La temperatura di un forno per porcellana La temperatura del forno è generalmente compresa tra 600°C e 1200°C, a seconda dell'applicazione specifica e del tipo di porcellana da lavorare.Questo intervallo di temperatura è significativamente inferiore a quello dei forni di grafitizzazione, che operano a temperature molto più elevate (da 2500°C a 3000°C) a causa della necessità di trasformare i materiali carboniosi in grafite.I forni per porcellana sono progettati per sinterizzare o fondere i materiali di porcellana, che richiedono un controllo preciso della temperatura per ottenere le proprietà desiderate, quali resistenza, densità e finitura estetica.
Punti chiave spiegati:
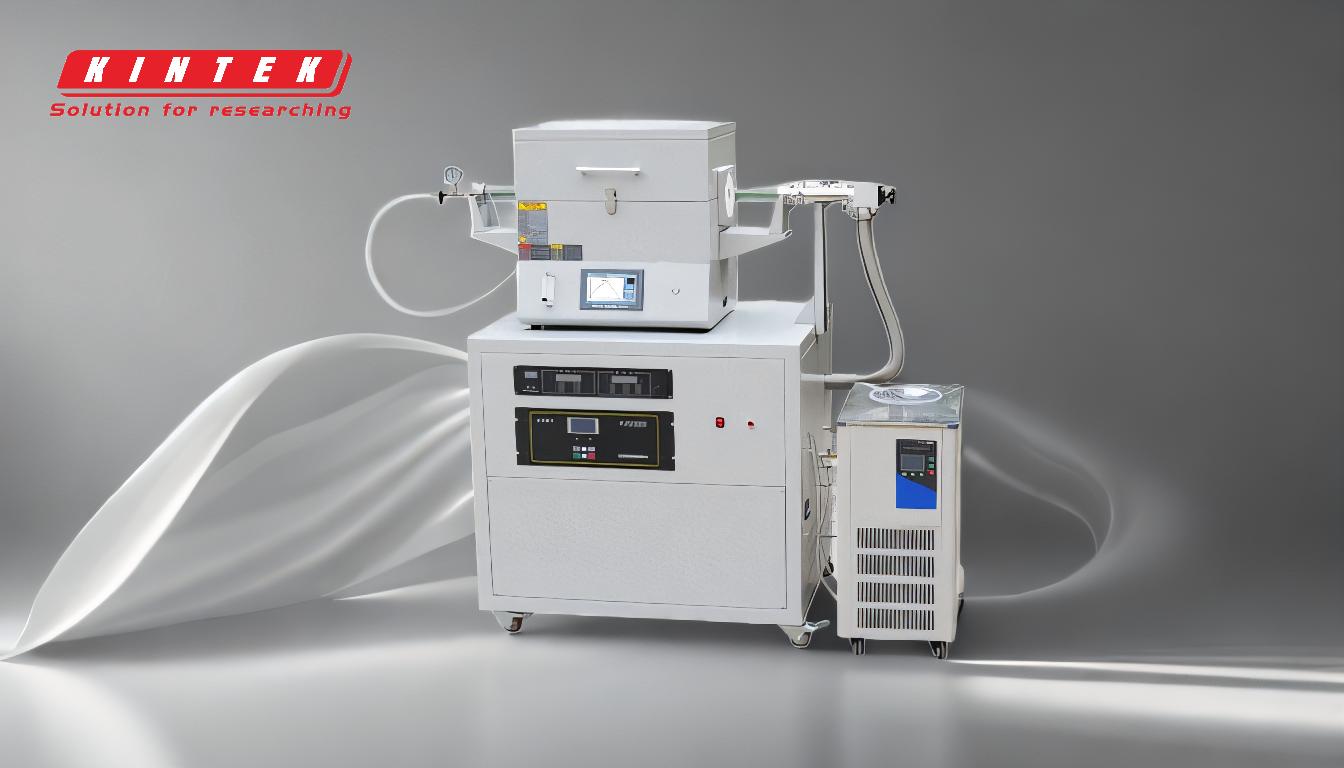
-
Intervallo di temperatura dei forni per porcellana:
- I forni per porcellana operano generalmente tra 600°C a 1200°C .Questa gamma è adatta alla sinterizzazione e alla fusione di materiali in porcellana, garantendo un'adeguata adesione e densificazione senza causare danni termici.
- La temperatura esatta dipende dal tipo di porcellana e dall'applicazione specifica, come la ceramica dentale, la porcellana artistica o i componenti industriali.
-
Confronto con i forni di grafitizzazione:
- I forni di grafitizzazione operano a temperature molto più elevate ( 2500°C - 3000°C ) perché sono progettati per convertire i materiali carboniosi in grafite.Questo processo richiede un calore estremo e un'atmosfera inerte per evitare l'ossidazione.
- I forni per porcellana, invece, operano a temperature più basse perché i materiali in porcellana non richiedono un calore così estremo per la sinterizzazione o la fusione.
-
Importanza del controllo della temperatura:
- Il controllo preciso della temperatura è fondamentale nei forni per porcellana per garantire che il materiale raggiunga le proprietà desiderate, come la resistenza, la traslucenza e la consistenza del colore.
- Il surriscaldamento può causare deformazioni, crepe o altri difetti, mentre un calore insufficiente può causare una sinterizzazione incompleta o un legame debole.
-
Applicazioni dei forni per porcellana:
- Ceramica dentale:Utilizzata per creare corone, ponti e faccette dentali.La temperatura è attentamente controllata per soddisfare i requisiti specifici della porcellana dentale.
- Porcellana artistica:Utilizzata da artisti e artigiani per creare intricati pezzi di porcellana.La temperatura viene regolata in base al tipo di smalto e alla finitura desiderata.
- Componenti industriali:Utilizzata per la produzione di parti in porcellana ad alta resistenza per applicazioni tecniche, come isolatori o apparecchiature di laboratorio.
-
Fattori che influenzano le impostazioni di temperatura:
- Composizione del materiale:Le diverse formulazioni di porcellana possono richiedere temperature diverse per ottenere risultati ottimali.
- Ciclo di cottura:La velocità di riscaldamento e raffreddamento e la durata del processo di cottura possono influenzare le proprietà finali della porcellana.
- Design del forno:I moderni forni per porcellana sono spesso dotati di controlli avanzati e impostazioni programmabili per garantire una gestione precisa della temperatura.
In sintesi, la temperatura di un forno per porcellana è adattata ai requisiti specifici del materiale di porcellana e dell'applicazione prevista.Pur operando a temperature significativamente più basse rispetto ai forni di grafitizzazione, un controllo preciso è essenziale per ottenere i risultati desiderati.
Tabella riassuntiva:
Aspetto | Dettagli |
---|---|
Intervallo di temperatura | Da 600°C a 1200°C, a seconda dell'applicazione e del tipo di porcellana. |
Confronto | I forni di grafitizzazione operano a 2500°C - 3000°C per la formazione di grafite. |
Applicazioni principali | Ceramica dentale, porcellana artistica, componenti industriali. |
Importanza del controllo | Assicura resistenza, densità e finitura estetica; previene i difetti. |
Fattori che influenzano | Composizione del materiale, ciclo di cottura e design del forno. |
Avete bisogno di un forno per porcellana su misura per le vostre esigenze specifiche? Contattateci oggi stesso per saperne di più!