Lo spessore del rivestimento di un forno a induzione è un fattore critico che dipende da diverse variabili, tra cui il tipo di forno, il materiale da fondere e la temperatura di esercizio.Sebbene i riferimenti forniti non specifichino gli spessori esatti del rivestimento, essi evidenziano l'importanza del rivestimento per proteggere il forno e garantirne il funzionamento efficiente.Il rivestimento deve resistere a temperature estreme, shock termici e reazioni chimiche con i metalli fusi.In genere, lo spessore è progettato per bilanciare l'isolamento termico, l'integrità strutturale e la capacità del forno.Per uno spessore preciso del rivestimento, si consiglia di consultare le specifiche del produttore o gli standard industriali.
Punti chiave spiegati:
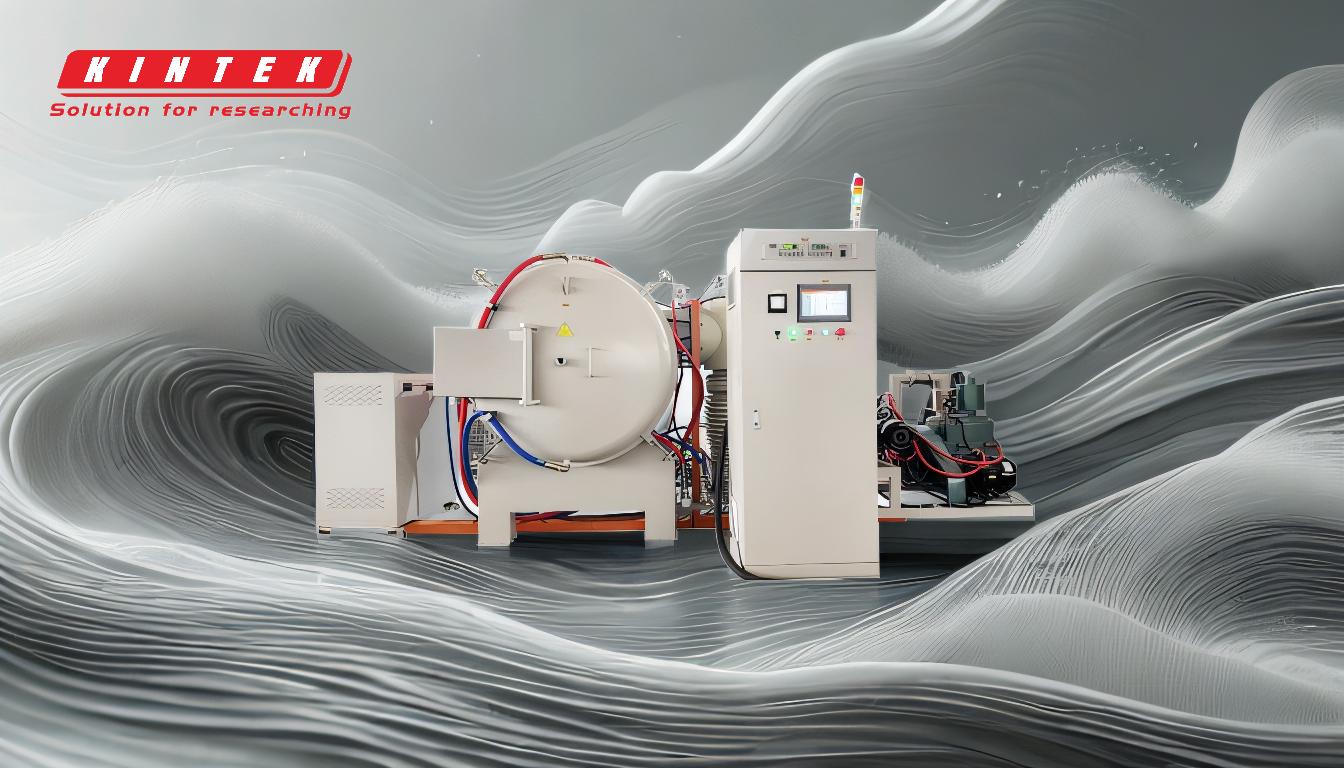
-
Scopo del forno a induzione Fodera:
- Il rivestimento di un forno a induzione funge da barriera tra il metallo fuso e i componenti strutturali del forno, come la bobina.Protegge il corpo del forno dai danni causati dalle alte temperature e dalle reazioni chimiche.
