La temperatura per la sinterizzazione della ceramica, in particolare nelle applicazioni dentali, varia tipicamente tra 1200°C e 1400°C. Questa temperatura elevata è essenziale per facilitare la diffusione atomica attraverso i confini delle particelle, consentendo alle particelle di fondersi insieme senza raggiungere il punto di fusione del materiale. Il processo prevede diverse fasi, tra cui la preparazione della polvere, il riscaldamento, la fusione delle particelle e la solidificazione. Per materiali come la zirconia, la temperatura di sinterizzazione spesso supera i 1100°C-1200°C, con alcuni forni che operano più vicino ai 1500°C per ottenere la massima densità. La temperatura precisa dipende dalle proprietà del materiale e dal risultato desiderato, garantendo densità e integrità strutturale ottimali.
Punti chiave spiegati:
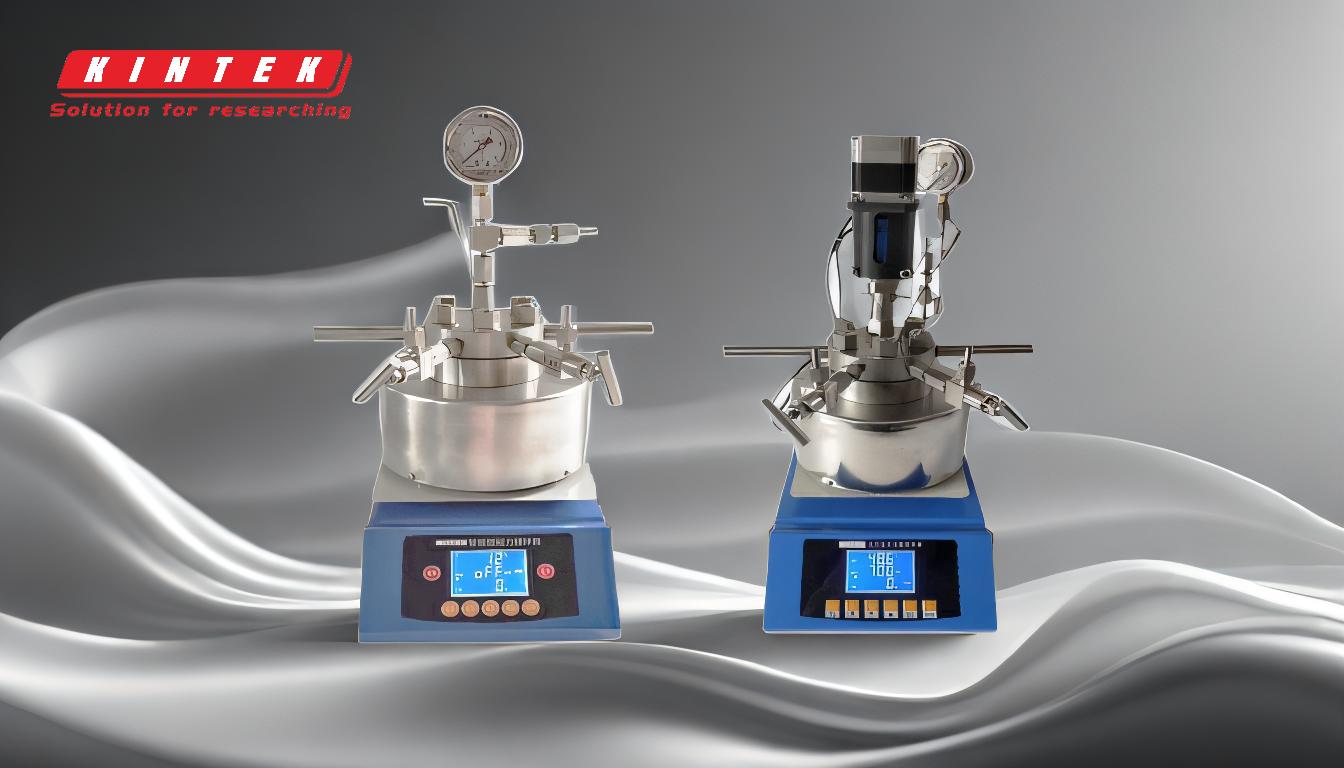
-
Intervallo di temperatura per la ceramica di sinterizzazione:
- Il processo di sinterizzazione richiede tipicamente temperature comprese tra 1200°C e 1400°C per la ceramica, soprattutto nelle applicazioni dentali.
