Il rivestimento per sinterizzazione è un processo specializzato utilizzato per creare rivestimenti densi, durevoli e funzionali su substrati fondendo insieme le particelle senza fondere il materiale di base.Questo processo prevede la preparazione di una miscela di polveri, la loro compattazione nella forma desiderata e l'applicazione di calore e pressione per unire le particelle.Il risultato è un rivestimento coeso, a bassa porosità e con proprietà meccaniche migliorate.La sinterizzazione è ampiamente utilizzata in settori quali la metallurgia delle polveri, la ceramica e la produzione additiva per produrre rivestimenti ad alta resistenza, resistenza all'usura e stabilità termica.Di seguito, vengono spiegate in dettaglio le fasi e i principi chiave del processo di sinterizzazione dei rivestimenti.
Punti chiave spiegati:
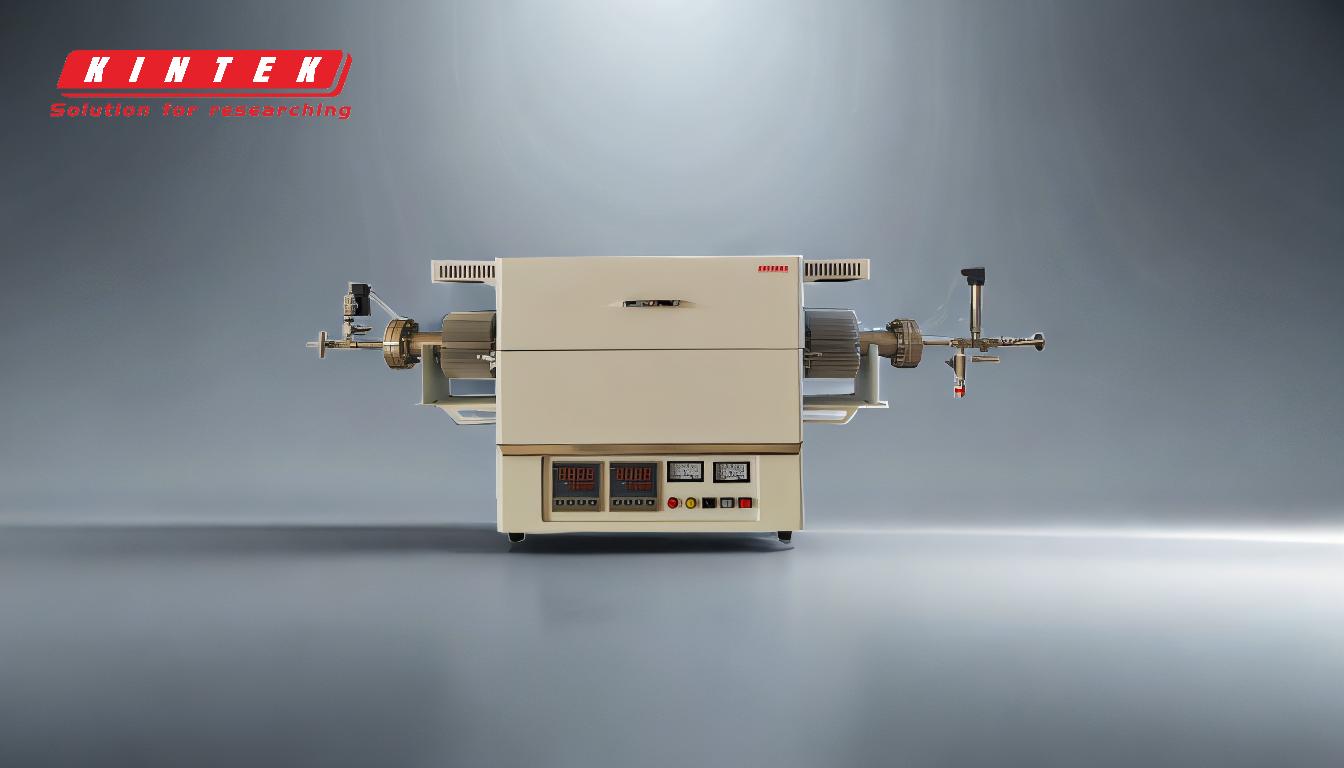
-
Preparazione della miscela di polveri
- Il processo inizia con la preparazione di una miscela di polveri, che in genere comprende il materiale primario (ad esempio, metallo, ceramica o plastica) e un agente legante (ad esempio, cera o polimero).
- L'agente legante aiuta le particelle di polvere ad aderire l'una all'altra durante la fase iniziale di modellazione.