- Assicura che il metallo fuso sia contenuto in modo sicuro, evitando perdite o contaminazioni.
-
Fattori che influenzano lo spessore del rivestimento:
- Materiale da fondere:Metalli e leghe diversi richiedono rivestimenti con proprietà specifiche, come la resistenza alle reazioni chimiche o agli shock termici.Ad esempio, la fusione dell'acciaio può richiedere un rivestimento più spesso o più robusto rispetto alla fusione dell'alluminio.
- Temperatura di esercizio:I forni a induzione possono raggiungere temperature fino a 1800°C e oltre.Il rivestimento deve essere abbastanza spesso da fornire un isolamento adeguato e resistere a queste temperature estreme.
- Tipo e dimensioni del forno:I forni più grandi o quelli progettati per il funzionamento continuo possono richiedere rivestimenti più spessi per garantire la durata e la longevità.
- Sollecitazioni termiche e meccaniche:Il rivestimento deve resistere ai cicli termici e alle sollecitazioni meccaniche causate dall'azione di agitazione del metallo fuso.
-
Materiali di rivestimento tipici:
- I rivestimenti sono spesso realizzati con materiali refrattari come l'allumina, la silice o la magnesia, scelti per il loro elevato punto di fusione e la resistenza all'usura.
- La scelta del materiale e del suo spessore viene adattata all'applicazione specifica, garantendo prestazioni e sicurezza ottimali.
-
Considerazioni sulla progettazione:
- Lo spessore del rivestimento è un equilibrio tra l'isolamento sufficiente e il mantenimento della capacità interna del forno.
- I rivestimenti più spessi offrono un isolamento e una durata migliori, ma possono ridurre il volume di lavoro effettivo del forno.
- I rivestimenti più sottili possono aumentare la capacità ma richiedono una manutenzione o una sostituzione più frequente.
-
Implicazioni pratiche per gli acquirenti:
- Quando si sceglie un forno a induzione, l'acquirente deve considerare lo spessore e il materiale del rivestimento in relazione ai propri requisiti specifici di fusione.
- Consultare i produttori o gli esperti del settore può aiutare a determinare le specifiche ottimali del rivestimento per una determinata applicazione.
- L'ispezione e la manutenzione regolari del rivestimento sono essenziali per garantire un funzionamento sicuro ed efficiente del forno.
In conclusione, sebbene lo spessore esatto del rivestimento di un forno a induzione non sia specificato nei riferimenti, è chiaro che il design del rivestimento è adattato ai requisiti operativi del forno.Fattori come il tipo di materiale, la temperatura di esercizio e le dimensioni del forno giocano un ruolo importante nel determinare lo spessore appropriato del rivestimento.Per dettagli precisi, gli acquirenti devono fare riferimento alle linee guida del produttore o rivolgersi a un esperto.
Tabella riassuntiva:
Fattore | Impatto sullo spessore del rivestimento |
---|---|
Materiale da fondere | Rivestimenti più spessi per metalli come l'acciaio; più sottili per l'alluminio a causa della diversa resistenza chimica. |
Temperatura di esercizio | Temperature più elevate richiedono rivestimenti più spessi per un migliore isolamento e una maggiore durata. |
Tipo e dimensioni del forno | I forni più grandi o a funzionamento continuo necessitano di rivestimenti più spessi per garantire una maggiore durata. |
Sollecitazioni termiche/meccaniche | I rivestimenti devono resistere alle sollecitazioni dovute ai cicli termici e all'agitazione del metallo fuso. |
Materiali dei rivestimenti | L'allumina, la silice o la magnesia vengono scelte per gli elevati punti di fusione e la resistenza all'usura. |
Avete bisogno di aiuto per determinare il giusto spessore del rivestimento per il vostro forno a induzione? Contattate i nostri esperti oggi stesso per una consulenza su misura!