- Questo intervallo è fondamentale perché consente agli atomi di diffondersi e alle particelle di fondersi senza liquefare il materiale.
- Per la zirconia, la trasformazione dallo stato cristallino monoclino a quello politetragonale avviene intorno da 1100°C a 1200°C , ma temperature più elevate (fino a 1500°C ) sono spesso utilizzati per ottenere una densità massima quasi teorica.
-
Ruolo della temperatura nella sinterizzazione:
- La temperatura è un fattore chiave nella sinterizzazione poiché deve essere sufficientemente elevata da consentire la diffusione atomica e il legame delle particelle, ma al di sotto del punto di fusione del materiale per prevenire la liquefazione.
- Il forno di sinterizzazione deve mantenere un controllo preciso della temperatura per garantire che il materiale raggiunga la densità e le proprietà strutturali desiderate.
-
Fasi del processo di sinterizzazione:
- Preparazione della polvere: La materia prima viene preparata in una forma compatta utilizzando metodi come la saldatura a freddo, la stampa 3D o la pressatura.
- Riscaldamento e consolidamento: Il compatto viene riscaldato appena al di sotto del suo punto di fusione, attivando le microstrutture cristalline e avviando il legame delle particelle.
- Fusione di particelle: Le particelle si densificano e si fondono, un processo che può essere accelerato utilizzando tecniche come la sinterizzazione in fase liquida (LPS).
- Solidificazione: Il materiale si raffredda e si solidifica in una struttura unificata e densa.
-
Considerazioni specifiche sui materiali:
- Per la zirconia, la temperatura di sinterizzazione è fondamentale per ottenere la trasformazione cristallina e la densità desiderate.
- I forni di sinterizzazione spesso funzionano a temperature più elevate (ad esempio, 1500°C) per garantire la massima densità, che può raggiungere fino a 99% del massimo teorico .
-
Importanza del controllo preciso della temperatura:
- I forni di sinterizzazione devono mantenere la temperatura al di sotto del punto di fusione del materiale per evitare la liquefazione garantendo al contempo un calore sufficiente per la fusione delle particelle.
- Questa precisione è fondamentale per ottenere le proprietà meccaniche e strutturali desiderate nel prodotto finale.
-
Applicazioni e implicazioni:
- Nelle applicazioni dentali, la sinterizzazione viene utilizzata per creare restauri in ceramica ad alta resistenza come corone e ponti.
- La capacità di controllare la temperatura di sinterizzazione influisce direttamente sulla qualità, sulla durata e sulle prestazioni del prodotto finale.
Per maggiori informazioni sui forni di sinterizzazione potete fare riferimento a questa guida dettagliata: forno di sinterizzazione .
Tabella riassuntiva:
Aspetto | Dettagli |
---|---|
Intervallo di temperatura | 1200°C–1400°C (fino a 1500°C per zirconia) |
Ruolo chiave della temperatura | Consente la diffusione atomica e il legame delle particelle senza liquefazione |
Fasi della sinterizzazione | Preparazione delle polveri, riscaldamento, fusione delle particelle, solidificazione |
Fattori specifici del materiale | La zirconia richiede 1100°C–1200°C per la trasformazione cristallina |
Importanza della precisione | Garantisce densità, integrità strutturale e proprietà meccaniche ottimali |
Applicazioni | Restauri dentali (corone, ponti) e componenti in ceramica ad alta resistenza |
Hai bisogno di soluzioni di sinterizzazione precise per la tua ceramica? Contatta i nostri esperti oggi stesso per saperne di più!