I forni a induzione, in particolare il forno a induzione IGBT sono ampiamente utilizzati nell'industria metallurgica e manifatturiera grazie alla loro efficienza e precisione.Tuttavia, presentano diversi svantaggi che possono influire sulla loro idoneità per determinate applicazioni.Tra questi, le limitazioni nella capacità di raffinazione, i costi operativi più elevati, la minore efficienza energetica in alcuni progetti e le difficoltà legate alla manutenzione e alla sostituzione delle leghe.Di seguito analizziamo in dettaglio questi inconvenienti per fornire una comprensione completa degli svantaggi associati ai forni a induzione.
Punti chiave spiegati:
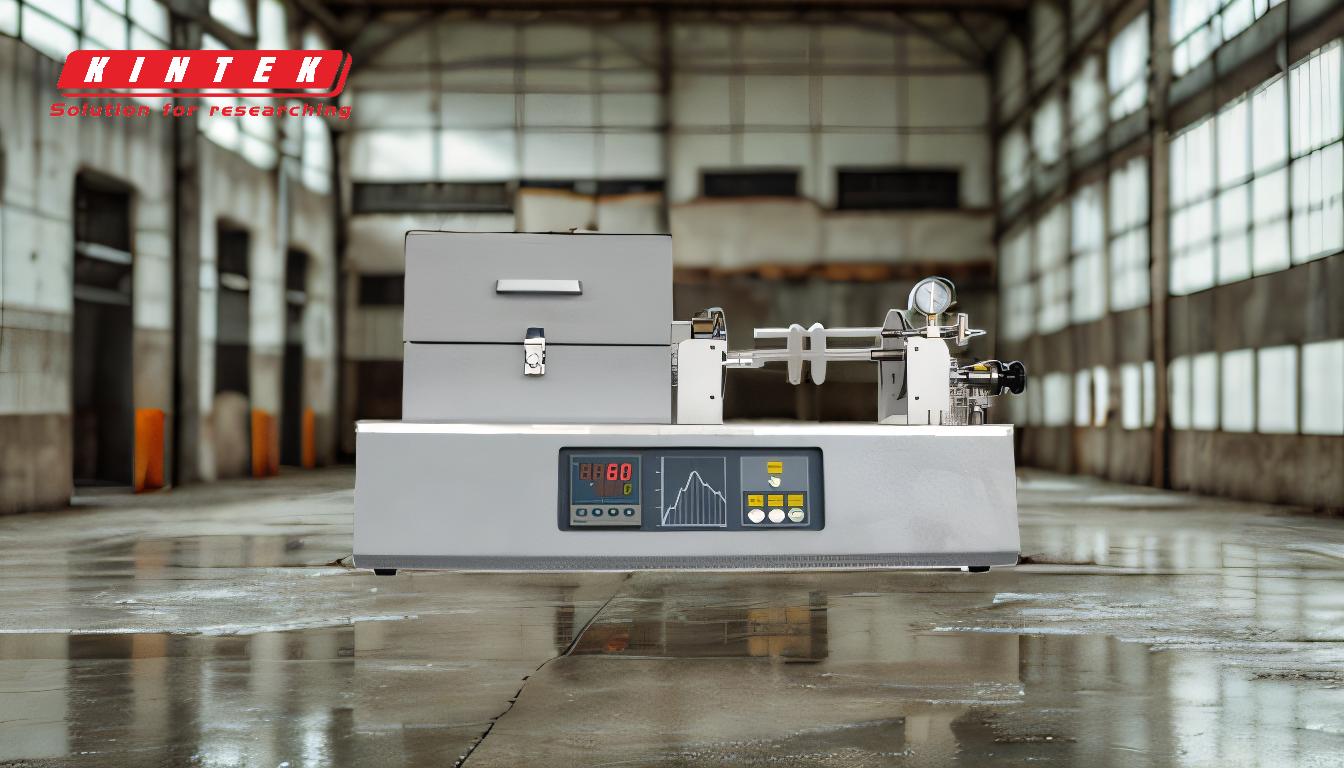
-
Mancanza di capacità di raffinazione
- I forni a induzione, compreso il forno a induzione IGBT non sono progettati per i processi di raffinazione.
