Introduzione ai metodi di rivestimento
Tipi di metodi di rivestimento
I metodi di rivestimento per la crescita di film di cristallo singolo comprendono uno spettro di tecniche, ciascuna con meccanismi e applicazioni particolari. I metodi principali includonoDeposizione chimica da vapore (CVD),Deposizione fisica da vapore (PVD)eEpitassia. Questi metodi non solo sono diversi nei loro principi operativi, ma offrono anche una serie di sottotipi e di tecniche specifiche, adatte a varie esigenze scientifiche e industriali.
-
La deposizione chimica da vapore (CVD) prevede la reazione chimica di gas precursori per depositare un film solido su un substrato. Questo metodo comprende sottotipi comeCVD a bassa pressione (LPCVD),CVD a pressione atmosferica (APCVD),CVD potenziata al plasma (PECVD)e altro ancora. Ogni sottotipo è ottimizzato per condizioni specifiche, consentendo un controllo preciso delle proprietà del film.
-
La deposizione fisica da vapore (PVD)si basa invece sull'evaporazione fisica o sullo sputtering del materiale per depositarlo su un substrato. I sottotipi di PVD includonoEvaporazione a fascio di elettroni,sputtering di magnetroneDeposizione laser pulsata (PLD). Queste tecniche sono particolarmente utili per creare film sottili e uniformi con elevata purezza.
-
Epitassi comeEpitassi a fascio molecolare (MBE),Epitassia in fase di vapore (VPE)eEpitassia in fase liquida (LPE)si concentrano sulla crescita di un film di cristallo singolo su un substrato di cristallo singolo. Questi metodi sono fondamentali per ottenere strutture monocristalline di alta qualità, essenziali per le applicazioni avanzate dei semiconduttori.
Ciascuno di questi metodi presenta una serie di vantaggi e limitazioni che li rendono adatti a diverse applicazioni. Per esempio, mentre la CVD e la PVD sono versatili e ampiamente utilizzate, l'epitassia offre un controllo superiore sulla struttura e sull'orientamento dei cristalli, rendendola ideale per applicazioni specializzate nell'elettronica e nella fotonica.
Deposizione chimica da vapore (CVD)
Sottotipi di CVD
La deposizione chimica da vapore (CVD) comprende una serie di tecniche diverse, ognuna adattata a specifiche applicazioni e proprietà dei materiali. I metodi principali includono la deposizione di vapore chimico a bassa pressione (LPCVD), la deposizione di vapore chimico a pressione atmosferica (APCVD), la deposizione di vapore chimico assistita da substrato (SACVD), la deposizione di vapore chimico potenziata dal plasma (PECVD), la deposizione di vapore chimico al plasma ad alta densità (HDPCVD), la deposizione di vapore chimico condizionata dal flusso (FCVD) e la deposizione di vapore chimico metallo-organico (MOCVD).
Queste tecniche si basano fondamentalmente sulla reazione chimica dei gas precursori per depositare un film solido su un substrato. La scelta del metodo dipende spesso da fattori quali la velocità di deposizione, l'uniformità del film e le proprietà del materiale desiderato. Ad esempio, l'LPCVD è rinomato per i suoi film uniformi e di alta qualità, che lo rendono ideale per la produzione di semiconduttori, mentre il PECVD, sfruttando il plasma, può depositare film a temperature più basse, il che è fondamentale per i substrati sensibili alla temperatura.
Metodo CVD | Caratteristiche principali | Applicazioni tipiche |
---|---|---|
LPCVD | Alta uniformità, bassa pressione | Dispositivi a semiconduttore |
APCVD | Funziona a pressione atmosferica | Rivestimento di substrati di grandi dimensioni |
SACVD | Potenziato dalle proprietà del substrato | Strutture avanzate di semiconduttori |
PECVD | Temperatura di deposizione più bassa, utilizza il plasma | Materiali sensibili alla temperatura |
HDPCVD | Alta densità di plasma, alta velocità di deposizione | Rivestimenti ad alte prestazioni |
FCVD | Controllo del flusso per una deposizione precisa | Rivestimenti di precisione |
MOCVD | Utilizza precursori metallo-organici | Dispositivi optoelettronici |
Ogni sottotipo di CVD offre vantaggi e sfide uniche, che li rendono adatti a diverse fasi di sviluppo e produzione dei materiali. La comprensione di queste sfumature è essenziale per ottimizzare la crescita di film a cristallo singolo e altri materiali avanzati.
