I pezzi sinterizzati possono presentare vari difetti dovuti a condizioni di sinterizzazione non corrette o al comportamento del materiale durante il processo.I difetti più comuni includono sinterizzazione eccessiva, sinterizzazione insufficiente, bolle, sudorazione, deformazione e cedimento.Questi difetti derivano da fattori quali temperatura errata, tempo di sinterizzazione insufficiente o eccessivo, scarico di gas o sollecitazioni meccaniche.La comprensione di questi difetti è fondamentale per ottimizzare il processo di sinterizzazione e garantire che il prodotto finale soddisfi gli standard di prestazione e qualità.
Punti chiave spiegati:
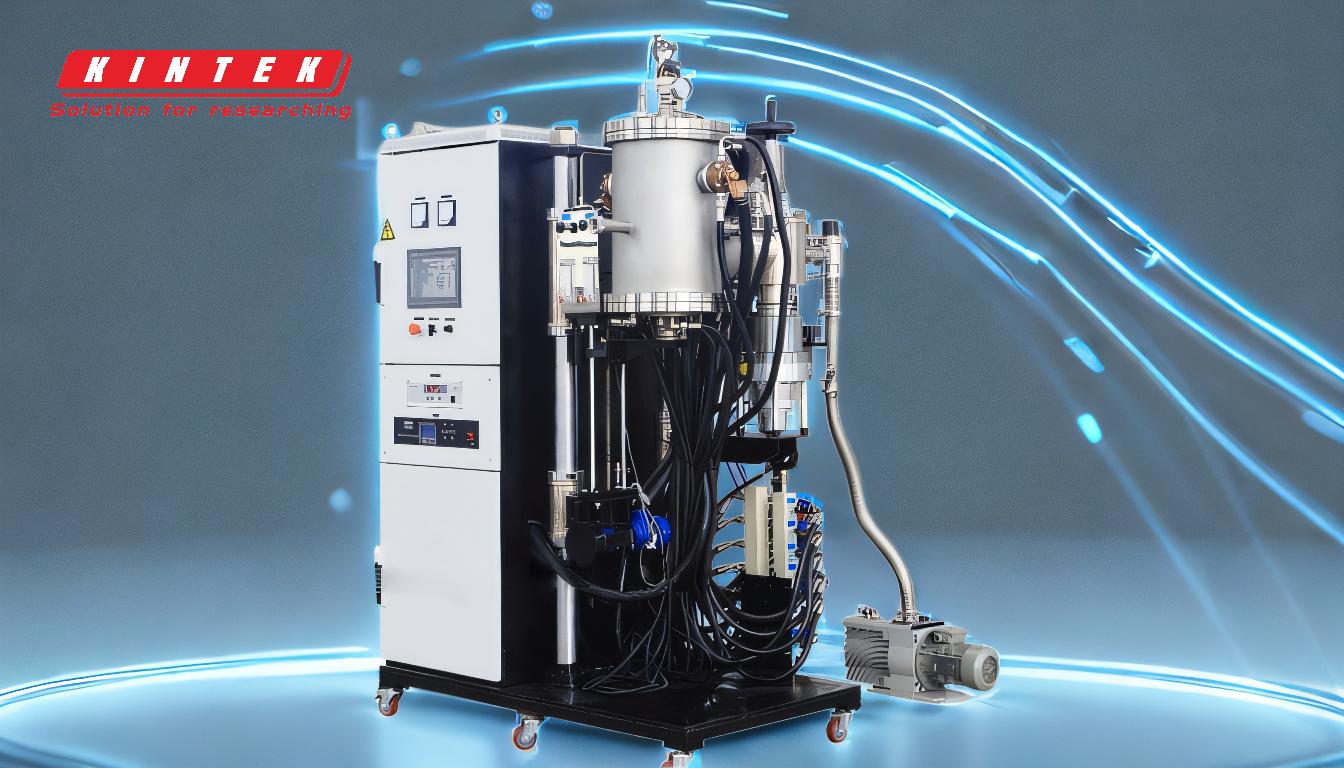
-
Sovrainteressamento:
- Causa:Si verifica quando la temperatura di sinterizzazione è troppo alta o il tempo di sinterizzazione è troppo lungo.
- Effetto:Porta al deterioramento del prodotto, come l'eccessiva crescita dei grani, la riduzione delle proprietà meccaniche o addirittura la fusione del materiale.
