Il ciclo di sinterizzazione è un processo critico nella scienza dei materiali e nella produzione, in cui i materiali in polvere vengono trasformati in corpi solidi e densi attraverso l'applicazione di calore e pressione, senza raggiungere il punto di fusione del materiale.Questo processo è ampiamente utilizzato in settori quali la metallurgia delle polveri, la ceramica e la plastica per creare prodotti durevoli e coesi.Il ciclo di sinterizzazione prevede in genere diverse fasi, tra cui la preparazione delle polveri, la compattazione e il riscaldamento controllato, seguito dal raffreddamento.Ogni fase svolge un ruolo fondamentale nel garantire l'integrità strutturale del prodotto finale e le proprietà desiderate.
Punti chiave spiegati:
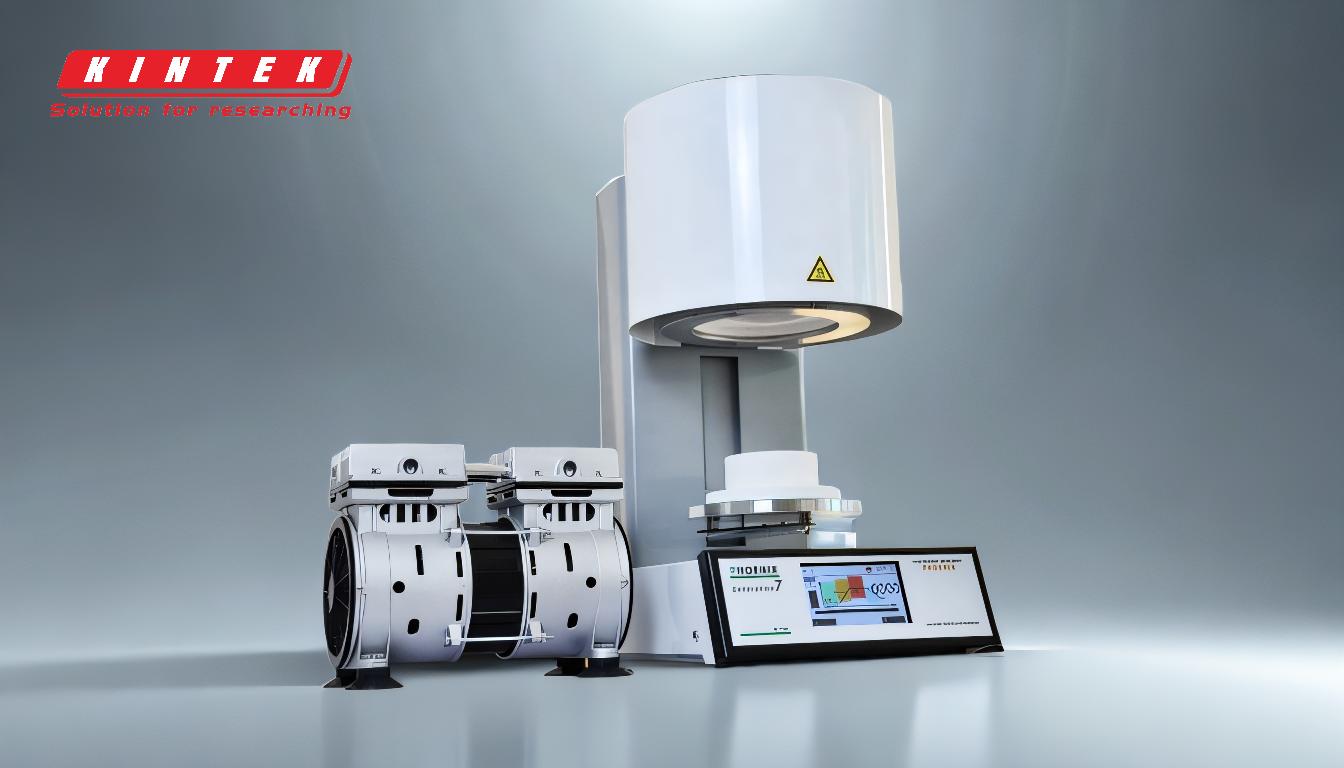
-
Definizione e scopo della sinterizzazione:
- La sinterizzazione è un processo che fonde piccole particelle in una massa solida senza fondere il materiale.Viene utilizzato per creare prodotti densi e durevoli da materiali in polvere come metalli, ceramiche e plastiche.
- Lo scopo principale della sinterizzazione è quello di legare le particelle di polvere adiacenti, ottenendo una struttura coesiva con proprietà meccaniche migliorate come resistenza, durezza e durata.
-
Fasi del ciclo di sinterizzazione:
-
Preparazione della polvere:
- Il processo inizia con la preparazione delle materie prime in polvere.Questo può comportare la miscelazione delle polveri con additivi come leganti, deflocculanti e acqua per creare un impasto, che viene poi essiccato a spruzzo per formare dei granuli.
