La sinterizzazione è un processo produttivo versatile utilizzato per creare componenti da un'ampia gamma di materiali, tra cui metalli, ceramiche, polimeri e compositi.Il processo prevede la compattazione e il riscaldamento di materiali in polvere al di sotto del loro punto di fusione per formare strutture solide con proprietà migliorate.I materiali comunemente utilizzati includono acciai al ferro e al carbonio, acciaio inossidabile, alluminio, nichel, rame, leghe di titanio, molibdeno, tungsteno e ceramica.Questi materiali vengono scelti in base alle loro proprietà specifiche e all'applicazione desiderata, come la resistenza alle alte temperature, la forza o la durata.La sinterizzazione è particolarmente vantaggiosa per i materiali con punti di fusione elevati ed è ampiamente utilizzata nella metallurgia delle polveri, nella fabbricazione additiva e nella produzione di componenti come ingranaggi, cuscinetti e filtri.
Punti chiave spiegati:
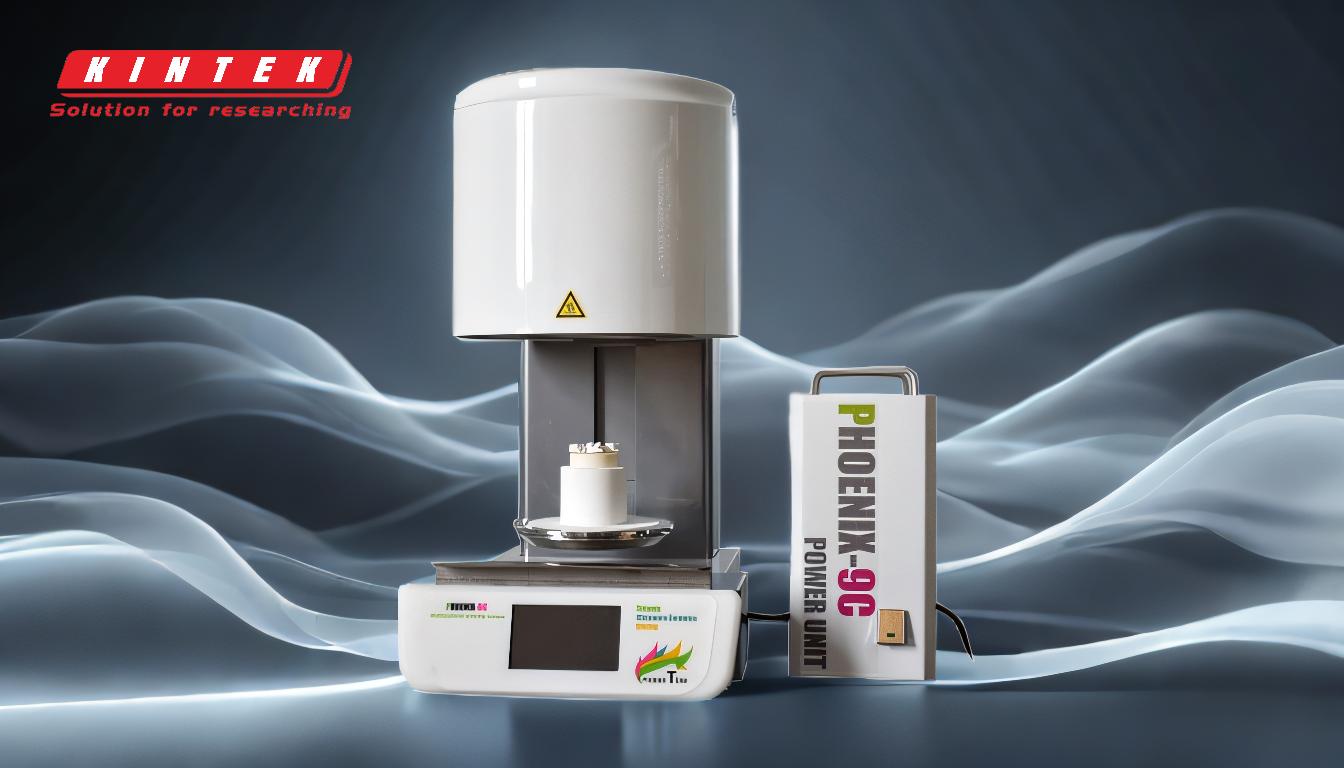
-
Materiali comunemente utilizzati nella sinterizzazione:
- Ferro e acciai al carbonio:Ampiamente utilizzati nella sinterizzazione per la loro resistenza e convenienza.Spesso vengono lavorati per migliorare le proprietà meccaniche, come la durezza e la resistenza all'usura.
- Acciaio inossidabile:Noto per la sua resistenza alla corrosione e la sua durata, l'acciaio inossidabile è una scelta popolare per i componenti sinterizzati in settori come quello automobilistico e aerospaziale.