- Prevenzione:Controllare attentamente i parametri di temperatura e tempo per evitare di superare le condizioni ottimali di sinterizzazione.
-
Sottosinterizzazione:
- Causa:Risultati di una temperatura o di un tempo di sinterizzazione insufficienti.
- Effetto:Produce pezzi con densità inadeguata, scarsa resistenza meccanica e legame incompleto tra le particelle.
- Prevenzione:Assicurarsi che il processo di sinterizzazione raggiunga la temperatura e la durata necessarie per una corretta densificazione.
-
Blisteratura:
- Causa:Difetti superficiali causati da gas intrappolati che si scaricano durante la sinterizzazione.
- Effetto:Crea bolle o vesciche sulla superficie, compromettendo l'integrità e l'estetica del pezzo.
- Prevenzione:Utilizzare tecniche di degassificazione adeguate prima della sinterizzazione e ottimizzare la velocità di riscaldamento per consentire la fuoriuscita graduale dei gas.
-
Sudorazione:
- Causa:Si verifica quando una fase liquida fuoriesce durante il trattamento termico, spesso a causa di impurità o di condizioni di sinterizzazione non corrette.
- Effetto:Si creano superfici irregolari e una potenziale contaminazione del pezzo.
- Prevenzione:Utilizzare materiali di elevata purezza e controllare l'ambiente di sinterizzazione per ridurre al minimo la formazione di fase liquida.
-
Deformazione:
- Causa:Causato dalla gravità o dall'attrito durante la sinterizzazione, con conseguente ritiro o deformazione non uniforme.
- Effetto:Produce pezzi con forme distorte, che influiscono sulla precisione dimensionale e sulla funzionalità.
- Prevenzione:Utilizzare strutture di supporto adeguate durante la sinterizzazione e ottimizzare le velocità di riscaldamento e raffreddamento per ridurre al minimo le sollecitazioni.
-
Cedimento:
- Causa:Si verifica quando i pezzi si deformano sotto il loro stesso peso durante la sinterizzazione, soprattutto nei processi ad alta temperatura.
- Effetto:Porta a imprecisioni dimensionali e a debolezze strutturali.
- Prevenzione:Utilizzare supporti di sinterizzazione adeguati e ottimizzare il profilo di sinterizzazione per ridurre i rischi di deformazione.
-
Problemi di porosità:
- Causa:Influenzato dalla porosità iniziale del compatto verde, dalla temperatura di sinterizzazione e dalla durata.
- Effetto:Una porosità eccessiva può indebolire il pezzo, mentre una porosità insufficiente può ostacolare applicazioni specifiche.
- Prevenzione:Regolare i parametri di sinterizzazione e, se necessario, applicare pressione durante la sinterizzazione per ottenere la porosità desiderata.
Affrontando questi punti chiave, i produttori possono identificare e ridurre i difetti di sinterizzazione più comuni, garantendo pezzi sinterizzati di qualità superiore e processi produttivi più efficienti.
Tabella riassuntiva:
Difetto | Causa | Effetto | Prevenzione |
---|---|---|---|
Svergolamento | Temperatura o tempo eccessivi | Crescita dei grani, riduzione della resistenza, fusione | Controllo della temperatura e del tempo |
Sottosinterizzazione | Temperatura o tempo insufficienti | Bassa densità, scarsa resistenza, legame debole | Assicurare una temperatura e una durata adeguate |
Formazione di bolle | Scarico di gas intrappolati | Bolle superficiali, integrità compromessa | Degasare prima della sinterizzazione, ottimizzare il riscaldamento |
Sudorazione | Infiltrazione di fase liquida | Superfici irregolari, contaminazione | Utilizzare materiali di elevata purezza, controllare l'ambiente di sinterizzazione |
Deformazione | Gravità o attrito durante la sinterizzazione | Forme distorte, imprecisioni dimensionali | Utilizzare supporti, ottimizzare il riscaldamento/raffreddamento |
Cedimento | Deformazione sotto peso durante la sinterizzazione | Imprecisioni dimensionali, strutture deboli | Utilizzare supporti, ottimizzare il profilo di sinterizzazione |
Problemi di porosità | Porosità iniziale, temperatura, durata | Parti deboli o applicazioni ostacolate | Regolare i parametri, applicare la pressione se necessario |
Avete bisogno di aiuto per ottimizzare il vostro processo di sinterizzazione? Contattate oggi stesso i nostri esperti per soluzioni su misura!