-
Compattazione:
- La polvere preparata viene compattata mediante pressione meccanica, a freddo o a caldo, per formare un pezzo "verde".Questa fase garantisce l'uniformità ed elimina i vuoti nel materiale.
-
Sinterizzazione (cottura):
- Il pezzo verde viene riscaldato in un ambiente controllato, in genere in un forno di sinterizzazione o in un forno.La temperatura è accuratamente regolata per facilitare il legame delle particelle attraverso la diffusione, che porta alla formazione del collo e alla densificazione.Il materiale non fonde, ma subisce una diffusione atomica che fonde le particelle tra loro.
-
Raffreddamento:
- Dopo la sinterizzazione, il materiale viene raffreddato gradualmente per consentire la solidificazione in una struttura rigida e coesa.Questa fase è fondamentale per ottenere le proprietà meccaniche desiderate e prevenire i difetti.
-
Preparazione della polvere:
-
Fattori chiave che influenzano il processo di sinterizzazione:
-
Temperatura:
- La temperatura di sinterizzazione deve essere sufficientemente alta per favorire il legame delle particelle, ma inferiore al punto di fusione del materiale per evitare la liquefazione.
-
Pressione:
- La pressione applicata durante la compattazione assicura una densità uniforme e riduce la porosità nella parte verde.
-
Tempo:
- La durata della sinterizzazione influisce sul grado di legame e densificazione delle particelle.Tempi di sinterizzazione più lunghi producono generalmente legami più forti, ma devono essere bilanciati con il consumo di energia e l'efficienza della produzione.
-
Atmosfera:
- L'ambiente di sinterizzazione (ad esempio, gas inerte, vuoto o aria) può influenzare le proprietà finali del materiale impedendo l'ossidazione o facilitando reazioni chimiche specifiche.
-
Temperatura:
-
Applicazioni della sinterizzazione:
-
Metallurgia delle polveri:
- La sinterizzazione è ampiamente utilizzata per produrre componenti metallici come ingranaggi, cuscinetti e parti di automobili.Consente di creare forme complesse con elevata precisione e scarti minimi.
-
La ceramica:
- Nell'industria ceramica, la sinterizzazione è utilizzata per produrre piastrelle, isolanti e altri prodotti con elevata stabilità termica e meccanica.
-
Materie plastiche e compositi:
- La sinterizzazione viene impiegata per creare componenti in plastica durevoli e materiali compositi con proprietà personalizzate.
-
Metallurgia delle polveri:
-
Vantaggi della sinterizzazione:
-
Costo-efficacia:
- La sinterizzazione riduce gli scarti di materiale e consente la produzione di componenti di forma quasi netta, riducendo al minimo la necessità di ulteriori lavorazioni.
-
Versatilità del materiale:
- Il processo può essere applicato a un'ampia gamma di materiali, tra cui metalli, ceramiche e polimeri.
-
Proprietà migliorate:
- I prodotti sinterizzati presentano una maggiore resistenza meccanica, durezza e resistenza all'usura grazie alla densificazione e al legame delle particelle.
-
Costo-efficacia:
-
Sfide e considerazioni:
-
Controllo dei parametri di processo:
- Per ottenere risultati costanti è necessario un controllo preciso della temperatura, della pressione e del tempo, che può essere impegnativo nella produzione su larga scala.
-
Limitazioni dei materiali:
- Non tutti i materiali sono adatti alla sinterizzazione, in particolare quelli con basso punto di fusione o scarsa stabilità termica.
-
Costi dell'apparecchiatura:
- I forni e le presse di sinterizzazione possono essere costosi, soprattutto per le applicazioni ad alta temperatura o ad alta pressione.
-
Controllo dei parametri di processo:
In sintesi, il ciclo di sinterizzazione è un processo versatile ed essenziale nella produzione moderna, che consente di produrre materiali e componenti ad alte prestazioni.Comprendendo le fasi, i fattori di influenza e le applicazioni della sinterizzazione, i produttori possono ottimizzare il processo per soddisfare i requisiti specifici dei prodotti e ottenere risultati superiori.
Tabella riassuntiva:
Aspetto | Dettagli |
---|---|
Definizione | Fonde le particelle di polvere in una massa solida senza fondere il materiale. |
Fasi | Preparazione della polvere, compattazione, sinterizzazione (cottura), raffreddamento. |
Fattori chiave | Temperatura, pressione, tempo, atmosfera. |
Applicazioni | Metallurgia delle polveri, ceramica, plastica e materiali compositi. |
Vantaggi | Economicità, versatilità del materiale, proprietà meccaniche migliorate. |
Sfide | Controllo preciso dei parametri, limiti dei materiali, costi elevati delle apparecchiature. |
Ottimizzate il vostro processo di sinterizzazione con una guida esperta... contattateci oggi stesso !