- La miscela di polveri viene spesso personalizzata per ottenere proprietà specifiche nel rivestimento finale, come la durezza, la conduttività termica o la resistenza alla corrosione.
-
Compattazione e modellazione
- La miscela di polveri viene compattata nella forma desiderata utilizzando metodi come strumenti di pressatura, saldature a freddo o laser stampati in 3D.
- Questa fase assicura che le particelle di polvere siano densamente imballate e uniformemente distribuite, il che è fondamentale per ottenere un rivestimento omogeneo.
- La compattazione viene generalmente eseguita in atmosfera controllata per evitare la contaminazione e l'ossidazione.
-
Riscaldamento e consolidamento
- La polvere compattata viene riscaldata a una temperatura appena inferiore al punto di fusione del materiale primario.
- Questo riscaldamento attiva la diffusione degli atomi attraverso i confini delle particelle, provocandone la fusione e la densificazione.
- In alcuni casi, si ricorre alla sinterizzazione in fase liquida (LPS), in cui un materiale secondario con un punto di fusione inferiore fonde e riempie gli spazi tra le particelle, accelerando il processo di incollaggio.
-
Rimozione dell'agente legante
- Con l'aumento della temperatura, l'agente legante evapora o brucia, lasciando una struttura porosa del materiale primario.
- Questa fase è fondamentale per garantire che il rivestimento finale sia privo di impurità e abbia una composizione uniforme.
-
Fusione e densificazione delle particelle
- A temperature più elevate, le particelle primarie iniziano a fondersi in superficie, formando una massa solida con porosità ridotta.
- Il processo di fusione è guidato dalla diffusione atomica, che rafforza i legami tra le particelle e migliora le proprietà meccaniche del rivestimento.
- Il risultato è un rivestimento denso e coeso che aderisce saldamente al substrato.
-
Raffreddamento e solidificazione
- Al termine del processo di fusione, il materiale viene lasciato raffreddare e solidificare in una massa unificata.
- Il raffreddamento controllato è essenziale per prevenire gli stress termici e garantire che il rivestimento mantenga le proprietà desiderate.
- Il prodotto finale è un rivestimento duro e durevole, con una maggiore forza, resistenza all'usura e stabilità termica.
-
Applicazioni dei rivestimenti per sinterizzazione
- I rivestimenti per sinterizzazione sono ampiamente utilizzati in settori come quello aerospaziale, automobilistico ed elettronico per applicazioni che richiedono materiali ad alte prestazioni.
- Ne sono un esempio i rivestimenti resistenti all'usura per gli utensili da taglio, i rivestimenti a barriera termica per i componenti dei motori e i rivestimenti resistenti alla corrosione per le apparecchiature industriali.
- Il processo viene utilizzato anche nella produzione additiva per creare parti complesse, ad alta resistenza e con geometrie precise.
-
Vantaggi dei rivestimenti per sinterizzazione
- Il processo di sinterizzazione consente di creare rivestimenti con proprietà personalizzate, come durezza, porosità e conduttività termica.
- È conveniente per la produzione di grandi quantità di rivestimenti di alta qualità.
- Il processo può essere utilizzato con un'ampia gamma di materiali, tra cui metalli, ceramiche e compositi.
Seguendo questi passaggi, i rivestimenti per sinterizzazione raggiungono un equilibrio di resistenza, durata e funzionalità che li rende una valida soluzione per una varietà di applicazioni industriali.
Tabella riassuntiva:
Passo | Descrizione |
---|---|
1.Preparazione della polvere | Mescolare il materiale primario (ad es. metallo, ceramica) con un agente legante (ad es. cera). |
2.Compattazione e modellazione | Compattare la polvere nella forma desiderata utilizzando strumenti di pressatura o laser stampati in 3D. |
3.Riscaldamento e consolidamento | Riscaldare al di sotto del punto di fusione per consentire l'adesione e la densificazione delle particelle. |
4.Rimozione dell'agente legante | L'agente legante evapora, lasciando una struttura porosa del materiale primario. |
5.Fusione delle particelle | Le particelle si fondono in superficie, formando un rivestimento denso e coesivo. |
6.Raffreddamento e solidificazione | Il raffreddamento controllato garantisce la resistenza e la durata del rivestimento. |
7.Applicazioni | Utilizzato nei settori aerospaziale, automobilistico ed elettronico per rivestimenti resistenti all'usura. |
8.Vantaggi | Proprietà personalizzate, convenienti e compatibili con metalli, ceramiche ecc. |
Scoprite come i rivestimenti per sinterizzazione possono migliorare le vostre applicazioni industriali. contattateci oggi stesso !