La temperatura di sinterizzazione ottimale dipende dal materiale da lavorare, dalle proprietà desiderate del prodotto finale e dalla specifica tecnica di sinterizzazione utilizzata. In genere, le temperature di sinterizzazione vanno dal 70% al 90% del punto di fusione del materiale. Per molti materiali, ciò si traduce in temperature comprese tra 900°C e 1400°C. I fattori chiave che influenzano la temperatura ottimale sono la composizione del materiale, la dimensione delle particelle, la densità desiderata e le proprietà meccaniche del prodotto finale. Inoltre, la velocità di riscaldamento, la velocità di raffreddamento e le condizioni atmosferiche (ad esempio, aria, vuoto o gas inerte) svolgono un ruolo fondamentale per ottenere i migliori risultati. Di seguito analizziamo in dettaglio questi fattori per determinare la temperatura di sinterizzazione ottimale per le varie applicazioni.
Punti chiave spiegati:
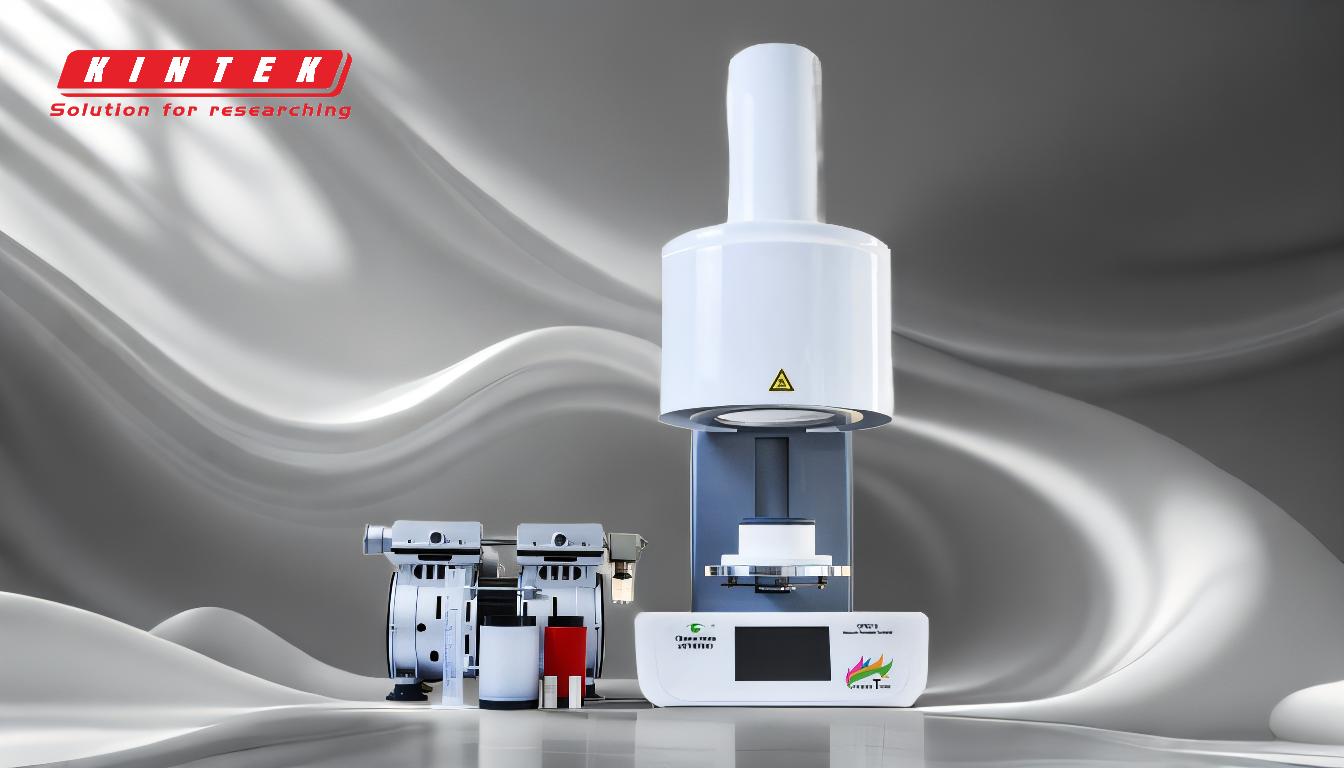
-
Temperature di sinterizzazione specifiche per i materiali:
-
La temperatura di sinterizzazione ottimale dipende in larga misura dal materiale da lavorare. Ad esempio:
- Ceramica: Tipicamente sinterizzato a 1200°C - 1400°C.