- Alluminio:Leggero e resistente alla corrosione, l'alluminio è utilizzato nella sinterizzazione per applicazioni che richiedono un peso ridotto e un'elevata conducibilità termica.
- Leghe di nichel e rame:Questi materiali sono apprezzati per la loro conducibilità elettrica, resistenza termica e forza, che li rendono adatti ad applicazioni elettriche e ad alta temperatura.
- Leghe di titanio:Utilizzati nella sinterizzazione per l'elevato rapporto resistenza/peso e la biocompatibilità, spesso in applicazioni mediche e aerospaziali.
- Molibdeno e tungsteno:Questi metalli ad alto punto di fusione vengono sinterizzati per applicazioni che richiedono una resistenza a temperature estreme, come i componenti di forni e parti aerospaziali.
- Ceramica:Le ceramiche sinterizzate sono utilizzate per la loro stabilità alle alte temperature, la resistenza all'usura e le proprietà di isolamento elettrico, che le rendono ideali per componenti come cuscinetti e isolatori.
- Polimeri:I polimeri sinterizzati sono utilizzati nella prototipazione rapida e nella produzione di filtri grazie alla loro versatilità e facilità di lavorazione.
-
Applicazioni dei materiali sinterizzati:
- Metallurgia delle polveri:La sinterizzazione è un processo chiave della metallurgia delle polveri, in cui le polveri metalliche vengono compattate e sinterizzate per produrre piccoli componenti come ingranaggi, pulegge e cuscinetti.
- Produzione additiva:Le tecnologie di sinterizzazione avanzate, come la sinterizzazione laser selettiva (SLS), sono utilizzate nella stampa 3D per creare componenti complessi da polveri di metallo e polimeri.
- Componenti ad alta temperatura:Materiali come il molibdeno, il tungsteno e la ceramica vengono sinterizzati per essere utilizzati in ambienti ad alta temperatura, come parti di forni e componenti aerospaziali.
- Filtri e prototipi:I polimeri e i metalli sinterizzati vengono utilizzati per produrre filtri e prototipi, sfruttando la capacità del processo di creare strutture porose e intricate.
-
Vantaggi della sinterizzazione:
- Proprietà del materiale migliorate:La sinterizzazione migliora le proprietà meccaniche, termiche ed elettriche dei materiali, rendendoli adatti ad applicazioni complesse.
- Costo-efficacia:Il processo consente di produrre forme complesse con uno scarto minimo di materiale, riducendo i costi.
- Versatilità:La sinterizzazione può essere applicata a un'ampia gamma di materiali, tra cui metalli, ceramiche e polimeri, consentendo la produzione di diversi componenti.
- Sostenibilità:La sinterizzazione utilizza spesso materiali riciclati e produce meno rifiuti rispetto ai metodi di produzione tradizionali.
-
Progressi tecnologici nella sinterizzazione:
- Tecniche di sinterizzazione migliorate:I progressi nelle tecnologie di sinterizzazione, come la sinterizzazione al plasma di scintilla (SPS) e la sinterizzazione a microonde, hanno migliorato l'efficienza e la precisione del processo.
- Integrazione della produzione additiva:La sinterizzazione è sempre più integrata con le tecniche di produzione additiva, consentendo la produzione di componenti complessi e ad alte prestazioni.
- Raffinamento dei materiali:La ricerca e lo sviluppo continui hanno portato al perfezionamento dei materiali sinterizzati, migliorandone le proprietà e ampliandone le applicazioni.
Grazie alla comprensione dei materiali e dei processi coinvolti nella sinterizzazione, i produttori possono scegliere i materiali e le tecniche appropriate per soddisfare i requisiti di applicazioni specifiche, garantendo prestazioni ottimali e un buon rapporto costo-efficacia.
Tabella riassuntiva:
Materiale | Proprietà chiave | Applicazioni comuni |
---|---|---|
Ferro e acciai al carbonio | Forza, convenienza, resistenza all'usura | Ingranaggi, cuscinetti, componenti automobilistici |
Acciaio inossidabile | Resistenza alla corrosione, durata | Aerospaziale, dispositivi medici |
Alluminio | Leggerezza, conducibilità termica | Scambiatori di calore, componenti leggeri |
Leghe di nichel e rame | Conducibilità elettrica, resistenza termica | Componenti elettrici, parti ad alta temperatura |
Leghe di titanio | Elevato rapporto resistenza/peso, biocompatibilità | Impianti medici, componenti aerospaziali |
Molibdeno e tungsteno | Resistenza alle temperature estreme | Parti di forni, componenti aerospaziali |
Ceramica | Stabilità alle alte temperature, resistenza all'usura | Cuscinetti, isolanti |
Polimeri | Versatilità, facilità di lavorazione | Filtri, prototipazione rapida |
Avete bisogno di aiuto per selezionare i materiali giusti per il vostro processo di sinterizzazione? Contattate i nostri esperti oggi stesso !