Deposizione fisica da vapore (PVD)
Sottotipi di PVD
La deposizione fisica da vapore (PVD) comprende una serie di tecniche, ciascuna con meccanismi e applicazioni particolari.L'evaporazione a fascio di elettroni è uno di questi metodi, in cui un fascio di elettroni ad alta energia viene diretto verso un materiale di partenza, provocandone l'evaporazione e il successivo deposito su un substrato. Questa tecnica è particolarmente utile per i materiali ad alto punto di fusione e viene spesso impiegata nella produzione di rivestimenti ottici.
Un altro sottotipo importante è ilsputtering magnetronicoche prevede l'uso di un campo magnetico per aumentare la ionizzazione degli atomi bersaglio. Questo metodo è altamente efficiente ed è ampiamente utilizzato nell'industria dei semiconduttori per depositare film sottili con un controllo preciso della composizione e dello spessore.
La deposizione laser pulsata (PLD) si distingue per la sua capacità di depositare materiali complessi di ossido con elevata precisione. Nella PLD, un impulso laser ad alta energia viene diretto verso un materiale target, creando un pennacchio di plasma che si deposita sul substrato. Questa tecnica è preferita per la sua capacità di riprodurre la composizione del materiale target con impurità minime.
Questi metodi, insieme ad altri comela deposizione con fascio di ioni eevaporazione termicacondividono tutti l'obiettivo comune di trasferire fisicamente il materiale da una sorgente a un substrato per formare un film sottile. La scelta del metodo dipende spesso dai requisiti specifici dell'applicazione, come l'uniformità del film, l'adesione e le proprietà desiderate del materiale.
Epitassia
Sottotipi di epitassia
L'epitassia comprende una serie di tecniche specializzate progettate per far crescere film di cristallo singolo su substrati di cristallo singolo. I metodi principali includono l'epitassia a fascio molecolare (MBE), l'epitassia in fase di vapore (VPE), l'epitassia in fase liquida (LPE) e l'epitassia in fase solida (SPE). Ognuno di questi sottotipi ha caratteristiche e applicazioni uniche, che li rendono adatti a materiali e condizioni di crescita diversi.
L'epitassia a fascio molecolare (MBE) è una tecnica sofisticata che prevede la deposizione di materiale su un substrato riscaldato in un ambiente ad alto vuoto. Questo metodo consente un controllo preciso della composizione e dello spessore degli strati depositati, rendendolo ideale per la creazione di strutture complesse come pozzi quantici e superlattici.
L'epitassi in fase di vapore (VPE), invece, utilizza reazioni chimiche in fase di vapore per depositare il materiale desiderato sul substrato. Questa tecnica è particolarmente utile per la crescita dei semiconduttori e può essere eseguita in varie condizioni, tra cui la pressione atmosferica e la pressione ridotta.
L'epitassi in fase liquida (LPE) prevede la crescita di cristalli da una soluzione satura, in cui il substrato è immerso in una colata contenente il materiale desiderato. Questo metodo è spesso utilizzato per produrre film di cristalli singoli di alta qualità di materiali come l'arseniuro di gallio e il fosfuro di indio.
L'epitassia in fase solida (SPE) è un metodo unico in cui la crescita avviene attraverso la diffusione allo stato solido degli atomi nel substrato. Questa tecnica è comunemente utilizzata per i processi di ricristallizzazione ed è particolarmente efficace per i materiali difficili da far crescere con altri metodi epitassiali.
Ciascuna di queste tecniche epitassiali svolge un ruolo cruciale nella fabbricazione di dispositivi elettronici e optoelettronici avanzati, contribuendo al continuo progresso della tecnologia dei semiconduttori.
Meccanismi di formazione del film
Modalità di crescita 2D strato per strato
Nella modalità di crescita 2D strato per strato, il film si sviluppa in modo altamente strutturato e ordinato, con ogni strato che viene meticolosamente completato prima che lo strato successivo inizi la sua formazione. Questo processo metodico garantisce che la superficie del film rimanga eccezionalmente piatta, una caratteristica particolarmente vantaggiosa per la coltivazione di strutture a cristallo singolo.