- Metalli: Spesso sinterizzati al 70%-90% del loro punto di fusione, che può variare da 900°C a 1300°C.
- Polimeri: Richiedono temperature più basse, di solito inferiori a 300°C.
- La scelta della temperatura assicura un'adeguata densificazione senza causare un'eccessiva crescita dei grani o la degradazione del materiale.
-
La temperatura di sinterizzazione ottimale dipende in larga misura dal materiale da lavorare. Ad esempio:
-
Influenza della dimensione delle particelle:
- Le polveri più fini richiedono generalmente temperature di sinterizzazione più basse a causa della loro maggiore energia superficiale, che favorisce una densificazione più rapida.
- Le particelle più grandi possono richiedere temperature più elevate per ottenere lo stesso livello di compattazione.
-
Tariffe di riscaldamento e raffreddamento:
- Tasso di riscaldamento: Una velocità di rampa controllata da 900°C alla temperatura massima è fondamentale per evitare shock termici e garantire una densificazione uniforme.
- Velocità di raffreddamento: Un raffreddamento rapido può portare a tensioni residue, mentre un raffreddamento lento favorisce l'equilibrio delle microstrutture. La velocità di raffreddamento a 900°C è particolarmente importante per ottenere le proprietà meccaniche desiderate.
-
Condizioni atmosferiche:
-
L'atmosfera di sinterizzazione (ad esempio, aria, vuoto o gas inerti come argon o azoto) influisce sulla temperatura ottimale:
- Vuoto o gas inerte: Impedisce l'ossidazione e consente temperature più elevate per una migliore densificazione.
- Aria: Può limitare la temperatura massima per evitare l'ossidazione o la degradazione del materiale.
-
L'atmosfera di sinterizzazione (ad esempio, aria, vuoto o gas inerti come argon o azoto) influisce sulla temperatura ottimale:
-
Proprietà del prodotto desiderate:
- Temperature di sinterizzazione più elevate migliorano generalmente la resistenza alla trazione, la resistenza alla fatica da flessione e l'energia d'impatto.
- Tuttavia, temperature eccessive possono portare alla crescita dei grani, alla riduzione della resistenza e all'instabilità dimensionale.
-
Parametri di processo:
- Spessore dello strato: Gli strati più spessi (250-500 mm) possono richiedere temperature più elevate per garantire una sinterizzazione uniforme.
- Velocità della macchina: Controllato a 1,5-4 m/min per garantire che l'alimentazione di sinterizzazione venga bruciata al punto finale previsto.
- Volume d'aria e vuoto: Un flusso d'aria adeguato (ad esempio, 3200m³ per tonnellata di minerale da sinterizzare) e livelli di vuoto sono essenziali per ottenere risultati costanti.
-
Considerazioni pratiche:
- Il tipo di forno di sinterizzazione (a nastro, a spinta o batch) e le sue capacità influenzano l'intervallo di temperatura raggiungibile.
- La scelta del processo dipende dall'equilibrio tra le proprietà desiderate del prodotto e i parametri limitanti, come i vincoli delle apparecchiature e il comportamento del materiale.
In sintesi, la temperatura di sinterizzazione ottimale non è un valore fisso, ma un parametro scelto con cura che bilancia le proprietà del materiale, le condizioni di processo e i risultati desiderati. Considerando fattori quali la composizione del materiale, le dimensioni delle particelle, le velocità di riscaldamento e raffreddamento, le condizioni atmosferiche e i parametri di processo, i produttori possono determinare la temperatura migliore per la loro specifica applicazione.
Tabella riassuntiva:
Fattore | Influenza sulla temperatura di sinterizzazione |
---|---|
Materiale | Ceramica: 1200°C-1400°C; Metalli: 70%-90% del punto di fusione (900°C-1300°C); Polimeri: <300°C. |
Dimensione delle particelle | Polveri più fini: Temperature più basse; particelle più grandi: Temperature più elevate. |
Tariffe di riscaldamento/raffreddamento | Il riscaldamento controllato evita lo shock termico; il raffreddamento lento favorisce l'equilibrio delle microstrutture. |
Atmosfera | Vuoto/gas inerte: Temperature più elevate; aria: Limitata per evitare l'ossidazione. |
Proprietà desiderate | Temperature più elevate migliorano la resistenza, ma rischiano la crescita dei cereali; l'equilibrio è fondamentale. |
Parametri di processo | Lo spessore dello strato, la velocità della macchina, il flusso d'aria e i livelli di vuoto influiscono sulla consistenza della sinterizzazione. |
Avete bisogno di aiuto per determinare la temperatura di sinterizzazione ottimale per i vostri materiali? Contattate i nostri esperti oggi stesso !