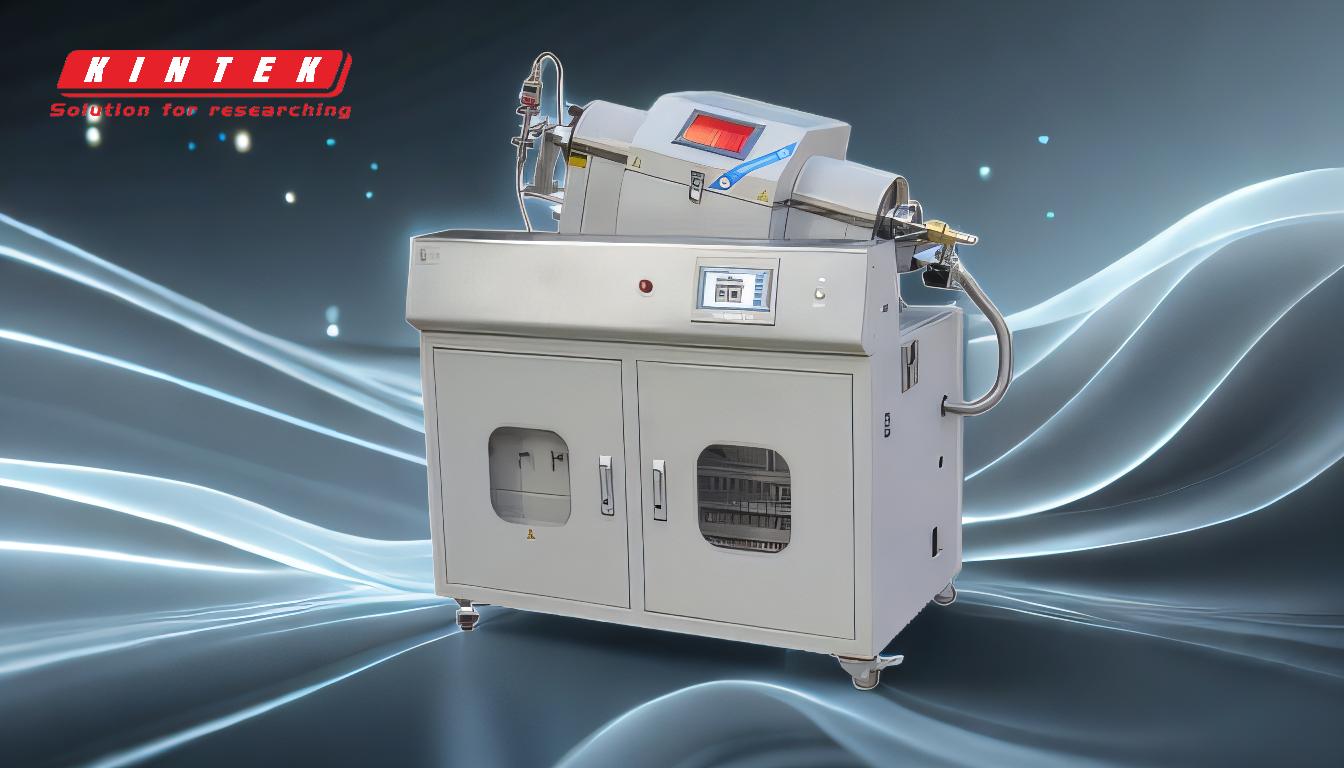
-
Impossibilità di spruzzare materiali non conduttivi:
- Lo sputtering DC è limitato ai materiali conduttivi. I materiali non conduttivi, come gli isolanti, non possono essere spruzzati in modo efficace utilizzando metodi DC perché accumulano carica, che interrompe il processo di sputtering. Questa limitazione è significativa nei settori in cui vengono comunemente utilizzati materiali isolanti, come in alcune applicazioni di semiconduttori. Per tali materiali, viene spesso utilizzato lo sputtering del magnetron RF poiché utilizza corrente alternata per prevenire l'accumulo di carica.
-
Tassi di deposizione più bassi:
- Rispetto alle tecniche di sputtering più avanzate come l'HIPIMS (High Power Impulse Magnetron Sputtering), lo sputtering DC offre generalmente tassi di deposizione inferiori. Ciò è dovuto alle densità del plasma più basse e alle densità dei gas più elevate nel processo di sputtering DC. Tassi di deposizione più bassi possono portare a tempi di lavorazione più lunghi, il che potrebbe non essere l’ideale per ambienti di produzione ad alta produttività.
-
Erosione e non uniformità del target:
- Uno dei notevoli svantaggi dello sputtering del magnetron DC è l'erosione non uniforme del materiale target. Questa usura irregolare può portare ad una riduzione della durata di vita del target e può anche influenzare la qualità e l'uniformità della pellicola depositata. Per mitigare questi effetti sono necessari una manutenzione regolare e la sostituzione degli obiettivi, che si aggiungono ai costi operativi.
-
Sensibilità ai parametri di processo:
- Per ottenere risultati ottimali con lo sputtering DC è necessario un controllo preciso su vari parametri di processo, tra cui la pressione del gas, la distanza dal substrato target e la tensione. Qualsiasi deviazione dalle impostazioni ottimali può avere un impatto significativo sulla qualità della pellicola depositata. Questa sensibilità richiede sistemi di controllo sofisticati e operatori qualificati, aumentando la complessità e il costo del processo.
-
Sfide con la deposizione multistrato:
- All'aumentare del numero di strati, i rendimenti di produzione nello sputtering DC possono diminuire. Ciò è dovuto all'effetto cumulativo di difetti e incoerenze in ogni strato, che possono compromettere la qualità complessiva della struttura multistrato. Questa limitazione è particolarmente problematica nelle applicazioni che richiedono elevata precisione e affidabilità, come nella produzione di dispositivi ottici e semiconduttori.
-
Limitazioni materiali:
- Lo sputtering DC non è adatto a tutti i tipi di materiali. Ad esempio, i materiali sensibili all'umidità o con proprietà di adesione deboli potrebbero non funzionare bene con lo sputtering DC. Questi materiali possono richiedere trattamenti aggiuntivi o metodi di deposizione alternativi per ottenere le proprietà della pellicola desiderate.
In sintesi, sebbene lo sputtering DC offra numerosi vantaggi, come semplicità ed efficacia in termini di costi, presenta anche notevoli svantaggi che possono influire sulla sua idoneità per determinate applicazioni. Comprendere queste limitazioni è essenziale per prendere decisioni informate nella selezione delle tecniche di sputtering per specifiche esigenze industriali.
Tabella riassuntiva:
Svantaggio | Descrizione |
---|---|
Impossibilità di spruzzare materiali non conduttivi | Lo sputtering DC è limitato ai materiali conduttivi; gli isolanti non possono essere spruzzati efficacemente. |
Tassi di deposizione più bassi | Lo sputtering DC offre velocità di deposizione più lente rispetto a tecniche avanzate come HIPIMS. |
Erosione e non uniformità del target | L'erosione del target non uniforme riduce la durata della vita e influisce sulla qualità della pellicola. |
Sensibilità ai parametri di processo | Richiede un controllo preciso della pressione del gas, della distanza e della tensione per ottenere risultati ottimali. |
Sfide con la deposizione multistrato | Le rese diminuiscono con l'aumento degli strati a causa di difetti e incoerenze. |
Limitazioni materiali | Non adatto per materiali sensibili all'umidità o debolmente adesivi. |
Hai bisogno di aiuto per scegliere il metodo di sputtering giusto per la tua applicazione? Contatta i nostri esperti oggi stesso !