La natura meticolosa di questa modalità di crescita è ulteriormente evidenziata dal processo di deposizione controllata, in cui ogni strato atomico aderisce con precisione al precedente, creando un film uniforme e senza soluzione di continuità. Questa precisione è fondamentale per mantenere l'integrità strutturale e la qualità cristallina del film, rendendolo una scelta ideale per le applicazioni che richiedono materiali a cristallo singolo di elevata purezza.
Inoltre, la planarità ottenuta con questo metodo non solo migliora le proprietà ottiche ed elettroniche del film, ma facilita anche l'integrazione con altri componenti a semiconduttore. L'ambiente controllato e le precise tecniche di deposizione impiegate in questa modalità consentono la fabbricazione di film con difetti minimi e prestazioni ottimali, soddisfacendo i severi requisiti delle tecnologie avanzate dei semiconduttori.
Crescita a isola 3D (Volmer-Weber)
Nella modalità di crescita a isole 3D, nota anche come meccanismo Volmer-Weber, il film si sviluppa in cluster o isole tridimensionali localizzate. A differenza della modalità di crescita 2D Layer-by-Layer, in cui il film si espande uniformemente sul substrato, il processo Volmer-Weber produce regioni di crescita discrete che alla fine si uniscono per coprire l'intera superficie.
Questo modello di crescita a isole è dovuto alla debole adesione tra il materiale depositato e il substrato. La mancanza di forti forze di legame permette al materiale di formare isole distinte piuttosto che diffondersi uniformemente. Di conseguenza, il film risultante presenta un'elevata energia libera superficiale, indicativa di una superficie instabile e reattiva.
La debole interazione tra il film e il substrato può portare a diverse sfide. Ad esempio, il film può presentare una scarsa adesione meccanica, rendendolo più suscettibile alla delaminazione o alla fessurazione. Inoltre, l'elevata energia libera superficiale può contribuire ad aumentare la reattività, che potrebbe essere indesiderata in alcune applicazioni in cui la stabilità e la durata sono fondamentali.
A titolo esemplificativo, si consideri un processo di deposizione in cui il materiale forma isole anziché uno strato continuo. Questo può essere visualizzato come piccoli cumuli di materiale sparsi sulla superficie, ogni cumulo rappresenta un evento di crescita separato. Man mano che viene depositato altro materiale, questi cumuli crescono e alla fine si fondono, formando un film continuo ma strutturalmente debole.
Caratteristica | Descrizione |
---|---|
Modello di crescita | Agglomerati 3D a isole |
Adesione | Debole interazione con il substrato |
Energia di superficie | Alta energia libera di superficie |
Sfide | Scarsa adesione meccanica, suscettibilità alla delaminazione |
In sintesi, la modalità di crescita Volmer-Weber rappresenta una sfida unica nella formazione dei film, caratterizzata dalla crescita di isole localizzate e da un'elevata energia libera superficiale. Sebbene questa modalità possa coprire l'intero substrato, l'integrità strutturale e la stabilità del film risultante sono compromesse a causa della debole interazione con il substrato.
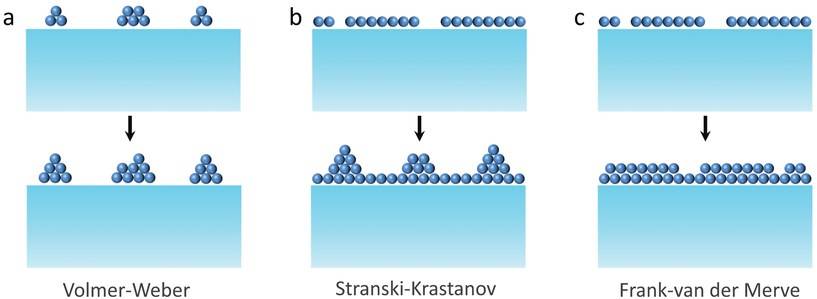
Crescita in modalità mista
La crescita in modalità mista rappresenta una fase di transizione dinamica nella formazione di film di cristallo singolo, in cui le fasi iniziali di crescita strato per strato lasciano gradualmente il posto alla formazione di isole. Questo meccanismo di crescita ibrido è guidato principalmente dall'accumulo di stress all'interno del film, che interrompe la progressione ordinata della deposizione monostrato.