- I materiali di carica devono essere privi di ossidi e avere una composizione nota per evitare problemi durante la fusione.
- Gli elementi di lega possono andare persi a causa dell'ossidazione, richiedendo una nuova aggiunta, con conseguente aumento dei costi dei materiali e della complessità operativa.
-
Minore efficienza energetica nei forni a induzione di tipo coreless
- I forni a induzione di tipo coreless, che operano in un'ampia gamma di frequenze (da 50 Hz a 10 kHz), hanno un'efficienza energetica di circa il 75%.
- Si tratta di un valore significativamente inferiore rispetto ai forni a induzione di tipo core, che possono raggiungere un'efficienza energetica del 98%.
- La frequente sostituzione delle leghe nei forni di tipo coreless può inoltre ridurre la durata del rivestimento refrattario, aumentando i costi di manutenzione.
-
Costi operativi elevati
- I forni a induzione si basano sull'elettricità, che può essere più costosa del gas o del petrolio, con conseguenti costi di esercizio più elevati.
- Il costo dell'elettricità può variare in modo significativo a seconda della posizione geografica, rendendolo un'opzione meno economica nelle regioni con prezzi energetici elevati.
-
Manutenzione e sfide operative
- I forni a induzione a nucleo richiedono una manutenzione continua del ciclo di metallo e raramente possono raffreddarsi, il che può aumentare la complessità operativa.
- Sebbene i forni elettrici siano generalmente robusti, eventuali problemi possono richiedere riparazioni professionali, che possono essere costose e richiedere molto tempo.
-
Limitazioni nella modifica delle leghe
- I forni a induzione di tipo core sono meno flessibili per quanto riguarda i cambi di lega, in quanto sono ottimizzati per operazioni ad alta produttività con pochi cambi di lega.
- I forni di tipo coreless, pur essendo più flessibili, devono comunque affrontare problemi di usura del rivestimento refrattario a causa dei frequenti cambi di lega.
-
Controllo della temperatura e perdita di materiale
- Sebbene i forni a induzione offrano un controllo preciso della temperatura, la mancanza di capacità di raffinazione può portare alla perdita di materiale, in particolare per gli elementi a rischio di ossidazione.
- Ciò può comportare costi aggiuntivi per il reinserimento degli elementi persi e per garantire che il prodotto finale soddisfi gli standard di qualità.
In sintesi, mentre i forni a induzione, compreso il forno a induzione forno a induzione IGBT I forni a induzione IGBT offrono numerosi vantaggi, come il riscaldamento rapido, l'alta efficienza e il controllo preciso della temperatura, ma presentano anche notevoli svantaggi.Tra questi, le limitazioni nella capacità di raffinazione, i costi operativi più elevati, la minore efficienza energetica in alcuni progetti e le difficoltà legate alla manutenzione e alla sostituzione delle leghe.La comprensione di questi svantaggi è fondamentale per prendere decisioni informate quando si sceglie un forno per applicazioni industriali specifiche.
Tabella riassuntiva:
Svantaggio | Dettagli |
---|---|
Mancanza di capacità di raffinazione | Non è progettato per la raffinazione; richiede materiali pre-puliti. |
Efficienza energetica inferiore | I forni di tipo coreless hanno un'efficienza di circa il 75% rispetto al 98% dei forni di tipo core. |
Costi operativi elevati | La dipendenza dall'elettricità comporta costi più elevati, soprattutto nelle aree ad alto consumo energetico. |
Problemi di manutenzione | Richiede una manutenzione continua; le riparazioni possono essere costose e richiedere molto tempo. |
Limitazioni nei cambi di lega | I forni a nocciolo sono meno flessibili; usura del refrattario nei progetti senza nocciolo. |
Perdita di materiale | Gli elementi a rischio di ossidazione possono andare persi, aumentando i costi dei materiali. |
Avete bisogno di aiuto per scegliere il forno giusto per le vostre esigenze? Contattate i nostri esperti oggi stesso!