Fasi chiave della crescita in modalità mista
-
Crescita iniziale strato per strato:
- Durante la fase iniziale, il film cresce in modo controllato, strato per strato, in modo simile alla modalità di crescita 2D. Questa fase è caratterizzata dalla copertura completa di ogni strato atomico prima che inizi il successivo, garantendo una superficie liscia e uniforme.
- Tecniche come la Molecular Beam Epitaxy (MBE) e la Vapor Phase Epitaxy (VPE) sono particolarmente adatte a facilitare questa crescita iniziale strato per strato, grazie al loro preciso controllo sul processo di deposizione.
-
Transizione alla formazione di isole:
- Man mano che il film continua a crescere, iniziano ad accumularsi tensioni interne, dovute principalmente alle discrepanze nelle costanti reticolari tra il film e il substrato. Queste sollecitazioni possono derivare da differenze di espansione termica, interazioni chimiche o sforzi meccanici.
- Lo stress accumulato porta alla fine all'interruzione della crescita continua strato per strato, causando la transizione del film in una modalità di crescita a isola 3D. Questa transizione è spesso indicata come modalità di crescita Volmer-Weber, in cui regioni localizzate del film crescono indipendentemente come isole.
Caratteristiche strutturali
- Struttura mista: Il film risultante presenta una struttura complessa che combina elementi di entrambe le modalità di crescita 2D e 3D. Gli strati inferiori mantengono la struttura ordinata e piatta della crescita strato per strato, mentre gli strati superiori sono caratterizzati dalla presenza di isole.
- Distribuzione delle sollecitazioni: La struttura a modalità mista aiuta a ridistribuire le sollecitazioni accumulate, prevenendo il cedimento catastrofico del film. Le isole agiscono come punti di scarico delle sollecitazioni, consentendo al film di adattarsi ai disallineamenti senza fratturarsi.
Implicazioni per le proprietà del film
- Ruvidità della superficie: La transizione dalla crescita 2D a quella 3D introduce una rugosità superficiale che può influire sulle proprietà ottiche, elettriche e meccaniche del film.
- Adesione e coesione: La struttura mista può portare a variazioni nell'adesione e nella coesione tra il film e il substrato, con un impatto sulla stabilità e sulle prestazioni complessive del rivestimento.
In sintesi, la crescita in modalità mista è una fase critica nella formazione di film a cristallo singolo, in cui l'interazione tra la deposizione strato per strato e la formazione di isole dà luogo a una morfologia strutturale unica che bilancia le sollecitazioni e promuove l'integrità del film.
Conclusione
Metodi preferiti per la crescita di cristalli singoli
I metodi di epitassia, come l'epitassia a fascio molecolare (MBE), l'epitassia in fase di vapore (VPE), l'epitassia in fase liquida (LPE) e l'epitassia in fase solida (SPE), sono particolarmente favoriti per la produzione di film di cristallo singolo grazie alla loro particolare modalità di crescita 2D strato per strato. Questo approccio metodico garantisce che ogni strato atomico sia depositato e allineato meticolosamente, favorendo la formazione di una struttura cristallina altamente ordinata e continua.
Al contrario, le tecniche di deposizione chimica da vapore (CVD) e di deposizione fisica da vapore (PVD) spesso producono film policristallini o amorfi, a meno che non vengano mantenute meticolosamente condizioni di processo rigorose. La variabilità di questi metodi deriva dai loro meccanismi di deposizione intrinseci, che possono portare alla formazione di orientamenti cristallini multipli o di strutture non cristalline se non sono attentamente controllati.
Metodo | Modalità di crescita | Risultato tipico |
---|---|---|
Epitassia | 2D Strato per strato | Film a cristallo singolo |
CVD | Variabile (2D/3D) | Film policristallini o amorfi |
PVD | Variabile (2D/3D) | Film policristallini o amorfi |
La tabella precedente evidenzia le principali differenze tra le modalità di crescita e i risultati tipici di ciascun metodo, sottolineando il ruolo critico della modalità di crescita nel determinare la qualità cristallina dei film depositati.
CONTATTATECI PER UNA CONSULENZA GRATUITA
I prodotti e i servizi di KINTEK LAB SOLUTION sono stati riconosciuti da clienti di tutto il mondo. Il nostro personale sarà lieto di assistervi per qualsiasi richiesta. Contattateci per una consulenza gratuita e parlate con uno specialista del prodotto per trovare la soluzione più adatta alle vostre esigenze applicative!